What does Injection Mold mean?
- The industrial method known as injection mould involves pumping molten material into a mould cavity to create pieces. The melted substance is commonly a thermoplastic or thermosetting polymer injected under high pressure into the mould after melting. The material is subsequently cooled and consolidated, giving the component its desired shape.
- Creating a mould cavity, which will ultimately be the form of the finished product, is the first step in the injection moulding process. After that, a metal mould is created, often out of steel or aluminium. The molten material may flow into the cavity and fill the mould thanks to the channels and gates that are built into the mould. The material is melted and injected into the mould under high pressure once the mould has been prepared. The mould is then opened, and the component is extracted when the material has had time to cool and harden. Repeating the procedure will result in several identical components.
- The method of injection moulding is adaptable and may be used to create a variety of parts, from microscopic things to massive ones. It is extensively employed in manufacturing goods in various sectors, including automotive, aerospace, medical device, consumer product, and more.
Why Choose ACE?
- We respond quickly to requests. Quotes are delivered the same day they are received and within minutes of getting an email.
- Our own design and development team is here.
- We have a robust quality control system to guarantee the highest quality for our products.
- We provide competitive pricing that is cheaper than that of our rivals.
- We provide samples as soon as possible, and each sample has undergone quality control.
- We offer OEM/ODM services to a variety of clients.
- We truly work with our clients during shipping and deliver goods on schedule.
- We are proud that at least 96% of our customers have been with us from now on.
The Method of Injection Moulding:
- Plastic items with high precision are produced using the injection moulding method. Plastic pellets are melted in this highly automated process, followed by their injection into a mould cavity. The product will be produced in the desired size and form thanks to the design of the mould cavity. After cooling, the plastic can adopt the shape of the mould. The final item is then removed after opening the mould.
- The mould preparation is the first step in the injection moulding process. A wax or plastic material is first poured into the mould to mould the product into the required shape. Once injected, the wax or plastic substance is heated in the mould, causing it to melt and take the desired shape. After that, molten plastic is poured into the mould to replace the wax or plastic substance.
- After being injected into the mould, the molten plastic is cooled and given time to set. The final item is removed from the mould once it has been opened. Injection moulding is a highly exact method that can create components with fine features and high precision.
The Beneficial Effects of Injection Molding in the manufacturing process:
Injection moulding is a manufacturing method where melted materials are injected into a mould to create a range of parts and goods, typically plastic pellets. Many advantages of this approach include the following:
- Efficiency:
Due to its ability to quickly create many parts, injection moulding is a very effective manufacturing technology. Additionally, it enables excellent reproducibility, ensuring precision and consistency in every component manufactured.
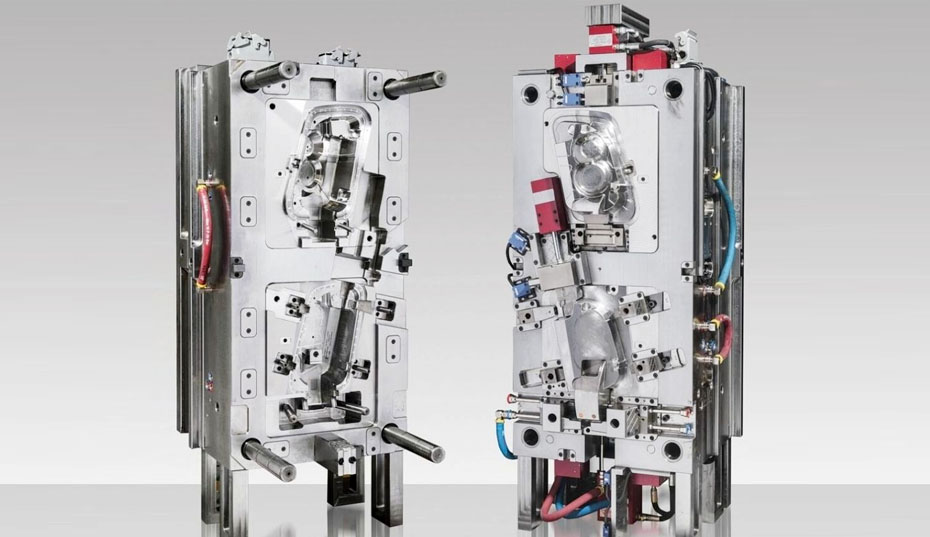
- Cost-effectiveness:
Because injection moulding requires less manual work and produces less waste than other methods, it can be economical to produce large quantities of plastic parts. Utilizing computer-controlled machinery further lowers the possibility of mistakes and flaws.
- Versatility:
An extensive range of goods, from basic home items to intricate car parts, may be produced using injection mould. With traditional manufacturing processes, producing parts with fine forms and features can be challenging. The procedure makes this possible.
- Rapid production:
Each cycle of the injection moulding process only takes a few seconds to complete. This translates to the ability to create huge volumes of components rapidly and effectively.
The different types of injection mould:
Different injection moulds are available that may be used to create plastic components. The kind of mould that will be utilized will rely on the components created and the intended end-use for the parts. Steel, aluminum, and brass are just a few materials that may be used to create injection moulds. The application and the intended strength and durability level will determine the material to be utilized.
The significance of a quality design:
- The success of the plastic injection moulding process depends on a well-designed injection mould. The kind of plastic to be used, the size and shape of the parts to be produced, and the intended end use of the pieces must all be considered in the mould design. Poor mould design can result in subpar components, subpar performance, and expensive manufacturing costs. Confirming that the mould is made to the required specifications and can produce excellent quality pieces is crucial.
- Numerous advantages of injection mould design include better product quality, higher manufacturing effectiveness, and lower prices. When an injection mould is properly designed, it may create appropriate quality and performance components. Sales and customer happiness may both rise as a result of this.
- A correctly constructed mould can also improve production efficiency and lower costs. The amount of time and money required for production may be decreased by using an injection mould built to make parts fast and effectively. The corporation may see more earnings as a result of this.
Conclusion:
The injection moulding method is used to create plastic parts by injecting molten plastic material into a mould cavity. The method is commonly used to create plastic objects of all shapes and sizes. The injection moulding department can work around the clock to ensure on-time delivery. A competent quality control system ensures the final goods' quality by monitoring all processes carried out in a regulated way. Meanwhile, ACE offers a sizable, trustworthy partner in the area that is outfitted with machinery weighing between 50 and 2000 tons, including tools for two-shot moulding, gas-assisted injection moulding, etc.