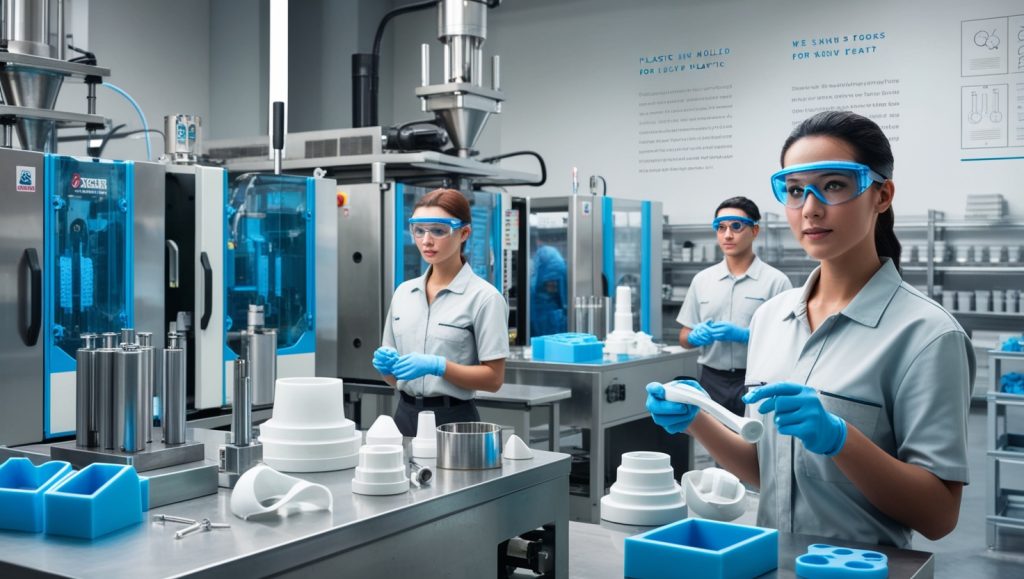
Plastic is everywhere! From toys and phone cases to car parts and kitchen utensils, plastic is an important material in our daily lives. But have you ever wondered how these plastic products are made? One of the most popular ways to produce plastic items quickly and cheaply is plastic injection molding.
In this article, we’ll explain what plastic injection molding for low-cost production means, why it’s used, and how it helps companies make affordable products. Whether you're a student, a hobbyist, or just curious about manufacturing, this guide will help you understand the process in a simple and fun way.
Why is Plastic Injection Molding Used for Low-Cost Production?
Plastic injection molding is a cost-effective way to make products, especially when producing large quantities. Here’s why:
Saves Money on Large Orders
Once a mold is made, the cost of making each plastic part is very low. This makes it perfect for companies that need thousands or even millions of the same product.
Fast and Efficient
A single mold can produce hundreds of plastic parts every hour. This helps manufacturers create products quickly, reducing labor costs.
Reduces Waste
Since the process is highly precise, there is very little wasted plastic. Some manufacturers also recycle leftover plastic, making it an eco-friendly choice.
Strong and Durable Products
Plastic injection molding allows manufacturers to create products that are both strong and lightweight. Many industries, including automotive, medical, and electronics, use this method because of its durability.
Creates Complex Shapes
Some plastic products have very complicated designs, with tiny details and unique shapes. Injection molding makes it easy to produce these designs without extra effort.
How Does Plastic Injection Molding Work?
To better understand why this process is so effective for low-cost production, let’s break it down step by step:
Step 1: Designing the Mold
Before production starts, engineers design a special mold that has the exact shape of the plastic product. These molds are usually made from metal, such as steel or aluminum, because they must withstand high temperatures and pressure.
Step 2: Choosing the Right Plastic
Different types of plastic materials are used for injection molding, depending on the product’s needs. Some plastics are flexible, while others are hard and durable.
Step 3: Melting the Plastic
Small plastic pellets are heated inside a machine until they turn into liquid. The temperature is carefully controlled to ensure the plastic melts evenly.
Step 4: Injecting the Plastic
The melted plastic is then injected at high pressure into the mold. This ensures that the liquid plastic fills every part of the mold, creating an exact replica of the design.
Step 5: Cooling and Hardening
After the mold is filled, the plastic is left to cool and solidify. This usually takes just a few seconds to a couple of minutes, depending on the size of the product.
Step 6: Removing the Final Product
Once the plastic has hardened, the mold opens, and the finished product is removed. If necessary, the product is trimmed to remove any excess plastic.
Step 7: Repeating the Process
The cycle repeats, allowing manufacturers to create thousands of identical plastic parts quickly.
Common Products Made with Plastic Injection Molding
Plastic injection molding is used in many industries to create everyday products. Some examples include:
- Toys – Action figures, dolls, and building blocks are often made using this method.
- Household Items – Plastic containers, chairs, and utensils.
- Medical Equipment – Syringes, pill bottles, and other medical tools.
- Automobile Parts – Car dashboards, bumpers, and small plastic components.
- Electronics – Phone cases, remote controls, and computer parts.
- Packaging – Bottle caps, plastic boxes, and food packaging.
Because of its versatility, plastic injection molding is one of the most widely used manufacturing methods in the world.
How is Plastic Injection Molding Cost-Effective?
Companies always look for ways to reduce production costs while maintaining quality. Plastic injection molding is ideal for low-cost production because:
Low Material Costs
Plastic is generally inexpensive, and many factories use recyclable plastics, further reducing costs.
Fast Production Time
Since each molding cycle only takes a few seconds or minutes, large quantities can be produced quickly.
Less Waste
Unlike other manufacturing methods that involve cutting and shaping plastic, injection molding produces very little scrap material.
Automation Reduces Labor Costs
Many plastic injection molding machines are automated, meaning fewer workers are needed to operate them. This helps companies save money on labor.
One Mold Can Make Thousands of Parts
Although molds can be expensive to design and create, they can be used over and over again, making them cost-effective in the long run.
Challenges of Plastic Injection Molding
While plastic injection molding is an excellent choice for low-cost production, there are some challenges:
High Initial Cost for Molds
Designing and creating a mold can be expensive, especially for complex products. However, once the mold is ready, the cost per item becomes very low.
Design Limitations
Some extremely complex designs may require additional processing or adjustments, which can increase costs.
Material Selection
Not all plastics work well with injection molding. Choosing the wrong plastic can result in weak or brittle products.
Cooling Time
Although the process is fast, larger products may take longer to cool, slowing down production.
Despite these challenges, plastic injection molding remains one of the best ways to manufacture plastic products at a low cost.
Frequently Asked Questions (FAQs) About Plastic Injection Molding for Low-Cost Production
1. Why is plastic injection molding considered a cost-effective manufacturing process?
Plastic injection molding is cost-effective because it allows for high-volume production at a low per-unit cost. Once the mold is created, each plastic part can be made quickly and efficiently, reducing labor costs and material waste. Additionally, automation further lowers production costs.
2. How much does it cost to create an injection mold?
The cost of an injection mold depends on its complexity, size, and material.
- Simple molds (for basic shapes) can cost between $5,000 - $10,000.
- More complex molds (for intricate designs or multi-part products) can range from $50,000 - $100,000 or more.
However, this cost is spread across thousands or millions of units, making production highly cost-efficient in the long run.
3. What types of plastics are used in injection molding?
Common plastics used in injection molding include:
- Polypropylene (PP) – Lightweight, flexible, and commonly used for containers.
- Acrylonitrile Butadiene Styrene (ABS) – Strong and impact-resistant, used for electronics and automotive parts.
- Polyethylene (PE) – Widely used in packaging and household items.
- Polycarbonate (PC) – Transparent and durable, often used for lenses and safety equipment.
The choice of plastic depends on the product’s required strength, flexibility, and heat resistance.
4. What are the main advantages of plastic injection molding for mass production?
- High-speed production – Can manufacture hundreds of parts per hour.
- Low per-unit cost – The more units produced, the cheaper each part becomes.
- Minimal material waste – Efficient use of plastic with the possibility of recycling excess material.
- Complex design capabilities – Can produce intricate shapes with high precision.
- Strong and lightweight parts – Ideal for industries like automotive, medical, and consumer goods.
5. How does injection molding compare to 3D printing in terms of cost and efficiency?
Feature | Injection Molding | 3D Printing |
---|---|---|
Setup Cost | High (molds are expensive) | Low (no molds needed) |
Per-Unit Cost | Very Low (after mold setup) | High (slow process) |
Production Speed | Very Fast | Slow |
Design Complexity | High (complex shapes possible) | Very High (ideal for prototypes) |
Best for | Mass production (thousands/millions of units) | Low-volume or prototype production |
While 3D printing is great for prototyping and small batches, injection molding is the superior choice for mass production due to its low cost per unit and speed.
6. Is plastic injection molding environmentally friendly?
Plastic injection molding minimizes waste because excess plastic can be recycled and reused. Additionally, manufacturers can use biodegradable plastics and energy-efficient machines to reduce environmental impact. However, like any plastic-based process, sustainability depends on responsible material sourcing and recycling efforts.