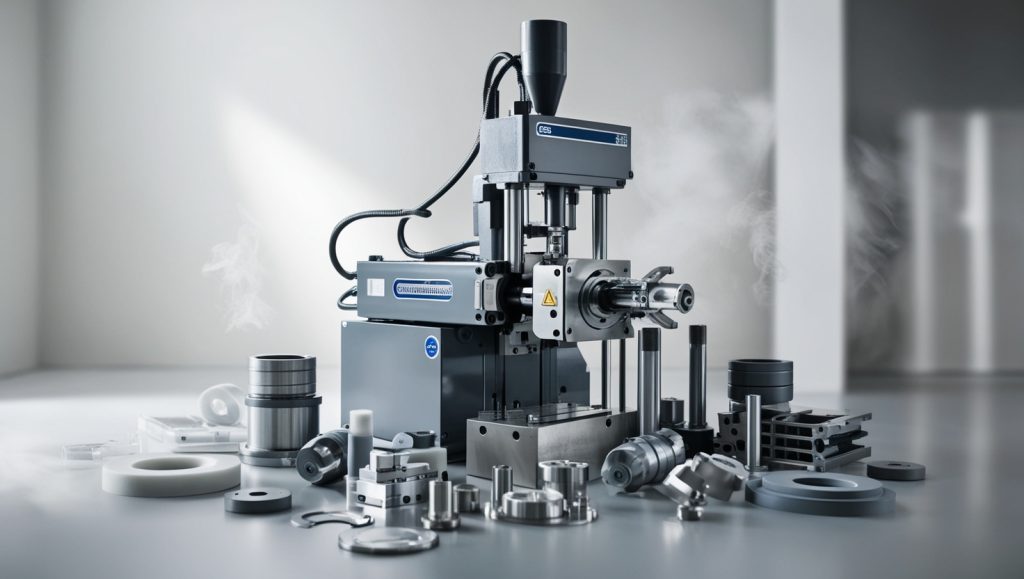
Injection molding is a manufacturing process used to produce high-volume plastic parts with extreme accuracy and consistency. It involves injecting molten plastic into a precisely engineered mold, allowing it to cool and solidify into the desired shape. This method is widely used due to its efficiency, repeatability, and ability to create complex geometries with tight tolerances.
Why Precision Matters?
Precision injection molding is essential in industries where dimensional accuracy, minimal variation, and high-performance characteristics are crucial. A deviation of just a few microns can lead to failure in medical devices, automotive components, or electronic parts. Achieving ultra-tight tolerances ensures seamless functionality, durability, and compliance with industry standards.
Key Benefits of Precision Injection Molding
- High Repeatability – Ensures identical parts across large production runs.
- Complex Geometries – Allows for intricate designs that would be difficult or impossible with traditional machining.
- Cost-Effectiveness – Once the mold is created, large-scale production is relatively inexpensive.
- Reduced Material Waste – Optimized injection processes result in minimal scrap.
- Durability & Performance – Suitable for high-performance applications in demanding environments.
Common Industries Using Precision Molding
- Medical & Healthcare: Microfluidic devices, surgical instruments, drug delivery systems.
- Automotive: High-precision connectors, sensor housings, interior and exterior components.
- Aerospace & Defense: Lightweight structural parts, high-heat-resistant components.
- Electronics: Miniature gears, casings, circuit board mounts.
- Industrial & Robotics: High-strength plastic parts for automation and heavy-duty machinery.
How Precision Injection Molding Works
Precision injection molding follows a systematic and highly controlled process to ensure each part meets strict quality standards. Below is a step-by-step breakdown of how it works.
Step 1: Part Design & Engineering
Before molding begins, engineers create 3D CAD models of the part, ensuring it meets Design for Manufacturability (DFM) guidelines.
- Factors considered:
- Wall thickness uniformity (to prevent warping)
- Draft angles (for easy mold release)
- Tolerance requirements (typically ±0.001 to ±0.005 inches)
- Material selection (shrinkage rates, strength, flexibility)
Step 2: Mold Tooling & Fabrication
Once the design is finalized, the mold is created using CNC machining, EDM (Electrical Discharge Machining), or 3D metal printing.
- Types of molds used for precision injection molding:
- Single-cavity molds (for prototyping or small-scale production)
- Multi-cavity molds (for mass production)
- Micro-molds (for ultra-small, high-precision parts)
- Hot runner vs. cold runner molds (to optimize cycle time and material use)
Step 3: Material Selection
Choosing the right plastic resin is critical for precision. The most commonly used high-performance materials include:
- PEEK (Polyetheretherketone) – Used in aerospace and medical due to its heat and chemical resistance.
- PPS (Polyphenylene Sulfide) – Excellent dimensional stability and heat resistance.
- LCP (Liquid Crystal Polymer) – Ideal for micro-molding electronic components.
- Nylon (PA) – Tough, wear-resistant, and widely used in automotive.
- PC (Polycarbonate) – High impact resistance and optical clarity.
Each material has a specific shrinkage rate, which engineers account for to maintain tight tolerances.
Step 4: Injection Molding Machine Setup
The mold is placed into an injection molding machine, where precise control over:
- Injection speed (to prevent defects like flow lines)
- Pressure & clamping force (to maintain dimensional accuracy)
- Temperature control (to ensure proper material flow and cooling)
Step 5: Production Cycle
- Injection: Molten plastic is injected into the mold at high pressure.
- Cooling: The part solidifies inside the mold, carefully controlled to prevent warpage.
- Ejection: The part is released from the mold using ejector pins.
- Post-processing: If necessary, additional steps like trimming, ultrasonic welding, or surface finishing are applied.
Step 6: Quality Control & Testing
To maintain high precision, automated inspection systems and metrology tools are used, such as:
- Coordinate Measuring Machines (CMMs) – For checking dimensional accuracy.
- Optical Profilers & CT Scanners – Used for micro-molding quality control.
- AI-Based Real-Time Monitoring – Detects defects and adjusts machine parameters dynamically.
Materials Used in Precision Injection Molding
Importance of Material Selection
Material selection is one of the most critical factors in precision injection molding. The right material ensures dimensional stability, mechanical strength, resistance to environmental factors, and compatibility with the intended application. High-performance plastics are commonly used in precision molding due to their superior thermal and mechanical properties.
High-Performance Plastics for Precision Molding
Material | Key Properties | Common Applications |
---|---|---|
PEEK (Polyetheretherketone) | High temperature & chemical resistance, excellent mechanical strength | Medical implants, aerospace components, automotive parts |
PPS (Polyphenylene Sulfide) | High dimensional stability, heat resistance, low moisture absorption | Automotive sensor housings, electrical components |
LCP (Liquid Crystal Polymer) | Extremely high flow, ultra-thin part capability, chemical resistance | Micro-molded electronics, semiconductor parts |
Nylon (PA6, PA66, PA12) | High toughness, good wear resistance, lightweight | Gears, bearings, automotive parts |
PC (Polycarbonate) | Impact-resistant, optically transparent, good heat resistance | Safety helmets, electronic displays, automotive lighting |
ABS (Acrylonitrile Butadiene Styrene) | Good mechanical properties, high surface quality, easy to mold | Consumer goods, automotive dashboards |
PBT (Polybutylene Terephthalate) | Good electrical properties, heat resistance, chemical resistance | Electrical connectors, automotive components |
Ultem (PEI - Polyetherimide) | High strength, flame resistance, low outgassing | Aerospace, medical devices, high-temperature applications |
Material Selection Considerations
When choosing a plastic resin for precision injection molding, several factors must be considered:
- Shrinkage & Warpage: Some materials have higher shrink rates than others, affecting part accuracy.
- Thermal Expansion: Expansion under heat can impact dimensional stability.
- Moisture Absorption: Some materials, like nylon, absorb moisture, which can alter properties.
- Chemical & Heat Resistance: Essential for applications in harsh environments like automotive and aerospace.
- Moldability: Flow characteristics determine whether the material can form ultra-thin features.
Comparison of Engineering Plastics Based on Performance Factors
Factor | Best Material Choices |
---|---|
High Temperature Resistance | PEEK, Ultem, PPS |
Dimensional Stability | PPS, LCP, PBT |
Wear Resistance | Nylon, PEEK |
Electrical Insulation | PBT, LCP, Ultem |
Moisture Resistance | PEEK, PPS, LCP |
Tooling & Mold Design for Precision Parts
Importance of Mold Design in Precision Injection Molding
The mold is the foundation of precision injection molding. A well-designed mold ensures:
- Tight Tolerances (±0.001 inches or better)
- Repeatability (Each part is identical across thousands of cycles)
- Defect Reduction (Minimizing warpage, sink marks, and flash)
Types of Injection Molds for Precision Parts
1. Single-Cavity vs. Multi-Cavity Molds
- Single-Cavity Molds: Used for prototyping and low-volume production.
- Multi-Cavity Molds: Used for high-volume manufacturing, reducing per-part costs.
2. Hot Runner vs. Cold Runner Molds
- Hot Runner Systems: Reduce material waste, improve cycle times, and allow better flow control.
- Cold Runner Systems: More cost-effective for small production runs but produce more scrap.
3. Micro-Molding Tooling
- Used for ultra-small components requiring micron-level precision (e.g., medical and electronic parts).
- Requires specialized mold inserts made using EDM (Electrical Discharge Machining) or precision CNC milling.
Tight Tolerance Mold Design
- Precision CNC machining is used to create molds with tolerances within ±0.001 inches.
- EDM (Electrical Discharge Machining) is used for intricate geometries and micro-sized components.
- High-Polish Surfaces prevent defects and improve part aesthetics.
- Uniform Cooling Channels prevent warping and shrinkage variations.
Cooling Systems & Venting for Precision Control
- Cooling Channels: Proper cooling prevents part deformation and improves cycle times.
- Venting: Trapped air inside the mold can cause short shots or burns, making venting critical for precision parts.
Mold Maintenance & Longevity
- Regular Mold Cleaning prevents residue build-up and ensures part accuracy.
- Periodic Tooling Inspections detect wear before defects occur.
- Using Hardened Steel (H13, S136, etc.) increases mold lifespan for high-volume production.
Process Optimization for High Precision & Repeatability
Why Process Optimization is Critical in Precision Injection Molding?
In precision injection molding, even minor inconsistencies in temperature, pressure, or cooling time can result in defects or dimensional variations. Optimizing the process ensures:
- Consistent quality across all production runs
- Minimized defects (warpage, shrinkage, flash, short shots, etc.)
- Reduced cycle time for cost-effective manufacturing
- Extended mold life through proper process control
Key Factors That Influence Precision
- Injection Speed & Pressure:
- High injection speeds can lead to flow lines and poor filling.
- Low speeds may cause short shots or incomplete fills.
- Solution: Optimized injection profile for smooth and complete cavity filling.
- Clamping Force:
- Excessive force can damage the mold and lead to flash.
- Insufficient force can cause parting-line mismatch or burrs.
- Solution: Proper force calculations based on material and mold design.
- Temperature Control:
- Variations in melt temperature can cause shrinkage inconsistencies.
- Incorrect cooling rates may lead to internal stresses and warping.
- Solution: Real-time temperature monitoring and controlled cooling channels.
- Holding & Packing Pressure:
- If too low, it results in sink marks and voids.
- If too high, it can cause excessive stress in the part.
- Solution: Balanced packing pressure for proper material distribution.
Advanced Process Control Technologies
- Closed-Loop Control Systems: Sensors monitor and adjust process parameters in real time.
- AI & Machine Learning: AI-based monitoring detects defects and adjusts machine settings dynamically.
- IoT-Enabled Smart Molding Machines: Cloud-based data analysis improves efficiency and predictive maintenance.
- Automation & Robotics: Robotic part handling reduces human error and increases repeatability.
Reducing Defects in Precision Molding
Defect | Cause | Solution |
---|---|---|
Warping | Uneven cooling, residual stress | Optimize cooling rates, use uniform wall thickness |
Short Shots | Insufficient material flow, low injection pressure | Increase pressure, improve venting |
Flash | Excessive injection pressure, poor mold fit | Adjust pressure, maintain mold integrity |
Sink Marks | Inadequate holding pressure, thick sections | Increase pressure, optimize cooling |
Burn Marks | Trapped air, excessive injection speed | Improve venting, adjust speed |
Case Study: How Advanced Sensors Improve Precision in Injection Molding
A major automotive components manufacturer integrated real-time pressure sensors into their molding process. The result:
- Reduction in defect rates by 35%
- 50% faster cycle time adjustment
- Lower scrap rate, saving $100,000 annually
Quality Control & Inspection in Precision Injection Molding
Importance of Quality Control in Precision Injection Molding
With tight tolerances (as low as ±0.001 inches), quality control ensures that parts meet the required specifications, durability, and regulatory standards.
Inspection Techniques for High-Tolerance Parts
- Coordinate Measuring Machines (CMM):
- Measures dimensions with sub-micron accuracy.
- Used for complex geometries and tight tolerances.
- Optical Measurement Systems:
- Non-contact inspection using laser scanners and vision systems.
- Best for micro-molded parts and transparent components.
- CT Scanning (Computed Tomography):
- Provides a 3D internal view of molded parts.
- Detects voids, cracks, and fiber orientation without destroying the part.
- First Article Inspection (FAI):
- Ensures the first batch of molded parts matches design specifications.
- Automated Quality Assurance with Machine Vision Systems:
- AI-powered real-time defect detection for mass production.
- Reduces human error and improves efficiency.
ISO & Industry Standards for Precision Molding
Standard | Industry | Purpose |
---|---|---|
ISO 13485 | Medical Devices | Ensures regulatory compliance for medical parts |
IATF 16949 | Automotive | Quality management for automotive components |
ISO 9001 | General Manufacturing | Quality assurance for consistent production |
AS9100 | Aerospace | High-precision manufacturing standards for aviation |
Ensuring Consistency in High-Volume Production
- Statistical Process Control (SPC):
- Uses real-time data to monitor production trends.
- Reduces defects by adjusting process parameters before failure occurs.
- Six Sigma in Injection Molding:
- Uses DMAIC (Define, Measure, Analyze, Improve, Control) to minimize variability.
- Helps achieve near-zero defects in precision molding.
Case Study: Machine Vision for Real-Time Defect Detection
A medical device manufacturer implemented AI-based vision inspection to analyze 1,000 parts per hour.
Results:
- 40% faster defect detection
- 99.7% inspection accuracy
- Reduced manual inspection labor costs by 60%
Applications of Precision Injection Molding
Precision injection molding is widely used in industries that require tight tolerances, repeatability, and high-performance plastic components. From medical devices to aerospace components, precision molding plays a crucial role in modern manufacturing.
Key Industries and Applications
1. Medical Devices & Healthcare
Precision injection molding is essential in medical-grade plastic parts due to strict regulatory requirements and biocompatibility.
- Common Applications:
- Surgical Instruments: Handles, grips, housings for medical tools
- Microfluidic Devices: Lab-on-a-chip devices for diagnostic testing
- Drug Delivery Systems: Insulin pens, inhalers, IV components
- Implants & Prosthetics: Biocompatible polymer implants
- Catheters & Tubing: High-precision extruded and molded parts
✔ Regulatory Compliance: Medical molding must meet ISO 13485 and FDA standards.
2. Automotive Industry
Automakers rely on high-precision plastic parts for lightweighting, durability, and functionality.
- Common Applications:
- Sensors & Connectors: High-precision electronic housings
- Fuel & Engine Components: Heat-resistant plastic parts
- Dashboard & Interior Parts: Injection-molded trims, control panels
- Lightweight Structural Parts: Replacing metal with high-performance polymers
✔ Compliance with IATF 16949 for automotive quality management.
3. Aerospace & Defense
The aerospace sector uses precision-molded plastic components to reduce weight and enhance performance.
- Common Applications:
- Aircraft Interior Components: Lightweight seat frames, overhead bins
- Heat-Resistant Components: High-performance plastics like PEEK and Ultem
- Electronic Enclosures: Shielding components for avionics
- Fuel System Components: Lightweight, corrosion-resistant fuel line parts
✔ Compliance with AS9100 aerospace manufacturing standards.
4. Consumer Electronics & Miniaturization
With devices getting smaller and more complex, precision molding plays a crucial role in electronics manufacturing.
- Common Applications:
- Micro Gears & Actuators: Tiny plastic gears for smart devices
- Smartphone Components: SIM trays, camera modules
- Semiconductor Housings: High-precision plastic packaging for chips
- Wearable Tech Components: Smartwatch cases, flexible connectors
✔ Micro-molding enables production of parts as small as 10 microns.
5. Industrial & Robotics
- Common Applications:
- High-Strength Gears & Bearings: Plastic gears with self-lubricating properties
- Automation Equipment Components: Custom housings for robotic arms
- Sealing & Insulating Parts: Plastic seals and gaskets for industrial machinery
✔ High-performance plastics like PEEK and LCP ensure durability.
Case Study: Automotive Lightweighting with Precision Molding
A leading automotive manufacturer replaced metal sensor housings with injection-molded high-performance plastic, reducing:
- Component weight by 40%
- Manufacturing cost by 25%
- Fuel consumption by improving vehicle efficiency
Cost Considerations & ROI for Precision Molding
Understanding the Cost Structure of Injection Molding
The cost of precision injection molding depends on tooling, material selection, production volume, and part complexity.
Cost Breakdown
Cost Factor | Description | Impact on Pricing |
---|---|---|
Tooling Costs | Initial cost for mold design and fabrication | High upfront cost but reduces long-term per-part cost |
Material Costs | High-performance plastics like PEEK and LCP are more expensive | Directly impacts per-part pricing |
Machine & Labor Costs | CNC machining, AI-driven quality control, automation | Higher precision reduces defects and waste |
Cycle Time & Production Volume | Faster cycle times and larger volumes lower per-part cost | Optimized for mass production |
Cost Comparison: Traditional vs. Precision Injection Molding
Precision molding has higher upfront tooling costs but offers better accuracy, lower waste, and reduced long-term costs.
Factor | Traditional Molding | Precision Molding |
---|---|---|
Upfront Tooling Cost | Lower | Higher |
Per-Part Cost | Higher due to defects & scrap | Lower due to consistent quality |
Tolerance Range | ±0.01 inch | ±0.001 inch |
Defect Rate | Higher | Near zero |
Long-Term ROI | Moderate | High |
✔ Precision molding is cost-effective in high-volume production and for industries requiring tight tolerances.
How to Reduce Costs Without Compromising Precision?
- Design for Manufacturability (DFM): Optimize part design for easier molding.
- Use Multi-Cavity Molds: Increases production efficiency for large runs.
- Choose Cost-Effective Materials: Balance performance with affordability.
- Optimize Cycle Time: Reduce cooling and ejection delays.
- Leverage Automation & AI: Reduces manual errors and labor costs.
ROI Analysis for High-Precision Injection Molding Projects
Investment Area | Cost | ROI Benefits |
---|---|---|
High-Quality Tooling | $50,000 | Long mold life, reduced defects |
Automated Quality Control | $20,000 | Reduces scrap and labor costs |
Advanced Materials | $5–$50 per part | Improves performance and longevity |
Cycle Time Optimization | Lower operating costs | Increases production efficiency |
✔ Companies see an average 25–40% reduction in waste and defects with precision molding.
Case Study: Medical Device Cost Savings
A medical device company switched to micro-molding, reducing:
- Per-part cost by 30%
- Production waste by 50%
- Defect rates to nearly zero
Future Trends in Precision Injection Molding
1. Smart Factories & Industry 4.0 in Injection Molding
The integration of Industry 4.0 technologies is revolutionizing injection molding by enhancing automation, real-time monitoring, and data-driven decision-making.
- IoT-Enabled Molding Machines: Sensors provide real-time data on temperature, pressure, and cycle time to optimize production.
- AI-Powered Process Optimization: Machine learning algorithms predict potential defects and adjust settings automatically.
- Digital Twin Technology: Simulations replicate the entire molding process to reduce trial-and-error and optimize part design.
2. Advancements in 3D Printing & Hybrid Molding
- Rapid Prototyping with 3D Printing: Allows for faster iteration of mold designs before full-scale production.
- Hybrid Injection Molding & Additive Manufacturing: Combines the benefits of injection molding with 3D-printed inserts to create complex geometries with lower costs.
3. Sustainability & Eco-Friendly Materials in Precision Molding
As industries move towards green manufacturing, several sustainability-focused trends are emerging:
- Biodegradable Plastics: Materials like PLA (Polylactic Acid) and PHA (Polyhydroxyalkanoates) are being explored for medical and consumer applications.
- Recycled Resins: Companies are adopting PCR (Post-Consumer Recycled) plastics to reduce waste.
- Energy-Efficient Molding Machines: Servo-driven systems consume 40–70% less energy than traditional hydraulic machines.
4. Emerging Technologies (AI, Machine Learning, IoT) in Injection Molding
- Predictive Maintenance: AI-powered analytics reduce downtime by forecasting machine failures before they occur.
- Automated Defect Detection: AI-driven vision systems identify defects in real-time, ensuring 99.9% accuracy in quality control.
- Self-Optimizing Injection Molding Machines: These machines adjust pressure, temperature, and cycle time automatically based on production data.
Case Study: AI in Injection Molding
A leading aerospace manufacturer implemented AI-driven defect prediction in its molding process, resulting in:
- 30% reduction in cycle times
- 45% decrease in part rejection rates
- 20% energy savings due to optimized machine settings
Conclusion
Summary of Key Takeaways
- Precision injection molding ensures tight tolerances, repeatability, and superior quality in industries like medical, automotive, aerospace, and electronics.
- Advanced materials like PEEK, LCP, and PPS provide exceptional durability, heat resistance, and performance.
- Process optimization through AI, automation, and real-time monitoring reduces defects and improves efficiency.
- Sustainability initiatives, including biodegradable plastics and energy-efficient machines, are shaping the future of injection molding.
Why Choose Precision Injection Molding for Your Business?
If you require high-precision, cost-effective, and scalable manufacturing, injection molding is the ideal solution. With advancements in AI, automation, and sustainable materials, companies can achieve higher efficiency and reduced production costs while maintaining top-tier quality.
How to Find a Reliable Precision Injection Molding Manufacturer?
When selecting a manufacturing partner, consider:
- Experience in high-precision molding
- Compliance with industry standards (ISO 13485, IATF 16949, AS9100, etc.)
- Use of advanced technologies like AI-based quality control
- Capabilities for custom mold design and automation integration