Custom molds for plastic injection molding are essential for producing high-precision plastic components tailored to unique designs. Unlike standard molds, custom molds provide manufacturers with better accuracy, efficiency, and long-term cost savings. They are widely used in automotive, medical, electronics, and packaging industries, where consistency is critical.
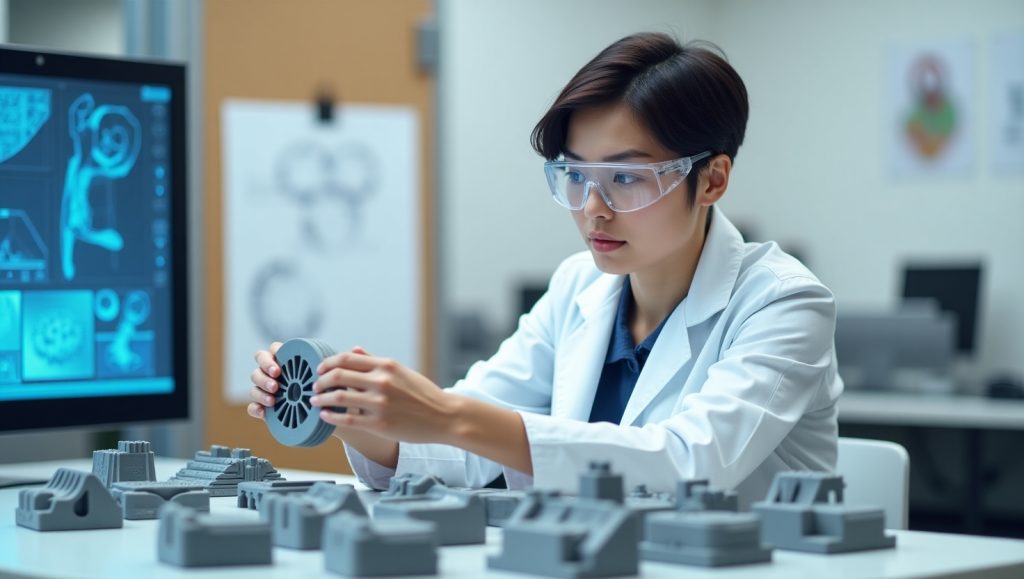
Manufacturers investing in custom molds must consider design, material selection, production costs, and manufacturing techniques to ensure optimal performance and affordability. This guide explores how custom molds are designed, manufactured, and optimized for cost efficiency.
Why are they essential for high-precision manufacturing?
Industries that require tight tolerances and consistent part quality depend on custom molds. A poorly designed mold can lead to defects such as warping, shrinkage, or improper fits, which increase production waste and costs.
Pain Point: Manufacturers using generic molds often face higher rejection rates and post-production modifications, leading to delays and financial losses.
Example: An automotive supplier once struggled with inconsistent part dimensions due to an off-the-shelf mold. After investing in a custom mold, their defect rate dropped by 35%, reducing overall costs.
Key industries that rely on custom injection molds
- Automotive – Produces dashboards, bumpers, and engine components.
- Medical – Manufactures syringes, surgical instruments, and prosthetic parts.
- Consumer Electronics – Creates precise casings and small internal components.
- Packaging – Develops custom bottles, food containers, and protective enclosures.
Understanding Custom Injection Molds
How custom molds differ from standard molds
- Tailored Design – Custom molds match exact product specifications, whereas standard molds offer limited flexibility.
- Higher Precision – Designed to meet strict dimensional tolerances, reducing defects.
- Material-Specific Engineering – Custom molds are optimized for specific plastic resins, preventing production issues like warping or brittleness.
Pain Point: Businesses using standard molds often struggle with inconsistent part quality, leading to rework and scrap losses.
Example: A medical device company initially used a generic mold for syringe manufacturing. The inconsistent wall thickness caused frequent breakage under pressure, forcing them to invest in a custom mold that improved product durability and reliability.
Components of a custom mold
- Cavity and Core – Define the external and internal shape of the molded part.
- Runner System – Channels that guide molten plastic into the mold cavity.
- Cooling System – Regulates temperature to prevent defects and speed up production cycles.
- Ejection System – Pushes the finished part out of the mold without damaging it.
Each component plays a vital role in ensuring a defect-free molding process.
Benefits of using custom molds for production efficiency
- Reduced Cycle Times – Optimized cooling systems increase production speed.
- Lower Material Waste – Custom mold designs minimize excess plastic usage.
- Improved Part Strength – Precision engineering enhances product durability.
Pain Point: Inefficient molds lead to longer production times and higher operational costs.
Example: A packaging manufacturer reduced cycle time by 20% after upgrading to a custom mold with an optimized cooling system, allowing them to increase output without raising labor costs.
The Custom Mold Design and Manufacturing Process
Product design and specification requirements
Custom mold design starts with a detailed 3D model, defining the product’s dimensions, wall thickness, and structural integrity. Engineers consider:
- Tolerance levels – Ensuring parts fit properly in assemblies.
- Material compatibility – Selecting the right plastic resin for performance and durability.
- Undercuts and complex geometries – Designing molds that allow easy ejection without defects.
Pain Point: Poorly designed molds result in costly mold rework and production delays.
Example: A consumer electronics manufacturer initially designed a mold with deep undercuts, making ejection difficult. Redesigning with a draft angle adjustment eliminated the issue and reduced cycle times by 15%.
Mold material selection: steel, aluminum, and hybrid options
- Steel Molds – Best for high-volume production, highly durable but expensive.
- Aluminum Molds – Lower cost, suitable for prototyping and low-volume runs.
- Hybrid Molds – Combine steel and aluminum for a balance of cost and durability.
Pain Point: Choosing the wrong mold material leads to early wear and frequent replacements.
Example: A startup producing small plastic components opted for an aluminum mold to save costs but found it wore out quickly under high-volume production. Switching to a hybrid mold extended its lifespan without significantly increasing costs.
CNC machining and precision manufacturing techniques
Custom molds are manufactured using high-precision machining processes, including:
- CNC Machining – Ensures precise cutting and shaping of mold cavities.
- Electrical Discharge Machining (EDM) – Used for complex geometries and fine details.
- Surface Finishing – Polishing and texturing to enhance product appearance.
Pain Point: Low-precision molds result in dimensional inconsistencies, requiring costly post-processing.
Example: A toy manufacturer used an imprecise mold that created parts requiring excessive trimming. Investing in high-precision CNC machining eliminated this issue, improving productivity and reducing labor costs.
Testing and validation through prototyping
Before full-scale production, molds undergo rigorous testing to ensure:
- Proper part formation – No warping, sink marks, or flash.
- Efficient cooling and ejection – Preventing cracks and deformations.
- Durability under production conditions – Ensuring the mold withstands multiple cycles.
Prototyping methods include:
- 3D Printing – Produces sample molds quickly for early-stage testing.
- Soft Tooling – Temporary molds made from silicone or urethane for small production runs.
Pain Point: Skipping prototyping leads to expensive mold modifications later.
Example: A medical device company invested in a soft tooling prototype, allowing them to identify design flaws before committing to an expensive steel mold, saving tens of thousands of dollars in rework costs.
Cost Factors in Custom Mold Manufacturing
The cost of manufacturing a custom mold depends on various factors, including design complexity, material selection, production volume, and location of manufacturing. Understanding these factors can help businesses plan their investment efficiently and avoid unexpected expenses.
How complexity and part geometry impact cost
The more complex a mold design, the higher the cost of manufacturing. Features such as undercuts, thin walls, and intricate details require additional machining time, advanced tooling, and skilled labor, increasing overall production costs. Simple designs with uniform wall thickness and fewer intricate features help reduce costs.
Differences in cost between high-volume and low-volume production
- Low-volume production: Requires soft tooling such as aluminum molds, which are cheaper but less durable.
- High-volume production: Steel molds are more expensive upfront but last longer, making them more cost-effective over time.
For businesses that produce different part variations in small quantities, modular molds offer an alternative by allowing different components to be produced from a single mold base.
The effect of material choice on pricing
- Steel molds: High cost but durable and suitable for mass production.
- Aluminum molds: Lower cost, faster to produce, but wears out quickly.
- Hybrid molds: A mix of steel and aluminum, offering a balance between cost and durability.
Choosing the right material depends on production needs, product lifespan, and budget constraints.
Domestic vs. overseas manufacturing: pros and cons
- Domestic manufacturing: Higher cost but offers better quality control, faster communication, and lower shipping risks.
- Overseas manufacturing: Lower initial costs but may involve longer lead times, higher shipping fees, and potential quality inconsistencies.
Businesses should weigh these factors based on their project timeline, quality requirements, and cost objectives.
Optimizing Custom Mold Design for Cost Efficiency
Reducing manufacturing costs without compromising quality is crucial in custom mold production. Here are some strategies to optimize mold design and lower expenses.
Reducing unnecessary features to lower expenses
Removing excessive undercuts, complex geometries, and unnecessary details can significantly lower machining time and material usage, leading to cost savings. Ensuring uniform wall thickness also prevents defects and reduces material waste.
Modular molds for multi-part variations
Modular molds allow manufacturers to produce multiple part variations from a single base mold by using interchangeable inserts. This approach reduces tooling costs and shortens production timelines, making it an ideal solution for companies producing variations of a product.
Using 3D printing for rapid prototyping before final mold production
3D printing is a cost-effective method for testing mold designs before committing to expensive steel or aluminum molds. This technique allows manufacturers to detect design flaws early, optimize mold cooling systems, and improve part geometry, minimizing costly revisions in the later stages of production.
Partnering with experienced mold manufacturers for better ROI
Working with an experienced mold manufacturer ensures that the design is optimized for efficiency. They can provide cost-saving insights, recommend the best materials, and suggest alternative tooling approaches that reduce expenses while maintaining quality.
Case Study: How a Manufacturer Reduced Costs with Custom Molds
A consumer electronics company was experiencing high production costs due to frequent mold changes for different product versions. They implemented modular molds and automated their manufacturing process, which resulted in significant cost savings.
Implementation of modular molds and process automation
The company switched to a single mold base with interchangeable inserts, reducing the need for multiple molds. They also introduced an automated ejection and cooling system, improving efficiency.
Achieved improvements in speed and defect reduction
- 30% faster production cycles by eliminating the need for frequent mold changes.
- 20% reduction in material waste due to optimized mold design.
- Lower overall manufacturing costs, saving the company over $500,000 annually.
This case study highlights how businesses can reduce costs and increase efficiency by adopting strategic mold design and automation solutions.
Challenges in Custom Mold Tooling and How to Overcome Them
Manufacturers face several challenges in custom mold tooling that can affect production efficiency and costs.
Common issues like design flaws, cooling inefficiencies, and material failures
- Design flaws: Poorly designed molds lead to defective parts, high rejection rates, and frequent rework.
- Cooling inefficiencies: Improper cooling channels increase cycle time, leading to slower production.
- Material failures: Choosing the wrong mold material can result in early wear, increased maintenance, and replacement costs.
Solutions for reducing lead times and improving mold longevity
- Optimize mold design early in the process to prevent rework.
- Use conformal cooling to enhance cooling efficiency and reduce cycle time.
- Select durable materials that match production volume requirements.
The importance of proper maintenance and reusability
Regular mold maintenance, including cleaning, lubrication, and repair, extends the mold's lifespan and prevents costly downtime. Reusable mold components, such as interchangeable inserts, also help lower long-term expenses.
Future Trends in Custom Mold Tooling
As technology advances, several trends are shaping the future of custom mold tooling.
The role of AI in mold design and defect prediction
Artificial intelligence is being used to analyze mold designs, predict potential defects, and optimize cooling systems. AI-driven automation reduces errors and increases production efficiency.
The shift toward sustainable and biodegradable mold materials
With growing environmental concerns, manufacturers are exploring eco-friendly mold materials such as biodegradable plastics and recycled resins. These alternatives help reduce plastic waste while maintaining production efficiency.
Advancements in 3D printing for on-demand mold creation
3D printing continues to evolve, making it possible to create functional molds with minimal lead time. This technology is especially useful for low-volume production and prototyping, reducing costs and accelerating the development process.
Conclusion and Final Tips
Reducing costs in custom mold manufacturing requires a combination of efficient design, proper material selection, and advanced production techniques. By optimizing mold design, using modular tooling, leveraging 3D printing, and selecting the right manufacturing partner, businesses can increase production efficiency while lowering expenses.
When choosing a mold manufacturer, consider experience, material options, production timelines, and post-production support. Investing in high-quality custom molds results in better product consistency, longer mold lifespan, and improved return on investment.
Frequently Asked Questions
How much do custom molds for injection molding cost?
The cost of a custom mold can range from $5,000 to $100,000+, depending on material choice, complexity, and production volume.
What is the best material for plastic molds?
- Steel: Best for high-volume production due to durability.
- Aluminum: Suitable for prototyping and low-volume runs.
- Hybrid molds: A combination of steel and aluminum for balanced performance.
Can 3D printing be used for injection mold tooling?
Yes, 3D printing is widely used for rapid prototyping and low-volume production. It helps identify design flaws early and reduces tooling costs.
How long does it take to manufacture a custom mold?
Production times typically range from 4 to 12 weeks, depending on mold complexity and manufacturing workload.
What industries benefit the most from custom molds?
Industries such as automotive, medical, consumer electronics, and packaging rely on custom molds for high-precision, mass production of plastic parts.
This guide provides insights into cost-saving strategies, production challenges, and future trends in custom mold tooling, helping businesses make informed decisions for their plastic injection molding needs.