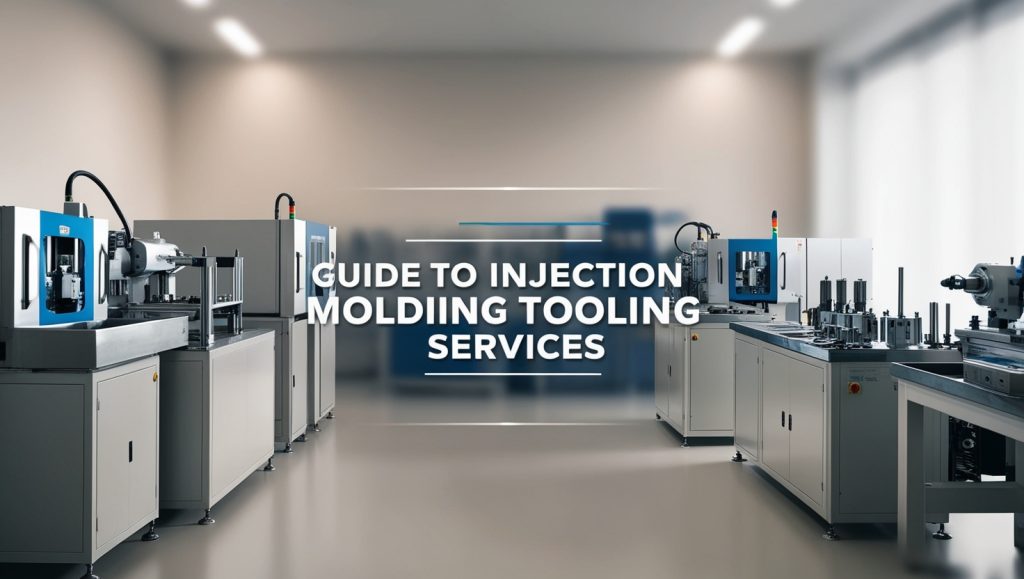
Injection molding is a widely used manufacturing process for producing plastic components across various industries, including automotive, medical, consumer goods, and aerospace. It enables mass production with high precision, consistency, and cost efficiency.
What is Injection Molding Tooling?
Injection molding tooling refers to the molds used to shape molten plastic into finished products. These molds are engineered with precision to ensure that the final product meets design and functional requirements.
Importance of High-Quality Tooling
Well-designed and durable tooling plays a critical role in manufacturing efficiency and product quality. Properly engineered molds enhance production speed, minimize defects, and reduce long-term costs by improving durability and efficiency.
Industries That Rely on Injection Molding Tooling
Manufacturers in industries such as automotive, medical devices, electronics, packaging, and aerospace depend on precision tooling to meet strict quality and performance standards.
What Are Injection Molding Tooling Services?
Definition of Injection Molding Tooling
Injection molding tooling includes the design, engineering, manufacturing, and maintenance of molds used in the injection molding process. The tooling determines the shape, accuracy, and production efficiency of molded parts.
Types of Injection Molding Tooling
Prototype Tooling
Prototype molds are used to test product designs before full-scale production. They are typically made of aluminum or softer steel to allow for quick modifications.
Bridge Tooling
Bridge tooling serves as an intermediate solution between prototyping and full production. These molds are more durable than prototype molds but not as expensive as high-volume production tooling.
Production Tooling
Production molds are designed for high-volume manufacturing and made from hardened steel or high-grade aluminum to withstand long-term use. These molds require advanced precision machining and are optimized for efficiency.
Overmolding and Insert Molding Tooling
Overmolding involves molding a second layer of material over an existing part, while insert molding embeds metal or other materials into the plastic during molding. These processes require specialized tooling for precision and durability.
The Tooling Development Process
Tooling Design and Engineering
Designing an effective mold requires a combination of computer-aided design (CAD) and mold flow analysis. These tools help optimize cooling, fill time, and cycle time to enhance efficiency and product quality.
Mold flow analysis ensures that the molten plastic fills the mold cavity evenly, reducing defects such as warping or air pockets. Design for Manufacturability (DFM) principles guide the creation of molds that are easier and more cost-effective to produce and maintain.
Material Selection for Injection Molding Tooling
The choice of mold material impacts durability, cost, and performance.
Steel vs. Aluminum Molds
Steel molds offer high durability and longevity, making them ideal for high-volume production. Aluminum molds are faster and cheaper to produce but have a shorter lifespan, making them more suitable for prototyping or low-volume runs.
Hardened vs. Soft Tooling
Hardened tooling is heat-treated for added strength and wear resistance, while soft tooling is made from untreated metals for easier modifications but reduced lifespan. The selection depends on production needs and budget constraints.
Mold Manufacturing and Fabrication
Mold manufacturing involves a combination of precision machining and finishing techniques to achieve the required specifications.
CNC Machining and EDM
Computer numerical control (CNC) machining and electrical discharge machining (EDM) are two common processes used in mold fabrication. CNC machining provides high precision, while EDM is used to create complex shapes and fine details in hardened materials.
Multi-Cavity Molds and Runner Systems
Multi-cavity molds allow multiple parts to be produced in a single injection cycle, increasing efficiency and reducing costs. Runner systems, which guide the flow of molten plastic, come in two main types: hot runner and cold runner systems. Hot runner systems improve cycle time and reduce material waste, while cold runner systems offer a simpler and lower-cost alternative.
Types of Injection Molding Tooling Services
Prototype Tooling Services
Prototype tooling is essential for testing and refining product designs before full-scale production. It allows manufacturers to validate part geometry, functionality, and manufacturability before investing in expensive production molds.
Benefits of Rapid Prototyping in Mold Development
- Allows for quick iterations and design modifications
- Reduces the risk of costly errors in production
- Provides a cost-effective way to validate designs before finalizing tooling
Cost-Effectiveness and Speed
Prototype molds are typically made from aluminum or softer steels, making them quicker and more affordable to produce than full-scale production molds.
Production Tooling Services
Production molds are designed for long-term, high-volume manufacturing. These tools are made from hardened steel or premium-grade aluminum to withstand thousands to millions of cycles without significant wear.
High-Precision, Long-Life Molds for Mass Production
- Built with tight tolerances to ensure consistent part quality
- Designed for long-term durability to reduce replacement costs
- Optimized for automated production lines to minimize manual labor
Automation-Friendly Tooling
- Integrates with robotic systems for efficient operation
- Supports high-speed injection cycles for maximum productivity
- Reduces material waste through optimized runner and gate designs
Maintenance & Repair Services
Mold maintenance and repair services ensure that tooling remains in optimal condition throughout its lifecycle, preventing costly downtime and defects.
Importance of Preventive Mold Maintenance
- Extends mold lifespan and maintains part quality
- Reduces downtime by preventing unexpected breakdowns
- Ensures consistent production efficiency
Troubleshooting Common Tooling Issues
- Wear and tear leading to dimensional inconsistencies
- Damage from excessive pressure or improper handling
- Misalignment issues affecting part accuracy
Tooling Modifications and Refurbishment
- Mold surface refinishing to restore precision
- Component replacement for worn-out parts
- Adjustments to accommodate new design changes
Custom Tooling & Secondary Operations
Overmolding & Insert Molding
Overmolding allows different materials to be combined into a single component, improving grip, durability, and aesthetics. Insert molding integrates metal or other materials into a plastic mold during the injection process.
Two-Shot Molding & Multi-Material Tooling
- Enables the production of complex, multi-material parts in a single cycle
- Reduces assembly costs by integrating multiple materials during molding
Post-Processing and Finishing Services
- Surface texturing for aesthetic and functional improvements
- Polishing and coating for enhanced durability
- Secondary assembly operations such as ultrasonic welding or adhesive bonding
Factors to Consider When Choosing an Injection Molding Tooling Provider
Expertise & Experience
A tooling provider with industry-specific experience ensures high-quality mold design and manufacturing. Established companies have the knowledge to optimize mold performance and minimize defects.
Technology & Equipment
Advanced manufacturing techniques such as CNC machining, EDM, and mold flow analysis improve tooling precision and efficiency. The use of high-tech software allows for accurate simulations before production.
Cost vs. Quality Trade-Offs
- Higher upfront costs for premium molds result in lower long-term expenses due to increased durability
- Cheap molds may lead to higher maintenance and production downtime, affecting overall ROI
Lead Times & Production Speed
- Faster turnaround times reduce delays in product launches
- Efficient project management and in-house capabilities ensure timely mold delivery
Cost Breakdown of Injection Molding Tooling
Factors Affecting Tooling Costs
- Material selection: Steel molds are more expensive but last longer, while aluminum molds are cheaper but wear out faster
- Mold complexity: Multi-cavity and intricate designs increase production costs
- Size and volume requirements: Larger molds require more material and machining time
- Runner system choice: Hot runner systems reduce material waste but are more expensive upfront
Prototype vs. Production Mold Costs
- Prototype molds cost significantly less but have limited lifespan
- Production molds are a long-term investment designed for large-scale manufacturing
Ways to Reduce Tooling Costs Without Compromising Quality
- Optimize mold design to reduce complexity and machining time
- Choose modular tooling solutions for interchangeable mold components
- Regular maintenance to prevent costly repairs and extend mold life
Future Trends in Injection Molding Tooling Services
Smart Molds with IoT Sensors for Predictive Maintenance
Advancements in Industry 4.0 have introduced smart molds equipped with IoT sensors. These sensors monitor mold performance in real time, tracking variables like temperature, pressure, and cycle count. Predictive maintenance systems can analyze this data to anticipate potential failures, reducing downtime and improving mold longevity.
3D-Printed Molds for Rapid Prototyping
Additive manufacturing technologies, such as metal and polymer 3D printing, are revolutionizing mold production. 3D-printed molds allow for faster iteration of prototype tooling, significantly reducing development time and costs. While they may not yet replace traditional tooling for high-volume production, they provide a flexible solution for low-volume and experimental applications.
Sustainable and Eco-Friendly Mold Materials
Sustainability is becoming a key focus in manufacturing. Tooling providers are exploring recyclable mold materials and energy-efficient production processes to minimize waste. Biodegradable and recycled plastics are also being tested in conjunction with traditional molds to support greener production practices.
Conclusion
Injection molding tooling services are essential for manufacturing high-quality plastic components efficiently and cost-effectively. The right tooling ensures precision, durability, and optimized production cycles, making it a critical investment for companies in industries such as automotive, medical, and consumer goods.
Choosing the right tooling provider is crucial for achieving high-quality results. Factors such as expertise, technology, lead time, and cost-effectiveness should be carefully evaluated. With the latest advancements in smart molds, 3D printing, and sustainable materials, the future of injection molding tooling is evolving to offer even greater efficiency and innovation.
For businesses looking to get started with injection molding tooling services, working with an experienced provider that offers comprehensive design, manufacturing, and maintenance solutions is the best approach.
FAQs
How long does it take to manufacture an injection mold?
The time required to manufacture an injection mold depends on factors such as complexity, material selection, and production volume. Prototype molds can take as little as one to four weeks, while full-scale production molds typically require six to twelve weeks.
What’s the difference between prototype and production molds?
Prototype molds are used for initial design validation and testing, often made of aluminum or softer steels for cost efficiency. Production molds are designed for long-term use, built from hardened steel to withstand high-volume manufacturing cycles.
What materials are best for injection molding tooling?
Steel is the most common material for high-durability production molds, while aluminum is used for rapid prototyping and low-volume applications. Specialty coatings and heat treatments can enhance mold performance based on specific manufacturing needs.
How much does an injection mold cost?
Injection mold costs vary widely depending on size, complexity, and material. Prototype molds can range from $5,000 to $20,000, while high-volume production molds may cost anywhere from $20,000 to $100,000 or more.
Can injection molds be modified after production?
Yes, injection molds can be modified to accommodate design changes or production improvements. Common modifications include altering cavity dimensions, adding new features, and repairing worn or damaged sections. However, extensive modifications may require significant retooling costs.