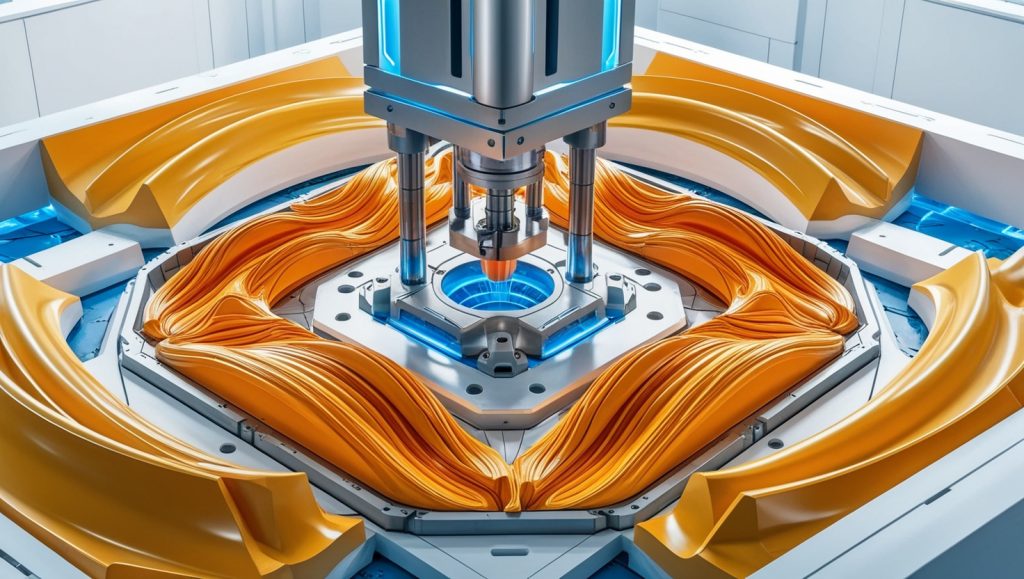
Plastic molding has revolutionized modern manufacturing, enabling the production of intricate and high-precision components. As industries demand more complex designs, molding techniques must evolve to accommodate intricate geometries, thin walls, undercuts, and fine details. With advanced technologies, plastic molding for complex geometries has become more efficient, precise, and cost-effective.
This guide explores the challenges, techniques, and innovations that allow manufacturers to create complex plastic parts with superior accuracy and performance.
Understanding Complex Geometries in Plastic Molding
Complex geometries refer to intricate shapes, fine details, and structural challenges in plastic molding. These designs often include sharp angles, undercuts, thin-walled sections, and multi-functional features.
Key factors that make a design complex include:
- Thin walls that require precise control over material flow.
- Undercuts that need specialized mold mechanisms.
- Multi-cavity molds for high-volume production.
- Tight tolerances that demand precision in mold making.
With the right approach, manufacturers can successfully mold intricate parts without compromising quality or efficiency.
Challenges in Molding Complex Geometries
Producing plastic parts with complex geometries presents several challenges that must be addressed to ensure quality and durability.
Material flow and shrinkage: The way molten plastic flows within the mold can impact the final shape. Improper flow can lead to defects such as short shots, warping, or uneven surfaces. Shrinkage must also be accounted for to maintain accurate dimensions.
Cooling and warping issues: Uneven cooling can cause distortions, resulting in warped or misshaped parts. Optimized cooling systems are essential to ensure uniform cooling and prevent defects.
Undercuts and intricate details: Certain design features, such as undercuts or deep cavities, require specialized mold components like lifters, slides, or collapsible cores to ensure proper part ejection.
Tooling complexity and cost: More complex parts require advanced molds, which can be expensive to design and manufacture. High-precision machining and multi-component mold assemblies add to production costs.
Understanding these challenges helps in developing better solutions for complex plastic molding applications.
Advanced Molding Techniques for Complex Geometries
Modern molding techniques have evolved to address the challenges of complex geometries, ensuring precise and defect-free production.
Multi-shot injection molding: This technique allows the molding of multiple materials or colors within a single cycle. It is widely used for complex parts requiring different material properties in a single component.
Overmolding: A process where a second material is molded over an existing part, creating a single, multi-material product. This method enhances durability and functionality.
Gas-assisted injection molding: By injecting pressurized gas into the molten plastic, this process creates hollow sections within the part. It is ideal for reducing weight while maintaining structural integrity.
Micro-molding: Used for ultra-small components with intricate details, this process ensures precision and accuracy in micro-sized applications such as medical devices and electronics.
3D-printed molds for prototyping: Additive manufacturing has enabled rapid prototyping of complex molds, reducing lead times and allowing for quick design iterations before finalizing metal molds.
Using these advanced techniques allows manufacturers to produce highly detailed and functional parts efficiently.
Material Selection for Complex Plastic Molding
Choosing the right material is critical for successfully molding complex geometries. Certain materials offer better flow properties, impact resistance, and flexibility for intricate designs.
High-flow plastics: Materials like polycarbonate (PC) and acrylonitrile butadiene styrene (ABS) provide excellent flow characteristics, making them suitable for fine details and thin-walled sections.
Thermoplastic elastomers (TPE): Used for overmolding applications, TPE offers flexibility and a rubber-like texture.
Glass-filled plastics: Reinforced plastics like glass-filled nylon enhance strength and dimensional stability but may require specialized molding techniques.
Heat-resistant resins: Materials such as polyether ether ketone (PEEK) and liquid crystal polymer (LCP) are ideal for high-temperature applications and precision molding.
Selecting the right material ensures part durability, functionality, and ease of production.
Innovations in Mold Design for Complex Geometries
Mold design plays a crucial role in the successful production of complex plastic parts. Innovations in tooling have improved accuracy, efficiency, and reliability.
Conformal cooling channels: Traditional molds use straight-line cooling channels, which may not efficiently cool complex parts. Conformal cooling follows the part’s shape, improving temperature control and reducing warping.
Collapsible cores and lifters: These mold components enable the molding of intricate internal features and undercuts without damaging the part during ejection.
Hybrid molds with modular inserts: Modular mold systems allow for quick adjustments and part variations, reducing overall tooling costs.
High-precision machining and polishing: Advanced CNC machining and EDM (Electrical Discharge Machining) techniques ensure high accuracy in mold fabrication.
Innovations in mold design enhance efficiency, reduce cycle times, and improve part quality for intricate designs.
Quality Control and Defect Prevention
Ensuring precision and consistency in complex plastic molding requires strict quality control measures.
Mold flow simulation: Software tools like Moldflow analyze material flow, pressure, and cooling behavior before mold fabrication, reducing defects.
Automated inspection systems: High-speed vision systems detect dimensional inconsistencies, ensuring every part meets specifications.
In-mold sensors: Real-time sensors monitor pressure, temperature, and cycle time, optimizing process parameters for defect-free production.
Proper gate placement: Gates control the entry point of molten plastic. Optimized gate positioning prevents air pockets, weld lines, and stress concentration.
Regular maintenance and mold calibration: Scheduled inspections, cleaning, and lubrication ensure long-term mold performance and precision.
Implementing these quality control measures guarantees high-performance and reliable plastic components.
Applications of Plastic Molding for Complex Geometries
Various industries rely on plastic molding to produce highly complex components with tight tolerances and advanced functionalities.
Automotive industry: Precision-molded parts such as dashboard panels, connectors, and under-the-hood components require durability and intricate designs.
Medical devices: Components for surgical instruments, implants, and diagnostic equipment demand micro-molding and biocompatible materials.
Aerospace and defense: Lightweight, high-strength plastic parts are essential for aircraft interiors, electronic enclosures, and safety components.
Consumer electronics: Smartphones, wearables, and connectors require precise molding for miniaturized components.
Industrial equipment: Custom plastic housings, gears, and machinery parts utilize advanced molding techniques for high-performance applications.
These applications highlight the importance of molding innovations for producing high-quality plastic components across industries.
Future Trends in Plastic Molding for Complex Geometries
Advancements in technology continue to push the boundaries of what’s possible in plastic molding.
Smart molds with real-time monitoring: IoT-enabled molds with embedded sensors track performance metrics, improving process efficiency.
AI-driven mold design optimization: Artificial intelligence enhances design accuracy by predicting defects and optimizing mold flow.
Sustainable and biodegradable plastics: The industry is shifting towards eco-friendly materials and recyclable plastics for greener manufacturing.
Nanotechnology in molding: Nano-coatings and micro-texturing enhance surface properties, improving friction resistance and part performance.
Hybrid manufacturing techniques: Combining injection molding with 3D printing allows for greater design flexibility and cost efficiency.
The future of plastic molding will continue to innovate, enabling even more complex geometries with higher precision and efficiency.
Conclusion
Plastic molding for complex geometries requires a combination of advanced techniques, precision mold design, and high-performance materials. Overcoming challenges such as material flow, cooling efficiency, and intricate detailing is possible with innovations in tooling, automation, and AI-driven optimization.
As industries demand increasingly sophisticated plastic components, manufacturers must stay ahead by adopting cutting-edge molding solutions. With continuous advancements in technology, the future of plastic molding is set to become more precise, sustainable, and cost-effective.