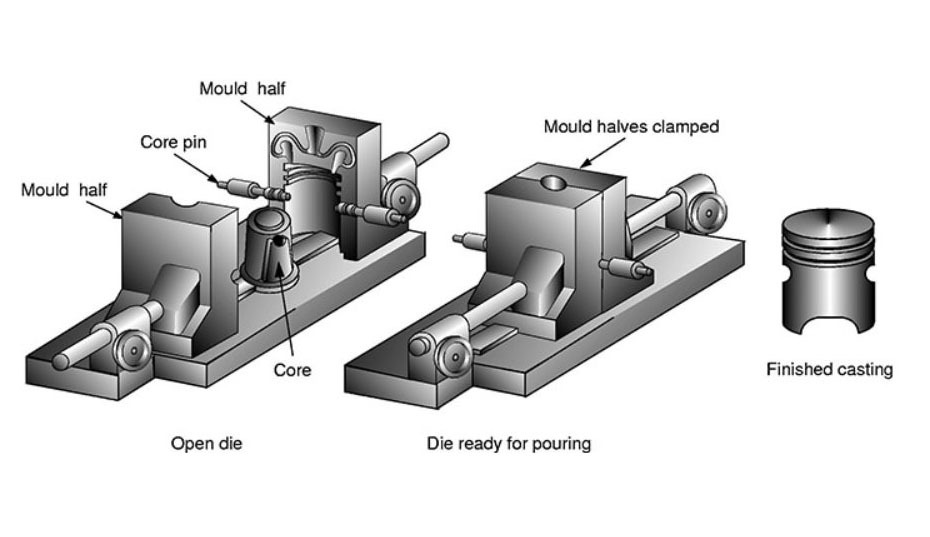
Die casting and permanent mold casting are two common methods used in the manufacturing industry for producing metal parts. While both methods involve pouring molten metal into a mold to create a desired shape, there are some differences between them.
Die casting is a process that involves injecting molten metal under high pressure into a steel mold or die. The die is made up of two halves, and the molten metal is injected into the die through a gate or sprue. The high pressure ensures that the molten metal fills every corner of the mold, producing parts with tight tolerances and excellent surface finishes. Die casting is ideal for producing large quantities of small to medium-sized parts, typically made of non-ferrous metals such as zinc, aluminum, and magnesium.
Permanent mold casting, on the other hand, is a process that involves pouring molten metal into a reusable mold made of steel or cast iron. The mold is designed with a cavity that has the desired shape of the final part. The molten metal is poured into the mold, which is then cooled to solidify the metal. Once the metal has solidified, the mold is opened, and the part is removed. Permanent mold casting is best suited for producing larger parts, typically made of alloys with higher melting points, such as brass, bronze, and iron.
In summary, die casting is best suited for producing small to medium-sized parts with high precision and excellent surface finishes, while permanent mold casting is ideal for larger parts made of alloys with higher melting points.
Die casting and permanent mold casting are two of the most common casting processes used in the manufacturing industry. Both techniques are used to produce high-quality metal parts for various industries. In this article, we will explore the differences between these two casting techniques in detail.
Die Casting:
Die casting is a casting process that involves injecting molten metal into a die (also known as a mold or tool). The die is a steel or ceramic mold that is designed to produce a specific part or component. The molten metal is injected into the die under high pressure, which forces the metal to take the shape of the mold. Once the metal has solidified, the die is opened, and the part is ejected.
The die casting process is used to produce complex shapes with high accuracy and repeatability. It is commonly used to produce parts for the automotive, aerospace, and electronics industries. Die casting is also used to produce small parts, such as fasteners and connectors, as well as large parts, such as engine blocks and transmission housings.
Advantages of Die Casting:
- High accuracy and repeatability: Die casting produces parts with high accuracy and repeatability, making it an ideal process for producing parts that require tight tolerances.
- Complex shapes: Die casting can produce parts with complex shapes that are difficult or impossible to produce using other casting processes.
- High production rates: Die casting can produce parts at high production rates, making it an efficient process for mass production.
- High strength: Die cast parts have high strength and stiffness, making them suitable for applications where strength and durability are critical.
- Low porosity: Die casting produces parts with low porosity, which improves their mechanical properties and reduces the risk of leaks or defects.
Disadvantages of Die Casting:
- High tooling costs: Die casting requires expensive tooling, which can be a significant barrier to entry for small businesses or startups.
- Limited material selection: Die casting is limited to materials that can be melted and injected under high pressure. This limits the range of materials that can be used in the process.
- Limited size range: Die casting is typically limited to small and medium-sized parts, although larger parts can be produced with specialized equipment.
- Surface finish: Die casting produces parts with a smooth surface finish, but the finish may not be as good as other casting processes, such as sand casting or investment casting.
Permanent Mold Casting:
Permanent mold casting is a casting process that involves pouring molten metal into a reusable mold. The mold is typically made of steel or cast iron and is designed to produce a specific part or component. The molten metal is poured into the mold, which is preheated to a specific temperature. The metal solidifies in the mold, and the part is removed once it has cooled.
Permanent mold casting is commonly used to produce parts for the automotive, aerospace, and industrial industries. It is also used to produce parts for the marine and power generation industries.
Advantages of Permanent Mold Casting:
- Low tooling costs: Permanent mold casting requires less expensive tooling compared to die casting, making it more accessible to small businesses and startups.
- Wide range of materials: Permanent mold casting can be used with a wide range of materials, including aluminum, magnesium, and copper alloys.
- High strength: Permanent mold cast parts have high strength and stiffness, making them suitable for applications where strength and durability are critical.
- Good surface finish: Permanent mold casting produces parts with a good surface finish, making them suitable for applications where appearance is important.
- Large size range: Permanent mold casting can be used to produce small and large parts, making it suitable for a wide range of applications.
Disadvantages of Permanent Mold Casting:
Continuing from the previous section on Permanent Mold Casting, here are some of the disadvantages of this casting process:
- Limited complexity: Permanent mold casting is not suitable for producing parts with complex shapes or intricate details. The mold must be designed with simple shapes and features to allow for easy removal of the part.
- Limited design flexibility: The design of the part is limited by the capabilities of the mold. Any changes to the design of the part require modifications to the mold, which can be time-consuming and expensive.
- Limited surface finish options: While permanent mold casting produces parts with a good surface finish, the options for surface treatments are limited compared to other casting processes.
- Porosity: Permanent mold casting can produce parts with porosity issues due to trapped gases during the casting process. This can affect the mechanical properties of the part and require additional inspection and testing.
- Limited scalability: While permanent mold casting can be used to produce small and large parts, it may not be suitable for mass production due to limitations in the size of the molds and the rate of production.
- Limited material properties: While permanent mold casting can be used with a wide range of materials, the properties of the material may be limited by the casting process. For example, the mechanical properties of the part may be affected by the cooling rate during casting.
In conclusion, both die casting and permanent mold casting have their advantages and disadvantages. The choice of casting process will depend on the specific requirements of the part or component being produced, including size, complexity, and material properties. Companies must carefully evaluate these factors and consider the cost, production rate, and quality of the final product before selecting a casting process.