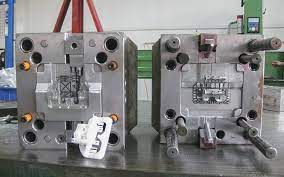
Plastic injection molding is a process used to create plastic parts by injecting molten plastic into a mold. The design of the mold is one of the most important steps in this process. A well-designed mold helps create high-quality parts, reduces defects, and improves production efficiency. This blog will explore how plastic injection molds are designed, the different types of molds, and key factors to consider in the design process.
What is a Plastic Injection Mold
A plastic injection mold is a tool used to shape plastic parts. It consists of two halves that come together to form a cavity where the plastic is injected and cooled. The mold is designed to withstand high temperatures and pressure during the injection process. Once the plastic hardens, the mold opens, and the part is ejected. Molds can be simple or complex, depending on the shape and size of the part being made.
Main Components of a Plastic Injection Mold
A plastic injection mold has several important parts. The mold base holds everything together. The cavity and core are the shaped sections that create the part. The runner system is a set of channels that direct the molten plastic into the cavity. Gates control the flow of plastic into the mold. The cooling system helps the plastic cool and harden quickly. The ejector system removes the part from the mold once it is finished. Each of these components plays a key role in making sure the final product is accurate and defect-free.
Important Design Considerations
Wall Thickness
One of the most important factors in mold design is wall thickness. The walls of the plastic part should be the same thickness throughout. Uneven walls can cause problems like warping, sink marks, or incomplete filling of the mold. If the walls are too thick, the part may take too long to cool. If they are too thin, the plastic may not fill the mold properly. Keeping a consistent wall thickness helps ensure a strong and well-formed part.
Draft Angles
Draft angles are slight tapers added to the walls of a molded part to help it come out of the mold easily. Without draft angles, the part may get stuck in the mold and cause damage. Even a small draft angle of one or two degrees can make a big difference. Draft angles also help reduce wear on the mold, making it last longer and work more efficiently.
Radii and Corners
Sharp corners in a mold can create weak points in the final part. Adding rounded corners, known as radii, helps improve strength and reduces stress. This also allows the plastic to flow more smoothly into the mold, preventing defects. A good rule is to use a radius of at least half the wall thickness to create a stronger part.
Gating Design
The gate is where the molten plastic enters the mold cavity. The location and type of gate can affect the way the plastic flows and cools. Some common types of gates include edge gates, which are placed along the outer edge of a part, and submarine gates, which allow automatic trimming of excess plastic. The choice of gate type depends on the size and shape of the part, as well as the quality of the finish needed.
Cooling System
Cooling is a crucial part of the injection molding process. If the plastic does not cool evenly, it can lead to warping or shrinkage. Mold designers add cooling channels to help control the temperature inside the mold. These channels carry water or another cooling liquid to keep the mold at the right temperature. A well-designed cooling system helps reduce cycle time and ensures a high-quality final product.
Types of Injection Molds
Single Cavity Mold
A single cavity mold makes one part per cycle. This type of mold is often used for prototypes or small production runs. It is less expensive to make but takes longer to produce large numbers of parts.
Multi-Cavity Mold
A multi-cavity mold produces several identical parts in one cycle. This increases production speed and efficiency. It is commonly used when a large number of the same part is needed.
Family Mold
A family mold can make different parts in one cycle. These parts are usually part of the same assembly. This type of mold helps save time and cost by producing multiple components at once.
Hot Runner Mold
A hot runner mold uses a heated system to keep plastic melted inside the mold. This prevents waste and reduces cycle time. However, hot runner molds are more expensive to make and maintain.
Cold Runner Mold
A cold runner mold is a simpler and cheaper option. It allows plastic to flow into the mold naturally, but it creates excess plastic that must be trimmed and recycled. This type of mold is often used for lower-cost production.
Material Selection for Molds
The material used to make the mold affects its durability and cost. Aluminum molds are lightweight and less expensive, making them ideal for low-volume production. P20 steel molds are strong and can be used for mid-volume production. H13 steel molds are heat-resistant and durable, making them suitable for long production runs. Stainless steel molds resist corrosion and are often used in medical and food-grade applications. Choosing the right material for a mold depends on the number of parts needed and the type of plastic being used.
Common Mold Defects and How to Prevent Them
Warping
Warping happens when a part bends or twists after cooling. It is usually caused by uneven cooling or incorrect mold design. To prevent warping, mold designers must ensure uniform wall thickness and proper cooling channels.
Short Shots
A short shot occurs when the plastic does not completely fill the mold cavity. This can be caused by low injection pressure, poor venting, or improper gating design. Increasing the pressure and improving the mold’s venting system can help prevent short shots.
Flash
Flash is excess plastic that leaks out of the mold and forms a thin layer on the part. This happens when the mold does not close tightly or when there is too much injection pressure. Improving clamping force and checking for worn-out mold parts can help prevent flash.
Sink Marks
Sink marks are small dents or depressions that appear on the surface of a part. They are caused by uneven cooling or thick sections of plastic. To avoid sink marks, designers should use ribs and support structures instead of making thick sections.
Choosing the Right Manufacturing Method Plastic Injection Mold Design
3D Printing
3D printing is good for making small numbers of plastic parts with complex designs. It allows quick testing of new ideas but does not have the strength and finish quality of injection molding. It is mostly used for prototyping rather than mass production.
CNC Machining
CNC machining is used to make strong, precise plastic parts from solid blocks. It is best for parts that need to be very accurate or cannot be made with injection molding. However, it is slower and more expensive for high-volume production.
Urethane Casting
Urethane casting is a process where liquid plastic is poured into a silicone mold. It is used for mid-range production of up to a few thousand parts. It provides good quality and flexibility but is not as durable as injection molding for high production runs.
Finding the Right Injection Molding Partner
Experience and Expertise
Choosing the right manufacturer is important for making high-quality plastic parts. An experienced company can help improve mold design and production efficiency.
Quality Assurance
A good manufacturer should have strict quality control processes. This includes checking dimensions, testing materials, and making sure parts meet design requirements.
Flexibility and Responsiveness
Since low-volume production often requires design changes, a good manufacturing partner should be able to adapt to new requirements and offer fast turnaround times.
Conclusion Plastic Injection Mold Design
Plastic injection mold design is a complex process that requires careful planning. Factors like wall thickness, draft angles, cooling systems, and gating design all play a role in making high-quality parts. Choosing the right type of mold and material is also essential for cost-effective production. Understanding these design principles helps ensure successful manufacturing with fewer defects and higher efficiency.