Plastic tooling is an essential process in manufacturing, helping businesses produce high-quality plastic parts efficiently. However, the cost of tooling can be a significant investment, especially for startups and small businesses. Finding a cost-effective plastic tooling approach can reduce production expenses while maintaining quality and efficiency.
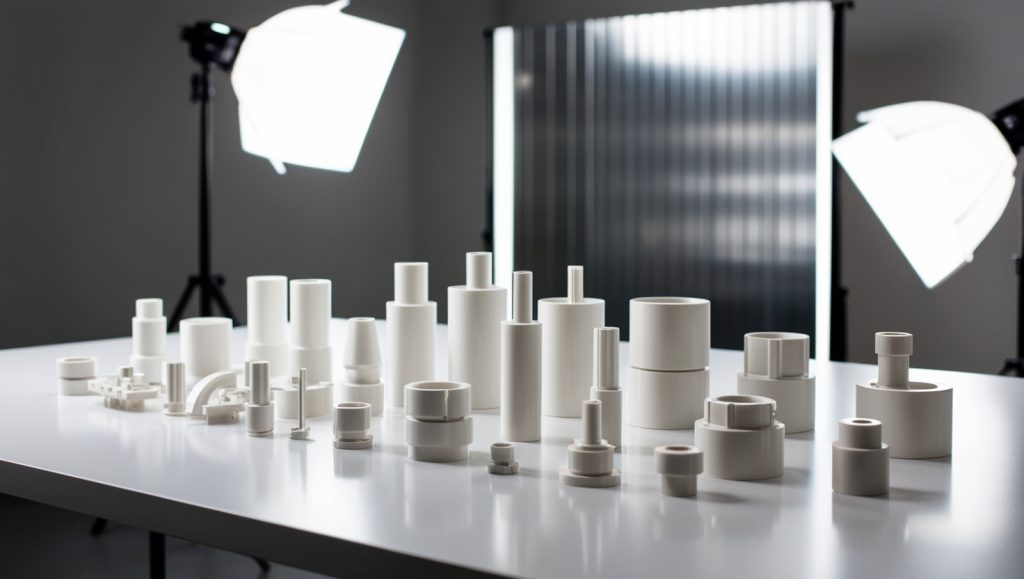
In this article, we’ll explore cost-effective plastic tooling strategies, factors influencing tooling costs, and ways to optimize your investment in plastic part production. Additionally, we will dive deeper into advanced manufacturing techniques, explore alternative materials, and discuss long-term cost-saving measures to help businesses make informed decisions.
What is Plastic Tooling?
Plastic tooling refers to the design and manufacturing of molds used in plastic injection molding and other plastic-forming processes. These molds create identical plastic parts by shaping melted plastic into a desired form. The most common plastic tooling methods include:
- Injection Molding – The most widely used method, where melted plastic is injected into a mold cavity and cooled into a solid part.
- Blow Molding – Used for hollow plastic parts, such as bottles and containers.
- Compression Molding – Involves compressing plastic materials into a preformed mold.
- Rotational Molding – Suitable for large, hollow plastic parts.
- Thermoforming – A cost-effective alternative for certain applications, involving heating plastic sheets and forming them over a mold.
Each method has different cost structures and applications, making it essential to select the right approach for your project. By understanding the intricacies of each method, manufacturers can tailor their tooling choices to best suit production needs and budget constraints.
Factors Influencing Plastic Tooling Costs
Several factors impact the cost of plastic tooling, including:
Material Selection
- Tooling Materials: The mold’s material significantly affects cost. Steel molds last longer but are expensive, while aluminum molds are cheaper but wear out faster.
- Plastic Resin: The type of plastic used for production affects tooling costs. High-performance resins may require stronger molds, increasing expenses.
- Alternative Materials: In some cases, hybrid tooling materials like composite molds can provide a balance between cost and longevity.
Mold Complexity
- Simple molds with basic geometries cost less than complex multi-part molds with intricate details.
- Features like undercuts, threads, and internal channels add complexity and raise tooling costs.
- Optimizing mold complexity through strategic design changes can reduce production costs while maintaining functionality.
Production Volume
- Higher production volumes justify the cost of expensive, high-quality molds.
- Low-volume production can use more affordable molds, such as soft tooling options like silicone or 3D-printed molds.
- Scalability considerations play a significant role in determining which tooling strategy is most cost-effective.
Lead Time and Speed
- Expedited tooling processes cost more due to additional labor and materials.
- Longer lead times allow for optimized tooling costs by using more affordable processes.
- Lean manufacturing techniques can help minimize lead time without inflating costs.
Manufacturing Location
- Overseas tooling can be cheaper, but quality control and shipping costs must be considered.
- Domestic tooling often ensures higher precision and faster communication but comes at a higher price.
- Hybrid production models that combine domestic prototyping with offshore mass production can be a cost-saving alternative.
Strategies for Cost-Effective Plastic Tooling
Choose the Right Tooling Material
Selecting the right mold material can reduce costs without sacrificing quality. Common options include:
- Aluminum Molds: Lower upfront costs and quicker production, ideal for low-volume runs.
- Steel Molds: Higher durability and precision for high-volume production but more expensive.
- Hybrid Molds: A combination of aluminum and steel for balanced performance and cost savings.
- 3D-Printed Molds: Emerging as a viable low-cost solution for prototyping and small batch production.
Optimize Design for Manufacturability (DFM)
Reducing mold complexity lowers tooling costs. Design for Manufacturability (DFM) principles include:
- Avoiding unnecessary undercuts and complex features.
- Using uniform wall thickness to prevent defects.
- Minimizing the number of mold cavities if not needed.
- Designing parts that can be ejected easily without additional tooling components.
- Incorporating automation-friendly designs to reduce manual handling costs.
Utilize Rapid Prototyping and 3D-Printed Molds
- 3D printing allows for affordable prototype molds before investing in expensive tooling.
- Additive manufacturing techniques reduce lead times and enable quick design iterations.
- Silicone molds or low-cost urethane casting can be used for short-run production before full-scale injection molding.
- Hybrid rapid tooling techniques integrate traditional machining with 3D printing to reduce costs and lead times.
Consider Soft Tooling for Low-Volume Production
- Silicone and aluminum molds are cheaper alternatives to hard steel molds.
- CNC-machined molds provide mid-range cost solutions for short production runs.
- Vacuum forming and urethane casting help lower initial tooling investment for low production quantities.
- Reusable master molds allow for cost-effective small-batch runs.
Leverage Modular Tooling
- Interchangeable mold inserts reduce costs for producing multiple part variations.
- Family molds allow different parts to be produced in a single mold setup.
- Multi-cavity molds reduce per-part cost at higher production volumes.
- Standardized mold bases can be used across multiple projects to save money.
Work with an Experienced Tooling Partner
Choosing a reliable tooling manufacturer ensures:
- Efficient mold design that minimizes costs.
- High-quality materials that extend mold lifespan.
- Faster production times and fewer revisions.
- Post-tooling support, reducing maintenance costs over time.
- Access to cost-saving insights from industry experts.
Optimize Cooling and Cycle Times
- Conformal cooling channels can improve cooling efficiency, reducing cycle times.
- Using proper ejection systems prevents defects and speeds up production.
- Automation in mold handling can reduce labor costs and improve efficiency.
- Advanced temperature control techniques enhance overall process efficiency.
Conclusion: Maximizing Cost Savings in Plastic Tooling
Reducing plastic tooling costs does not mean sacrificing quality. By selecting the right materials, optimizing design, and leveraging alternative tooling techniques, businesses can create high-quality plastic parts without exceeding budget limits.
Key Takeaways:
- Material choice and mold complexity significantly impact costs.
- Design for Manufacturability (DFM) reduces unnecessary tooling expenses.
- Soft tooling and 3D-printed molds are excellent for low-volume production.
- Working with an experienced tooling partner ensures efficiency and durability.
- Optimizing cooling and cycle times can further cut production costs.
- Hybrid manufacturing and alternative tooling approaches provide additional savings.
By implementing these strategies, manufacturers can achieve cost-effective plastic tooling and improve their bottom line. If you’re looking for the best approach for your specific project, consulting with an expert tooling provider can help tailor the best solution for your needs.
FAQ:
What is the most cost-effective material for plastic tooling?
The most cost-effective material depends on production volume and part complexity. Aluminum molds are ideal for low to medium production runs due to their lower cost and faster machining times, while steel molds are better suited for high-volume production due to their durability.
How can I reduce the cost of plastic tooling without sacrificing quality?
You can reduce costs by optimizing Design for Manufacturability (DFM), using 3D-printed or soft tooling for prototypes, selecting modular tooling approaches, and working with an experienced tooling manufacturer who can guide material and process selection efficiently.
Is 3D printing a viable option for plastic tooling?
Yes, 3D-printed molds are a viable option for low-volume production and prototyping. While they may not be as durable as aluminum or steel molds, they provide a cost-effective and quick alternative for testing and short production runs.
What are the trade-offs between domestic and overseas tooling manufacturers?
Domestic manufacturers offer better quality control, faster lead times, and easier communication, but at a higher cost. Overseas manufacturers, especially in China and India, offer lower tooling costs, but you may face longer shipping times, potential quality issues, and higher logistics expenses.
How can modular tooling help save costs?
Modular tooling, such as interchangeable mold inserts and family molds, allows manufacturers to produce multiple part variations using the same base mold. This approach reduces upfront costs, minimizes production downtime, and enhances flexibility in product design.