Companies in the modern manufacturing sector are always looking for ways to enhance efficiency, reduce costs, and improve quality. One such technique that has been gaining traction in recent years is 2 Shot moulding. In this blog post, we will explore what 2 Shot moulding is and how it works, as well as examine some of its benefits and how ACE, a leading manufacturer of moulds and tooling components, is at the forefront of providing this service.
What is 2 Shot moulding?
2 Shot moulding, also known as two-shot injection moulding or dual-shot moulding, is an advanced plastic injection moulding process that enables the creation of complex, multi-material, or multi-colour plastic parts in a single moulding cycle. Unlike traditional injection moulding, where a single material is injected into a mould to create a part, 2 Shot moulding involves the sequential injection of two or more materials into the same mould cavity. This process allows for the integration of different materials or colours into a single part, eliminating the need for secondary assembly processes.
The Process of 2 Shot Moulding
The 2 Shot moulding process is a fascinating blend of precision engineering and intricate control. Here's a simplified breakdown of how it works:
Step 1: First Shot Injection
In the initial stage, the first material is injected into the mould cavity to form the base layer of the part. This material can be selected based on its functional properties, such as rigidity or durability.
Step 2: Rotating the mould
After the first material is injected and partially solidified, the mould rotates or moves to a different position to prepare for the second shot. This movement ensures that the first shot material remains in the correct position while the second shot is injected.
Step 3: Second Shot Injection
The second material, often of a different colour or with distinct properties, is then injected into the mould. This second material bonds seamlessly with the first shot, creating a single, integrated part.
Step 4: Ejection and Cooling
Once the second shot is complete, the moulded part is ejected from the mould cavity. It is then cooled and prepared for any necessary finishing or quality control processes.
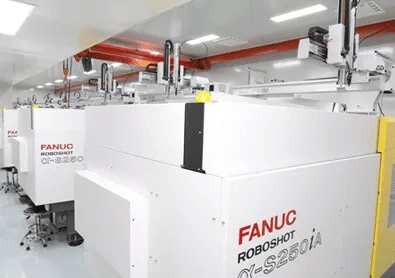
Manufacturing Benefits of 2 Shot Moulding
The advantages of it are numerous and far-reaching, making it an attractive option for manufacturers across various industries:
1. Enhanced Design Flexibility
2 Shot moulding allows for the integration of different materials with varying properties, enabling the creation of complex, multi-functional parts that would be challenging to produce using traditional methods.
2. Reduced Assembly Costs
By eliminating the need for secondary assembly processes, 2 Shot moulding streamlines production reduces labour costs and minimizes the risk of assembly errors.
3. Improved Product Aesthetics
The ability to use multiple colours and materials in a single part enhances product aesthetics, making it an ideal choice for consumer goods and products with branding requirements.
4. Increased Product Durability
The combination of materials in 2 Shot moulding can enhance the durability and performance of the final product, particularly in applications that require resistance to wear, heat, or chemicals.
Design Considerations for 2 Shot Moulding
2 shot moulding, also known as two-shot or over-moulding, is a manufacturing technique that involves injecting two different materials into a single mould in two consecutive cycles. This process offers several advantages, including reduced assembly time, improved part functionality, and enhanced aesthetics. To make the most of these benefits, designers should consider the following factors:
1. Material Compatibility
The first step in designing for it is selecting materials that are compatible with each other. These materials should adhere well to each other during the moulding process to ensure a strong bond between the layers. Consult with material suppliers or your plastic mould manufacturer to identify suitable combinations that meet your project requirements.
2. Part Geometry
The complexity of part geometry plays a crucial role in 2 shot moulding. Designers should aim for parts with smooth transitions and minimal sharp corners, as these features can be challenging to mould accurately. Radii and fillets should be incorporated into the design to facilitate material flow and reduce the risk of defects.
3. Mould Design
Collaborating closely with your plastic mould manufacturer, such as ACE, is essential for successful 2 shot moulding. The mould design must accommodate the sequential injection of materials, ensuring that there is no contamination or mixing of the two materials during the process. Proper venting and gating are also critical to prevent air traps and maintain part quality.
Optimizing Designs for 2 Shot Moulding
Now that we've covered the fundamental design considerations, let's delve deeper into optimizing designs for 2 shot moulding:
4. Design for Functionality
One of the primary advantages of 2 shot moulding is the ability to combine different materials to enhance product functionality. Designers should leverage this capability by carefully considering how each material contributes to the part's overall performance. For example, soft-touch grips can be over-moulded onto rigid handles for ergonomic benefits.
5. Aesthetics and Branding
2 shot moulding allows for the creation of visually appealing and highly customized parts. Designers should explore the potential for incorporating branding elements, textures, or colour contrasts into their designs. ACE's expertise in mould design and material selection can help achieve the desired aesthetic outcomes.
6. Cost Efficiency
While 2 shot moulding offers numerous advantages, it's essential to balance these benefits with cost considerations. Designers should work with plastic mould manufacturers to optimize the design for efficient production, minimizing waste and reducing cycle times.
7. Testing and Validation
Before committing to mass production, it's crucial to prototype and test your 2 shot moulded parts thoroughly. This allows for adjustments and refinements to ensure the final product meets all performance and quality standards.
ACE: Your Trusted Partner in 2 Shot Moulding
As the demand for 2 Shot moulding continues to grow, finding a reliable manufacturing partner is crucial. ACE, a leading manufacturer with a commitment to innovation, precision, and customer satisfaction, is at the forefront of providing 2 Shot moulding services.
With state-of-the-art machinery, a team of skilled engineers, and a track record of delivering high-quality products, ACE is well-equipped to meet the diverse needs of various industries. Whether you require complex multi-material parts for the automotive sector or vibrant, multi-colour components for consumer electronics, ACE has the expertise and capabilities to bring your vision to life.
Conclusion
In conclusion, 2 Shot moulding is a game-changer in the manufacturing industry, offering unparalleled design flexibility, cost savings, and improved product quality. As the demand for innovative solutions continues to rise, ACE stands ready to meet the challenges of tomorrow with its cutting-edge 2 Shot moulding services. When it comes to precision and efficiency, ACE is your trusted partner for all your manufacturing needs.