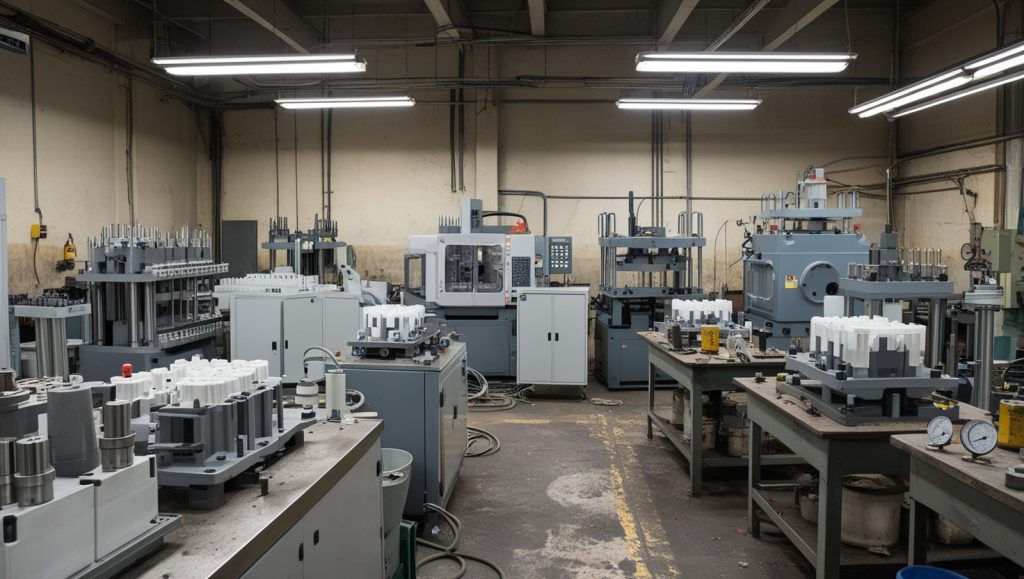
Batch production is a manufacturing method where a set number of identical products are produced in a series of controlled stages. Plastic tooling plays a vital role in batch production by ensuring precision, cost-effectiveness, and efficiency while maintaining high-quality standards.
Unlike mass production, batch production allows flexibility in design changes, reduced tooling costs, and optimized production cycles, making it ideal for industries such as automotive, medical devices, consumer electronics, and packaging.
This guide explores the various aspects of plastic tooling for batch production, including types of tooling, materials used, design considerations, manufacturing steps, and the challenges and advantages of this approach.
Role of Plastic Tooling in Batch Production
Plastic tooling enables manufacturers to produce consistent, high-quality parts with minimal waste while offering the ability to switch between different product batches with ease. Key advantages include:
- Cost-Effectiveness – Reduces per-unit cost by spreading tooling expenses over multiple batches.
- Flexibility – Enables manufacturers to quickly adjust designs, materials, or production processes.
- Quality Consistency – Ensures uniformity in dimensions, finish, and performance across multiple batches.
- Efficient Production Cycles – Optimizes material usage and reduces downtime between batches.
Batch production using plastic tooling is often used for limited edition products, prototype testing, seasonal production, and customized components.
Types of Plastic Tooling for Batch Production
Different tooling techniques are used depending on production volume, part complexity, and material requirements.
Soft Tooling (Prototype & Low-Volume Production)
Soft tooling is typically used for small batch production runs and rapid prototyping. It involves molds made from materials like silicone, aluminum, or low-grade steel, offering:
- Lower cost compared to hard tooling
- Faster turnaround times
- Good for testing and pre-production validation
Hard Tooling (Medium to High-Volume Batch Production)
For longer production runs, hard tooling uses high-quality steel molds that provide:
- Higher durability and repeatability
- Precision for tight tolerances
- Better resistance to wear and tear
Modular and Hybrid Tooling
Some manufacturers use modular mold designs, allowing interchangeable inserts to modify specific part features without creating an entirely new mold. Hybrid tooling, which combines 3D-printed inserts with traditional molds, is also gaining popularity for small-batch production.
Materials Used in Plastic Tooling for Batch Production
The choice of plastic depends on mechanical properties, durability, and environmental exposure. Common materials include:
Material | Properties | Common Applications |
---|---|---|
ABS (Acrylonitrile Butadiene Styrene) | Impact-resistant, easy to mold | Consumer electronics, automotive interiors |
Polypropylene (PP) | Lightweight, chemical-resistant | Packaging, medical devices, automotive parts |
Polycarbonate (PC) | Transparent, UV-resistant, durable | Lighting components, protective gear |
Nylon (PA6, PA66) | High strength, heat-resistant | Mechanical parts, under-the-hood automotive parts |
PEEK (Polyether Ether Ketone) | High-temperature and chemical resistance | Aerospace, medical implants |
Each plastic type is carefully selected based on batch size, part function, and performance requirements.
Design Considerations for Batch Production Plastic Tooling
Proper tooling design ensures efficiency, cost savings, and defect minimization in batch production.
Mold Flow Analysis & Shrinkage Compensation
- Simulation software predicts how molten plastic flows within the mold, ensuring even distribution and minimal defects.
- Shrinkage compensation is essential, as plastics contract when cooled. Designing for predictable shrink rates prevents dimensional inaccuracies.
Tooling Lifespan and Maintenance
- Soft tooling (silicone or aluminum) may wear out faster and require frequent replacements.
- Hard tooling (steel) lasts longer but requires regular maintenance to prevent degradation.
Cooling System Optimization
- Efficient cooling reduces cycle times and production costs.
- Using conformal cooling channels (3D-printed cooling paths) enhances temperature control and part quality.
Part Ejection and Draft Angles
- Proper draft angles (typically 1-3 degrees) ensure smooth part ejection and prevent mold damage.
- Ejector pins and air release systems reduce defects like warping and sink marks.
Steps in Plastic Tooling Fabrication for Batch Production
1. CAD Modeling and Prototyping
- Engineers create 3D CAD designs of the mold and simulate material flow and cooling behavior.
- 3D-printed prototypes allow rapid testing before full-scale tooling production.
2. Tooling Fabrication (Soft or Hard Molds)
- CNC machining and EDM (Electrical Discharge Machining) create high-precision tooling cavities.
- Aluminum molds (for short runs) or steel molds (for high-volume batches) are prepared.
3. Injection Molding or Thermoforming
- Injection molding injects molten plastic into a pre-made mold to form high-precision parts.
- Thermoforming is used for larger plastic sheets shaped using heat and vacuum pressure.
4. Surface Finishing and Texturing
- Polishing, chemical etching, and coatings improve part aesthetics and durability.
- Laser engraving or embossing adds branding elements if needed.
5. Quality Control and Testing
- Dimensional accuracy checks ensure consistency across the batch.
- Tensile, impact, and heat resistance testing validate part durability.
- Defect inspections (such as warping, shrinkage, or flash marks) ensure compliance with industry standards.
Challenges in Plastic Tooling for Batch Production
Despite its benefits, batch production faces several challenges:
Tooling Costs vs. Production Volume
- High tooling costs for low-volume production may not always be cost-effective.
- Manufacturers must balance mold cost against projected batch size to ensure profitability.
Material Selection and Availability
- Some high-performance plastics require specialized processing and may not be readily available.
- Certain materials need additives or reinforcements to meet specific application requirements.
Cycle Time and Efficiency
- Cooling time directly impacts cycle times, affecting overall production efficiency.
- Advanced cooling techniques, such as conformal cooling, help reduce cycle times.
Defect Management
- Short-run tooling can wear out faster, leading to increased defect rates.
- Warping, flashing, and shrinkage must be carefully controlled through mold design adjustments.
Advantages of Batch Production Plastic Tooling
Batch production bridges the gap between prototyping and mass manufacturing, offering unique benefits:
- Scalability – Can increase or decrease production volume based on demand.
- Design Flexibility – Easy to modify or update designs between batches.
- Cost Optimization – Reduces upfront investment compared to mass production.
- Faster Market Entry – Enables businesses to quickly test new products before full-scale production.
This makes batch production an ideal choice for startups, limited-edition product lines, medical devices, and seasonal goods.
Future Trends in Plastic Tooling for Batch Production
- 3D-Printed Tooling – Hybrid molds combining additive manufacturing with traditional techniques reduce costs for small-batch runs.
- Sustainable Materials – Increased use of biodegradable and recycled plastics for environmentally conscious production.
- AI-Powered Process Optimization – AI-driven mold simulations and real-time monitoring enhance efficiency and defect detection.
- Smart Molds with IoT Sensors – Sensors embedded in molds provide real-time data on temperature, pressure, and wear conditions.
Conclusion
Plastic tooling for batch production offers cost-effective, high-quality, and flexible manufacturing solutions across multiple industries. Whether using soft tooling for prototypes or hard tooling for medium-scale production, the right approach depends on volume, material selection, and production goals.
With advances in 3D printing, AI, and smart manufacturing, batch production will continue to evolve, enabling businesses to produce innovative plastic components efficiently and sustainably.
FAQs on Plastic Tooling for Batch Production
1. What is the main advantage of plastic tooling for batch production?
Plastic tooling for batch production offers cost-effective and flexible manufacturing, allowing businesses to produce limited quantities without the high investment of mass production tooling. It enables design modifications, quick market entry, and efficient material use, making it ideal for startups, prototypes, and seasonal products.
2. How does batch production differ from mass production in plastic tooling?
Batch production focuses on producing a set quantity of parts in controlled stages, allowing for design adjustments and lower upfront costs. In contrast, mass production is high-volume manufacturing optimized for cost efficiency and minimal variation, often requiring expensive hard tooling with long lifespans.
3. What type of plastic tooling is best for small-batch production?
For small-batch production, soft tooling (e.g., silicone, aluminum, or 3D-printed molds) is preferred due to lower costs, faster production, and easier modifications. Hybrid tooling, combining traditional molds with 3D-printed inserts, is also gaining popularity for short-run production and prototyping.
4. How can I reduce defects in plastic tooling for batch production?
To minimize defects like warping, shrinkage, and flashing, consider:
- Mold flow analysis to optimize material distribution.
- Proper cooling system design to prevent uneven shrinkage.
- Draft angles and ejection mechanisms to facilitate smooth part removal.
- Regular mold maintenance to ensure consistent quality over multiple batches.
5. What are the best plastic materials for batch production?
The best materials depend on application requirements:
- ABS – Impact-resistant, ideal for consumer products and electronics.
- Polypropylene (PP) – Lightweight, chemical-resistant, used in packaging and medical devices.
- Nylon (PA6, PA66) – Heat and wear-resistant, used in automotive and mechanical parts.
- Polycarbonate (PC) – High strength and UV-resistant, suitable for lighting and transparent parts.
- PEEK – High-performance plastic for aerospace and medical applications.
6. What future trends are shaping plastic tooling for batch production?
Emerging trends include:
- 3D-printed tooling for rapid prototyping and small production runs.
- AI-driven mold optimization to reduce defects and improve efficiency.
- Smart molds with IoT sensors for real-time production monitoring.
- Sustainable materials like biodegradable plastics and recycled resins for eco-friendly production.