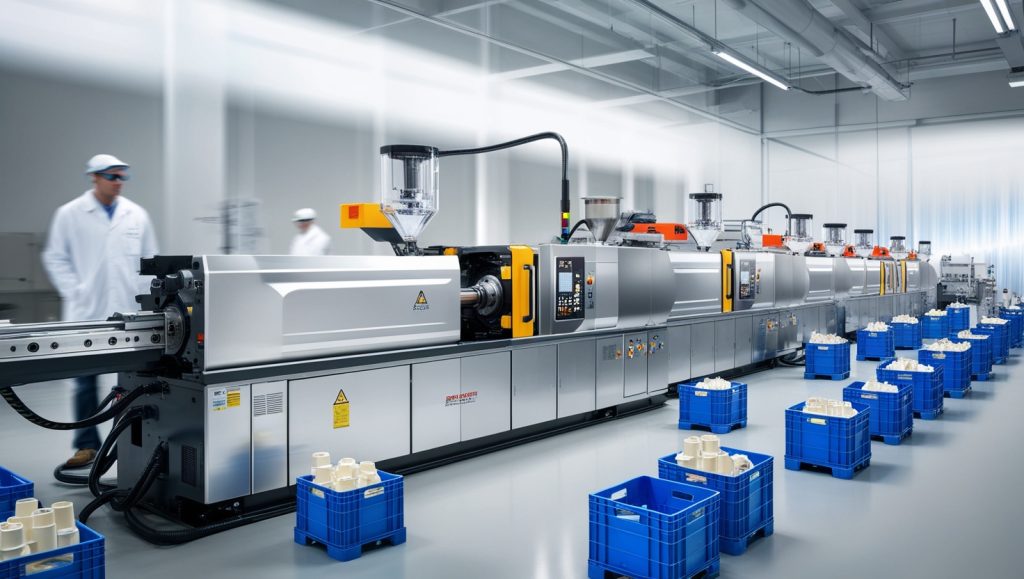
Plastic injection molding stands as a cornerstone in modern manufacturing, enabling the mass production of intricate plastic components with remarkable precision and efficiency. When it comes to high-volume production, this process offers unparalleled advantages, making it the go-to method for industries ranging from automotive to consumer electronics. In this guide, we'll explore the intricacies of plastic injection molding for high-volume production, delve into its benefits, compare it with other manufacturing methods, and provide insights into selecting the right partner for your manufacturing needs.
Understanding Plastic Injection Molding
At its core, plastic injection molding involves melting plastic pellets and injecting the molten material into a mold cavity. Once cooled, the plastic solidifies into the desired shape, and the part is ejected, ready for use. This process is highly repeatable, making it ideal for producing large quantities of identical parts with consistent quality.
Advantages of Injection Molding for High-Volume Production
- High Efficiency and Productivity: Injection molding is renowned for its rapid production cycles. Once the initial setup is complete, machines can produce thousands of parts in a short period, ensuring that high-volume demands are met promptly.
- Consistent Quality: The precision of injection molding ensures that each part produced adheres to strict tolerances, maintaining uniformity across large production runs. This consistency is crucial for industries where exact specifications are mandatory.
- Cost-Effectiveness: While the initial investment in tooling can be substantial, the cost per part decreases significantly as production volumes increase. This economy of scale makes injection molding highly cost-effective for large orders.
- Material Versatility: A wide range of thermoplastics can be used in injection molding, allowing manufacturers to select materials that best suit the mechanical and aesthetic requirements of the final product.
- Minimal Waste: The process is designed to use only the necessary amount of material, reducing waste. Additionally, excess material can often be recycled, contributing to more sustainable manufacturing practices.
Comparing Injection Molding with Other Manufacturing Methods
When considering high-volume production, it's essential to evaluate how injection molding stacks up against other manufacturing techniques:
Manufacturing Method | Advantages | Disadvantages |
---|---|---|
Injection Molding | - High production speed - Consistent part quality - Suitable for complex geometries |
- High initial tooling cost - Not economical for low-volume production |
3D Printing | - Low initial setup cost - Ideal for prototyping and complex designs - No need for tooling |
- Slower production speed - Higher cost per part - Limited material options |
CNC Machining | - High precision - Suitable for both metals and plastics - No need for molds |
- Material wastage - Longer production times - Higher cost for complex parts |
Blow Molding | - Ideal for hollow parts like bottles - Faster production for specific shapes |
- Limited to hollow designs - Less precise than injection molding |
Key Considerations for High-Volume Injection Molding
- Tooling Design and Quality: The mold is the heart of the injection molding process. Investing in high-quality tooling ensures durability and precision, which are vital for maintaining part consistency over large production runs.
- Material Selection: Choosing the right plastic material affects the product's strength, flexibility, and appearance. Collaborate with material experts to select a resin that aligns with your product's requirements.
- Manufacturing Partner: Partnering with an experienced injection molding company can significantly impact the success of your project. Look for partners with a proven track record in high-volume production, robust quality control systems, and the ability to scale operations as needed.
Case Studies Highlighting High-Volume Injection Molding Success
To illustrate the practical applications and benefits of high-volume injection molding, let's explore a few real-world examples:
Case Study 1: Consumer Electronics Enclosures
A leading consumer electronics company needed to produce enclosures for a new line of smart home devices. They required a manufacturing process that could deliver high precision and aesthetic appeal at large volumes. By opting for injection molding, they achieved:
- Consistent Quality: Each enclosure met strict dimensional tolerances, ensuring compatibility with internal components.
- Cost Savings: The high-volume production run led to a reduced cost per unit, optimizing profitability.
- Aesthetic Flexibility: Injection molding allowed for various surface finishes and colors, enhancing the product's market appeal.
Case Study 2: Automotive Components
An automotive manufacturer sought to produce durable interior components, such as dashboard panels and door handles, for their latest vehicle model. Injection molding provided:
- Material Durability: The use of high-strength thermoplastics ensured the components could withstand daily wear and tear.
- Efficient Production: The ability to produce large quantities in a short time frame kept the assembly line moving without delays.
- Integration of Features: Complex features like mounting points and clips were integrated directly into the molded parts, reducing the need for additional assembly steps.
Case Study 3: Medical Device Housings
A medical device company required sterile, reliable housings for a new diagnostic tool. Injection molding offered:
- Precision: Tight tolerances were maintained to ensure the proper functioning of sensitive internal components.
- Compliance: The process adhered to strict medical manufacturing standards, ensuring patient safety.
- Scalability: As demand for the device grew, injection molding facilitated rapid scaling of production without compromising quality.
Selecting the Right Injection Molding Partner
Choosing the right manufacturing partner is crucial for the success of high-volume injection molding projects. Consider the following factors:
- Experience and Expertise: Look for companies with a proven history in injection molding, particularly in your industry. Their experience can provide valuable insights and anticipate potential challenges.
- Capacity and Scalability: Ensure the manufacturer has the capacity to handle your current volume requirements and can scale up if demand increases.
- Quality Assurance: Robust quality control measures are essential. Verify that the manufacturer follows international quality standards and has certifications relevant to your industry.
- Communication and Support: Open and transparent communication fosters a collaborative relationship, ensuring that any issues are promptly addressed, and project milestones are met.
- Technological Capabilities: Manufacturers that invest in the latest technologies, such as automation and advanced monitoring systems, can offer improved efficiency and part quality.
Conclusion
Plastic injection molding remains a dominant force in high-volume manufacturing, offering a blend of efficiency, precision, and versatility. By understanding its advantages, comparing it with alternative methods, and carefully selecting a manufacturing partner, businesses can harness this process to deliver high-quality products that meet market demands. Whether you're in the automotive, medical, or consumer electronics industry, injection molding provides a reliable pathway to mass production success.
Frequently Asked Questions (FAQs) About Plastic Injection Molding for High-Volume Production
1. What makes plastic injection molding the best choice for high-volume production?
Plastic injection molding is ideal for high-volume production because it offers fast cycle times, high precision, and cost efficiency once the mold is created. The process ensures consistent quality across thousands or even millions of parts, making it the preferred method for industries like automotive, medical devices, consumer electronics, and packaging.
2. What are the main costs involved in plastic injection molding?
The primary costs in injection molding include:
- Tooling Costs: The mold itself can be expensive to design and manufacture, often ranging from $5,000 to $100,000+, depending on complexity.
- Material Costs: The price depends on the type of plastic used (e.g., ABS, Polypropylene, Nylon).
- Production Costs: Labor, machine operation, and maintenance.
Once the mold is created, the per-unit cost drops significantly, making it very cost-effective for high-volume production.
3. What materials are commonly used in injection molding?
A wide variety of plastics can be used, depending on the desired strength, flexibility, and resistance properties. Some of the most popular include:
- ABS (Acrylonitrile Butadiene Styrene) – Durable and impact-resistant (used in automotive and electronics).
- Polypropylene (PP) – Lightweight and chemical-resistant (used in packaging and medical devices).
- Polycarbonate (PC) – High-strength and transparent (used in lenses and safety gear).
- Nylon (PA) – Wear-resistant (used in gears and mechanical parts).
4. How long does it take to manufacture a mold for injection molding?
The design and manufacturing of a mold typically take 4 to 12 weeks, depending on complexity and material selection. While this upfront investment in time is significant, the mold can last hundreds of thousands to millions of cycles, making it highly efficient for large-scale production.
5. What are the biggest challenges in high-volume injection molding?
Some of the main challenges include:
- Initial tooling costs – The upfront expense for the mold can be high.
- Material shortages and price fluctuations – Plastic resin costs can vary based on market conditions.
- Maintaining precision at scale – Large production runs require strict quality control to prevent defects.
- Sustainability concerns – Companies are shifting towards biodegradable or recycled plastics to reduce environmental impact.
6. How can injection molding companies improve sustainability?
Manufacturers are adopting several strategies to make injection molding more environmentally friendly:
- Using recycled plastics to reduce raw material consumption.
- Implementing closed-loop manufacturing to minimize waste.
- Switching to biodegradable materials like PLA (Polylactic Acid).
- Improving energy efficiency by using advanced molding machines with lower power consumption.