What does "die casting" mean?
- The mould, also known as a die, normally consists of two pieces installed in a die-casting machine. It is often constructed of steel. The molten metal is poured into the mould cavity using a plunger that the machine activates. Die casting is a manufacturing method used to make vast quantities of metal parts with great accuracy and consistency. Under intense pressure, molten metal is forced into a mould cavity, forming the required shape.
- The two parts of the mould are split when the metal has hardened, and the final object is discharged. It is frequently used to manufacture intricately shaped pieces that would be challenging or expensive to manufacture using other manufacturing processes. Engine parts for automobiles, electrical housings, and appliance parts are some products frequently created utilizing die castings.
- Compared to other manufacturing processes, die casting has many benefits, such as high production rates, exceptional dimensional precision and reproducibility, and the capacity to create components with thin walls and precise features. It is better suited for large-scale production runs since the tooling setup costs might be high.
Where Is Die Casting Most Effective?
Here are a few instances:
- It is used in vehicle components.
- Appliances for the home and consumer electronics.
- Electronic device housings.
- Commercial item.
- Communication tools and Tools for farming.
- Mechanical industry.
The Positive Effects of Using Die Casting:
Die casting is a manufacturing method that uses metal moulds (also known as dies) to accurately and consistently construct complicated metal parts forms. The casting has certain benefits, such as:
- High dimensional precision and consistency:
It creates components with high accuracy and consistency, making it the perfect choice for applications requiring exact requirements.
- High production rates:
The casting is a highly automated technique that can swiftly and effectively create huge quantities of components.
- Versatility:
From basic to complicated geometries, die casting may be utilized to make parts in various sizes and forms.
- Cost-effective:
Casting is a highly affordable approach for creating high-quality parts in big quantities compared to other production techniques.
- Superior surface quality:
The casting results in parts with a flawless surface finish, obviating the need for extra finishing processes.
- Strength and durability:
Die-cast components are renowned for their strength and durability, making them perfect for uses that call for strong mechanical qualities.
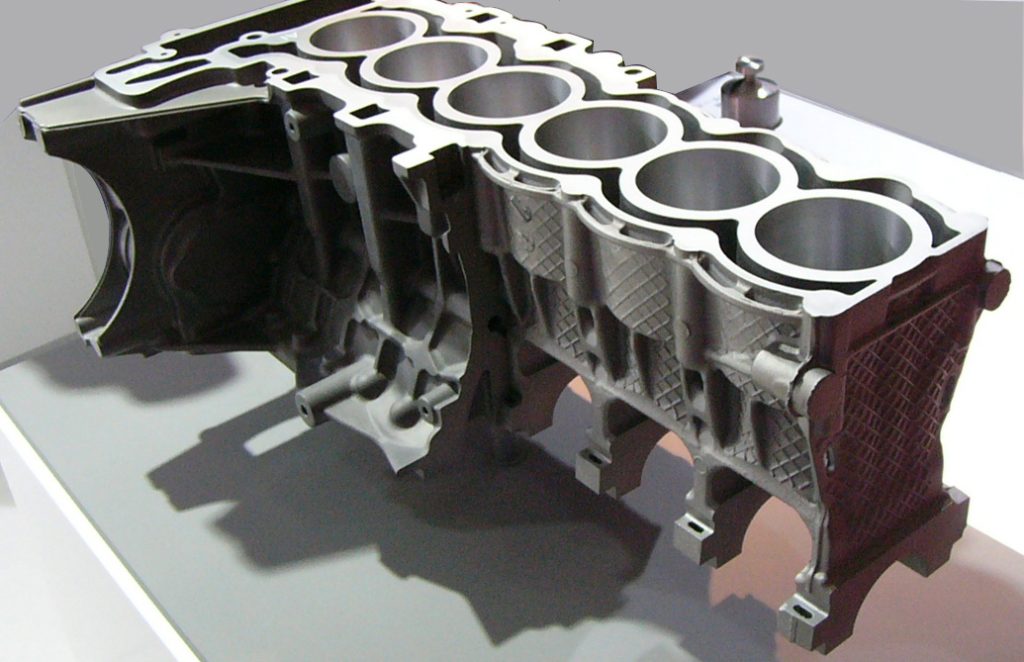
- Reduced waste:
It produces less waste than other manufacturing techniques because scrap metal is readily recyclable and reusable.
The Die Casting Procedure:
- Die casting is a technique that requires applying intense pressure to the injection of molten metal into a mould cavity. The mould cavity is often constructed of steel or aluminium and is intended to make the product in the specified form and size. Molten metal is poured into the mould, which is subsequently cooled, causing the metal to assume the mould shape.
- The preparation of the mould is the first step in the die-casting process. A wax or plastic material is first poured into the mould to mould the product into the required shape. Once injected, the wax or plastic substance is heated in the mould, causing it to melt and take the desired shape. Then, molten metal is pumped into the mould to replace the wax or plastic substance. After being poured into the mould, the molten metal is cooled and given time to set. The final item is removed from the mould once it has been opened. It is a very precise process that can create components with fine features and high precision. The final item is removed from the mould once it has been opened.
The Things to Think About When Choosing Die Casting:
By pressing molten metal into a mould hole, die casting is a manufacturing method that produces metal pieces. There are several things to take into consideration while choosing to cast. The following are a few of the most crucial elements:
- Material selection:
In casting, the choice of materials is crucial. Aluminum, and zinc casting materials. The application's individual needs, such as strength, weight, and corrosion resistance, should be considered while selecting the material.
- Part design:
The part's design is another important consideration. Considering elements like wall thickness, draught angles, and the position of gate and ejector pins, the component design should be optimized for die casting.
- Tooling:
The design and quality of the die-casting tooling greatly influence the ultimate quality of the pieces produced. The tooling should be created to reduce flaws and guarantee reliable output.
- Production volume:
Another crucial aspect to consider when choosing die casting is the anticipated production volume. To achieve the most economical manufacturing of the specified volume of components, consideration should be given to the die-casting method, material, and tooling choices.
The Price of Aluminum Die Casting Moulds:
Depending on the mould type you want and the complexity of the component you are making, the price of aluminium die-casting moulds might change. The component size and the kind of production procedure you're utilizing affect how much the moulds cost. The price of the moulds might also change based on the kind of metal you use and the temperature range you need to work with. The kind of manufacturing technique you are utilizing and your budget should also be considered. After considering every one of these variables, you ought to be able to choose the ideal aluminium die-casting mould for your needs and calculate the mould price.
Conclusion:
Die casting is a technique frequently used in industry to create intricate, high-quality metal pieces with precise dimensions. High pressure feeds molten metal into a steel die, causing it to solidify and take the required shape. For more than ten years, our firm has specialized in die castings. ACE can develop and manufacture moulds, carry out die casting, carry out CNC processing, polish, electroplate, carry out oil injection, and cover zinc alloy, aluminium alloy, and magnesium alloy. In addition to sophisticated detecting equipment, our plant is equipped with cutting-edge die castings and mould-making machinery.