Why Does the Future of Manufacturing Lie in High-Speed Molding?
The manufacturing technique known as high-speed moulding uses cutting-edge equipment and technology to create huge quantities of high-quality parts quickly. High speed mold machines are used in this procedure, allowing for manufacturing complicated components with excellent accuracy and consistency. This technology is getting increasingly popular since it has many benefits over conventional moulding techniques. These machines may run at a faster cycle time and greater injection speed. High-speed moulding is seen as the manufacturing technology of the future for several reasons:
- Enhanced Productivity:
This moulding equipment can create more components quickly, enhancing productivity and efficiency. This is crucial in the automotive, healthcare, and electronics sectors, with a strong demand for parts and quick turnaround times.
- Better Quality:
These moulding machines include sophisticated sensors and controls that enable exact temperature and pressure control, resulting in consistent and high-caliber components. As a result, less expensive post-production inspections and reworks are required.
- Savings:
These moulding machines may minimize manufacturing costs by reducing cycle times and cutting down on material waste. Additionally, automated technologies can help save expenses by reducing the need for physical labour.
- Flexibility:
These moulding machines are perfect for sectors that demand customization and flexibility since they can make a wide range of parts with complicated forms and sizes. It is a promising technology that has the potential to completely transform the manufacturing sector by boosting productivity, raising quality, cutting prices, and enhancing flexibility. As a result, it is anticipated to impact manufacturing in the future significantly.
Using high speed moulding in your production process has several advantages:
The industrial sector has undergone a revolution thanks to high-speed moulding, a relatively new technique. Compared to conventional manufacturing techniques, the technology enables faster output, higher accuracy, and better quality control. Energy, resources, and labour may all be saved by this moulding. With the help of high-speed machining, injection moulding, and other cutting-edge procedures, complicated parts may be produced swiftly and effectively. This method enables producers to create improved precision, strength, and longevity components.
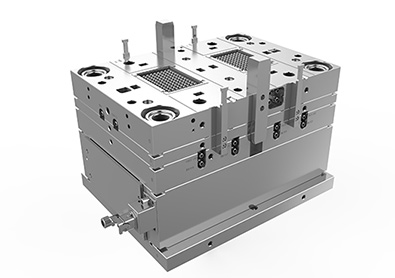
- Faster creation:
These machines' high injection speeds enable the creation of components at a pace that is far faster than that of conventional moulding techniques, cutting down on both production time and costs.
- Higher Accuracy and Consistency:
The high speed and accuracy of the machines allow for the production of components with a higher degree of correctness and consistency, resulting in fewer faults and less waste.
- Improved Productivity:
This moulding can improve productivity and efficiency, raising production and profitability overall. These factors include shorter cycle durations and lower scrap rates.
- Cost savings:
This moulding can aid in lowering manufacturing costs and boosting profitability by reducing production time and waste.
- Greater Design Flexibility:
This moulding can create complicated pieces with complex geometries that would be challenging or impossible to create using conventional moulding techniques. This is wise for many production applications since it may simplify your manufacturing process, raise product quality, and save expenses.
Faster Cycle Times using Scientific Molding for High-Speed Molding:
A systematic approach to injection moulding known as "scientific moulding" uses data and analysis to streamline the procedure and produce reliable, high-quality products. Scientific moulding may assist producers in achieving even shorter cycle times and better production outcomes when used with high-speed moulding. Here are some ways that high speed moulding and scientific moulding can work together to shorten cycle times:
- Improved Mold build:
Manufacturers may increase flow and decrease cycle times by employing scientific moulding concepts to build moulds with optimized gate and runner systems.
- Precise Material Selection:
Manufacturers may choose the best material for the job using scientific moulding, considering variables like viscosity, flow rate, and shrinkage. This guarantees correct material flow and shortens cycle times.
- Accurate Process Control:
Important process variables like temperature, pressure, and cooling time are carefully monitored and controlled in scientific moulding. Cycle times may be shortened, and part quality and uniformity may be improved.
- Data-Driven Optimization:
Manufacturers may use scientific moulding to gather and analyze data from each moulding cycle to improve the procedure and shorten cycle durations continually. Overall, the combination of high speed mold and scientific moulding may assist firms in achieving shorter cycle times, higher component quality, and enhanced productivity, improving profitability and increasing competitiveness in the market.
What are the significances of high-speed mould?
Increased productivity, greater quality, lower prices, design flexibility, and a competitive edge in the market are some benefits of high speed moulding.
- Low cycle durations and improved component quality are the aims of this moulding to boost production efficiency and lower costs.
- Enhanced Productivity: High speed moulding can manufacture more components in less time, boosting efficiency. This is crucial in sectors with high demand for parts and quick turnaround times.
- Design Flexibility: High speed moulding is perfect for sectors that need customization and flexibility since it can manufacture a broad range of parts with complicated forms and sizes.
- High-speed moulding may give enterprises a competitive edge by allowing them to make high-quality products more quickly than their rivals, increasing profitability and market share.
Conclusion:
The industrial sector has undergone a revolution thanks to high speed mold, a relatively new technique. Compared to conventional manufacturing techniques, the technology enables faster output, higher accuracy, and better quality control. Energy, resources, and labour may all be saved by high-speed moulding. For your particular requirements, it's crucial to do your homework and pick a dependable and knowledgeable supplier among the many ACE that offers high-speed mould production services or equipment. Consider taking into account aspects like their expertise, capabilities, quality control procedures, customer service, and price when choosing this mould maker or equipment provider. Reviewing client testimonials, references, and any credentials or professional associations the business may hold also informative.