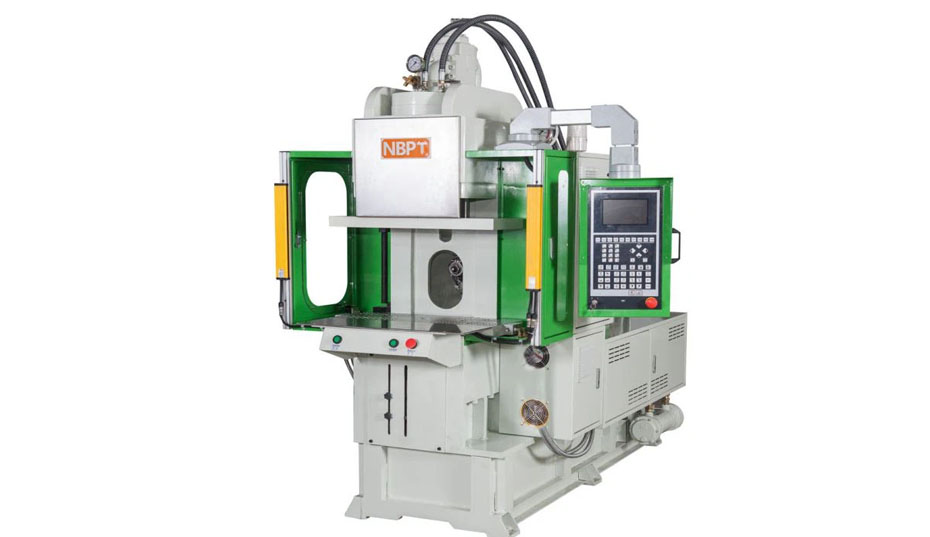
An advanced injection molding machine is a machine that is capable of producing high-quality, complex parts with precise dimensions. These machines typically have advanced features such as multiple stages of injection, specialized nozzles, and precision temperature control. They can also be programmed for automation and can be integrated with robotics and other advanced technologies. These machines are typically used in the manufacturing of products such as automotive parts, medical devices, and electronics.
The modern manufacturing industry is constantly evolving and developing new and innovative ways to create products. One of the most significant advancements in recent times has been the emergence of advanced injection moulding machines.
These machines are highly advanced and can be used to create a variety of products with a high level of precision and accuracy. In this blog, we will take a closer look at these advanced injection moulding machines, their features, and what makes them so beneficial for modern manufacturing.
Introduction to Advanced Injection Moulding Machines
Advanced injection moulding machines are the latest evolution in injection moulding technology. They are designed to handle a range of materials and sizes, and are capable of producing highly precise and accurate parts.
These machines are highly efficient and require minimal manual intervention, making them ideal for large-scale manufacturing operations. They are also capable of producing parts with tight tolerances, making them perfect for producing highly complex components.
Advantages of Using Advanced Injection Moulding Machines
Advanced injection moulding machines offer a number of advantages over traditional injection moulding machines. These include:
- High level of precision and accuracy: Advanced injection moulding machines are capable of producing parts with very high levels of precision and accuracy. This makes them ideal for producing highly complex components.
- Faster production: Advanced injection moulding machines are capable of producing parts much faster than traditional injection moulding machines. This means they are perfect for large-scale manufacturing operations.
- Low production costs: The high efficiency of advanced injection moulding machines means they require less manual intervention, resulting in lower production costs.
- Versatility: Advanced injection moulding machines are capable of handling a wide range of materials and sizes, making them ideal for a variety of applications.
Types of Advanced Injection Moulding Machines
There are a number of different types of advanced injection moulding machines available on the market. The most common include:
- Multi-component injection moulding machines: These machines are capable of producing parts with multiple components in one process. This is ideal for producing complex components such as medical devices.
- Micro-injection moulding machines: These machines are designed to handle very small parts and are perfect for producing highly precise components.
- Automated injection moulding machines: These machines are capable of producing parts without any manual intervention, making them ideal for large-scale manufacturing operations.
Basic Components of an Advanced Injection Moulding Machine
An advanced injection moulding machine typically consists of a few basic components. These include:
- The injection unit: This is the part of the machine responsible for melting the plastic material and injecting it into the mould.
- The mould: This is the part of the machine where the molten plastic is injected and cooled to form the desired part.
- The clamping unit: This is the part of the machine that holds the mould in place during the injection process.
- The control unit: This is the part of the machine responsible for controlling all the other components and ensuring they work together to produce the desired part.
The Working of an Advanced Injection Moulding Machine
The working of an advanced injection moulding machine is relatively simple. The process begins with the injection unit melting the plastic material and injecting it into the mould. The mould is then held in place by the clamping unit while it cools and takes the shape of the desired part. Once the part is cooled, it is ejected from the mould and the process can begin again.
Injection Moulding Process Overview
Injection moulding is a highly precise process that involves a few key steps. These steps are:
- Material selection: The first step is to select the material to be used for the part. This will depend on the application and the desired properties of the final part.
- Design: The second step is to design the mould for the part. This will involve designing the cavity, runners, and gates for the part.
- Machining: The third step is to machine the mould to the desired shape and size. This will involve using a variety of tools and machines to achieve the desired finish.
- Injection: The fourth step is to inject the molten plastic into the mould. This is done using the injection unit of the injection moulding machine.
- Cooling: The fifth step is to cool the part in the mould. This is done using cooling channels in the mould and can take a few minutes.
- Ejection: The sixth step is to eject the part from the mould. This is done using the ejector pins of the injection moulding machine.
Benefits of Advanced Injection Moulding Machines
Advanced injection moulding machines offer a number of benefits to manufacturers. These include:
- High levels of precision and accuracy: Advanced injection moulding machines are capable of producing parts with very high levels of precision and accuracy. This makes them perfect for producing highly complex components.
- Faster production: Advanced injection moulding machines are capable of producing parts much faster than traditional injection moulding machines. This makes them ideal for large-scale manufacturing operations.
- Low production costs: The high efficiency of advanced injection moulding machines means they require less manual intervention, resulting in lower production costs.
- Versatility: Advanced injection moulding machines are capable of handling a wide range of materials and sizes, making them ideal for a variety of applications.
Market Trends and Statistics for Advanced Injection Moulding Machines
The global advanced injection moulding machines market is expected to grow at a compound annual growth rate (CAGR) of around 6% from 2021 to 2026. This growth will be driven by the increasing demand for high-precision components in various industries, such as automotive, medical, and consumer goods.
In addition, the increasing demand for energy-efficient injection moulding machines is also expected to drive the market growth. The increasing use of recycled materials in injection moulding is also expected to drive the market growth.
Challenges Faced with Advanced Injection Moulding Machines
Despite the numerous benefits of advanced injection moulding machines, there are also a few challenges that need to be addressed. These include:
- High initial cost: Advanced injection moulding machines are typically more expensive than traditional injection moulding machines. This can be a challenge for smaller companies with limited budgets.
- Lack of skilled operators: Advanced injection moulding machines require skilled operators to ensure they are used correctly and to their full potential. This can be a challenge in markets where there is a lack of skilled operators.
- Maintenance: Advanced injection moulding machines require regular maintenance to ensure they are operating at their peak performance. This can be a challenge for companies with limited resources.
Conclusion
Advanced injection moulding machines are highly advanced and capable of producing highly precise and accurate parts. These machines offer a number of benefits, such as higher levels of precision and accuracy, faster production, lower production costs, and versatility.
Despite the numerous benefits, there are also a few challenges that need to be addressed, such as the high initial cost, lack of skilled operators, and maintenance requirements.
Nevertheless, the increasing demand for high-precision components in various industries is expected to drive the market growth for advanced injection moulding machines. So if you are looking for a cutting-edge solution for your manufacturing needs, then advanced injection moulding machines could be the perfect choice for you.