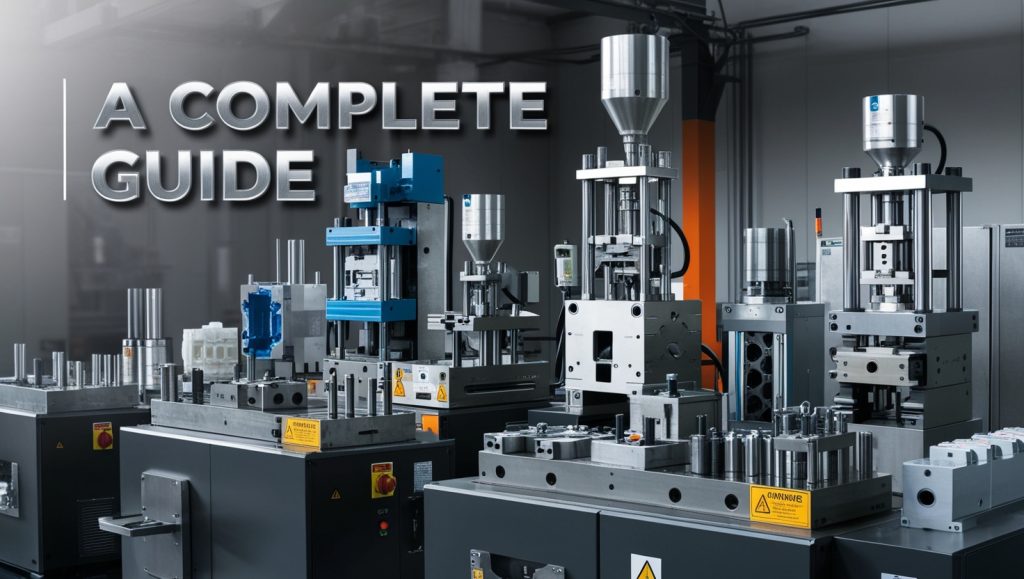
Injection mold tooling is a crucial element in plastic manufacturing, allowing businesses to produce high-quality parts with precision and efficiency. The right tooling ensures consistency, durability, and cost-effectiveness in mass production. This guide will cover everything you need to know about injection mold tooling, from its components and materials to costs and best practices.
What is Injection Mold Tooling?
Injection mold tooling refers to the specialized molds used in plastic injection molding, where molten plastic is injected into a shaped cavity, cooled, and solidified to form a final product. These molds are carefully designed to produce parts with exact dimensions, surface finishes, and mechanical properties. Depending on production volume, complexity, and material choice, different types of molds are used to optimize efficiency and cost.
Key Components of an Injection Mold
Core & Cavity
The mold consists of two main halves: the core and cavity. When the mold closes, the cavity forms the exterior shape of the part, while the core creates the internal features. These two sections must align perfectly to ensure accurate part dimensions.
Runner System & Gate
The runner system is a network of channels that direct molten plastic from the injection unit into the mold cavity. It consists of:
- Sprue – The main channel where plastic first enters.
- Runners – Distribute plastic to different cavities (for multi-cavity molds).
- Gates – Small openings where plastic flows into the cavity.
Gates play a crucial role in part quality, influencing factors like surface finish, shrinkage, and weld lines. Common gate types include edge gates, sub-gates, and pin gates, each suited for different applications.
Cooling System
Cooling is one of the most critical aspects of injection molding. An efficient cooling system helps regulate the mold temperature, reducing cycle times and preventing defects such as warping and shrinkage. Cooling channels circulate water or oil through the mold, ensuring even heat dissipation. Proper cooling system design improves part quality and increases production speed.
Ejector System
Once the plastic has cooled and solidified, it must be removed from the mold. The ejector system consists of ejector pins, sleeves, and plates that push the part out of the cavity. Proper ejector placement prevents part damage and ensures smooth removal without deformation.
Types of Injection Molds
Choosing the right type of injection mold depends on production requirements, cost considerations, and part complexity. Here’s an overview of the most common types:
Two-Plate Mold
A two-plate mold is the simplest and most widely used injection mold type. It consists of two halves—the core and cavity—separated along a single parting line. The molten plastic flows through a runner system and into the cavity, where it solidifies. After cooling, the mold opens, and the part is ejected.
- Advantages: Cost-effective, easy to manufacture, and ideal for simple parts.
- Disadvantages: Less flexibility in gating and runner system placement.
Three-Plate Mold
A three-plate mold has an additional plate that allows separate runner and gate placement, enabling more flexibility in part design. This type is useful for more complex geometries and better material flow control.
- Advantages: Better gating options, improved part quality, and automatic runner separation.
- Disadvantages: More expensive and complex to manufacture.
Hot Runner vs. Cold Runner Molds
- Hot Runner Mold – Uses heated runners to keep the plastic in a molten state, eliminating waste and improving cycle times.
- Pros: Reduces material waste, faster cycles, better part consistency.
- Cons: Higher upfront cost, requires more maintenance.
- Cold Runner Mold – The runner system cools and solidifies along with the part, requiring manual removal.
- Pros: Lower initial investment, simpler design.
- Cons: Increased material waste and longer cycle times.
Multi-Cavity vs. Single-Cavity Mold
- Multi-Cavity Mold – Produces multiple identical parts in a single cycle, improving efficiency and reducing costs per unit.
- Single-Cavity Mold – Produces one part per cycle, often used for prototypes or low-volume production.
Best Materials for Mold Tooling
The choice of mold material affects durability, heat resistance, and overall tooling cost.
Steel (P20, H13, S136)
Steel is the most commonly used material for high-volume production molds due to its durability and resistance to wear.
- P20 Steel – Pre-hardened, easy to machine, suitable for mid-volume production.
- H13 Steel – High hardness, excellent heat resistance, used for long production runs.
- S136 Stainless Steel – Corrosion-resistant, ideal for medical and food-grade applications.
Aluminum
Aluminum molds are lightweight and cost-effective, making them ideal for prototyping and low-volume production.
- Pros: Faster machining, lower cost.
- Cons: Shorter lifespan compared to steel.
Beryllium Copper
Used in mold inserts, beryllium copper enhances cooling efficiency due to its excellent thermal conductivity.
- Pros: Reduces cycle times, improves part quality.
- Cons: Expensive, limited to specific applications.
Mold Tooling Process
CAD Design & Flow Analysis
Mold design begins with computer-aided design (CAD) and mold flow analysis, which simulate how molten plastic will fill the cavity. This helps identify potential defects before manufacturing.
Machining (CNC & EDM)
Once the design is finalized, CNC machining and electrical discharge machining (EDM) are used to shape the mold components with high precision.
Polishing & Texturing
Polishing removes machining marks and enhances the final part’s surface finish. Texturing can also be applied for aesthetic or functional purposes.
Testing & Validation
Before production, the mold undergoes trial runs to ensure functionality, accuracy, and defect-free performance. Adjustments are made as needed before full-scale manufacturing begins.
Cost of Injection Mold Tooling
Injection mold tooling is a significant investment in the plastic manufacturing process, with costs varying based on several factors. Understanding what influences pricing and how to optimize costs can help businesses make informed decisions.
Factors Affecting Cost
Several key factors determine the cost of injection mold tooling:
- Complexity of the Design – Molds with intricate geometries, undercuts, and fine details require more advanced machining, increasing costs.
- Material Selection – Steel molds (e.g., P20, H13) are more expensive but last longer, while aluminum molds are cheaper but wear out faster.
- Number of Cavities – Single-cavity molds cost less upfront but produce fewer parts per cycle, while multi-cavity molds have a higher initial cost but reduce cost per part in large-scale production.
- Size of the Mold – Larger molds require more material and machining time, increasing production costs.
- Surface Finish & Texturing – Additional processing, such as high-gloss polishing or textured finishes, raises costs.
- Hot Runner vs. Cold Runner – Hot runner systems minimize material waste but are more expensive to manufacture.
Prototype vs. Production Molds
There are two main types of molds based on production needs:
- Prototype Molds
- Made from softer materials (e.g., aluminum).
- Lower cost, typically used for short-run testing.
- Suitable for design validation before investing in full-scale production.
- Production Molds
- Made from hardened steel for long-term use.
- High initial cost but lower cost per part over time.
- Built for high-volume manufacturing.
Cost-Saving Tips
- Optimize Design – Simplifying part geometry reduces mold complexity and machining time.
- Choose the Right Material – For small runs, aluminum molds can save costs while still producing functional parts.
- Utilize Multi-Cavity Molds – Higher upfront investment, but reduces cost per part in mass production.
- Reduce Cycle Time – Efficient cooling systems speed up production and increase output per mold.
- Consider Overseas vs. Domestic Manufacturing – Some manufacturers in regions like China and India offer lower tooling costs, but lead times and quality should be carefully evaluated.
Common Challenges & Solutions
Warping & Shrinkage
- Issue: Uneven cooling can cause parts to warp or shrink.
- Solution: Optimize cooling channel placement and use proper mold temperature control to ensure uniform cooling.
Cycle Time Delays
- Issue: Long cycle times increase production costs.
- Solution: Improve cooling efficiency by using beryllium copper inserts or optimized cooling lines. Selecting fast-cooling materials can also help.
Ejection Issues
- Issue: Parts sticking in the mold can slow production and damage the mold.
- Solution: Use well-placed ejector pins, air-assist ejection, or coatings to reduce friction and improve part release.
Choosing the Right Mold Manufacturer
Selecting the right mold manufacturer is crucial for ensuring high-quality production, cost efficiency, and timely delivery. The right supplier can help optimize mold performance and reduce long-term expenses.
Factors to Consider
When evaluating potential mold manufacturers, consider the following:
- Experience & Expertise – Look for manufacturers with a proven track record in your industry. Specialized experience in complex mold designs, tight tolerances, or specific materials is a plus.
- Capabilities & Technology – Ensure the manufacturer has advanced CNC machining, EDM, and mold flow analysis tools to produce precision molds.
- Lead Time & Production Capacity – Faster turnaround times are crucial for meeting production schedules. Ask about their typical lead time and ability to scale production.
- Quality Control & Certifications – A good manufacturer follows strict quality control processes, including testing and validation. ISO 9001 or other certifications indicate adherence to industry standards.
- Customer Support & After-Sales Service – Reliable after-sales support for maintenance and troubleshooting is essential to maximize mold lifespan.
Domestic vs. Overseas Mold Makers
Manufacturers can source molds either domestically or internationally. Both options have pros and cons:
- Domestic Manufacturers
- Higher costs but better quality control.
- Faster response time and easier communication.
- Reduced risk of intellectual property (IP) theft.
- Overseas Manufacturers (e.g., China, India, Mexico)
- Lower initial costs but may have quality consistency issues.
- Longer lead times due to shipping.
- Potential language barriers and challenges in after-sales service.
Future Trends in Injection Mold Tooling
AI-Driven Mold Design Optimization
Artificial intelligence (AI) is revolutionizing mold design by predicting defects, optimizing cooling layouts, and reducing cycle times. AI-powered simulations improve efficiency and reduce costly design iterations.
3D Printing for Rapid Prototyping
3D printing is being increasingly used to create prototype molds before committing to full-scale production tooling. This allows for faster design validation and reduced development costs. Hybrid molds—combining traditional machining with 3D-printed inserts—are also emerging as a cost-effective option.
Sustainable Mold Materials
The industry is shifting toward eco-friendly mold materials and recyclable plastics. Manufacturers are exploring biodegradable plastics and using energy-efficient molding processes to reduce carbon footprints.
Conclusion
Injection mold tooling is the backbone of plastic manufacturing. Selecting the right mold type, material, and manufacturer is essential for optimizing efficiency, quality, and cost-effectiveness. By staying informed about future trends such as AI-driven design, 3D-printed molds, and sustainable materials, businesses can stay ahead in the competitive landscape.
Key Questions to Ask Before Ordering an Injection Mold Tooling for Plastic Parts
Before committing to an injection mold manufacturer, it's crucial to ask the right questions to ensure you get a high-quality mold that meets your production needs. Here are some key questions to consider:
1. What Experience Do You Have with Similar Mold Designs?
- Ask if the manufacturer has produced molds similar to your part design, material, and complexity.
- Request case studies or references to verify their expertise.
2. What Materials and Finishes Do You Offer?
- Understand the types of steel (e.g., P20, H13, S136) or aluminum they use for molds.
- Inquire about surface finishes, texturing, and any special coatings to enhance mold longevity.
3. Can You Provide Mold Flow Analysis Before Production?
- Mold flow analysis helps detect issues like warping, air pockets, and shrinkage before the mold is built.
- A reputable manufacturer should provide this simulation to optimize mold design.
4. What Is Your Average Lead Time for Mold Fabrication?
- Ask about the estimated timeline from design approval to mold delivery.
- Understand factors that could cause delays, such as material shortages or complex machining requirements.
5. Do You Offer Mold Maintenance and Repair Services?
- Some manufacturers provide ongoing maintenance, repair, and refurbishment services.
- Check if they offer local support or require molds to be shipped back for servicing.
6. What Warranty or Guarantee Do You Provide on Molds?
- A good manufacturer should offer a warranty that covers defects, workmanship, or premature wear.
- Clarify terms on repairs, modifications, and expected mold lifespan under normal operating conditions.