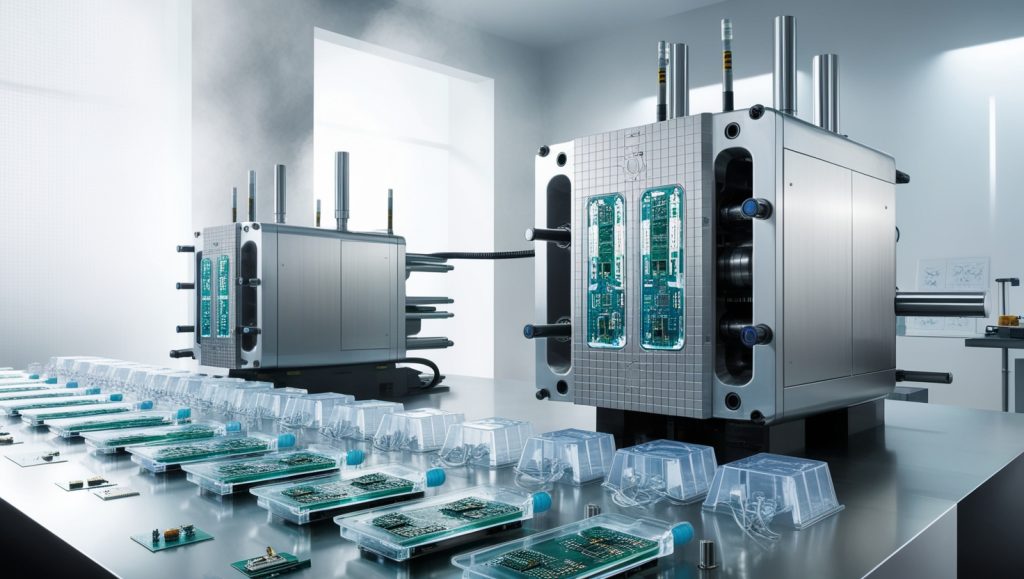
Plastic molding is a crucial part of the electronics industry, providing durable, lightweight, and cost-effective enclosures for various devices. Whether it's a smartphone case, a TV remote, or an industrial control panel, plastic molding plays a role in shaping modern electronics. Unlike metal or glass, plastic offers flexibility, electrical insulation, and a wide range of design possibilities.
Over the years, plastic molding techniques have evolved to meet the growing demand for high-quality, precision-engineered electronic components. With advancements in materials and manufacturing technologies, molded plastic parts now offer improved strength, heat resistance, and customization options.
Types of Plastic Molding Processes
Different plastic molding processes are used based on the complexity, volume, and application of the product. Some of the most common methods include:
Injection Molding
This is the most widely used technique for electronic parts. It involves injecting molten plastic into a mold, which then cools and solidifies into the desired shape. Injection molding is ideal for mass production, offering precision and consistency.
Blow Molding
Blow molding is used for making hollow plastic parts, such as casings for batteries or large electronic housings. The process involves inflating a heated plastic tube inside a mold to form the desired shape.
Compression Molding
In this method, plastic material is placed in a heated mold and compressed into shape. It is often used for making durable electronic components like circuit board insulators and switches.
Thermoforming
This process involves heating a plastic sheet until it becomes pliable, then forming it over a mold. It is commonly used for making packaging and casings for electronic devices.
Materials Used in Plastic Molding for Electronics
The selection of plastic material is crucial to ensure the performance and longevity of electronic components. Common plastics used in electronics molding include:
- Acrylonitrile Butadiene Styrene (ABS): Strong, impact-resistant, and easy to mold. Commonly used in laptop cases and keyboard frames.
- Polycarbonate (PC): Heat-resistant and transparent, making it ideal for LED covers and display panels.
- Polypropylene (PP): Offers excellent chemical resistance and is used in battery housings.
- Polyamide (Nylon): Known for its toughness and durability, used in high-performance electronic parts.
Each material has specific properties such as heat resistance, electrical insulation, and mechanical strength, which are considered during the selection process.
Injection Molding for Electronics
Injection molding is the preferred method for producing precise and high-quality electronic enclosures and components.
Process Overview
- Plastic pellets are melted and injected into a mold.
- The material cools and takes the shape of the mold.
- The finished part is ejected and undergoes quality checks.
Advantages of Injection Molding
- High production efficiency
- Consistent quality
- Capability for complex designs
Blow Molding in Electronics Manufacturing
Blow molding is primarily used for hollow plastic components, such as battery casings and protective housings.
How It Works
- A tube of melted plastic is placed inside a mold.
- Air is blown into the plastic, expanding it into the mold shape.
- The plastic cools and hardens into the final product.
Blow molding is particularly useful for large, lightweight parts that require durability.
Compression Molding for Electronics
Compression molding is commonly used for electrical insulation and high-strength plastic parts.
Benefits of Compression Molding
- Low waste production
- High mechanical strength
- Ideal for thermosetting plastics
It is widely used for making switch housings, electrical connectors, and other durable electronic components.
Thermoforming and Its Role in Electronics
Thermoforming is primarily used for packaging and lightweight electronic covers. It provides cost-effective solutions for producing protective casings and trays for electronic devices.
Key Design Considerations for Plastic Electronic Components
When designing plastic-molded electronic parts, several factors need to be considered:
- Heat Resistance: Prevents deformation due to high temperatures.
- Electrical Insulation: Ensures safety and prevents short circuits.
- Durability: Protects against physical impact and wear.
Plastic Molding vs. Metal Enclosures in Electronics
While metal enclosures offer superior strength, plastic molding provides:
- Lower Cost: More affordable than metal alternatives.
- Lightweight Design: Reduces overall device weight.
- Customization Options: Easier to mold into various shapes and sizes.
Customization and Aesthetics in Plastic Molding
Plastic molding allows for extensive customization, including:
- Various colors and textures
- Logo embossing and branding
- Matte, glossy, or soft-touch finishes
Quality Control in Plastic Molding for Electronics
Ensuring product quality involves:
- Rigorous testing for strength and durability
- Compliance with industry standards
- Consistency checks in mass production
Eco-Friendly and Sustainable Plastic Molding
The electronics industry is moving towards sustainable plastic solutions, such as:
- Biodegradable Plastics: Reducing environmental impact.
- Recycled Materials: Reusing plastic to cut down waste.
Challenges in Plastic Molding for Electronics
Some challenges in plastic molding include:
- Finding materials with high heat resistance
- Preventing defects such as warping and shrinkage
- Ensuring precision in mold design
Trends and Innovations in Plastic Molding Technology
Recent advancements include:
- Smart Materials: Plastics that change properties based on temperature or light exposure.
- 3D Printing Integration: Faster prototyping and customization.
Conclusion and Future of Plastic Molding in Electronics
Plastic molding remains a cornerstone of the electronics industry, offering cost-effective and durable solutions. With innovations in materials and sustainability, the future of plastic molding is geared toward efficiency and environmental consciousness.
Frequently Asked Questions (FAQs)
1. What is the best plastic material for electronic enclosures?
ABS (Acrylonitrile Butadiene Styrene) and Polycarbonate (PC) are among the best materials for electronic enclosures due to their durability, heat resistance, and electrical insulation properties.
2. How does injection molding benefit electronics manufacturing?
Injection molding provides high precision, consistency, and cost-effectiveness, making it ideal for mass-producing electronic components with complex designs.
3. Is plastic molding better than metal for electronic device casings?
Plastic molding is often preferred over metal because it is lightweight, cost-effective, offers better electrical insulation, and allows for more design flexibility. However, metal may be used for high-strength or heat-dissipating applications.
4. Can plastic-molded electronic parts be recycled?
Yes, many thermoplastics used in electronics, such as ABS and Polycarbonate, can be recycled. Sustainable practices are increasingly being adopted in plastic molding to reduce environmental impact.
5. What are the biggest challenges in plastic molding for electronics?
Common challenges include selecting the right material for heat resistance, preventing defects like warping or shrinkage, and ensuring precision in mold design for high-quality production.