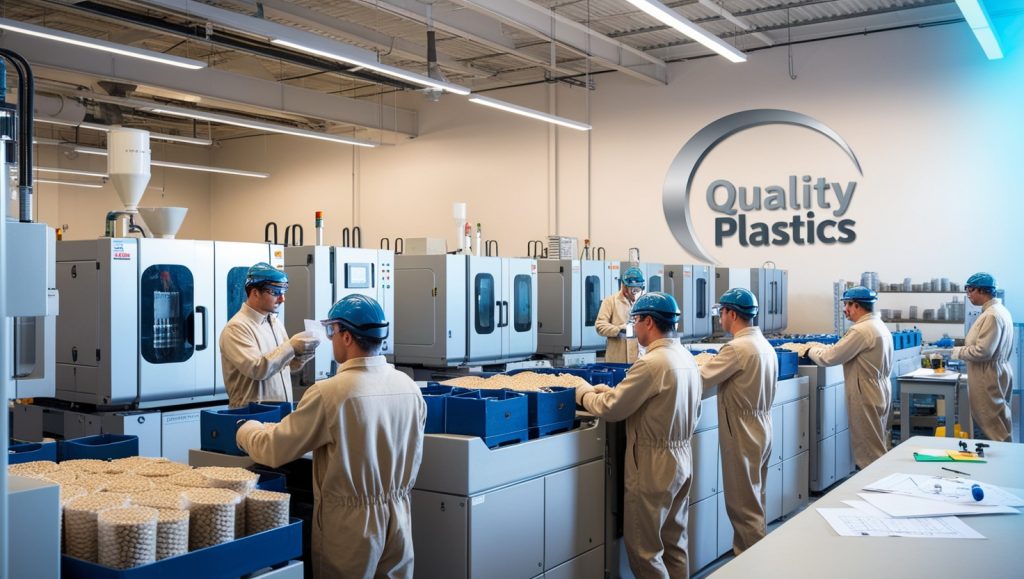
Plastic molding is a crucial process in modern manufacturing, used to create everything from automotive parts to consumer electronics and medical devices. The method involves shaping molten plastic into specific forms using various techniques, each tailored to different applications.
Plastic molding manufacturers play an essential role in producing durable, high-quality plastic components efficiently. With a growing demand for plastic products in nearly every industry, selecting the right manufacturing partner is key to ensuring product success.
Types of Plastic Molding Techniques
Injection Molding
Injection molding is one of the most widely used plastic molding techniques, known for its precision and efficiency.
- Process Overview: The process involves injecting molten plastic into a mold cavity under high pressure. Once the plastic cools and solidifies, the mold opens, and the final product is ejected.
- Advantages and Applications: This method is ideal for mass production, offering consistent quality, low waste, and the ability to produce complex shapes. It is commonly used in the automotive, medical, and electronics industries.
Blow Molding
Blow molding is mainly used to create hollow plastic objects such as bottles and containers.
- Process and Uses: It involves inflating a heated plastic tube inside a mold until it takes the shape of the cavity.
- Common Products Made: Beverage bottles, shampoo containers, and fuel tanks are typical products made using this method.
Compression Molding
This technique is suitable for producing large and durable plastic parts.
- How It Works: A preheated plastic material is placed in a mold, and high pressure is applied to shape it.
- Benefits of Compression Molding: It provides high strength, excellent surface finish, and is cost-effective for medium to high-volume production.
Rotational Molding
This method is popular for making large, hollow parts.
- Manufacturing Process: A mold containing powdered plastic is rotated while being heated, allowing the material to coat the interior surface evenly.
- Industries That Use Rotational Molding: Common in manufacturing storage tanks, playground equipment, and large containers.
Extrusion Molding
Extrusion molding is used to create continuous plastic shapes such as pipes and tubing.
- How It Differs from Other Methods: Instead of a mold cavity, the process pushes molten plastic through a die to create uniform cross-sections.
- Key Benefits and Applications: This technique is highly efficient and widely used in the construction and packaging industries.
Key Factors to Consider When Choosing a Plastic Molding Manufacturer
Selecting the right plastic molding manufacturer requires evaluating several critical factors:
- Material Quality and Selection: Different applications require different plastic materials, from high-strength polymers to biodegradable options.
- Production Capacity and Efficiency: Ensure the manufacturer can handle your required volume within your timeframe.
- Customization and Design Capabilities: If you need custom parts, choose a manufacturer with strong design and prototyping expertise.
- Compliance with Industry Standards: Look for manufacturers that meet ISO, FDA, or other regulatory requirements.
- Cost and Lead Time: Budget and production speed should align with your business needs.
Top Plastic Molding Manufacturers in the Industry
Several global companies dominate the plastic molding sector, offering high-quality services. Some of the top names include:
- Plastikon Industries – Specializes in precision plastic molding for automotive and medical industries.
- EVCO Plastics – Known for custom plastic injection molding.
- Proto Labs – Offers rapid prototyping and low-volume production.
- Rosti Group – A leader in high-volume, complex plastic components.
Each manufacturer has unique strengths, so businesses should compare their services to find the best fit.
Custom vs. Standard Plastic Molding – Which One to Choose?
Choosing between custom and standard plastic molding is a critical decision that depends on your product requirements, budget, and production scale. Both methods offer distinct advantages, but understanding when to opt for custom molding versus standard molding can save time, money, and production effort.
Benefits of Custom Molding
Custom plastic molding provides a tailored solution for businesses needing unique designs or specialized product features. Here’s why it might be the right choice:
- Unique Designs and Complex Geometries
- Custom molding allows for the creation of specific, intricate, and detailed designs that may not be available in pre-existing molds.
- Ideal for products that require tight tolerances and high precision, such as medical devices, aerospace components, or consumer electronics.
- Higher Performance and Product Durability
- Custom molds are designed with the intended use and durability requirements in mind, ensuring stronger, longer-lasting products.
- Can include reinforced materials or multi-material molding for enhanced performance.
- Material and Functionality Flexibility
- Custom molding provides greater control over the choice of plastic materials, allowing businesses to select materials with specific strength, flexibility, or resistance properties.
- Enables the incorporation of additives, coatings, or special finishes that improve aesthetics or functionality.
- Brand Differentiation
- Custom designs allow businesses to create branded and patented products, which can give them a competitive edge in the market.
- Helps maintain a unique look, feel, and function that standard parts may not provide.
- Integration of Additional Features
- Custom plastic molding makes it possible to integrate multiple components into a single part, reducing the need for assembly.
- Useful for creating complex parts with built-in hinges, threads, textures, or multi-color designs.
When to Opt for Standard Molding
Standard plastic molding is a more cost-effective and efficient solution for businesses that do not require unique product features. Here’s when it makes sense to choose standard molding:
- Lower Initial Investment
- Since standard molds are pre-designed and readily available, there is no need to invest in expensive custom tooling.
- Ideal for businesses looking to reduce upfront costs and maintain profitability.
- Faster Production Time
- Standard molds can immediately be put into production, eliminating the lead time required for custom mold design and testing.
- Best suited for businesses that need quick turnaround times.
- Mass Production and Scalability
- Standard molding is often used for high-volume production, where custom designs are unnecessary.
- Commonly used in packaging, household goods, and generic industrial components.
- Suitable for General Applications
- If a pre-existing mold meets your product requirements, it is more practical to use standard molds instead of investing in a custom design.
- Many industries use standardized parts that do not require modification, such as bottle caps, piping components, or storage containers.
- Proven Quality and Reliability
- Standard molds have been tried and tested, ensuring consistent quality and performance.
- Reduces the risk of design flaws, defects, or costly revisions.
Making the Right Choice
- If your product requires specific design features, higher durability, or brand differentiation, custom plastic molding is the best option.
- If you are looking for cost efficiency, quick production, and standard shapes, standard plastic molding is the ideal choice.
Innovations in the Plastic Molding Industry
The plastic molding industry is constantly evolving with new advancements in materials, technology, and sustainability. These innovations are helping manufacturers reduce waste, improve efficiency, and meet increasing demand for high-performance plastic products.
Use of Sustainable and Recyclable Materials
Environmental concerns have led to a major shift towards eco-friendly plastics. Some of the key developments include:
- Biodegradable Plastics
- Many manufacturers are transitioning to bioplastics made from renewable sources like corn starch, sugarcane, and algae.
- These materials break down naturally, reducing environmental impact.
- Recycled and Reprocessed Plastics
- Manufacturers are increasing the use of post-consumer recycled (PCR) plastics in production.
- Helps reduce the reliance on virgin plastics and supports a circular economy.
- Eco-friendly Additives
- Special additives are being developed to enhance the biodegradability of traditional plastics.
- These additives help plastic decompose faster without releasing harmful chemicals.
Advanced Technologies in Plastic Molding
- Automation and AI Integration
- AI-driven machines optimize mold designs, detect defects, and improve production efficiency.
- Robotic automation helps in faster and more precise assembly of molded parts.
- 3D Printing and Rapid Prototyping
- 3D printing technology is now widely used to create custom molds and prototypes.
- Reduces design time and cost, allowing for faster product development.
- Smart Molding with IoT
- Internet of Things (IoT) sensors are being integrated into injection molding machines for real-time monitoring and predictive maintenance.
- Improves overall quality control and reduces material waste.
Challenges Faced by Plastic Molding Manufacturers
Despite advancements, plastic molding manufacturers face several challenges:
Environmental Concerns and Sustainability Issues
- Increasing regulations on single-use plastics are pressuring manufacturers to find sustainable alternatives.
- The need for biodegradable and recyclable materials is growing, but finding cost-effective solutions remains a challenge.
Competition and Market Demand
- As more companies enter the industry, competition is increasing, leading to price pressure and the need for continuous innovation.
- Customers are demanding higher-quality products with shorter lead times, pushing manufacturers to adopt faster, more efficient production methods.
Future Trends in Plastic Molding Manufacturing
The plastic molding industry is expected to undergo major transformations in the coming years. Some of the key trends include:
Smart Manufacturing and Automation
- AI and machine learning will play a bigger role in process optimization and defect detection.
- Automated production lines will improve efficiency, reducing labor costs.
Eco-friendly and Biodegradable Plastics
- The use of plant-based and compostable plastics will increase to meet environmental regulations.
- New technologies will allow plastic products to break down faster without harming the environment.
Conclusion
Plastic molding manufacturers are a crucial part of modern industry, supplying components to automotive, medical, electronics, and packaging sectors. Whether you choose custom or standard molding depends on your specific needs, budget, and production volume.
Innovations in sustainability, automation, and smart manufacturing are shaping the industry, while challenges like environmental concerns and competition continue to push manufacturers toward more efficient and eco-friendly solutions.
By staying informed about industry trends and selecting the right molding partner, businesses can optimize production, reduce costs, and enhance product quality.
FAQs
What industries rely the most on plastic molding?
Plastic molding is widely used in automotive, medical, electronics, construction, and packaging industries.
How do I find a reliable plastic molding manufacturer?
Look for experience, certifications (ISO, FDA, etc.), customer reviews, and technological capabilities before selecting a manufacturer.
What is the most cost-effective plastic molding technique?
Injection molding is the most cost-effective for high-volume production, while extrusion molding is best for continuous shapes like pipes.
How is sustainability being integrated into plastic molding?
Manufacturers are using recycled plastics, bioplastics, and energy-efficient processes to reduce environmental impact.
Can small businesses afford custom plastic molding?
Yes! 3D printing, rapid prototyping, and low-cost custom molds make custom plastic molding accessible for small businesses.