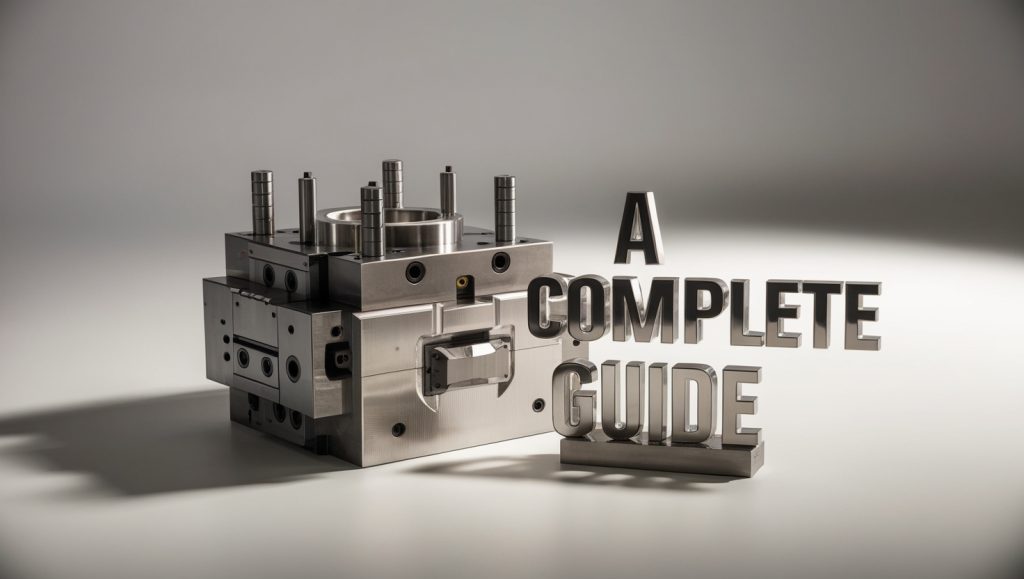
Custom plastic mold tooling is a key process in modern manufacturing, enabling the production of high-quality, precisely engineered plastic components. This process allows manufacturers to create customized molds that fit unique design specifications, ensuring accuracy, repeatability, and efficiency in large-scale production. The demand for custom molds is high across industries such as automotive, medical devices, packaging, consumer electronics, and industrial applications. By utilizing custom tooling, businesses can optimize production speed, reduce waste, and maintain consistency in their final products.
Mold tooling plays a crucial role in achieving smooth and defect-free plastic parts. Without a properly designed mold, manufacturers may face production inefficiencies, product inconsistencies, or higher defect rates. With advances in technology, custom mold tooling now integrates cutting-edge computer-aided design (CAD), CNC machining, and mold flow analysis to improve precision. These advancements have led to faster turnaround times and enhanced performance in the injection molding industry.
One of the major advantages of custom plastic mold tooling is its ability to provide tailored solutions based on the specific needs of a product. Unlike standard molds, custom molds are designed with unique geometries, complex features, and optimized cooling channels to enhance performance. Manufacturers can also select the appropriate mold material, whether steel or aluminum, based on their production volume and budget. With these options available, businesses can ensure that they receive cost-effective and high-performing mold solutions for their projects.
Understanding Plastic Mold Tooling
Plastic mold tooling is the process of creating molds that are used in the injection molding process to shape plastic parts. This involves the precise machining and assembly of mold components that define the final structure of a product. The design and engineering of a mold determine the quality, durability, and functionality of the plastic part it produces. High-quality tooling ensures smooth production runs, minimal defects, and improved efficiency in manufacturing.
A mold consists of several key components that work together to create a finished plastic part. The core and cavity are the primary elements that define the shape of the molded part. These two components come together to form the mold’s interior, where molten plastic is injected and cooled. The runner system directs the flow of molten plastic into the mold cavity, ensuring even distribution of material. The cooling system is another critical element, as it regulates the temperature of the mold to prevent warping and defects. Finally, ejector pins help remove the finished product from the mold after it has solidified.
Custom mold tooling differs from standard mold tooling in that it is specifically designed for unique product requirements. Standard molds are typically pre-designed and used for generic parts, while custom molds are built to accommodate intricate geometries and complex features. Custom molds allow manufacturers to produce parts with specific design elements, tighter tolerances, and enhanced material properties. By tailoring the mold to the exact specifications of a product, manufacturers can achieve better precision and performance in the final plastic components.
Types of Custom Mold Tooling
Custom mold tooling comes in several variations, each serving different purposes in the manufacturing process. The choice of mold type depends on factors such as production volume, complexity, and material requirements. One of the most commonly used mold types is the prototype mold, which is designed for low-volume production and product testing. These molds allow manufacturers to create early-stage samples before committing to full-scale production. Prototype molds are often made from aluminum due to its fast machining capabilities and cost-effectiveness.
Bridge tooling is another important category in custom mold manufacturing. It serves as an intermediate step between prototyping and full-scale production, providing manufacturers with a temporary mold solution while finalizing product designs. Bridge molds are typically used when demand increases unexpectedly or when minor adjustments are still being made to the product. They offer a balance between cost and durability, allowing businesses to test their designs in real-world applications before investing in long-term production molds.
For high-volume manufacturing, production molds are the preferred choice. These molds are built to withstand millions of cycles, making them ideal for mass production. Production molds are typically constructed from hardened steel, ensuring durability and extended lifespan. To further optimize production efficiency, multi-cavity molds and family molds are often utilized. Multi-cavity molds allow manufacturers to produce multiple identical parts in a single cycle, significantly reducing cycle time and costs. Family molds, on the other hand, enable the production of different parts within the same mold, making them ideal for assembly-based applications.
Mold Design Process
The mold design process is a crucial phase in custom mold tooling, as it determines the performance, efficiency, and longevity of the mold. The first step in mold design involves a detailed review of the product’s requirements through a process known as Design for Manufacturability (DFM). This analysis ensures that the part’s geometry, thickness, and material selection are optimized for injection molding. Engineers evaluate potential design flaws that could lead to defects such as warping, sink marks, or flow issues. By addressing these concerns early, manufacturers can reduce costs and improve overall production quality.
Material selection for the mold is another important consideration in the design process. Steel and aluminum are the most commonly used materials for mold construction. Steel molds are highly durable and capable of withstanding high-pressure injection cycles, making them suitable for large-scale production. Aluminum molds, while less durable, offer faster machining times and are often used for prototyping or low-volume runs. The choice of mold material depends on the expected production volume, budget constraints, and required part tolerances.
Before the final mold is produced, prototyping and testing play a critical role in refining the design. Rapid prototyping methods, such as 3D printing and CNC machining, allow manufacturers to create test samples quickly. These prototypes enable designers to assess part fit, function, and aesthetics before committing to full-scale production. Testing also helps verify mold performance, ensuring that the final product meets industry standards and customer expectations. Through iterative improvements and technological advancements, the mold design process continues to evolve, enabling manufacturers to create high-quality, cost-effective tooling solutions.
Manufacturing Process for Custom Molds
Once the mold design is finalized, the manufacturing process begins. Precision and attention to detail are crucial to ensure that the mold meets the required specifications and performs efficiently in production. The first step in manufacturing a custom mold is material selection. High-quality steel and aluminum are commonly used, with the choice depending on factors such as durability, production volume, and cost. Steel molds, particularly hardened tool steel, offer superior longevity and are ideal for high-volume production. Aluminum molds, on the other hand, are more cost-effective for low-volume or prototype applications.
CNC machining plays a vital role in mold manufacturing, ensuring that all components are precisely shaped and finished. Advanced CNC machines carve out the core and cavity of the mold with extreme accuracy, maintaining tight tolerances required for high-quality plastic parts. Electrical Discharge Machining (EDM) is another technique used in mold-making, particularly for intricate details and complex geometries. EDM uses electrical sparks to shape the mold with high precision, allowing for fine detailing that traditional machining cannot achieve.
Mold polishing and surface finishing are important steps in the manufacturing process. The mold's surface quality directly affects the final appearance of the molded plastic parts. Depending on the requirements, the mold surface can be polished to achieve a smooth finish or textured for specific aesthetic or functional purposes. Texturing techniques, such as bead blasting and chemical etching, help create patterns or improve grip on finished plastic products. Proper surface finishing ensures smooth ejection of parts and reduces defects like drag marks and surface blemishes.
Materials Used in Custom Plastic Mold Tooling
Selecting the right materials for custom mold tooling is essential to achieving the best performance, durability, and cost-effectiveness. Both the mold base and the plastic resin used in injection molding play significant roles in determining the final product's quality. The choice of mold materials impacts the mold’s lifespan, production efficiency, and resistance to wear and tear.
Steel is one of the most commonly used materials for mold bases due to its strength and durability. Different grades of steel offer varying levels of hardness and resistance to heat and wear. P20 steel is a popular choice for moderate production volumes, as it provides a good balance of durability and machinability. H13 and S136 steel are used for high-volume and high-precision molds due to their exceptional hardness and resistance to heat and corrosion. Stainless steel molds are often selected for medical and food-grade applications, as they offer excellent resistance to chemical corrosion and contamination.
Aluminum molds are widely used for prototyping and low-volume production runs. They are lightweight, easy to machine, and allow for faster production cycles due to their superior heat dissipation properties. While aluminum molds have a shorter lifespan compared to steel molds, they offer cost savings and rapid turnaround times, making them ideal for testing new product designs. Advances in aluminum mold technology have improved their durability, making them a viable option for small to medium-scale production.
Cost Factors in Custom Mold Tooling
The cost of custom mold tooling depends on several factors, including mold complexity, material selection, production volume, and design considerations. While the upfront investment in custom molds may be high, the long-term benefits in production efficiency and quality outweigh the initial costs. Understanding the cost factors involved in mold tooling helps manufacturers make informed decisions and optimize their budget.
The complexity of the mold design significantly impacts the overall cost. Molds with intricate geometries, undercuts, and multi-cavity layouts require more time and advanced machining techniques, increasing production expenses. Simple molds with basic designs are more cost-effective, while highly detailed molds with fine tolerances require precision engineering, leading to higher costs. Features such as slide mechanisms, lifters, and threaded inserts also contribute to increased mold costs due to the additional engineering and machining involved.
The choice of mold material affects both the initial investment and long-term cost efficiency. Steel molds are more expensive to manufacture but provide a longer lifespan, making them a cost-effective option for high-volume production. Aluminum molds are less expensive upfront but wear out faster, requiring replacement for extended production runs. Selecting the right material based on production needs helps balance cost and performance.
Quality Control & Testing
Ensuring quality in custom plastic mold tooling is a crucial step in maintaining precision, consistency, and durability in production. Mold quality directly impacts the final product, and manufacturers rely on advanced testing techniques to detect any potential flaws before full-scale production begins. By implementing strict quality control measures, businesses can prevent costly defects, reduce material waste, and optimize production efficiency.
Dimensional accuracy testing is one of the first quality control steps in custom mold tooling. Since even the slightest deviation in mold dimensions can affect the fit and function of the final part, precision measuring equipment such as Coordinate Measuring Machines (CMMs) is used to inspect mold cavities and features. CMMs provide highly accurate 3D measurements, ensuring that the mold meets the exact design specifications. Other measurement tools, including laser scanners and optical comparators, are also used to verify fine details and surface textures.
Process capability studies are conducted to evaluate the mold’s performance in actual production conditions. These studies assess key factors such as fill speed, hold pressure, and cycle time to determine how consistently the mold can produce defect-free parts. Scientific molding techniques, which involve data-driven monitoring of processing parameters, help engineers optimize mold settings for the best results. This method ensures that the injection molding process remains stable and produces consistent, high-quality parts over time.
Benefits of Custom Mold Tooling
Custom plastic mold tooling provides numerous advantages for manufacturers seeking precision, efficiency, and cost-effectiveness in plastic part production. Unlike standard molds, which may not accommodate complex designs or unique product requirements, custom molds are tailored to meet specific industry needs. This customization allows businesses to achieve higher product quality, faster production speeds, and lower overall manufacturing costs.
One of the primary benefits of custom mold tooling is precision and repeatability. Custom molds are designed to meet exact specifications, ensuring that every part produced is consistent in size, shape, and quality. This level of accuracy is essential in industries such as automotive, aerospace, and medical devices, where tight tolerances are required. By eliminating variations between parts, manufacturers can maintain product integrity and reduce defects, improving overall reliability.
Another key advantage of custom mold tooling is its ability to reduce waste and support sustainable manufacturing practices. Since molds are designed for efficiency, they optimize material usage, minimizing excess plastic and reducing overall production waste. Some mold manufacturers incorporate advanced recycling systems to reclaim and reuse plastic scraps, further contributing to environmental sustainability. Additionally, well-designed molds help prevent common defects such as flash, short shots, and warping, reducing the need for rework and material disposal.
Choosing the Right Mold Tooling Manufacturer
Selecting the right Custom Plastic Mold Tooling manufacturer is a crucial step in ensuring high-quality plastic parts and efficient production processes. With many options available, businesses must carefully evaluate potential partners based on their expertise, technology capabilities, and ability to meet specific manufacturing requirements. Choosing an experienced and reliable mold manufacturer can significantly impact product quality, production speed, and overall cost-effectiveness.
Expertise and industry experience should be a primary consideration when selecting a mold tooling manufacturer. Companies with a long track record in custom mold design and manufacturing have the knowledge and technical skills to handle complex projects. An experienced manufacturer can offer valuable insights into material selection, mold design optimization, and process improvements, ensuring that the final mold meets all production requirements. Reviewing past projects and client testimonials can provide a clear picture of a manufacturer’s expertise and reliability.
Technology and equipment capabilities are also critical factors in mold manufacturer selection. Modern injection mold tooling requires advanced CNC machining, EDM, and CAD software for precise mold design and production. Manufacturers that invest in the latest machinery and automation can deliver higher-quality molds with shorter lead times. In addition, mold makers who use simulation software, such as MoldFlow analysis, can predict and optimize plastic flow within the mold, preventing potential defects before production begins.
Conclusion
Custom plastic mold tooling is an essential component of modern manufacturing, offering precision, efficiency, and cost-effectiveness for producing high-quality plastic parts. Whether for prototyping, bridge tooling, or large-scale production, custom molds ensure consistency, durability, and optimized production cycles. With advancements in CAD software, CNC machining, and mold flow analysis, manufacturers can now achieve greater precision and reduce defects, improving overall product quality and reducing production costs.
Investing in custom mold tooling provides businesses with a competitive edge in industries such as automotive, medical devices, consumer goods, and industrial applications. The ability to tailor molds to specific product requirements ensures that manufacturers can meet strict design specifications while maintaining efficiency in mass production. Additionally, multi-cavity and family mold options enable cost savings by increasing the number of parts produced per cycle, reducing per-unit costs, and improving manufacturing speed.