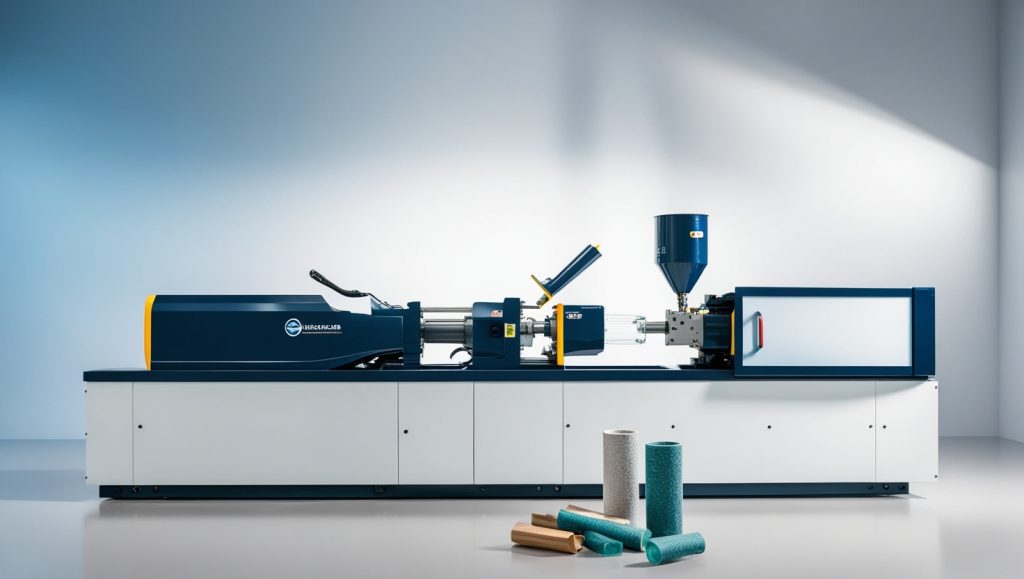
Injection molding is a manufacturing process used to create plastic parts quickly and efficiently. The process involves melting plastic pellets and injecting the molten material into a mold. Once the plastic cools and hardens, it takes the shape of the mold, creating a durable, finished product.
This method is widely used across industries because it allows for mass production with minimal waste. Common products made using injection molding include:
- Food containers and bottle caps
- Car parts such as dashboards and bumpers
- Medical tools like syringes and surgical equipment
- Electronic casings for phones, keyboards, and laptops
Why Sustainability Matters in Injection Molding
Plastic production has a significant impact on the environment. Traditional plastics take hundreds of years to decompose, contributing to pollution and landfill waste. Additionally, the energy-intensive process of making plastics increases carbon emissions.
Sustainable injection molding offers a way to reduce these environmental effects. By using eco-friendly materials and energy-efficient machines, manufacturers can produce high-quality plastic products while reducing waste and pollution. The shift toward sustainable practices also helps companies meet growing consumer demand for environmentally responsible products.
Sustainable Materials for Injection Molding
Biodegradable Plastics for Injection Molding
Biodegradable plastics break down naturally over time, reducing plastic waste in landfills and oceans. Several types of biodegradable plastics are now being used in injection molding.
Polylactic Acid (PLA) is a plant-based plastic derived from cornstarch or sugarcane. It is compostable and commonly used for food packaging, disposable cutlery, and medical implants.
Polyhydroxyalkanoates (PHA) are produced by microorganisms and can biodegrade in marine environments. This makes them an excellent choice for single-use items and packaging.
Polybutylene Succinate (PBS) is another biodegradable plastic that offers flexibility and durability. It is often used in food containers and agricultural films.
Recycled Plastics for Sustainable Manufacturing
Using recycled plastic helps reduce waste and decrease the need for virgin materials. There are two main types of recycled plastics used in injection molding.
Post-consumer recycled (PCR) plastics come from used products like water bottles and food containers. They help prevent plastic waste from ending up in landfills and oceans. However, PCR plastics can sometimes have quality and consistency challenges.
Post-industrial recycled (PIR) resins come from leftover plastic waste generated during the manufacturing process. Since these materials have not been used by consumers, they often have better quality than PCR plastics.
Some of the most commonly recycled plastics for injection molding include:
- rPET (recycled polyethylene terephthalate), often used for water bottles and packaging
- rPP (recycled polypropylene), commonly found in automotive parts and containers
- rHDPE (recycled high-density polyethylene), used for detergent bottles and pipes
Bio-Based Plastics and Fillers
Bio-based plastics come from renewable sources, making them an eco-friendly alternative to traditional petroleum-based plastics.
Cornstarch-based plastics are lightweight and compostable, commonly used for packaging and disposable tableware.
Hemp, flax, and bamboo fillers can be blended with plastics to create stronger, more sustainable materials. These natural fibers reduce the amount of plastic needed and make products biodegradable.
Calcium carbonate and other mineral-based fillers help improve the strength of plastic parts while reducing the amount of raw plastic required.
How to Choose the Right Sustainable Material for Injection Molding
Several factors determine which sustainable material is best for a product. The key considerations include:
- Cost: Some eco-friendly materials are more expensive than traditional plastics.
- Durability: Biodegradable and recycled plastics may have different strength and flexibility levels.
- End-of-life options: Some materials are compostable, while others can be easily recycled.
Many companies are already using sustainable plastics in their products. For example, brands like Coca-Cola and Nike have introduced recycled plastics in their packaging and footwear.
Energy-Efficient Injection Molding Machines
All-Electric vs. Hydraulic vs. Hybrid Machines
Traditional hydraulic machines consume a lot of energy and require frequent maintenance. Newer, energy-efficient options help reduce electricity use and lower carbon emissions.
All-electric injection molding machines use electric motors instead of hydraulic systems, making them more precise and energy-efficient. They also reduce waste and maintenance costs.
Hybrid machines combine electric and hydraulic components to balance energy efficiency with high performance. These machines are often used for complex manufacturing needs.
Comparing these machines shows that all-electric models can save up to 50 percent more energy than hydraulic machines. While they have a higher upfront cost, they help manufacturers save money in the long run through reduced energy bills.
Smart Manufacturing for Sustainability
New technologies like artificial intelligence (AI) and the Internet of Things (IoT) are making injection molding more efficient. These innovations help manufacturers reduce waste, improve production speed, and lower energy consumption.
AI-driven process optimization allows machines to adjust settings automatically, reducing errors and material waste.
IoT-enabled machines provide real-time data monitoring, helping manufacturers track energy use and identify inefficiencies.
Predictive maintenance helps prevent machine breakdowns by detecting issues before they cause major failures, reducing downtime and waste.
By adopting energy-efficient machines and smart manufacturing technologies, companies can produce high-quality plastic products while minimizing environmental impact.
Waste Reduction Strategies in Injection Molding
Closed-Loop Recycling in Injection Molding
A closed-loop recycling system ensures that excess plastic waste from the injection molding process is collected, processed, and reused. This approach helps reduce material waste, lower production costs, and minimize the environmental impact.
Manufacturers recycle excess plastic by grinding and reprocessing scrap material, including sprues, runners, and rejected parts. Advanced sorting and filtering technologies help maintain the quality of the recycled plastic, ensuring that it meets industry standards.
Many companies are now adopting zero-waste injection molding facilities, where every piece of plastic is either reused or repurposed. These facilities prioritize material efficiency and sustainable practices to reduce overall waste.
Hot Runner vs. Cold Runner Systems
Runner systems in injection molding play a crucial role in directing molten plastic into the mold cavity. Choosing the right system can significantly impact material waste.
Hot runner molds keep the plastic in a molten state, eliminating excess material left in the runner. This reduces waste and improves efficiency. However, hot runner systems are more expensive and require precise temperature control.
Cold runner molds, on the other hand, allow the plastic in the runner to cool and solidify, creating extra material that must be removed and often discarded or recycled. While cold runner molds are more affordable and easier to maintain, they generate more plastic waste.
By switching to hot runner molds, manufacturers can significantly reduce material waste and improve sustainability.
Design for Minimal Material Usage
Optimizing product design is another effective way to minimize plastic consumption in injection molding.
Thin-wall molding reduces the amount of plastic used while maintaining structural integrity. This technique is commonly used in packaging, electronics, and medical devices.
Lightweighting techniques help manufacturers create durable products with less material. This includes optimizing part geometry, using structural reinforcements, and selecting high-strength plastics that allow for thinner designs.
By integrating these strategies, manufacturers can reduce plastic usage without compromising product quality.
How Manufacturers Can Reuse and Regrind Scrap Material
Regrinding is a common practice in sustainable injection molding, where excess plastic is shredded and reused. Best practices for reusing scrap material include:
- Sorting and cleaning plastic waste to maintain quality
- Blending regrind material with virgin plastic for consistent performance
- Using advanced filtration systems to remove impurities
- Implementing automated waste collection systems to streamline recycling
Adopting these methods helps companies reduce raw material costs and minimize environmental impact.
Sustainable Product Design Injection Molding For Sustainable Products
Eco-Friendly Product Design Principles
Sustainable design strategies can improve the recyclability and lifespan of injection-molded products.
Design for Disassembly (DfD) makes it easier to separate materials for recycling. By using snap-fit connections instead of glue or mixed materials, manufacturers create products that can be easily taken apart and repurposed.
Monomaterial design uses a single type of plastic instead of multiple materials, making recycling simpler and more efficient. Many companies are now producing monomaterial packaging to improve sustainability.
Multi-Material Molding for Sustainability
Overmolding and two-shot molding allow manufacturers to combine different materials into a single product without adhesives. This reduces chemical waste and simplifies recycling.
These techniques are commonly used in automotive parts, medical devices, and consumer electronics, where durability and performance are essential.
Sustainable Packaging for Injection Molded Products
Reducing plastic waste in packaging is a critical step toward sustainability.
Biodegradable and recyclable packaging options include:
- Compostable bioplastics made from cornstarch or sugarcane
- Paper-based alternatives with minimal plastic coatings
- Recycled plastic packaging made from post-consumer waste
Minimizing packaging waste involves designing lightweight packaging, using reusable materials, and reducing unnecessary layers. Many brands are now moving toward minimalist packaging to align with sustainability goals.
Sustainable End-of-Life Strategies Injection Molding For Sustainable Products
How to Make Injection Molded Products More Recyclable
Manufacturers can improve recyclability by:
- Avoiding mixed-material designs that complicate sorting
- Using clear labeling to indicate plastic type
- Selecting widely accepted recyclable materials such as PET and HDPE
By ensuring products can be easily processed at recycling centers, companies contribute to a circular economy.
The Role of Biodegradability in Injection Molding
Biodegradable plastics are designed to break down naturally, but their decomposition depends on environmental conditions.
- PLA decomposes in industrial composting facilities but not in regular landfills.
- PHA can degrade in marine environments, making it ideal for single-use plastics.
- PBS offers flexibility and degrades faster than traditional plastics.
Choosing the right biodegradable material ensures sustainability while maintaining product performance.
Extended Producer Responsibility (EPR) Programs
EPR programs hold manufacturers accountable for the disposal and recycling of their products. Companies that participate in EPR initiatives:
- Offer take-back programs for used products
- Partner with recycling facilities to recover materials
- Design products with end-of-life management in mind
These programs encourage businesses to reduce waste and create more sustainable products.
Industry Certifications & Regulations for Injection Molding For Sustainable Products
Environmental Certifications for Sustainable Manufacturing
Certifications help businesses demonstrate their commitment to sustainability. Some of the most recognized certifications include:
- ISO 14001 – Focuses on environmental management systems and sustainable practices.
- Cradle to Cradle Certification – Evaluates product safety, material health, and recyclability.
- USDA BioPreferred Program – Certifies bio-based products made from renewable resources.
Meeting these standards improves credibility and ensures compliance with environmental regulations.
Government Regulations on Sustainable Plastics
Governments worldwide are implementing policies to reduce plastic waste and encourage sustainable manufacturing. Some key regulations include:
- Bans on single-use plastics in many countries, including plastic straws, bags, and cutlery.
- Extended producer responsibility (EPR) laws requiring companies to manage their product waste.
- Incentives for using recycled materials, such as tax benefits and grants.
Future Trends in Injection Molding For Sustainable Products
Advances in Biodegradable & Compostable Polymers
The demand for eco-friendly materials is driving innovation in biodegradable and compostable polymers. Researchers and manufacturers are developing new bio-based materials that provide the durability of traditional plastics while being environmentally friendly.
Some of the latest innovations include:
- Next-generation PLA and PHA blends – More flexible, heat-resistant, and compostable options for food packaging and medical applications.
- Algae-based bioplastics – Renewable and carbon-negative, these materials are being explored for packaging and consumer goods.
- Enzyme-infused plastics – Designed to break down faster under specific conditions, ensuring they decompose efficiently in composting facilities.
- High-performance bio-composites – Combining biodegradable plastics with natural fibers like hemp, flax, or bamboo for added strength and durability.
With continued research, these materials will become more affordable and widely adopted, making sustainable injection molding more accessible for businesses.
AI & Automation in Sustainable Injection Molding
The rise of smart manufacturing is revolutionizing the injection molding industry. Artificial intelligence (AI) and automation are helping manufacturers reduce waste, improve energy efficiency, and optimize production processes.
Key ways AI and automation contribute to sustainability:
- Automated waste reduction – AI-driven monitoring systems detect material waste and adjust machine settings to minimize excess plastic use.
- Real-time quality control – AI-powered sensors identify defects early in the process, preventing unnecessary material waste.
- Energy-efficient machine learning – Smart factories use AI to optimize energy consumption, reducing electricity use and carbon emissions.
- Predictive maintenance – AI predicts equipment failures before they happen, reducing downtime and preventing material loss.
The Shift Toward a Circular Economy
A circular economy focuses on reusing, recycling, and repurposing materials instead of disposing of them. In sustainable injection molding, this means designing products and processes that extend the life cycle of plastic materials.
Key developments in the shift toward closed-loop plastic production include:
- Advanced mechanical and chemical recycling – More efficient methods for breaking down plastic waste and reusing it in new products.
- Product-as-a-service models – Instead of selling disposable plastic products, companies offer reusable alternatives that customers return for recycling or refurbishment.
- Increased government regulations and incentives – More policies supporting recycled content and responsible waste management are pushing industries toward circular economy models.
- Eco-labeling and transparency – More brands are providing clear information on material sourcing, recyclability, and sustainability certifications to inform consumers.
Conclusion: The Future of Injection Molding For Sustainable Products
Sustainable injection molding is rapidly evolving, driven by material innovations, AI-driven efficiency, and circular economy principles.
Key takeaways for manufacturers:
- Switch to sustainable materials – Biodegradable, recycled, and bio-based plastics reduce environmental impact.
- Adopt smart manufacturing – AI and automation help optimize production, reduce waste, and improve energy efficiency.
- Embrace circular economy models – Designing products for recycling and reuse minimizes plastic waste and supports sustainability.
To stay competitive, businesses should implement sustainability strategies such as:
- Partnering with suppliers who offer eco-friendly materials.
- Investing in energy-efficient and AI-powered machinery.
- Redesigning products for recyclability and minimal material use.
- Complying with environmental regulations and certifications.
As technology advances and consumer demand for sustainability grows, companies that prioritize eco-friendly injection molding practices will lead the way in creating a cleaner, greener future.