When it comes to injection molding tools, ACE stands out as a leading manufacturer with a proven track record of delivering high-quality products. With their extensive expertise in tooling solutions, ACE offers a wide range of molds and auxiliary equipment designed to meet the diverse needs of the industry. Their commitment to innovation, precision, and customer satisfaction has earned them a strong reputation in the field of injection molding.
Injection molding is a widely adopted manufacturing process for producing high-quality plastic parts with precision and efficiency. At the heart of this process lies the injection molding tool, a vital component that determines the success of the production cycle. In this blog post, we will delve into the realm of injection molding tools, exploring their various types, functions, and significance in the manufacturing industry.
Understanding Injection Molding Tools:
Injection molding tools are specialized devices used in the injection molding process, which involves injecting molten plastic material into a mold cavity to create a desired shape. These tools are typically made of high-grade steel and are designed to withstand the extreme temperatures and pressures involved in the molding process. They serve as the foundation for manufacturing a wide array of plastic products across various industries.
1. Injection Mold:
The injection mold, also known as the primary tool, is the key component of the injection molding process. It consists of two main parts: the core and the cavity. The molten plastic material is injected into the cavity, which imparts the desired shape and structure to the final product. Injection molds are custom-built to meet the specific requirements of each product and are designed with meticulous precision to ensure optimal results.
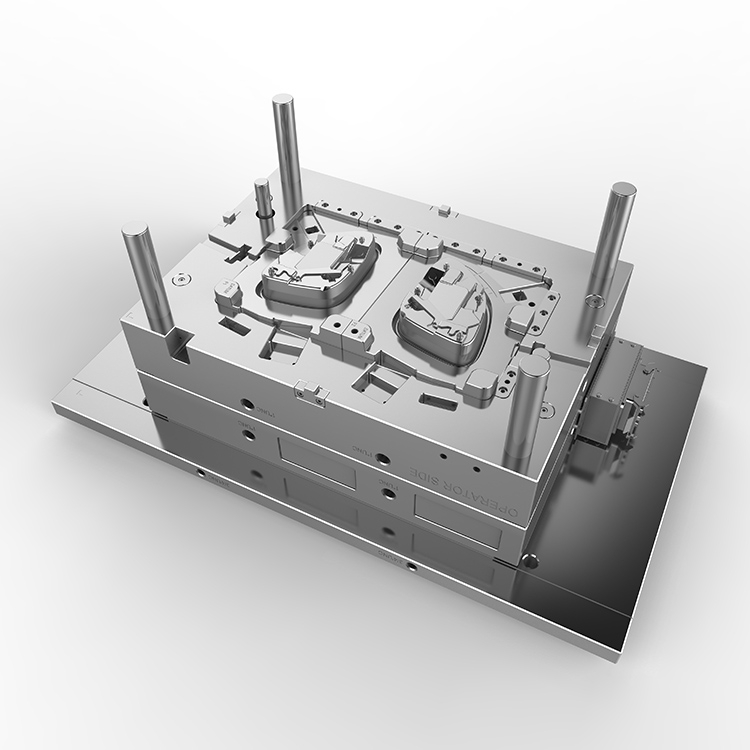
2. Runner System:
The runner system forms the network of channels through which the molten plastic flows from the injection molding machine to the mold cavity. It includes the sprue, runners, and gates. The sprue acts as the main channel through which the molten plastic enters the mold, while the runners distribute the material to the individual cavities. The gates control the flow and timing of the material into each cavity.
3. Cooling System:
Efficient cooling is crucial in the injection molding process to ensure proper solidification of the molten plastic. The cooling system, comprising cooling channels integrated within the mold, helps regulate the temperature of the mold and the plastic material. Proper cooling ensures consistent quality, reduces cycle time, and prevents warping or deformation of the final product.
4. Ejection System:
Once the plastic component has solidified within the mold, it needs to be ejected from the tool. The ejection system consists of ejector pins or ejector plates that push the product out of the mold. It is designed to facilitate smooth and reliable ejection while maintaining the integrity of the finished part.
Molds: Injection Molding Tools
1. Plastic Injection Mold:
The plastic injection mold is the primary tool used in the injection molding process. It is designed to shape molten plastic material into the desired form. Plastic injection molds consist of two halves, namely the cavity and the core, which come together to create the final part's shape.
2. Multi-Cavity Mold:
Multi-cavity molds enable the production of multiple identical parts in a single injection molding cycle. By incorporating multiple cavities within a single mold, manufacturers can significantly increase productivity and reduce manufacturing costs.
3. Hot Runner Mold:
Hot runner molds are equipped with a system of heated channels that deliver molten plastic directly into the cavities. This technology minimizes material waste, shortens cycle times, and enhances overall efficiency.
Auxiliary Equipment: Injection Molding Tools
1. Injection Molding Machine:
While not strictly a tool in the traditional sense, an injection molding machine is an essential piece of equipment used in conjunction with the mold. It is responsible for melting and injecting the plastic material into the mold under high pressure.
2. Temperature Controllers:
Temperature controllers regulate the temperature of the mold and the plastic material during the injection molding process. By maintaining precise temperature control, they ensure optimal part quality and prevent issues such as warping or shrinkage.
3. Robotics and Automation Systems:
Robotics and automation systems play a crucial role in injection molding by automating various tasks, such as part removal, quality inspection, and assembly. These systems enhance production efficiency, reduce labor costs, and improve overall process reliability.
Why You Should Choose ACE Plastic Injection Moulding For Your Project?
1. Unmatched Machinery and Production Capacity:
ACE takes pride in its 32 in-house injection molding machines, boasting a clamping force ranging from 98 to 1200 tons. This impressive range of machinery allows ACE to handle projects of varying sizes and complexities. Whether it's a small plastic part or a larger component, ACE has the capability to accommodate diverse production requirements. Furthermore, their department operates around the clock, ensuring on-time delivery and minimal lead times.
2. Quality Control Systems Ensuring Superior Products:
At ACE, maintaining product quality is a top priority. The injection molding department is equipped with a robust quality control system that meticulously monitors all operations. By adhering to controlled processes, ACE can effectively ensure the final products' quality. From the initial mold design to the production and finishing stages, every step is executed with precision and attention to detail. This commitment to quality guarantees that ACE delivers products that meet or exceed customer expectations.
3. Partnership for Expanded Capabilities:
ACE goes the extra mile to meet diverse customer requirements. Through a strong partnership with a nearby industry leader, ACE gains access to a wide range of injection molding machinery, with capacities ranging from 50 to 2000 tons. This collaborative effort enables ACE to explore advanced techniques such as two-shot molding and gas-assisted injection molding. By leveraging their partner's expertise and cutting-edge equipment, ACE can test a broader range of plastic molds and create samples for customer evaluation. This flexibility ensures that ACE can tackle even the most challenging manufacturing problems.
4. Versatile Material Expertise:
ACE is well-versed in working with various types of thermoplastic and thermosetting materials. Their expertise extends to reinforced and filled plastics, allowing them to cater to a wide range of applications. Common plastic materials such as PP, PE, ABS, PC, PC+ABS, Nylon+GF, POM, PMMA, PA, and PS are all within ACE's capabilities. Whether customers require durable components or aesthetically pleasing parts, ACE can provide suitable materials and deliver exceptional results.
Conclusion
ACE has established itself as a leading manufacturer in the field of injection molding. With an extensive range of injection molding machines, a commitment to quality control, and a collaborative partnership for expanded capabilities, ACE can confidently tackle diverse customer requirements. Their expertise in working with various thermoplastic and thermosetting materials further solidifies their position as a reliable solution provider. When it comes to injection molding tools, ACE is the go-to manufacturer for those seeking quality, precision, and innovative solutions.