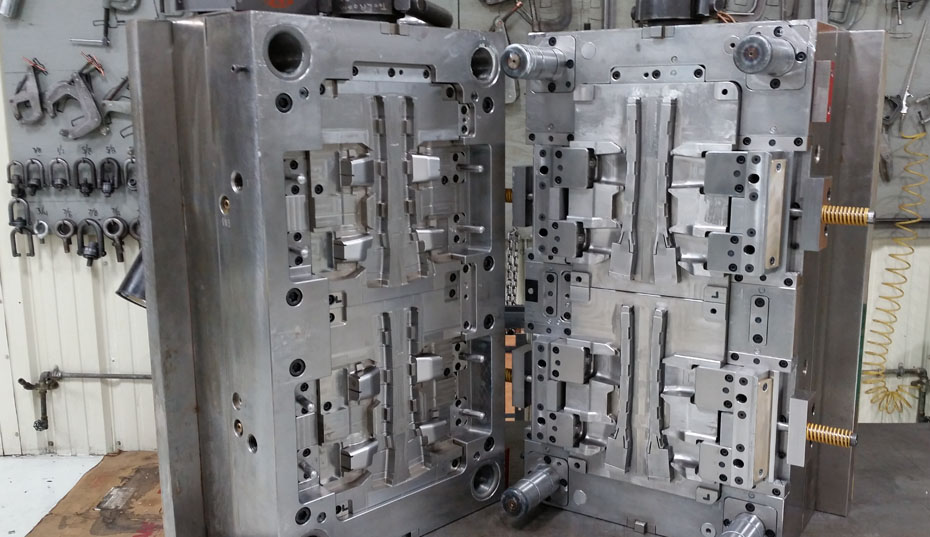
Custom plastic injection molding is a manufacturing process used to produce a wide range of plastic parts and components in large volumes. The process involves melting plastic pellets or granules and injecting them into a mold cavity under high pressure. The molten plastic then cools and solidifies inside the mold, taking on its shape and form.
Custom plastic injection molding is used to produce parts and components for a variety of industries, including automotive, medical, consumer goods, electronics, and more. The process allows for the production of complex and precise parts with high repeatability and consistency.
To begin the custom plastic injection molding process, the manufacturer creates a mold or tooling based on the desired part design. This mold is typically made of metal and is designed to withstand the high pressure and temperatures of the injection molding process.
Once the mold is complete, plastic pellets or granules are fed into the injection molding machine's hopper. The machine then heats the plastic to its melting point and injects it into the mold cavity under high pressure.
The plastic then cools and solidifies inside the mold, taking on its final shape and form. The mold is then opened, and the finished part is ejected from the mold. The process is repeated to produce multiple parts in a single production run.
Custom plastic injection molding offers several advantages over other manufacturing processes, including high production rates, cost-effectiveness, and the ability to produce complex geometries and precise parts with high consistency and repeatability.
Custom plastic injection molding is a manufacturing process that involves the use of plastic resin to produce parts and components for a variety of industries, from automotive to consumer electronics. Injection molding is one of the most common and cost-effective methods for producing plastic parts, and has become a popular choice for businesses looking to increase their production efficiency. In this article, we’ll explore the benefits of custom plastic injection molding and how it can help your business.
What is custom plastic injection molding?
Custom plastic injection molding is a process where molten plastic is injected into a mold at high pressure to create a part or component. The process is highly efficient and cost-effective, as the same mold can be used multiple times to produce the same part or component in a fraction of the time it would take to produce it with other methods. The injection molding process can also be customized to meet the exact specifications of the customer, ensuring that the parts or components are of the highest quality.
Benefits of custom plastic injection molding
There are many benefits to using custom plastic injection molding for your business. The process is highly efficient and cost-effective, as the same mold can be used multiple times to produce the same part or component in a fraction of the time it would take to produce it with other methods. Additionally, the process is highly accurate and repeatable, ensuring that each part or component is of consistently high quality. The injection molding process also allows for a wide variety of shapes, sizes, and designs, allowing for a greater degree of flexibility in the production process.
In addition to its efficiency and accuracy, custom plastic injection molding has a number of other benefits. The process is highly automated, allowing for a greater degree of consistency in the production process. It also offers a high degree of repeatability, ensuring that each part or component is identical to the last. Additionally, the injection molding process can be customized to meet the exact specifications of the customer, ensuring that the parts or components are of the highest quality.
Types of custom plastic injection molding
There are several different types of custom plastic injection molding processes, including thermoplastic injection molding and thermoset injection molding. Thermoplastic injection molding is a process where molten thermoplastic resin is injected into a mold at high pressure to create a part or component. Thermoset injection molding is a process where a thermoset resin is injected into a mold at high pressure to create a part or component. Both processes offer a high degree of accuracy and repeatability, ensuring that each part or component is of consistently high quality.
Advantages of using custom plastic injection molding
Custom plastic injection molding offers a number of advantages for your business. The process is highly efficient and cost-effective, as the same mold can be used multiple times to produce the same part or component in a fraction of the time it would take to produce it with other methods. Additionally, the process is highly accurate and repeatable, ensuring that each part or component is of consistently high quality. The injection molding process also allows for a wide variety of shapes, sizes, and designs, allowing for a greater degree of flexibility in the production process.
In addition to its efficiency and accuracy, custom plastic injection molding offers a number of other advantages. The process is highly automated, allowing for a greater degree of consistency in the production process. It also offers a high degree of repeatability, ensuring that each part or component is identical to the last. Additionally, the injection molding process can be customized to meet the exact specifications of the customer, ensuring that the parts or components are of the highest quality.
Applications of custom plastic injection molding
Custom plastic injection molding can be used in a wide variety of industries and applications. The process is highly versatile and can be used to produce parts and components for automotive, medical, consumer electronics, and other industries. The injection molding process can also be used to create a wide variety of shapes, sizes, and designs, making it a popular choice for creating parts and components for a variety of products.
Choosing the right partner for custom plastic injection molding
When it comes to choosing the right partner for custom plastic injection molding, it’s important to consider a few things. First, you should look for a partner with experience in the industry, as this will ensure that the parts or components you receive are of the highest quality. Additionally, you should look for a partner with a wide variety of services and capabilities, as this will ensure that you receive the exact parts or components you need. Finally, you should look for a partner with a proven track record of success, as this will ensure that your project is successful.
Design considerations for custom plastic injection molding
When designing parts and components for custom plastic injection molding, there are a few key considerations to keep in mind. First, it’s important to consider the type of plastic that will be used, as this will determine the strength and durability of the part or component. Additionally, it’s important to consider the shape and size of the part or component, as this will determine the injection molding process that will be used. Finally, it’s important to consider the production process, as this will determine the cost and efficiency of the project.
Cost considerations for custom plastic injection molding
The cost of custom plastic injection molding can vary depending on a number of factors, including the type of plastic used, the shape and size of the part or component, and the production process. Additionally, the cost can vary depending on the number of parts or components that need to be produced, as well as the complexity of the design. It’s important to consider all of these factors when calculating the cost of a custom plastic injection molding project.
Case studies of successful custom plastic injection molding projects
There are many case studies of successful custom plastic injection molding projects. For example, a medical device manufacturer used custom plastic injection molding to reduce the production time of its parts and components by 70%. Additionally, a consumer electronics company used the process to reduce the cost of its parts and components by 50%. These case studies demonstrate the potential of custom plastic injection molding in creating high-quality parts and components at an efficient and cost-effective rate.
Conclusion
Custom plastic injection molding is a highly efficient and cost-effective process for producing parts and components for a variety of industries. The process is highly automated, allowing for a greater degree of consistency in the production process. It also offers a high degree of repeatability, ensuring that each part or component is identical to the last. Additionally, the injection molding process can be customized to meet the exact specifications of the customer, ensuring that the parts or components are of the highest quality. With its many benefits, custom plastic injection molding is a great choice for businesses looking to increase their production efficiency.