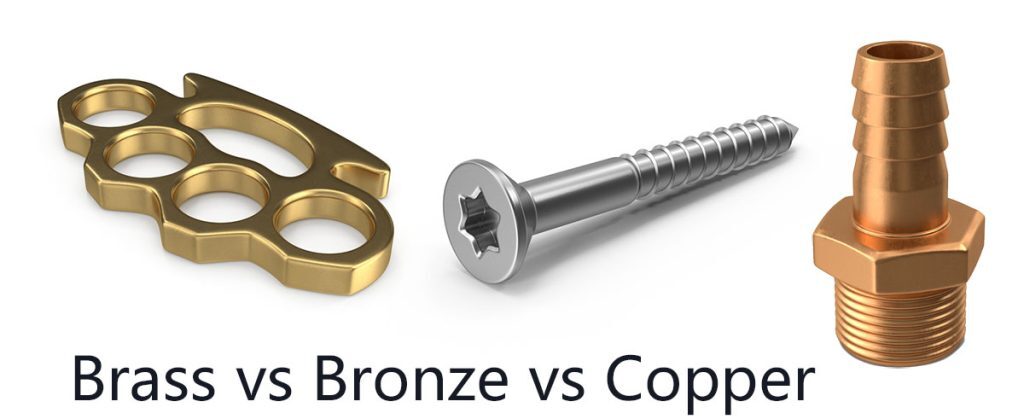
When it comes to differentiating between brass, bronze, and copper, it can be quite challenging as these metals share many similarities. However, understanding their distinct features is crucial for making the right material selection for your projects. In this article, we will delve into the detailed comparison of brass, bronze, and copper, including their available alloys, material properties, conductivity, strength, formability, appearance, applications, benefits, and pricing. So, let's dive in and explore the unique characteristics of these "Red Metals."
Available Alloys
Brass Alloys
Brass is an alloy composed primarily of copper and zinc, with other elements added to create different variations. Some of the most popular brass alloys used in various industries include:
- Alloy 260: Also known as cartridge brass, this alloy exhibits excellent cold working characteristics, making it suitable for applications in automobiles, ammunition, hardware, and fasteners.
- Alloy 272: Commonly referred to as yellow brass, alloy 272 contains approximately 33% zinc and is primarily used in industrial applications.
- Alloy 330: This brass alloy is valued for its high machinability and low lead content, making it suitable for piping applications.
- Alloy 353: Clock brass, known for its excellent machinability, is often used to fabricate high-precision parts like clock components.
- Alloy 360: The most common grade of brass available, alloy 360 is highly formable and machinable. It is widely used in the manufacturing of fittings, fasteners, valves, and hardware components. It is also suitable for brazing and soldering applications.
- Alloy 464: Also known as naval brass, alloy 464 is famous for its excellent corrosion resistance and ability to withstand temperature changes. It is commonly used in marine environments and various other applications.
Bronze Alloys
Bronze is primarily an alloy of copper, with the addition of other elements such as tin, aluminum, phosphorus, and silicon to enhance its properties. Some of the common bronze alloys are:
- Alloy 932: High-leaded bronze, commonly used for non-pressure components like washers and bushings.
- Alloy 954: An aluminum bronze alloy with industrial applications and mounting equipment due to its corrosion resistance.
- Phosphor Bronze: This alloy typically contains tin and phosphorus and is known for its toughness, strength, low friction coefficient, high fatigue resistance, and fine grain. It finds applications in electrical products, bellows, springs, washers, and corrosion-resistant equipment.
- Aluminum Bronze: With an aluminum content of 6% - 12% and excellent corrosion and wear resistance, this alloy is commonly used in marine hardware, sleeve bearings, pumps, and valves handling corrosive fluids.
- Silicon Bronze: An alloy containing copper, zinc, and silicon, it offers high strength, corrosion resistance, and is commonly used in pump and valve components.
Copper Alloys
Copper itself is a versatile metal with excellent electrical and thermal conductivity, good strength, formability, and corrosion resistance. Various copper alloys are used in different applications. Some commonly used copper alloys include:
- Oxygen-free Copper (Alloy 101): This copper alloy is preferred when high ductility and electrical conductivity are required.
- Electrolytic Copper (Alloy 110): Known for its highest thermal and electrical conductivity, as well as excellent ductility and malleability.
- Alloy 122: Similar to Alloy 110 mechanically, Alloy 122 exhibits superior weldability and formability.
- Tellurium Copper (Alloy 145): Contains approximately 0.7% tellurium, this alloy offers excellent electrical and thermal conductivity, machinability, and formability.
Material Properties Differences Between Brass, Bronze, and Copper
Understanding the material properties of brass, bronze, and copper is essential in determining their suitability for specific applications. Let's explore the differences in their elemental composition, corrosion resistance, durability, weight, machinability, and weldability.
Element Composition
Copper is a non-ferrous metal that exists in its pure state, while brass is an alloy of copper and zinc. Brass alloys can also contain other elements such as lead, manganese, iron, aluminum, and silicon. Bronze, on the other hand, is an alloy primarily composed of copper with the addition of tin and other elements like arsenic, phosphorus, aluminum, manganese, and silicon.
Corrosion Resistance
Corrosion resistance is an important factor to consider when selecting a metal for specific applications. Bronze, being an alloy of copper, often forms a protective layer of oxidized patina when exposed to air, providing adequate corrosion resistance. It is commonly used in marine applications and boat fittings. Copper also forms a protective layer of oxide, offering excellent corrosion resistance. Brass, however, has a lower level of corrosion resistance compared to bronze and copper, although some grades of brass with higher manganese content exhibit better corrosion resistance.
Durability
Bronze is known for its durability, with high strength and resistance to bending. Copper is also a durable metal but more flexible compared to bronze. It can be easily stretched and bent without cracking or scratching. Brass, on the other hand, is less durable, being vulnerable to splitting and cracking.
Weight
Weight is an important consideration, especially in applications where lightweight materials are desired. Brass and bronze have similar weights due to their densities, while copper is the heaviest of the three metals.
Machinability
Copper exhibits better machinability compared to brass and bronze. It is a more flexible metal, allowing for bending, turning, and other machining processes. Copper alloys also tend to have high ductility. Bronze, on the other hand, is a harder and sturdier metal that is less easily flexed. Brass falls in between, being less machinable than copper and bronze.
Weldability
Brass, bronze, and copper are all weldable in their respective domains. Oxygen-free copper and deoxidized copper are particularly easier to weld. MIG and TIG welding are popular techniques for melding copper. Brass alloys also support MIG, TIG, and silver soldering. However, alloys containing lead can be more challenging to weld. Among the bronze grades, unleaded bronze has fair weldability, while SMAW (Shielded Metal Arc Welding) may be the preferred technique.
Conductivity Differences Between Brass, Bronze, and Copper
The electrical and thermal conductivity of metals is an important factor to consider in many applications. Let's explore the differences in electrical and thermal conductivity between brass, bronze, and copper.
Electrical Conductivity
Copper is widely known for its excellent electrical conductivity and is often used as a benchmark for rating electrical materials. Brass, being an alloy of copper, has lower electrical conductivity, typically around 28% of copper's conductivity. Bronze, with its alloying elements, exhibits even lower electrical conductivity, usually around 15% of copper's conductivity.
Thermal Conductivity
Bronze has the highest thermal conductivity among the three metals, followed by copper. Brass has the lowest thermal conductivity of the three.
Strength Differences Between Brass, Bronze, and Copper
Strength is an important factor to consider in various applications. Let's examine the differences in tensile strength and yield strength between brass, bronze, and copper.
Tensile Strength
Bronze generally has higher tensile strength compared to brass and copper. It has a tensile strength ranging from 350 to 635 MPa. Brass follows with an ultimate tensile strength of 338 to 469 MPa, while copper has a tensile strength of 210 MPa.
Yield Strength
Bronze also boasts a higher yield strength compared to brass and copper. It has a yield strength ranging from 125 to 800 MPa. Brass has a yield strength of about 95 to 124 MPa, while copper possesses the least yield strength at 33.3 MPa.
Ability to Form
Formability is an important consideration when selecting a metal for manufacturing processes. Let's explore the formability, melting point, appearance, and touch of brass, bronze, and copper.
Formability
Copper exhibits excellent formability, allowing for plastic deformation without damage. It is often used to produce micron-sized wires. Some bronze alloys also offer good formability, such as PB1 phosphor bronze, which enables cold forming. Brass, however, is harder to form due to its low flexibility.
Melting Point
The melting point of a metal can affect its formability. Copper has a higher melting point of 1085 °C, which may limit its formability compared to bronze and brass. Bronze has a melting point of 913 °C, while brass has a melting point of 927 °C.
Appearance and Touch
Although brass, bronze, and copper may look similar, there are subtle differences in their appearance. Brass has a subdued yellowish-gold color, making it attractive for decorative elements. Bronze has a reddish-brown color, similar to copper, but with a dull gold shade. Copper, in its pure form, has a distinct reddish-brown color. When it comes to touch, copper scores 35 on the Brinell hardness scale, while brass scores between 55 and 73. Bronze falls between 40 and 420, making it the hardest of the three metals.
Applications of Brass, Bronze, and Copper
Brass, bronze, and copper find a wide range of applications due to their unique properties. Let's explore the applications of each metal.
Applications of Brass
Brass is commonly used in various industries for its aesthetic appeal and workability. Some of the common applications of brass include:
- Plumbing and piping materials
- Fittings
- Electronics and electrical terminals
- Musical instruments
- Clock and watch components
Applications of Bronze
Bronze is widely utilized in different fields due to its durability and resistance to corrosion. Some common applications of bronze include:
- Sculptures and artistic creations
- Musical instruments
- Industrial applications such as bushings and bearings
Applications of Copper
Copper is an essential metal in various industries, primarily due to its excellent electrical and thermal conductivity. Some applications of copper include:
- Electrical wiring and components
- Telecommunication equipment
- Heat sinks and heat exchangers
- Vacuum tubes
- Architectural components
Benefits of Brass, Bronze, and Copper
Each of these metals offers unique benefits that make them suitable for specific applications. Let's explore the advantages of brass, bronze, and copper.
Benefits of Brass
- Durability: Brass has good corrosion resistance, ensuring its durability and performance over time.
- Anti-bacterial properties: The copper content in brass produces ions that can attack microorganisms, making it suitable for sanitation and water filtration systems.
- Aesthetics: Brass is attractive and can be polished and buffed to achieve various textures and lusters.
Benefits of Bronze
- Corrosion and fatigue resistance: Bronze is highly resistant to corrosion and fatigue, making it suitable for applications in marine environments.
- Dimensional precision: Bronze is ideal for precision CNC machining services.
- Thermal and electrical conductivity: Bronze exhibits high thermal and electrical conductivity, making it suitable for electrical applications.
- Surface finishes: Bronze supports a wide range of metal surface finishing techniques, allowing for versatile aesthetics.
Benefits of Copper
- High thermal and electrical conductivity: Copper is known for its excellent thermal and electrical conductivity, making it ideal for electrical applications.
- Machinability: Copper is soft, malleable, and ductile, making it easy to work with and shape into various components.
- Corrosion resistance: Copper has low reactivity, resulting in excellent resistance to corrosion.
- Recyclability: Copper is highly recyclable, making it an environmentally friendly choice.
Pricing & Options
The prices of brass, bronze, and copper can vary depending on the specific alloys and market conditions. Generally, copper is the most expensive of the three metals, followed by bronze. Brass is typically the least expensive due to its higher zinc content, which is cheaper than copper. The availability of different grades and alloys also contributes to variations in pricing.
Conclusion
In conclusion, brass, bronze, and copper are distinct metals with unique properties and applications. Understanding their differences in terms of available alloys, material properties, conductivity, strength, formability, appearance, and benefits is essential for making informed material selections. Whether you need a corrosion-resistant material, high electrical conductivity, or superior formability, brass, bronze, and copper offer a range of options to suit your specific project requirements. Consider the specific characteristics and advantages of each metal to choose the most suitable option for your applications.
Additional Information: A brass vs bronze vs copper comparison is vital because it is very easy to muddle up these metals. In addition, the variations between these metal options are very subtle. Thus, parts designers may easily get confused during material selection. Moreover, the similarities in the elemental composition of these metals make it even harder to classify them.