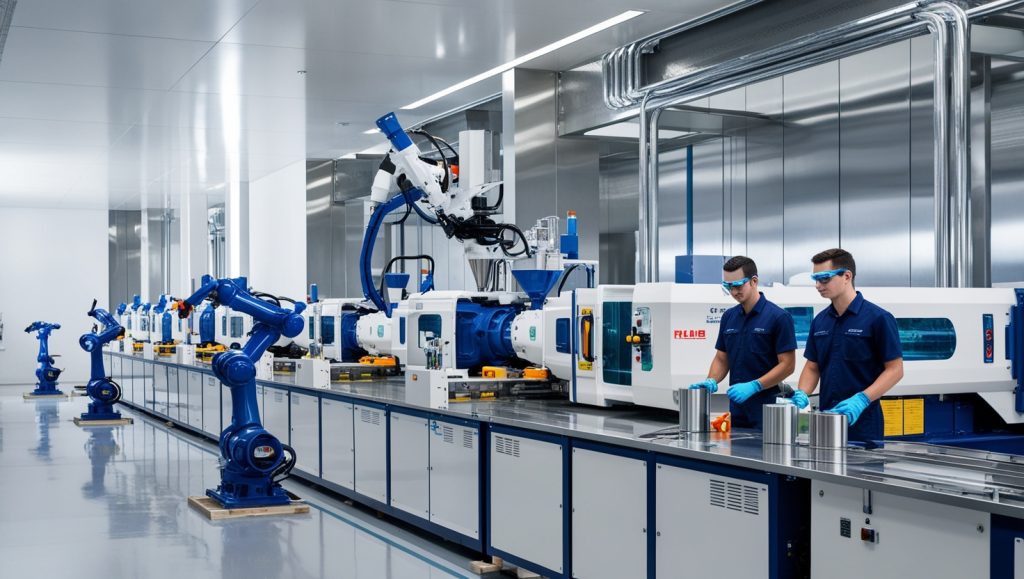
Plastic injection molding is a cornerstone of modern manufacturing, responsible for producing everything from automotive components to medical devices and consumer electronics. This process enables high-volume production of complex, durable plastic parts with excellent precision. In this deep dive, we’ll explore the plastic injection molding industry, highlight leading companies, analyze trends, and discuss key factors shaping the future of this manufacturing sector.
What is Plastic Injection Molding?
Plastic injection molding is a manufacturing process in which molten plastic is injected into a mold cavity, cooled, and solidified to form a specific shape. The process is favored for its ability to create intricate designs with high repeatability and minimal waste. It is used in industries such as:
- Automotive (dashboard components, interior panels)
- Medical (syringes, implants, diagnostic devices)
- Consumer Electronics (laptop casings, smartphone shells)
- Packaging (bottle caps, food containers)
- Industrial Components (gears, fasteners, machine parts)
Key Players in the Plastic Injection Molding Industry
Several companies dominate the plastic injection molding industry, providing expertise in design, prototyping, and full-scale production. Below are some of the most recognized names in this space.
Xometry Enterprise
- Founded: 2015
- Headquarters: Maryland, USA
- Specialties: On-demand manufacturing, rapid prototyping
- Industries Served: Aerospace, medical, automotive, consumer electronics
- Strengths: Extensive global network, automated quoting system, scalability
Xometry operates a vast network of manufacturing partners, offering services such as plastic injection molding, CNC machining, and 3D printing. Their on-demand platform allows businesses to source high-quality components quickly.
Berry Global, Inc.
- Founded: 1967
- Headquarters: Indiana, USA
- Specialties: Sustainable packaging solutions, engineered plastic products
- Industries Served: Healthcare, industrial, consumer packaging
- Strengths: Sustainability focus, high-volume production, global presence
Berry Global specializes in plastic injection molding for the packaging industry, with an emphasis on sustainability. The company has developed several eco-friendly plastic solutions, such as biodegradable and recycled resins.
Proto Labs, Inc.
- Founded: 1999
- Headquarters: Minnesota, USA
- Specialties: Rapid prototyping, small-batch production
- Industries Served: Medical, automotive, consumer electronics
- Strengths: Fast turnaround, digital manufacturing platform
Proto Labs is known for its quick turnaround times, providing prototypes and low-volume plastic injection molding services. Their digital manufacturing system allows clients to upload 3D CAD files and receive instant quotes.
Jabil Inc.
- Founded: 1966
- Headquarters: Michigan, USA
- Specialties: Contract manufacturing, high-precision injection molding
- Industries Served: Healthcare, packaging, automotive, consumer electronics
- Strengths: High-volume manufacturing, global supply chain
Jabil is a contract manufacturer that provides injection molding solutions across various industries. They work closely with Fortune 500 companies to develop high-quality, cost-effective plastic components.
The Rodon Group
- Founded: 1956
- Headquarters: Pennsylvania, USA
- Specialties: High-volume injection molding, mold design
- Industries Served: Medical, food and beverage, pharmaceuticals
- Strengths: USA-based production, cost-effective solutions
The Rodon Group focuses on high-volume production for sectors requiring precision plastic components. They are particularly strong in medical device manufacturing and food-safe plastic parts.
Ace Mold
- Founded: 1996
- Headquarters: Shenzhen, China
- Specialties: Custom injection molding, precision mold manufacturing
- Industries Served: Automotive, medical devices, consumer electronics, industrial components
- Strengths: Strong engineering expertise, cost-effective production, global reach
Ace Mold is a China-based manufacturer that provides custom plastic injection molding services. They offer full-scale solutions from mold design to high-volume production, making them a trusted partner for global companies looking for precision and affordability.
Key Factors to Consider When Choosing a Plastic Injection Molding Company
Selecting the right plastic injection molding company depends on various factors, including:
Manufacturing Capabilities
- Can the company handle low-volume prototyping as well as high-volume production?
- Does it offer multi-material injection molding, overmolding, or insert molding?
Industry Specialization
- Some companies specialize in medical devices, while others focus on automotive or consumer electronics. Choosing an industry-specific manufacturer ensures expertise in compliance and regulations.
Sustainability Practices
- As environmental concerns grow, companies are shifting toward recyclable plastics and biodegradable materials. A manufacturer with sustainability initiatives can help businesses meet eco-friendly goals.
Quality Control and Certifications
- Certifications such as ISO 9001 (Quality Management Systems) and ISO 13485 (Medical Devices) indicate a company’s commitment to high-quality standards.
Lead Time and Production Speed
- Fast turnaround times are crucial, especially for prototyping and product development. Companies like Proto Labs excel in this area.
Cost Efficiency
- Price competitiveness depends on the company’s location, automation level, and production efficiency. Some U.S.-based manufacturers offer cost savings by reducing import tariffs and shipping costs.
Comparison of Leading Plastic Injection Molding Companies
Company | Founded | Headquarters | Specialties | Industries Served | Strengths |
---|---|---|---|---|---|
Xometry Enterprise | 2015 | Maryland, USA | On-demand manufacturing, rapid prototyping | Aerospace, Medical, Automotive, Electronics | Extensive network, scalability |
Berry Global, Inc. | 1967 | Indiana, USA | Sustainable packaging, industrial plastic products | Healthcare, Industrial, Packaging | Sustainability, high-volume production |
Proto Labs, Inc. | 1999 | Minnesota, USA | Rapid prototyping, small-batch production | Medical, Automotive, Electronics | Fast turnaround, digital manufacturing |
Jabil Inc. | 1966 | Michigan, USA | Contract manufacturing, injection molding | Healthcare, Packaging, Automotive | High-volume manufacturing, global reach |
The Rodon Group | 1956 | Pennsylvania, USA | High-precision injection molding | Medical, Food & Beverage, Pharmaceuticals | Cost-effective, USA-based production |
Ace Mold | 1996 | Shenzhen, China | Custom injection molding, precision mold manufacturing | Automotive, Medical, Electronics, Industrial | Cost-effective, strong engineering expertise |
Trends in the Plastic Injection Molding Industry
Sustainable Materials
The increasing awareness of environmental concerns has pushed manufacturers toward sustainable materials. Traditional petroleum-based plastics, such as ABS (Acrylonitrile Butadiene Styrene) and Polypropylene, are being replaced or supplemented with eco-friendly alternatives.
- Biodegradable Plastics: Materials such as PLA (Polylactic Acid) and PCL (Polycaprolactone) break down naturally in the environment, reducing long-term waste accumulation. These are particularly useful in packaging and medical applications.
- Recyclable Plastics: Companies are investing in recycling programs to reuse materials like PET (Polyethylene Terephthalate) and HDPE (High-Density Polyethylene). Closed-loop recycling systems are being developed to ensure minimal material loss.
- Bio-Based Resins: Innovations in bio-plastics, derived from plant-based sources like cornstarch or sugarcane, are helping manufacturers reduce their carbon footprint.
- Legislation & Compliance: Governments worldwide are enforcing stricter regulations on plastic waste. The European Union's Single-Use Plastics Directive and China's plastic restriction policies are influencing manufacturers to adopt greener alternatives.
Companies such as Berry Global and Jabil are leading the way in sustainable plastics by implementing circular economy principles and adopting bio-based materials in their production processes.
Automation and AI Integration
Automation is revolutionizing plastic injection molding by increasing efficiency, reducing waste, and improving quality control. AI-driven systems and robotics are transforming how manufacturers operate.
- Robotics in Injection Molding: Advanced robotic arms and automated handling systems enhance precision in material feeding, molding, and assembly processes. This reduces defects and improves cycle times.
- AI-Powered Quality Control: Machine learning algorithms analyze production data in real time to detect defects, predict maintenance needs, and optimize production parameters. This reduces waste and downtime.
- Smart Factories: The integration of IoT (Internet of Things) allows real-time monitoring of machinery, ensuring better control over production environments. Sensors collect data on temperature, pressure, and material flow to optimize output.
- Automated Material Handling: AI-driven systems are being used to measure and distribute plastic granules efficiently, reducing material wastage and ensuring consistent quality.
Companies such as Xometry and Proto Labs have embraced digital manufacturing platforms that streamline ordering and production, significantly reducing turnaround times.
Advanced Molding Techniques
The demand for more complex and precise plastic components has led to innovations in molding techniques. These advancements enable the production of lightweight, durable, and intricate parts.
- Micro-Molding: This technique allows for the creation of ultra-small plastic components, often used in medical devices and electronics. Micro-molding enables the production of high-precision parts with tight tolerances.
- Overmolding: This process involves molding multiple materials into a single component, improving product strength, grip, and aesthetics. Overmolding is widely used in medical devices, tools, and automotive components.
- Gas-Assisted Injection Molding: This technique reduces material usage while maintaining structural integrity by injecting gas into molten plastic to create hollow sections.
- Multi-Shot Injection Molding: This enables the combination of multiple plastic types in a single molding cycle, allowing for enhanced product performance and design flexibility.
Companies such as Ace Mold specialize in precision molding techniques that cater to industries requiring high-detail components, such as medical and automotive sectors.
On-Demand Manufacturing and 3D Printing
The rise of digital manufacturing has introduced more flexible production methods, allowing companies to reduce inventory costs and shorten lead times.
- Just-in-Time (JIT) Manufacturing: On-demand production allows companies to manufacture only what is needed, reducing waste and storage costs.
- 3D-Printed Molds: While traditional mold-making can take weeks, 3D printing allows for rapid prototyping and mold production in days, significantly reducing development cycles.
- Customization and Small Batch Production: With on-demand services, businesses can order small quantities of custom plastic parts without the high upfront costs associated with traditional injection molding.
- Cloud-Based Manufacturing Platforms: Companies like Xometry provide instant pricing and production capabilities, allowing businesses to order injection-molded parts with minimal setup.
These innovations make it easier for startups and small businesses to enter the market without significant capital investment.
Regional Market Growth
The global plastic injection molding market is expected to experience steady growth, driven by industrial expansion and increasing consumer demand.
- Market Size and Projections: The injection-molded plastics market is expected to grow from $330 billion in 2024 to $346 billion in 2025.
- China’s Dominance: China remains the largest producer of injection-molded plastics, expected to reach $95.2 billion by 2030, growing at a CAGR of 7%.
- Growth in the U.S.: The U.S. market for injection-molded plastics was valued at $87.9 billion in 2024, fueled by increasing demand in automotive and medical device sectors.
- Expansion in Emerging Markets: Countries like India and Vietnam are becoming attractive destinations for plastic manufacturing due to lower labor costs and supportive government policies.
Jabil and Ace Mold are among the companies expanding their global reach by establishing facilities in emerging markets to meet growing demand.
Challenges in the Plastic Injection Molding Industry
Raw Material Costs
Fluctuations in the cost of raw materials can significantly impact production expenses.
- Petroleum-Based Plastics: The prices of ABS, Polypropylene, and Polycarbonate depend on crude oil prices, which are volatile due to global market conditions.
- Supply Chain Disruptions: The COVID-19 pandemic and geopolitical issues have led to shortages in raw materials, causing price spikes.
- Alternative Materials: Manufacturers are investing in bio-based and recycled plastics to mitigate cost volatility and reduce dependency on petroleum-derived resins.
Environmental Regulations
Governments are enforcing stricter environmental policies that affect the production and disposal of plastic products.
- Single-Use Plastic Bans: Several countries, including the EU member states, have imposed bans on single-use plastics, pushing manufacturers to explore biodegradable alternatives.
- Extended Producer Responsibility (EPR): Companies are being held accountable for the entire lifecycle of their plastic products, including recycling and waste management.
- Sustainability Certifications: Companies must meet standards such as ISO 14001 (Environmental Management Systems) to maintain compliance with global regulations.
Manufacturers like Berry Global are at the forefront of sustainable production, investing in closed-loop recycling programs.
Supply Chain Disruptions
The injection molding industry heavily relies on stable supply chains for raw materials, machinery, and transportation.
- Shipping Delays: Global container shortages and port congestions have disrupted the timely delivery of plastic resins and components.
- Geopolitical Factors: Trade tensions between major economies like the U.S. and China have led to tariffs on plastic products, increasing costs.
- Localization Strategies: Companies are setting up regional production facilities to reduce dependence on foreign suppliers and improve lead times.
Ace Mold and Jabil have diversified their supply chains by establishing manufacturing hubs in multiple regions to counteract disruptions.
Rising Competition
As more companies enter the market, differentiation is becoming crucial for survival.
- Price Pressure: Increased competition has led to price wars, forcing companies to either lower costs or improve product value.
- Customization and Innovation: Companies offering unique molding techniques, such as overmolding and multi-shot molding, gain a competitive edge.
- Customer Service and Lead Time: Faster production cycles and personalized customer service play a significant role in maintaining client loyalty.
Final Thoughts
Plastic injection molding remains a vital part of modern manufacturing, providing cost-effective and high-quality solutions across industries. Companies like Xometry, Berry Global, Proto Labs, Jabil, The Rodon Group, and Ace Mold continue to lead the sector, driven by advancements in sustainability, automation, and precision molding.
With the growing demand for eco-friendly materials, rapid prototyping, and advanced manufacturing techniques, the future of plastic injection molding is set for exciting developments. Whether you’re a startup looking for small-batch production or a large enterprise needing high-volume manufacturing, choosing the right partner will ensure product success.