Plastic injection mold maintenance is an essential aspect of the plastic manufacturing process. It ensures that the molds produce high-quality parts consistently and extends their lifespan. Proper maintenance of injection molds can prevent costly downtime and repairs while also reducing the risk of defective parts.
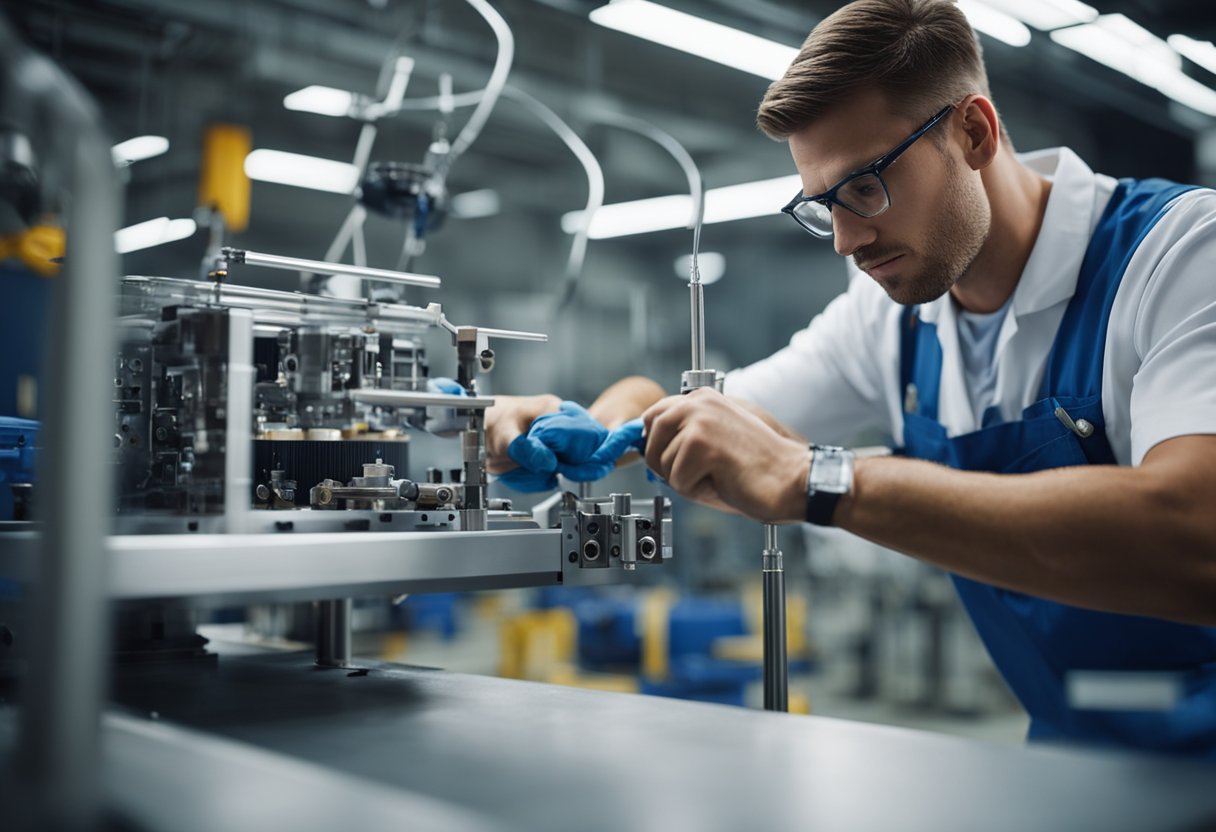
The maintenance of injection molds involves a variety of procedures, including cleaning, inspection, and repair. Regular cleaning of the molds helps to prevent buildup of contaminants, which can lead to defects in the finished product. Inspecting the molds for wear and tear, cracks, and other damage can help detect potential problems before they cause a breakdown, and timely repairs can prevent costly downtime.
In addition to avoiding downtime and repairs, proper maintenance of injection molds can also help reduce costs. By ensuring that the molds are functioning optimally, manufacturers can minimize material waste, which can be a significant expense. Proper maintenance can also help to extend the life of the molds, reducing the need for costly replacements.
Fundamentals of Plastic Injection Mold Maintenance
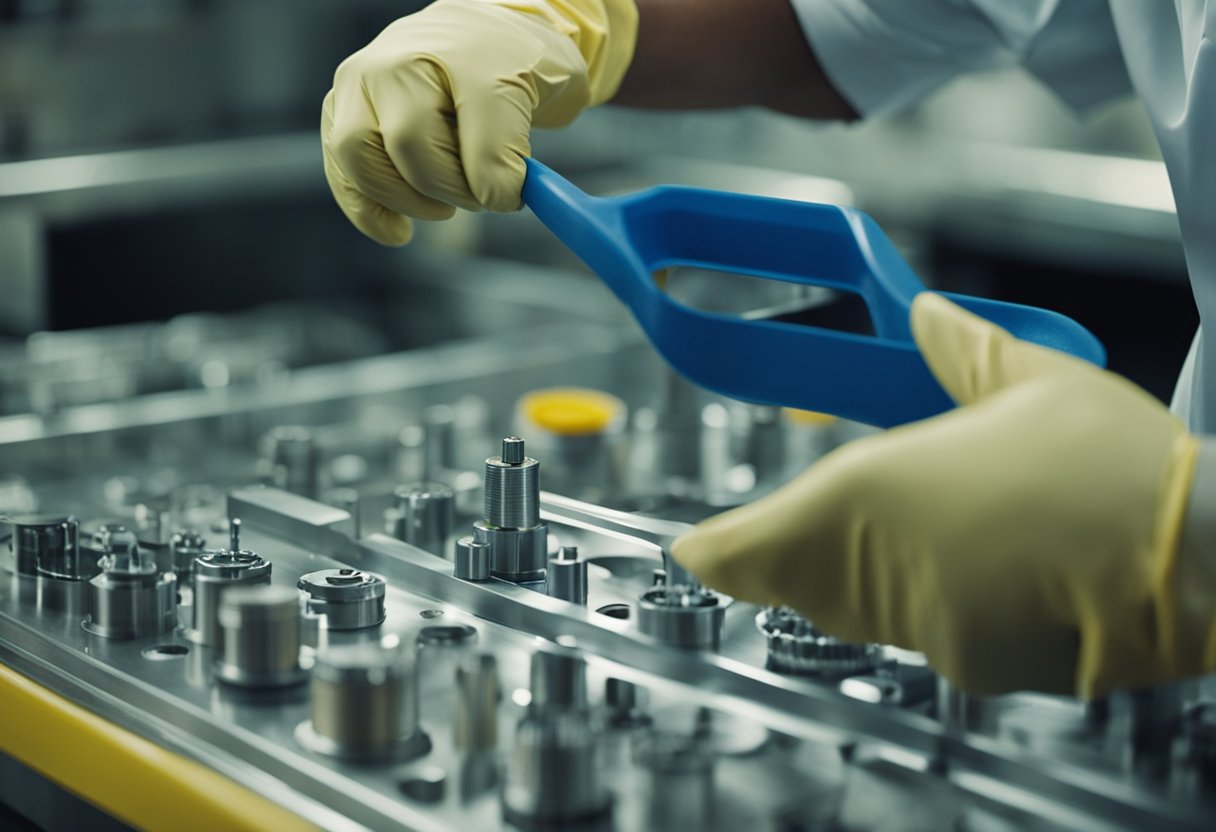
Proper maintenance of injection molds is crucial for the longevity and efficiency of the injection molding process. In this section, we will cover some of the fundamental aspects of plastic injection mold maintenance.
Understanding Mold Design
Before delving into mold maintenance, it is important to understand the basic design of an injection mold. Injection molds are typically made up of two halves, the cavity side, and the core side. The cavity side forms the outer surface of the molded part, while the core side forms the inner surface. The mold is designed with channels and gates to allow the molten plastic to flow into the cavity and core sides.
Material Considerations
The type of plastic material used in the injection molding process can have an impact on mold maintenance. For example, some materials may cause more wear and tear on the mold than others. Additionally, certain materials may require more frequent mold cleaning to prevent buildup and damage. It is important to consider the material being used when developing a maintenance plan for the mold.
Preventive Maintenance Strategies
Preventive maintenance is a critical aspect of mold maintenance. Regular cleaning and lubrication of the mold can help prevent wear and tear and extend the life of the mold. It is recommended to perform preventive maintenance on a monthly or quarterly basis, depending on the types of mold, material, and production schedule. This should include cleaning the mold regularly to remove debris and buildup, lubricating the mold to help prevent wear and tear on the moving parts, and inspecting the mold for damage.
In addition to preventive maintenance, regular maintenance of injection molds is also essential for the longevity and efficiency of the injection molding process. Regular maintenance can help identify potential issues before they become major problems, saving time and money in the long run.
Routine Maintenance Procedures
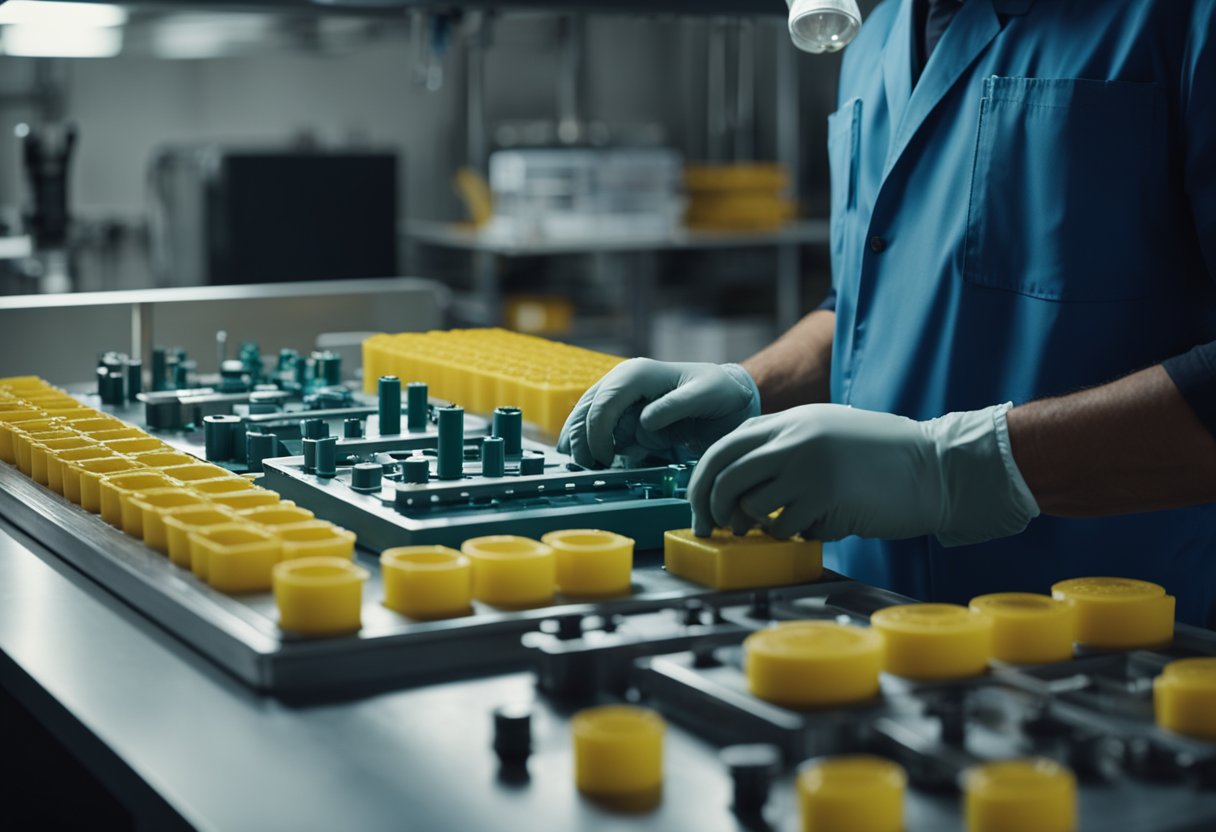
To ensure the longevity and efficiency of your plastic injection molds, it is crucial to follow a structured routine maintenance program. This program should include regular cleaning, lubrication, and wear and tear assessment. By incorporating these three maintenance procedures into your routine, you can minimize downtime, reduce scrap rates, and maximize the return on investment of your plastic injection molds.
Cleaning Protocols
Cleaning your injection molds is an essential maintenance procedure that should be performed after every production cycle. This helps to prevent contamination and ensures that your molds are ready for the next production run. The cleaning process should include:
- Removing all residual plastic from the molds using compressed air or other appropriate cleaning tools.
- Wiping down the molds with a clean cloth and a cleaning solution that is safe for the mold material.
- Inspecting the molds for any signs of damage or wear and tear.
Lubrication Techniques
Regular lubrication of the molds can help prevent wear and tear and extend their life. It is recommended to lubricate the molds after every cleaning cycle. The lubrication process should include:
- Applying a thin layer of lubricant to the mold surface using a clean cloth or brush.
- Wiping off any excess lubricant to prevent contamination of the plastic material.
Wear and Tear Assessment
Regular assessment of the wear and tear on your molds is crucial for identifying issues before they become major problems. This can help prevent production delays and minimize the need for costly repairs. The assessment process should include:
- Inspecting the molds for any signs of wear, such as cracks, chips, or scratches.
- Checking the alignment of the molds to ensure they are properly seated in the machine.
- Measuring the dimensions of the molds to ensure they are within the specified tolerances.
By following these routine maintenance procedures, you can extend the life of your plastic injection molds, maintain consistent part quality, and minimize the need for costly repairs.
Troubleshooting Common Mold Issues
If you encounter problems with your plastic injection mold, it's important to troubleshoot them as soon as possible to avoid costly downtime. Here are some common mold issues and how to troubleshoot them:
Surface Defects
Surface defects can be caused by a variety of factors, including improper mold design, poor mold maintenance, or incorrect injection molding parameters. Some common surface defects include:
- Scratches
- Weld lines
- Burn marks
- Sink marks
- Warping
To troubleshoot surface defects, start by checking the mold surface for any damage. If the mold surface is scratched or damaged, it may need to be repaired or replaced. If the mold is in good condition, check the injection molding parameters to ensure they are set correctly. Adjusting the injection speed or pressure may help reduce surface defects.
Flow Lines and Sink Marks
Flow lines and sink marks are caused by uneven cooling or filling of the mold cavity. Flow lines are visible lines on the surface of the part, while sink marks are depressions in the surface of the part.
To troubleshoot flow lines and sink marks, check the mold temperature and cooling system. Uneven cooling can cause flow lines and sink marks. Adjusting the cooling system or mold temperature may help reduce these defects. You can also try adjusting the injection speed or pressure to improve filling.
Ejector and Cooling System Problems
Ejector and cooling system problems can cause a variety of issues, including part sticking, warping, and cracking. Some common ejector and cooling system problems include:
- Sticking ejector pins
- Improper cooling channel design
- Insufficient cooling time
To troubleshoot ejector and cooling system problems, check the ejector pins for damage or wear. If they are sticking, they may need to be cleaned or replaced. Check the cooling channel design to ensure it is sufficient for the part. If the part is warping or cracking, it may need to cool for a longer period of time. Adjusting the cooling time or channel design may help reduce these defects.
Record-Keeping and Documentation
Maintaining accurate records and documentation is a critical component of effective injection molding machine maintenance. Detailed logs and the strategic use of these records can significantly enhance maintenance practices, leading to improved machine performance and increased production efficiency.
Maintenance Logs
Keeping a detailed maintenance log is essential for tracking the performance of your injection molding machine. This log should include information on regular maintenance tasks, such as cleaning and lubrication, as well as any repairs or replacements that have been made. By keeping a record of these tasks, you can identify patterns and trends in machine performance, allowing you to take proactive steps to prevent breakdowns and extend the life of your equipment.
In addition to tracking routine maintenance, your log should also include any unexpected downtime or production delays. By documenting these incidents, you can identify the root cause of the problem and take corrective action to prevent similar issues from occurring in the future.
Quality Control Records
Along with maintenance logs, it's also important to keep detailed records of your injection molding machine's quality control measures. This includes information on production runs, part quality, and any defects or rejects that occur during the manufacturing process.
By analyzing this data, you can identify areas for improvement in your production process and take corrective action to reduce defects and improve overall product quality. You can also use this information to track the performance of individual molds and identify any that may need maintenance or repair.
Overall, maintaining accurate records and documentation is essential for effective injection molding machine maintenance. By keeping detailed logs of maintenance tasks and quality control measures, you can identify patterns and trends in machine performance, take proactive steps to prevent breakdowns, and improve overall production efficiency.
Advanced Maintenance Techniques
When it comes to plastic injection mold maintenance, advanced techniques can help extend the life of your molds and improve their performance. Here are some advanced maintenance techniques you can consider:
Laser Welding Applications
Laser welding is a technique that can be used to repair damaged or worn mold components. It involves using a laser to melt the surface of the component and then adding material to build it up. This technique can be used to repair small cracks, chips, and other types of damage. Laser welding is precise, fast, and can be used on a wide range of materials, including steel, aluminum, and copper.
Coating Technologies
Coating technologies can be used to protect mold surfaces from wear and damage. There are several types of coatings available, including nitride coatings, chrome coatings, and diamond-like coatings. Nitride coatings are commonly used because they are hard, wear-resistant, and can withstand high temperatures. Chrome coatings are also used because they are corrosion-resistant and can improve part release. Diamond-like coatings are the most advanced and can provide the best wear resistance.
3D Printing for Mold Repair
3D printing is a technology that can be used to repair molds quickly and cost-effectively. It involves using a 3D printer to create a replica of the damaged component and then using it to replace the damaged part. This technique can be used to repair small components, such as pins and bushings, and can be done in a matter of hours. 3D printing can also be used to create new molds, which can be useful if you need to make changes to your product design.
By using these advanced maintenance techniques, you can extend the life of your molds and improve their performance. However, it is important to note that these techniques require specialized knowledge and equipment. If you are not familiar with these techniques, it is best to work with a professional who can help you implement them properly.