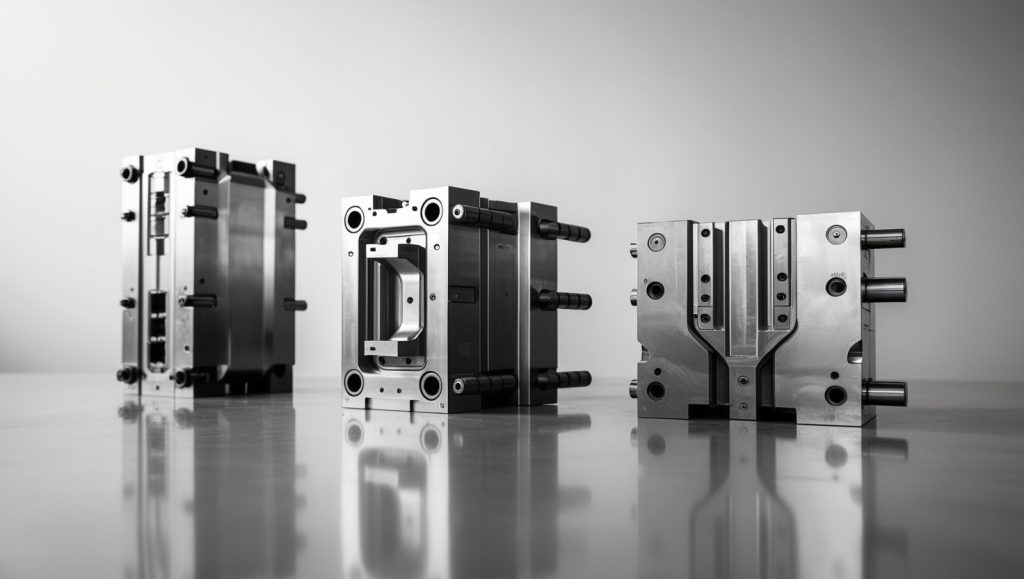
Plastic mold tooling plays a critical role in modern manufacturing, enabling the mass production of high-precision plastic parts. Whether used in the automotive, medical, or consumer goods industries, mold tooling ensures consistency, efficiency, and durability in plastic manufacturing.
Why is mold tooling so essential? The right tooling determines the quality, speed, and cost-effectiveness of production. With advances in technology, mold tooling has evolved to incorporate automation, high-precision machining, and innovative materials to enhance durability and efficiency.
This guide explores the fundamentals of plastic mold tooling, from design to manufacturing and maintenance, to help you understand its role in industrial production.
What is Plastic Mold Tooling?
Plastic mold tooling refers to the specialized molds and tooling components used to shape plastic materials into finished products. These tools define the dimensions, structure, and surface quality of plastic parts.
How Mold Tooling Works
- Design & Engineering: CAD software is used to design the mold.
- Machining & Fabrication: CNC machining, EDM, and polishing refine the mold.
- Molding Process: The mold is installed in an injection or compression molding machine.
- Ejection & Finishing: The final plastic part is removed and undergoes finishing.
Types of Plastic Mold Tooling
There are several types of mold tooling, each suited for different production needs.
Injection Mold Tooling
- Used for high-precision, high-volume plastic part production.
- Ideal for automotive, electronics, and consumer goods.
Blow Mold Tooling
- Used for making hollow plastic products like bottles and containers.
- Relies on air pressure to shape the plastic.
Compression Mold Tooling
- Best for thermoset plastics, where heated plastic is pressed into a mold.
- Common in electrical and automotive applications.
Transfer Mold Tooling
- Used for making parts with inserts, such as rubber-sealed components.
- Combines features of injection and compression molding.
Materials Used in Plastic Mold Tooling
Selecting the right material for a mold determines its durability, cost, and performance.
Common Metals for Mold Tooling
- Steel (P20, H13, S136): High durability and wear resistance.
- Aluminum: Lightweight and cost-effective for low-volume production.
- Beryllium Copper: Great for heat dissipation but expensive.
Coatings & Surface Treatments
- Nickel Plating: Prevents corrosion.
- Titanium Coating: Increases hardness.
- Teflon Coating: Reduces friction and improves release.
The Plastic Mold Tooling Process
Design & CAD Modeling
- Engineers use software like SolidWorks and AutoCAD to design precise molds.
Machining & Fabrication
- CNC machines and EDM create complex mold structures.
Assembly & Polishing
- The mold is assembled and finished for optimal performance.
Testing & Validation
- Mold trials ensure quality before mass production.
Key Components of Plastic Mold Tooling
A plastic mold consists of several essential components:
Core and Cavity
- The core forms the internal part of the molded plastic.
- The cavity shapes the external surface.
Runner System
- Hot Runner: Reduces material waste and improves cycle time.
- Cold Runner: More cost-effective but results in plastic waste.
Cooling System
- Ensures uniform cooling and prevents defects like warping.
Ejector System
- Pushes the final part out of the mold.
Factors Affecting Plastic Mold Tooling Design
Mold tooling design must be carefully planned to ensure efficiency, durability, and quality in the final plastic parts. Several factors play a crucial role in determining the design of a mold.
Part Complexity and Geometry
- The more complex the part, the more intricate the mold needs to be.
- Features like undercuts, thin walls, and threads require specialized mold components such as sliders, lifters, or inserts.
Material Shrinkage and Flow Behavior
- Different plastic materials shrink at different rates during cooling.
- Designers must compensate for shrinkage to ensure precise final dimensions.
- Mold flow analysis software helps predict material behavior.
Production Volume and Mold Longevity
- High-volume production requires durable steel molds that can withstand millions of cycles.
- Low-volume production can use aluminum molds, which are cheaper but wear out faster.
By addressing these factors, manufacturers can optimize mold performance and reduce defects.
The Role of CNC Machining and EDM in Mold Tooling
CNC Machining in Mold Tooling
- CNC (Computer Numerical Control) machines cut and shape metal with high precision.
- Used for making cavities, cores, and ejector systems.
- Ensures accurate and repeatable mold production.
Electrical Discharge Machining (EDM)
- EDM uses electrical sparks to cut complex details in hardened steel molds.
- Ideal for intricate features like sharp corners and deep cavities.
- Enhances mold accuracy and reduces manual finishing.
Together, CNC machining and EDM create high-precision molds with smooth finishes.
Benefits of High-Quality Plastic Mold Tooling
Investing in high-quality mold tooling offers several advantages:
Enhanced Production Efficiency
- Reduces cycle times, increasing the number of parts produced per hour.
- Minimizes downtime due to tool wear or defects.
Cost-Effectiveness for Large-Scale Manufacturing
- While the upfront cost is high, durable molds save money over time.
- Fewer mold replacements and maintenance costs improve ROI.
Consistency and High Precision
- Ensures uniformity in every part produced.
- Reduces the need for post-production modifications.
High-quality mold tooling is essential for maintaining efficiency and profitability in plastic manufacturing.
Common Challenges in Plastic Mold Tooling
Despite its advantages, plastic mold tooling comes with challenges that must be managed effectively.
High Initial Tooling Costs
- Steel molds are expensive, but they last longer than cheaper alternatives.
- Prototyping with aluminum molds can reduce initial expenses.
Mold Wear and Maintenance Challenges
- Frequent use causes wear, requiring periodic maintenance.
- Proper lubrication and cleaning extend mold life.
Defects in Molded Parts and Their Solutions
- Warping: Caused by uneven cooling; solved with optimized cooling channels.
- Sink Marks: Result from inadequate pressure; solved by adjusting injection speed.
- Flashing: Occurs when excess plastic leaks out; fixed with proper clamping force.
Addressing these challenges ensures better mold performance and longer tool life.
Innovations in Plastic Mold Tooling
Recent advancements have significantly improved mold tooling technology.
3D Printing for Rapid Mold Prototyping
- Speeds up mold design and testing.
- Reduces costs associated with trial-and-error manufacturing.
AI and Automation in Mold Tooling Design
- AI optimizes mold flow and cycle times.
- Automated quality control detects defects before production issues arise.
Eco-Friendly and Sustainable Tooling Materials
- Recyclable materials and biodegradable plastics are being explored.
- Energy-efficient mold heating and cooling systems reduce waste.
These innovations enhance the efficiency, sustainability, and affordability of plastic mold tooling.
Cost Considerations in Mold Tooling
Factors Affecting Tooling Costs
- Material Choice: Steel molds are costly but durable; aluminum molds are cheaper but wear faster.
- Mold Complexity: The more intricate the mold, the higher the cost.
- Production Volume: Higher volumes justify higher tooling investments.
Cost-Saving Strategies in Mold Tooling
- Using modular mold designs for multiple product variations.
- Implementing proper maintenance to extend tool life.
- Sourcing from cost-effective yet reputable manufacturers.
ROI and Long-Term Benefits of Quality Molds
- High-quality molds reduce rejection rates and rework costs.
- Investing in precision molds ensures long-term profitability.
Choosing the Right Mold Tooling Manufacturer
Selecting the right manufacturer is crucial for obtaining reliable mold tooling.
What to Look for in a Tooling Manufacturer
- Experience in mold making for your specific industry.
- Access to advanced machining technologies.
- Strong quality assurance and certification compliance.
Certifications and Industry Standards
- ISO 9001: Quality management system certification.
- ISO 13485: Required for medical mold manufacturing.
- IATF 16949: Standard for automotive plastic mold tooling.
Case Studies of Successful Mold Tooling Projects
- Automotive companies use high-precision molds for dashboard panels and engine parts.
- Medical device manufacturers rely on sterile, high-accuracy molds for syringes and surgical tools.
Choosing a qualified mold tooling partner ensures product quality and long-term cost savings.
Maintenance and Care of Plastic Mold Tooling
Proper maintenance extends the life of a mold and prevents defects in production.
Routine Cleaning and Lubrication
- Prevents plastic residue buildup and corrosion.
- Lubricates moving parts to reduce wear.
Preventive Maintenance Practices
- Regular inspections catch minor issues before they cause failure.
- Scheduled downtime for maintenance improves mold longevity.
Addressing Wear and Tear Issues
- Ejector pins wear out over time and must be replaced.
- Cooling channels may clog and require periodic flushing.
Routine maintenance reduces costly mold repairs and replacements.
Applications of Plastic Mold Tooling in Different Industries
Plastic mold tooling is essential for producing components across various industries.
Automotive Industry
- Used for making bumpers, dashboards, and interior panels.
- Requires durable and heat-resistant molds.
Medical Device Manufacturing
- Molds for syringes, medical housings, and laboratory equipment.
- Must meet strict hygiene and regulatory standards.
Consumer Electronics and Packaging
- Used for making mobile phone cases, laptop covers, and plastic packaging.
- Ensures lightweight, durable, and aesthetically appealing products.
Plastic mold tooling is a crucial part of modern industrial production.
Future Trends in Plastic Mold Tooling
The mold tooling industry is evolving with new materials and smart technologies.
Advanced Materials and Coatings for Durability
- New alloys and ceramic coatings enhance mold life.
- Self-lubricating materials reduce maintenance needs.
Integration of IoT for Real-Time Mold Monitoring
- Smart sensors track mold performance and predict failures.
- Data-driven maintenance improves mold longevity.
Future Outlook for Plastic Mold Tooling
- Increased automation and AI-driven design optimizations.
- Greater emphasis on eco-friendly materials and processes.
Conclusion
Plastic mold tooling is an essential part of modern manufacturing, enabling the production of high-quality plastic parts with precision and efficiency. While mold tooling involves high initial costs, investing in high-quality materials and advanced designs results in long-term savings and consistent product quality.
With continuous advancements in technology, including AI, 3D printing, and sustainable materials, the future of plastic mold tooling is set to become even more efficient and cost-effective.
FAQs
What is the lifespan of a plastic mold tool?
A well-maintained steel mold can last for millions of cycles.
How long does it take to manufacture plastic mold tooling?
Depending on complexity, it can take 4 to 12 weeks.
Steel for durability, aluminum for rapid prototyping.
How can defects in mold tooling be prevented?
By optimizing design, using proper cooling systems, and maintaining the mold.
What industries rely heavily on plastic mold tooling?
Automotive, medical, electronics, and packaging industries.