Moulding components play a crucial role in product design and manufacturing, impacting the quality, durability, and functionality of the final product. Whether you are a product designer, engineer, or manufacturer, understanding the intricacies of moulding components is essential for achieving success in your projects. In this comprehensive guide, we will delve into the world of moulding components, with a special focus on injection moulding components, and explore the common mistakes to avoid in the design process.
A Closer Look at Injection Moulding Components for Product Design
Injection moulding is one of the most popular and widely used techniques for creating plastic components in various industries. This process involves injecting molten plastic material into a mould cavity, which is then cooled and solidified to create the final product. To master the art of moulding components, it is essential to understand the various aspects of injection moulding components.
1. Material Selection: The choice of material is a critical factor in injection moulding. Moulding components manufacturer ACE offers a wide range of materials, each with its unique properties and advantages. Product designers must carefully select a material that meets the specific requirements of their project, considering factors such as strength, heat resistance, flexibility, and cost.
2. Mould Design: The design of the mould cavity is another crucial aspect of injection moulding. The mould must be precisely engineered to create the desired shape and size of the component. Precision and attention to detail are vital in mould design to ensure the final product meets the required tolerances and quality standards.
3. Cooling and Ejection: Effective cooling and ejection mechanisms are essential for the successful production of moulded components. Proper cooling ensures that the component solidifies evenly and prevents defects like warping or shrinkage. An efficient ejection system ensures the smooth release of the component from the mould without causing damage.
4. Injection Speed and Pressure: The injection speed and pressure can significantly affect the quality of the moulded component. Controlling these parameters is essential to prevent issues like air pockets, burns, or flash. It is essential to strike the right balance between speed and pressure to achieve optimal results.
5. Quality Control: Ensuring the quality of moulded components is an ongoing process. Quality control measures such as inspections, testing, and monitoring help identify and rectify any issues that may arise during production. ACE, as a reliable moulding components manufacturer, follows strict quality control procedures to guarantee the highest standards of its products.
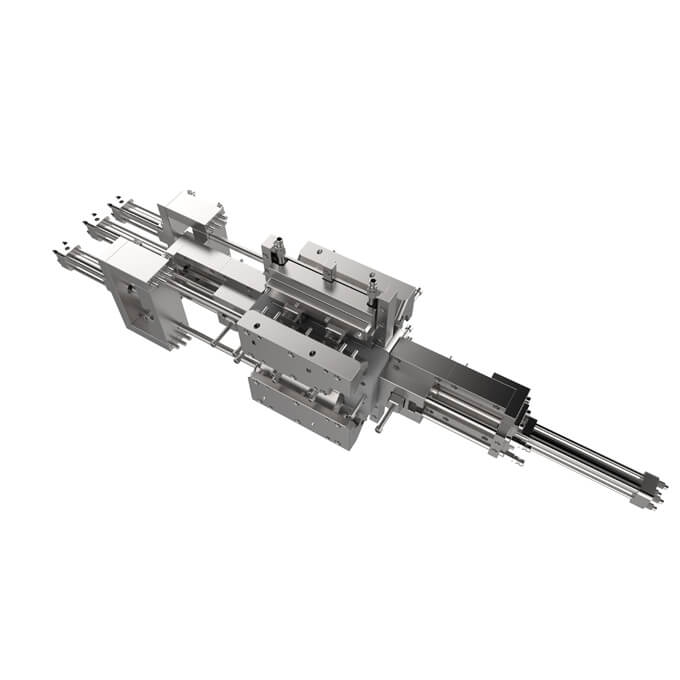
5 Common Mistakes to Avoid When Designing Moulding Components
While understanding the key aspects of injection moulding components is crucial, it is equally important to be aware of common mistakes that can occur during the design process. Here are five common mistakes to avoid:
1. Neglecting Material Selection: Choosing the wrong material can lead to various issues, including poor product performance, reduced durability, and increased production costs. To avoid this mistake, it is essential to thoroughly research and test materials to find the best fit for your project.
2. Inadequate Mould Design: Insufficient attention to mould design can result in defects and irregularities in the moulded components. Designing the mould with precision and factoring in shrinkage and cooling requirements is vital to producing high-quality components.
3. Ignoring Tolerances and Dimensional Accuracy: Failure to consider the required tolerances and dimensional accuracy can lead to components that do not fit or function correctly. Designers must be meticulous in defining these parameters and ensuring that the moulded components meet them.
4. Poor Gate and Runner Design: The gate and runner system in injection moulding is responsible for delivering the molten plastic into the mould cavity. Inadequate gate and runner design can cause issues like flow restrictions, material wastage, and cosmetic defects. It's crucial to optimize these elements for efficiency and quality.
5. Lack of Prototyping and Testing: Skipping the prototyping and testing phase can be a costly mistake. Prototyping allows designers to identify and rectify any design flaws before mass production, saving time and resources in the long run. Thoroughly testing prototypes ensures that the final components meet the desired standards.
How to Improve Efficiency with Precision Moulding Components
Efficiency is a crucial factor in the manufacturing industry. It not only affects the cost of production but also the quality of the final product. Here are some strategies for improving efficiency when working with precision moulding components:
1. Design Optimization
Efficiency begins with the design of moulding components. ACE places a strong emphasis on designing components that are not only functional but also easy to produce. Simplifying designs and reducing the number of complex features can significantly speed up the manufacturing process.
2. Material Selection
Choosing the right material for your moulding components is essential. ACE works closely with clients to select materials that are both cost-effective and meet the desired performance standards. The selection of the appropriate material can minimize wastage and reduce the need for extensive rework.
3. Advanced Moulding Techniques
Utilizing advanced moulding techniques can drastically improve efficiency. ACE invests in state-of-the-art machinery and technology to streamline the production process. This includes automated moulding machines, precision temperature control, and real-time monitoring for quality assurance.
4. Streamlined Workflow
Efficiency also depends on the workflow within the manufacturing facility. ACE follows Lean Manufacturing principles to eliminate waste, optimize production schedules, and reduce lead times. This approach ensures that moulding components are produced with minimal delays and bottlenecks.
5. Quality Control
Efficiency should not come at the cost of quality. ACE places a strong emphasis on quality control throughout the production process. Implementing stringent quality checks at every stage ensures that components meet or exceed industry standards.
Quality Assurance in Moulding Component Production: Best Practices
Maintaining consistent quality is paramount in the production of moulding components. ACE's commitment to quality assurance is a key factor in its success. Here are some best practices for ensuring top-notch quality in moulding component production:
1. Material Testing
Quality begins with the raw materials. ACE rigorously tests and inspects the materials before they are used in production. This ensures that only high-quality materials are used in the manufacturing process.
2. Process Control
Controlling the moulding process is critical. ACE uses a combination of automated systems and skilled operators to maintain precise control over temperature, pressure, and cycle times. This consistency results in components that meet tight tolerances.
3. Inspection and Testing
Components undergo thorough inspection and testing at multiple stages of production. This includes visual inspections, dimensional checks, and functional testing to ensure that the final product meets the required specifications.
4. Traceability
Traceability is essential in quality assurance. ACE maintains detailed records of each component's production history, making it possible to trace any issues back to their source. This traceability aids in identifying and rectifying problems quickly.
5. Continuous Improvement
Quality assurance is an ongoing process. ACE continuously reviews and improves its processes to eliminate defects and enhance overall quality. Regular training and feedback from the production team play a significant role in this improvement cycle.
Conclusion
In conclusion, mastering the art of moulding components, particularly injection moulding components, is a multi-faceted process that involves material selection, mould design, cooling and ejection mechanisms, injection parameters, and quality control. Working with a reputable moulding components manufacturer like ACE can provide valuable support and expertise in the journey to create high-quality moulded components. Additionally, being aware of common design mistakes and actively avoiding them is essential to achieve success in your projects. By adhering to best practices and continuously improving your design and manufacturing processes, you can produce top-notch moulded components that meet the highest standards of quality and performance.