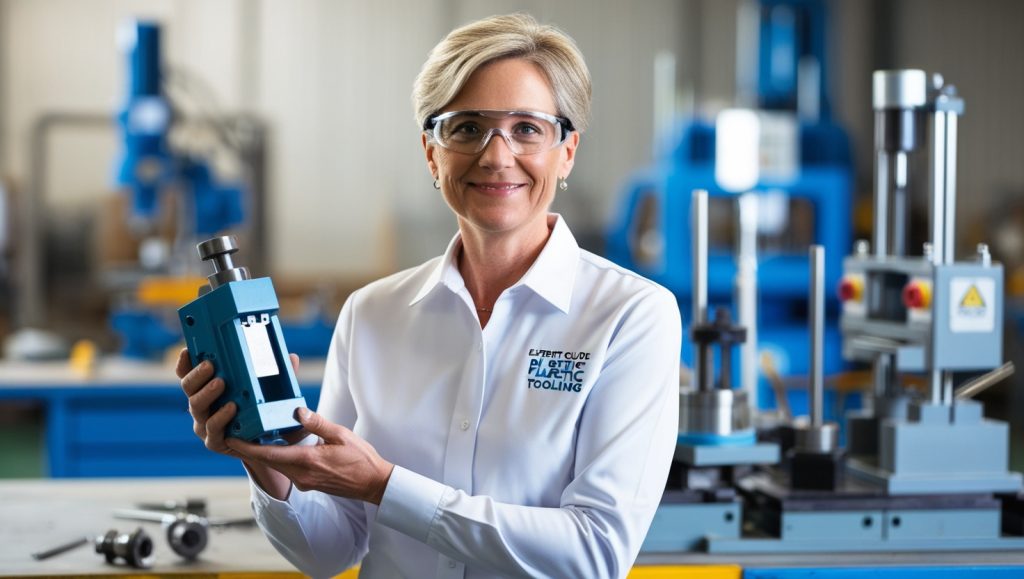
Plastic part tooling is the foundation of modern manufacturing, enabling the mass production of high-quality plastic components with precision and efficiency. From automotive parts to medical devices and consumer electronics, plastic tooling ensures consistency, durability, and cost-effectiveness in plastic molding.
The tooling process involves designing and fabricating molds that define the shape, structure, and surface finish of plastic parts. Advanced machining techniques, material selection, and innovative tooling designs contribute to the production of complex and intricate components.
This guide explores the essentials of plastic part tooling, including its types, materials, processes, challenges, and innovations shaping the industry.
What is Plastic Part Tooling?
Plastic part tooling refers to the specialized molds, dies, and fixtures used in the production of plastic components. These tools shape molten plastic into precise forms through various molding techniques.
Key aspects of plastic part tooling include:
- Designing and fabricating molds tailored to specific part geometries.
- Ensuring proper material flow, cooling, and ejection mechanisms.
- Maintaining tight tolerances for high-precision manufacturing.
- Enhancing production efficiency and reducing material waste.
A well-designed tooling system optimizes production speed, minimizes defects, and extends the lifespan of molds.
Types of Plastic Part Tooling
Different types of tooling are used based on the molding process and part requirements.
Injection mold tooling: The most common tooling method, used for producing high-precision plastic parts with tight tolerances. Includes single-cavity, multi-cavity, and family molds.
Blow mold tooling: Used for manufacturing hollow plastic products like bottles and containers, relying on air pressure to shape the plastic.
Compression mold tooling: Suitable for thermoset plastics, where the material is placed into a heated mold and compressed into shape.
Transfer mold tooling: A variation of compression molding where the material is preheated before being transferred into a closed mold cavity.
Rotational mold tooling: Used for large, hollow plastic parts, where powdered plastic is heated and rotated within the mold to coat the interior surface.
Each tooling type is designed for specific applications, production volumes, and material requirements.
Materials Used in Plastic Part Tooling
The choice of tooling material affects the durability, cost, and performance of the mold.
Steel molds: Preferred for high-volume production due to their durability and wear resistance. Common grades include P20, H13, and S136 steel.
Aluminum molds: Lightweight and cost-effective for prototyping and low-volume production but wear out faster than steel.
Beryllium copper inserts: Used for areas requiring high thermal conductivity to improve cooling efficiency.
Nickel and chrome coatings: Applied to enhance mold longevity, corrosion resistance, and surface finish.
Choosing the right material ensures longer mold life, improved part quality, and cost efficiency.
Plastic Part Tooling Process
The tooling process involves multiple stages to ensure precision and efficiency.
Design and engineering: CAD software is used to create a 3D model of the mold, incorporating features like gates, runners, and cooling channels.
Mold flow analysis: Simulations predict material flow, cooling patterns, and potential defects before manufacturing begins.
CNC machining and EDM: High-precision machining techniques shape the mold cavity and core, ensuring accurate part dimensions.
Polishing and surface finishing: The mold surface is treated to achieve the desired texture, gloss, or matte finish.
Mold assembly and testing: The final mold is assembled and tested with trial runs to validate its performance before full-scale production.
Proper tooling design and manufacturing ensure efficient production and minimal defects.
Key Components of Plastic Part Tooling
Core and cavity: The core shapes the internal features, while the cavity forms the external shape of the plastic part.
Runner system: Guides molten plastic from the injection unit to the mold cavity. Includes hot runner (efficient but costly) and cold runner (cheaper but produces more waste).
Cooling system: Channels within the mold regulate temperature, reducing cycle time and preventing warping.
Ejector system: Mechanisms like ejector pins and air blasts help remove the part from the mold without damage.
Gate design: The entry point for molten plastic, influencing flow patterns and part strength.
These components work together to ensure accurate, high-quality plastic part production.
Challenges in Plastic Part Tooling
Mold wear and tear: Continuous production causes wear on mold surfaces, requiring regular maintenance.
Shrinkage and warping: Plastic materials shrink as they cool, leading to dimensional variations if not properly controlled.
Cycle time optimization: Balancing cooling time with production speed is crucial to maintaining efficiency without compromising quality.
High initial tooling costs: Designing and fabricating molds require significant upfront investment, though costs decrease with large production volumes.
Material flow issues: Poor flow design can result in short shots, weld lines, or uneven distribution of material.
Addressing these challenges ensures longer mold life, better part quality, and reduced manufacturing costs.
Innovations in Plastic Part Tooling
Advancements in tooling technology have improved efficiency, precision, and sustainability.
3D-printed molds: Additive manufacturing allows rapid prototyping and testing of molds before full-scale production.
Conformal cooling: Cooling channels are designed to follow the shape of the part, improving heat dissipation and reducing cycle times.
AI-driven mold design: Artificial intelligence analyzes mold performance and optimizes flow paths for defect-free production.
IoT-enabled molds: Smart sensors monitor temperature, pressure, and wear in real-time, ensuring consistent quality and predictive maintenance.
Sustainable tooling materials: Recyclable and biodegradable materials are being explored for eco-friendly manufacturing solutions.
These innovations enhance productivity, reduce waste, and improve part quality.
Cost Considerations in Plastic Part Tooling
Several factors influence the cost of tooling, including material selection, complexity, and production volume.
Material costs: Steel molds are more expensive than aluminum but last significantly longer.
Tool complexity: Intricate designs with undercuts, thin walls, or multiple cavities require advanced machining and higher costs.
Production volume: High-volume production justifies investing in durable molds, while low-volume production may benefit from cheaper alternatives.
Maintenance and lifespan: Regular maintenance reduces long-term costs by extending mold life and preventing defects.
Understanding these cost factors helps manufacturers optimize tooling investments for long-term profitability.
Choosing the Right Tooling Manufacturer
Selecting the right tooling partner is crucial for quality and efficiency.
Experience and expertise: Look for manufacturers with proven experience in precision mold making.
Certifications and industry standards: Ensure compliance with ISO 9001 (quality management) and industry-specific certifications like ISO 13485 (medical device manufacturing).
Technology and capabilities: Choose a manufacturer with advanced CNC machining, EDM, and mold flow analysis capabilities.
Customer reviews and case studies: Research past projects to evaluate reliability, quality, and customer satisfaction.
A reputable tooling manufacturer ensures precision, durability, and cost-effective production.
Maintenance and Care of Plastic Part Tooling
Routine cleaning and lubrication: Prevents residue buildup and reduces friction on moving parts.
Inspection and wear analysis: Regularly checking for signs of wear or damage ensures timely repairs and extends mold life.
Preventive maintenance: Scheduled maintenance prevents unexpected breakdowns and costly production delays.
Repair and refurbishment: Worn-out parts like ejector pins and cooling channels should be replaced or refurbished as needed.
Proper maintenance practices maximize mold performance and reduce operational costs.
Applications of Plastic Part Tooling
Plastic tooling is widely used across industries for manufacturing complex, high-precision components.
Automotive: Dashboards, bumpers, connectors, and under-the-hood components.
Medical: Syringes, implants, diagnostic equipment, and surgical instruments.
Consumer electronics: Mobile phone casings, laptop housings, and connectors.
Industrial equipment: Custom plastic housings, machine components, and safety gear.
The versatility of plastic part tooling makes it an essential part of modern manufacturing.
Future Trends in Plastic Part Tooling
Smart molds with real-time monitoring: IoT-enabled molds track performance metrics to improve efficiency and reduce downtime.
AI-powered defect detection: Machine learning analyzes production data to predict and prevent defects.
Sustainable mold materials: Recyclable metals and energy-efficient production methods are being explored for eco-friendly manufacturing.
Hybrid tooling solutions: Combining injection molding with additive manufacturing allows for greater design flexibility and cost efficiency.
The future of plastic tooling is focused on precision, efficiency, and sustainability.
Conclusion
Plastic part tooling is the backbone of precision manufacturing, enabling the production of high-quality components with efficiency and consistency. By leveraging advanced technologies, material innovations, and quality control measures, manufacturers can optimize tooling processes for long-term success.
As industries demand more intricate designs, tooling techniques will continue to evolve, driving innovation in plastic molding for years to come.
FAQs
What materials are used for plastic part tooling?
Common materials include steel (P20, H13, S136) for high-volume production, aluminum for prototyping and low-volume runs, and beryllium copper for improved heat dissipation. Surface treatments like nickel or chrome plating enhance durability and performance.
How long does plastic tooling last?
The lifespan of a mold depends on the material, production volume, and maintenance. Steel molds can last for millions of cycles, while aluminum molds may be suitable for a few thousand cycles. Regular maintenance extends mold life significantly.
What factors affect the cost of plastic tooling?
Key cost factors include material selection, mold complexity, production volume, surface finishing, and maintenance requirements. High-precision molds with intricate details require advanced machining and higher initial investment.
How can defects in plastic molding be prevented?
Common defects like warping, sink marks, and short shots can be prevented by optimizing mold design, improving cooling systems, adjusting material flow, and maintaining proper injection parameters. Mold flow analysis software helps predict and eliminate potential defects.
What industries rely on plastic part tooling?
Industries such as automotive, medical, aerospace, electronics, and consumer goods heavily rely on plastic tooling to produce high-precision, durable, and cost-effective plastic parts.