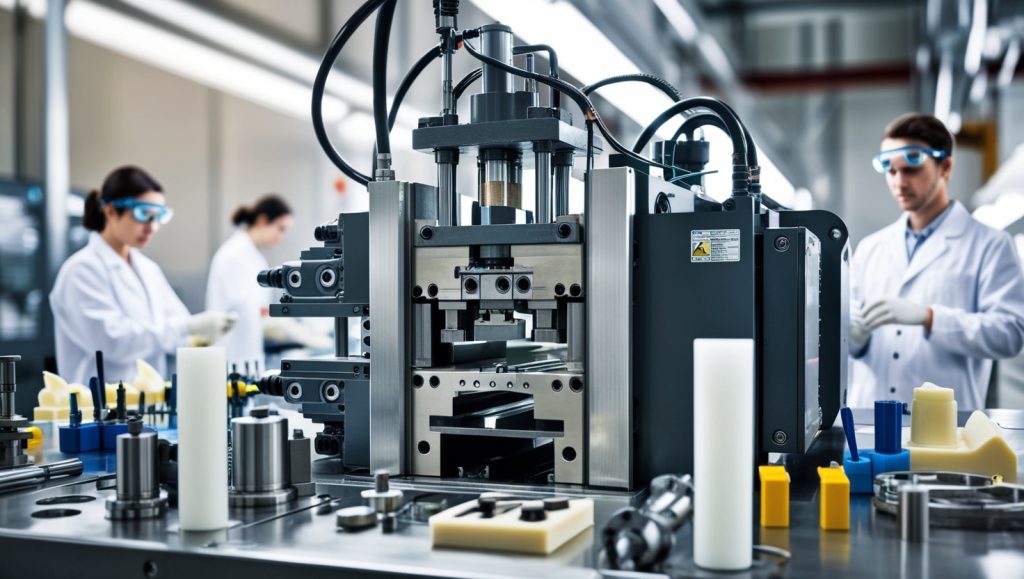
Injection molding is a manufacturing process used to create plastic parts by injecting melted plastic into a mold. Once the plastic cools and hardens, it takes the shape of the mold. This process is widely used in industries such as automotive, medical, packaging, and consumer products because it allows for mass production of consistent, high-quality parts.
The ability to produce detailed and complex designs with minimal waste makes injection molding one of the most efficient and cost-effective ways to manufacture plastic products. This guide explores how the process works, its history, and its importance in modern manufacturing.
What is Injection Molding?
Injection molding is a process where plastic is heated until it melts and is then forced into a mold under high pressure. The mold determines the final shape of the product. After the plastic cools and hardens, the mold opens, and the finished part is removed. This method allows manufacturers to produce large numbers of identical plastic parts quickly.
The origins of injection molding trace back to the late 19th century, when the first molding machine was invented to produce simple items like buttons and combs. Over time, advancements in technology allowed for more precise and complex parts to be made. Today, injection molding is the most common method for producing plastic products due to its efficiency, consistency, and ability to create intricate shapes.
Manufacturers prefer this process because it can produce millions of identical parts with very little variation. It is also more cost-effective compared to other plastic forming methods since waste is minimized, and production speeds are high.
How Injection Molding Works
The process begins with securing the mold in place. The mold consists of two halves: one fixed in position and the other that moves. When the mold is closed, it forms a hollow space where the plastic will be injected. Keeping the mold tightly shut is crucial to ensure that the plastic does not leak and that the final product has the correct shape and dimensions.
Once the mold is secured, plastic pellets are fed into a heated barrel where they melt. A rotating screw pushes the molten plastic forward, and pressure forces it through a nozzle into the mold cavity. The amount of plastic injected is carefully controlled to ensure the mold is filled completely without excess material escaping.
After the plastic is injected, it must cool and solidify before it can be removed. Cooling happens as heat transfers from the plastic to the mold, which is often designed with channels for circulating water or other cooling fluids. The cooling time depends on the type of plastic used and the thickness of the part. If the mold is opened too soon, the plastic may not be fully set, which can lead to defects.
Once the plastic has hardened, the mold opens, and the finished product is pushed out using ejector pins. These pins help remove the part without causing damage. Some parts may have extra plastic, known as flash, that needs to be trimmed off before the product is ready for use.
The final stage of the process involves inspecting the part for any defects such as air bubbles, warping, or incomplete filling. Some products may require additional finishing steps like painting, polishing, or adding textures. Quality control is essential to ensure that each part meets the required standards before it is sent for distribution or assembly.
This process is repeated continuously, making injection molding one of the fastest and most efficient ways to produce plastic parts. With automation and modern technology, manufacturers can produce thousands of parts per hour with very little human intervention.
Key Components of an Injection Molding Machine
An injection molding machine consists of several key parts that work together to melt, inject, shape, and release plastic parts efficiently. Each component plays a crucial role in ensuring precision, speed, and consistency in the manufacturing process.
The Hopper – Stores and feeds plastic material
The hopper is the starting point of the process, where raw plastic material, usually in the form of small pellets or granules, is stored before entering the machine. It is often equipped with a drying system to remove moisture from the plastic, preventing defects in the final product.
The Barrel & Heater – Where the plastic melts
The barrel and heater are responsible for melting the plastic before it is injected into the mold. The barrel is a long, cylindrical chamber where plastic pellets are heated using external heaters. The temperature inside the barrel must be carefully controlled to ensure the plastic reaches the right consistency without degrading.
The screw and nozzle
The screw and nozzle work together to inject molten plastic into the mold. When enough molten plastic accumulates, the screw moves forward like a plunger, forcing the plastic through the nozzle and into the mold cavity. The nozzle acts as the gateway between the barrel and the mold, ensuring the molten plastic flows smoothly into the right areas.
The Mold (Core & Cavity) – Where the part takes shape
The mold, which consists of a core and cavity, determines the final shape of the product. The cavity is the hollow space where the molten plastic fills, while the core helps form the internal structure of the part. Molds are made from durable metals like steel or aluminum and are designed with precise details to create high-quality parts. Cooling channels are often embedded within the mold to help regulate temperature and speed up the solidification process.
The Clamping Unit – Ensuring the mold stays closed
The clamping unit ensures that the mold stays securely closed during injection and cooling. Since molten plastic is injected under high pressure, the mold must be held tightly together to prevent leakage or defects. Hydraulic or mechanical clamps generate the necessary force to keep the mold closed until the plastic has solidified.
The ejector system is responsible for removing the finished part once it has cooled and hardened. Ejector pins push the part out of the mold cavity, ensuring it releases smoothly without damage. In some cases, air blasts or robotic arms assist in the ejection process to improve efficiency and prevent sticking.
Types of Injection Molding Techniques
Different types of injection molding techniques are used depending on the material, product design, and production requirements. These variations allow manufacturers to optimize production for strength, flexibility, and efficiency.
Thermoplastic Injection Molding
Thermoplastic injection molding is the most common type, using plastic materials that can be melted, molded, and remelted without significant degradation. This method is ideal for producing a wide range of consumer and industrial products, offering flexibility in material selection and recycling options.
Thermoset Injection Molding
Thermoset injection molding uses plastics that permanently harden after being heated and molded. Unlike thermoplastics, thermosetting materials cannot be remelted or reshaped once they solidify. This method is often used for parts that require high heat resistance and structural integrity, such as electrical components and automotive parts.
Overmolding – Multi-material molding
Overmolding is a process where multiple materials are molded together in a single part. It allows manufacturers to create products with soft grips, multi-colored designs, or different textures by molding one layer over another. This technique is commonly used in tools, toothbrushes, and electronic housings.
Insert Molding – Embedding metal parts
Insert molding involves embedding metal or other components inside the plastic part during the injection process. Instead of assembling separate pieces later, the plastic is molded directly around the insert, creating a strong bond. This method is frequently used in medical devices, automotive parts, and electrical connectors.
Gas-Assisted Injection Molding – Reducing material use
Gas-assisted injection molding is a specialized technique that introduces pressurized gas into the molten plastic inside the mold. The gas pushes the plastic against the mold walls, creating hollow sections and reducing material use. This technique is useful for making lightweight, strong parts with minimal warping, such as furniture and large structural components.
Micro Injection Molding – For small, detailed parts
Micro injection molding is used for producing extremely small, high-precision parts, often in the medical and electronics industries. This method requires specialized machines capable of handling tiny amounts of plastic while maintaining strict tolerances. It is used to create components such as hearing aids, microfluidic devices, and miniature gears.
Common Materials Used in Injection Molding
The choice of material in injection molding depends on factors such as strength, flexibility, temperature resistance, and cost. Different types of plastics offer unique properties that suit various applications.
Thermoplastics (e.g., ABS, PP, PE, Nylon)
Thermoplastics are widely used because they can be melted and reshaped multiple times without losing their properties. Common thermoplastics include acrylonitrile butadiene styrene (ABS), polypropylene (PP), polyethylene (PE), and nylon. ABS is known for its toughness and impact resistance, making it popular in automotive and consumer goods. Polypropylene is lightweight and resistant to chemicals, commonly used in packaging and medical applications. Polyethylene is flexible and durable, used in containers and piping. Nylon is strong and wear-resistant, often found in mechanical parts and textiles.
Thermosetting Plastics (e.g., Epoxy, Phenolics)
Thermosetting plastics differ from thermoplastics because they permanently harden once molded. They cannot be remelted or reshaped, making them ideal for high-temperature applications. Examples include epoxy, phenolics, and melamine. Epoxy is used in adhesives and coatings due to its strong bonding properties. Phenolics are heat-resistant and commonly found in electrical components. Melamine is used in heat-resistant kitchenware and countertops.
Elastomers (Rubber-like materials)
Elastomers, or rubber-like materials, provide flexibility and durability. These materials return to their original shape after stretching or compressing, making them ideal for seals, gaskets, and soft-touch components. Thermoplastic elastomers (TPE) and silicone rubber are common choices in applications requiring a combination of softness and strength.
Material selection is critical in injection molding, as different plastics offer varying properties that affect the final product’s performance. Strength determines the product’s durability and load-bearing capacity. Flexibility is important for parts that require bending or stretching. Temperature resistance ensures that the plastic can withstand heat without deforming. Other considerations include chemical resistance, UV stability, and cost-effectiveness to ensure the material meets the specific needs of the application.
Advantages and Disadvantages of Injection Molding
Injection molding is one of the most efficient and widely used manufacturing processes for plastic parts. However, like any manufacturing method, it has both benefits and drawbacks that should be considered before choosing it for production.
High Efficiency for Mass Production
Injection molding is ideal for large-scale manufacturing. Once the mold is created, the process can produce thousands or even millions of identical parts quickly. Modern machines are highly automated, further improving production speed and efficiency.
Precise and Consistent Parts
The process allows for tight tolerances and high precision, ensuring that each part is nearly identical. This consistency is crucial in industries such as medical, automotive, and aerospace, where uniformity is essential for product performance and safety.
Variety of Materials Available
Manufacturers can choose from a wide range of thermoplastics, thermosets, and elastomers to meet specific application needs. Additives such as colorants, fillers, and reinforcements can also be mixed into the plastic to enhance strength, flexibility, or appearance.
Low Labor Costs
Once set up, the process is mostly automated, requiring minimal human intervention. This reduces labor costs and increases production efficiency, making injection molding a cost-effective solution for mass production.
Minimal Material Waste
The process generates very little waste since excess plastic can often be recycled and reused in future production runs. This makes injection molding more environmentally friendly than many other manufacturing techniques.
High Initial Mold Cost
One of the biggest drawbacks is the high cost of designing and creating molds. Precision molds are made from durable materials like steel or aluminum, requiring significant investment upfront. This makes injection molding less suitable for small-scale production.
Long Lead Time for Mold Creation
The design and fabrication of a mold can take weeks or even months, depending on complexity. Any design changes require modifying or rebuilding the mold, further adding to lead times.
Limited Flexibility Once the Mold is Made
Once a mold is created, altering the product design is difficult and expensive. Any modifications require either reworking the existing mold or creating a completely new one, making it essential to finalize designs before production begins.
Not Ideal for Short Production Runs
Due to high tooling costs, injection molding is not cost-effective for low-volume production. Alternative methods like 3D printing or CNC machining are better suited for prototyping or small-batch manufacturing.
Applications of Injection Molding Process Industries
Injection molding is widely used across many industries due to its efficiency and ability to produce high-quality, durable parts.
Automotive
The automotive industry relies heavily on injection molding to manufacture a variety of components, including bumpers, dashboards, interior panels, and engine parts. These plastic parts must be strong, heat-resistant, and lightweight to improve fuel efficiency and vehicle performance.
Consumer Products
Many everyday items are made using injection molding, such as toys, kitchenware, storage containers, and electronic gadgets. The ability to create colorful, durable, and cost-effective products makes this process ideal for consumer goods.
Medical Industry
Medical devices and equipment require high precision and biocompatible materials. Injection molding is used to produce syringes, prosthetics, implants, and surgical instruments. The process ensures that medical products meet strict regulatory standards and maintain consistent quality.
Electronics
Injection molding is commonly used in the electronics industry to produce durable plastic casings and components for phones, laptops, and home appliances. The ability to create complex, lightweight designs with insulating properties makes it an ideal manufacturing method for electronic housings.
Aerospace and Defense
Lightweight and high-strength plastic components are essential in the aerospace and defense industries. Injection molding is used to manufacture aircraft interior parts, lightweight structural components, and specialized military-grade equipment. These parts must meet strict safety and performance standards.
Cost Considerations in Injection Molding Process
The cost of injection molding varies based on several factors, including mold design, material selection, and production volume. Understanding these cost drivers can help manufacturers optimize their budget and reduce expenses.
Factors Affecting Cost
Mold complexity is one of the most significant cost factors. A simple mold with minimal features is cheaper to produce than a complex mold with intricate details, multiple cavities, or moving parts. Material selection also impacts cost, as different plastics have varying prices based on their properties and availability. Production volume plays a crucial role, as higher quantities reduce the per-unit cost, making injection molding more economical for large-scale manufacturing.
Cost Comparison: Injection Molding vs. 3D Printing vs. CNC Machining
Injection molding is the most cost-effective method for mass production, while 3D printing is ideal for prototyping and small-batch production. CNC machining is best suited for precision metal or plastic parts but is typically more expensive than injection molding for large quantities. Choosing the right method depends on production needs, budget, and material requirements.
How to Reduce Costs Without Sacrificing Quality
Design optimization is key to reducing costs while maintaining product quality. Simplifying part geometry, reducing unnecessary features, and minimizing material usage can lower expenses. Selecting cost-effective materials that meet performance requirements without overengineering the product can also help. Additionally, using multi-cavity molds allows multiple parts to be produced simultaneously, improving efficiency and reducing per-unit costs.
Efficient production planning, automation, and minimizing waste further contribute to cost savings. Partnering with an experienced manufacturer can also help optimize design and production processes to achieve the best balance of cost and quality.
Future Trends in Injection Molding Process Technology
The injection molding industry continues to evolve with technological advancements that improve efficiency, sustainability, and precision. Emerging trends are shaping the future of manufacturing, making the process smarter, more sustainable, and highly adaptable to changing demands.
Industry 4.0 & Smart Factories
The integration of Industry 4.0 technologies is revolutionizing injection molding by making factories more automated and data-driven. The use of the Internet of Things (IoT) allows machines to communicate in real time, optimizing production efficiency and minimizing downtime. Sensors embedded in molding machines monitor temperature, pressure, and cycle times, ensuring precise control over the process. With predictive maintenance powered by AI, manufacturers can detect issues before they cause breakdowns, reducing repair costs and improving uptime.
Sustainable & Biodegradable Plastics
Environmental concerns are pushing the injection molding industry toward more sustainable materials. Biodegradable plastics, such as polylactic acid (PLA) and polyhydroxyalkanoates (PHA), are being increasingly adopted to reduce plastic waste. Recycled plastics are also being used to create new products, minimizing reliance on virgin materials. Innovations in bio-based polymers offer solutions that maintain durability while being compostable or recyclable. As regulations on plastic waste tighten, manufacturers are investing in sustainable alternatives to meet global environmental standards.
AI & Machine Learning in Quality Control
Artificial intelligence and machine learning are transforming quality control in injection molding. AI-powered systems analyze data from production runs to detect defects, optimize material usage, and improve consistency. Machine learning algorithms can predict potential defects based on historical data, allowing manufacturers to adjust parameters before flaws occur. This reduces waste and ensures that only high-quality parts are produced. Automated inspection systems using computer vision further enhance defect detection, reducing the need for manual quality checks.
Advancements in 3D Printing for Rapid Prototyping
3D printing is playing a crucial role in accelerating product development in injection molding. Traditionally, creating a new mold requires significant time and cost investment. With advancements in additive manufacturing, prototypes and even molds can now be 3D printed in a fraction of the time, allowing for faster testing and design iterations. Hybrid approaches combining 3D printing and injection molding are being explored to create complex designs with greater efficiency. The ability to produce custom and low-volume parts through 3D printing is expanding the capabilities of traditional injection molding.
Conclusion Injection Molding Process
Injection molding remains a dominant manufacturing process due to its efficiency, precision, and scalability. It allows for mass production of high-quality plastic parts across various industries, from automotive to medical devices. Despite the initial costs of mold creation, the process offers long-term benefits in terms of production speed, material variety, and cost-effectiveness.
With emerging technologies such as automation, AI-driven quality control, sustainable materials, and 3D printing integration, the future of injection molding is set to be even more efficient and environmentally friendly. Manufacturers embracing these innovations will stay competitive in an industry that continues to evolve.
For those looking to learn more about injection molding or explore manufacturing opportunities, partnering with industry experts and staying updated on technological advancements can provide a strategic advantage. Whether you are a product designer, manufacturer, or business owner, understanding the latest trends and best practices in injection molding can help you make informed decisions in your production process.