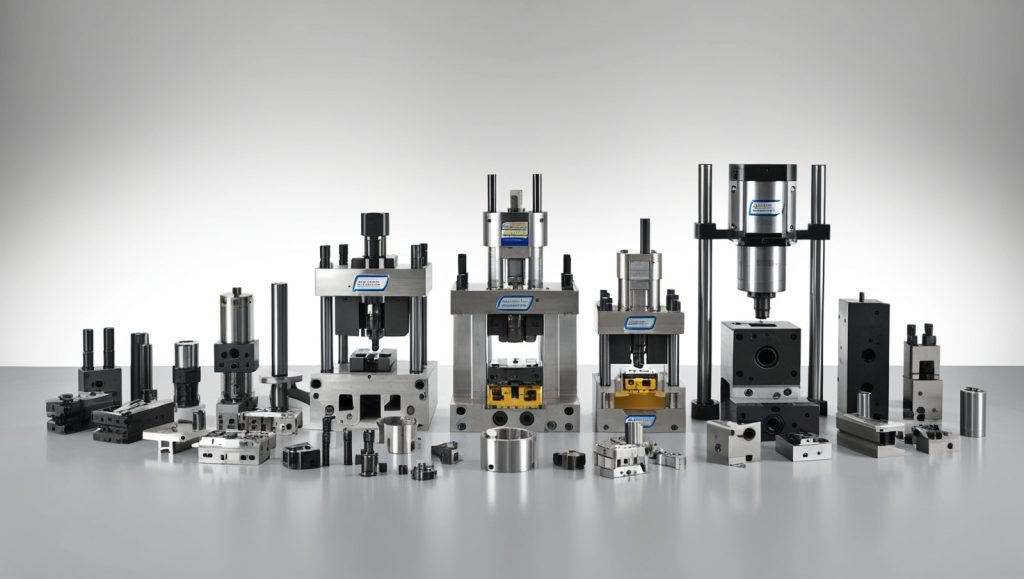
Have you ever wondered how plastic toys, containers, or even car parts are made? They all come from molds! Molds are special tools that shape melted plastic into the products we use every day. Custom tooling for plastic molds means making these molds in a way that fits the exact needs of a product. It helps companies create strong, high-quality plastic parts that look and work just right.
In this blog, we will explore how custom molds are designed, what materials are used, and why they are important. We will also look at how these molds are made, how they are cooled, and how much they cost. Finally, we will check out how to take care of molds and what exciting new technology is being used in mold-making today. Whether you are just curious or want to learn more about manufacturing, this guide will help you understand the world of plastic molds in a fun and simple way.
What is Custom Tooling for Plastic Molds?
Custom tooling for plastic molds means designing and making special molds that fit a product’s exact shape and size. Instead of using the same mold for everything, companies create custom molds to ensure their products come out just right. These molds are used in a process called injection molding, where melted plastic is poured into the mold and cooled into a solid shape.
Think of it like making cookies with a cookie cutter. If you want star-shaped cookies, you need a star-shaped cutter. In the same way, if a company wants a plastic bottle cap, they need a mold shaped like a cap. Custom tooling allows them to create molds that match the product’s design perfectly.
Molds are used in many industries. Car manufacturers use molds to make dashboards and small plastic parts. Toy companies use them to shape action figures and building blocks. Even medical devices like syringes and pill bottles come from molds. Custom tooling ensures that each plastic piece is made with precision, strength, and the right appearance.
How Molds Are Designed
Before a mold is made, engineers use special computer programs to design it. These programs help them create a 3D model of the mold, making sure every detail is correct. The mold needs to be strong, have the right thickness, and allow the plastic to flow evenly inside.
Once the design is ready, engineers run a mold flow analysis. This test helps them see how melted plastic will move inside the mold. It is important to prevent problems like air bubbles, cracks, or uneven shapes. If the mold design has any issues, changes can be made before it is built.
After testing, the final design is sent to a manufacturing workshop. The mold is made from metal, usually steel or aluminum, because they can handle high heat and pressure. Once the mold is built, it is polished and tested. If everything looks good, it is ready for use in making plastic products. Good mold design helps companies save time and money by reducing waste and ensuring quality products.
Different Types of Molds
There are different types of molds, and each one is made for a specific purpose. Some molds are used for testing new product designs, while others are built for mass production.
Prototype molds are used when a company wants to test a product before making thousands of copies. These molds are usually made from aluminum, which is cheaper and easier to shape. However, they do not last as long as steel molds.
Production molds are used when a company is ready to make large numbers of the same product. These molds are made from strong steel, which can last for years without wearing out.
Some molds are made with multiple cavities, meaning they can produce several plastic parts at the same time. This helps save time and money. Family molds are another special type where different but related parts are made in one mold. This is useful when a product has multiple small parts that need to be made together.
Materials Used in Molds
Molds need to be strong enough to handle high temperatures and pressure. The most common materials used for molds are aluminum and steel.
Aluminum molds are lightweight and easy to shape. They are perfect for small production runs or testing new products. However, aluminum molds wear out quickly and are not suitable for long-term use.
Steel molds are the best choice for mass production. They are durable and can last for thousands or even millions of cycles. Steel molds can handle high heat without getting damaged. Some steel molds have special coatings to make them even stronger and last longer.
Other materials like beryllium copper are sometimes used for specific parts of the mold. Beryllium copper helps with cooling because it transfers heat quickly. This is useful for molds that need to produce plastic parts in fast cycles.
How Molds Are Made
Once the design is ready, the mold-making process begins. First, a block of aluminum or steel is cut into the rough shape of the mold. Then, machines called CNC machines carve out the exact details needed for the mold.
For more complex parts, a process called EDM (Electrical Discharge Machining) is used. This process uses electric sparks to shape the mold with high precision. After machining, the mold is polished and checked for any flaws.
If needed, special coatings or finishes are added to improve the mold’s durability. Finally, the mold is tested by injecting plastic into it. If the product comes out perfect, the mold is ready for full production.
Cooling and Venting in Molds
Cooling is one of the most important steps in the mold-making process. After the plastic is injected, it needs to cool and harden before being removed. The faster the cooling process, the quicker new parts can be made.
Some molds have special cooling channels built inside them. These channels allow water or other cooling liquids to flow through and absorb heat. Faster cooling means less production time and lower costs.
Venting is also important. If air gets trapped inside the mold, it can create defects like bubbles or weak spots in the plastic. Molds have tiny vents that let air escape while the plastic fills the mold. Good venting ensures that the final product comes out smooth and strong.
Cost and Maintenance of Molds
Custom molds can be expensive to make. A simple mold can cost a few thousand dollars, while a complex mold can cost hundreds of thousands. However, the investment pays off because a high-quality mold can last for years and produce millions of parts.
To keep molds working well, they need regular maintenance. Molds should be cleaned after every use to remove plastic residue. They also need lubrication to prevent rust and wear. Small repairs should be done immediately to avoid bigger problems.
Future of Custom Tooling
Technology is making mold-making even better. 3D printing is now being used to create some molds quickly and cheaply. Artificial intelligence is helping engineers design better molds by predicting possible issues before production starts.
Another exciting trend is the use of smart molds with sensors that monitor temperature and pressure in real time. This helps manufacturers make adjustments and reduce waste.
In the future, molds will become even more efficient, reducing costs and improving product quality. With new technology, plastic products will be made faster, stronger, and more environmentally friendly.
Conclusion
Custom tooling for plastic molds is an important part of making plastic products. From toys to car parts, molds shape the world around us. Designing and making molds takes time and skill, but it ensures that plastic products are high-quality and durable.
By using the right materials, proper cooling, and regular maintenance, molds can last for years and produce millions of items. With new technology, the future of mold-making looks even brighter. Custom molds will continue to shape our everyday lives in amazing ways!