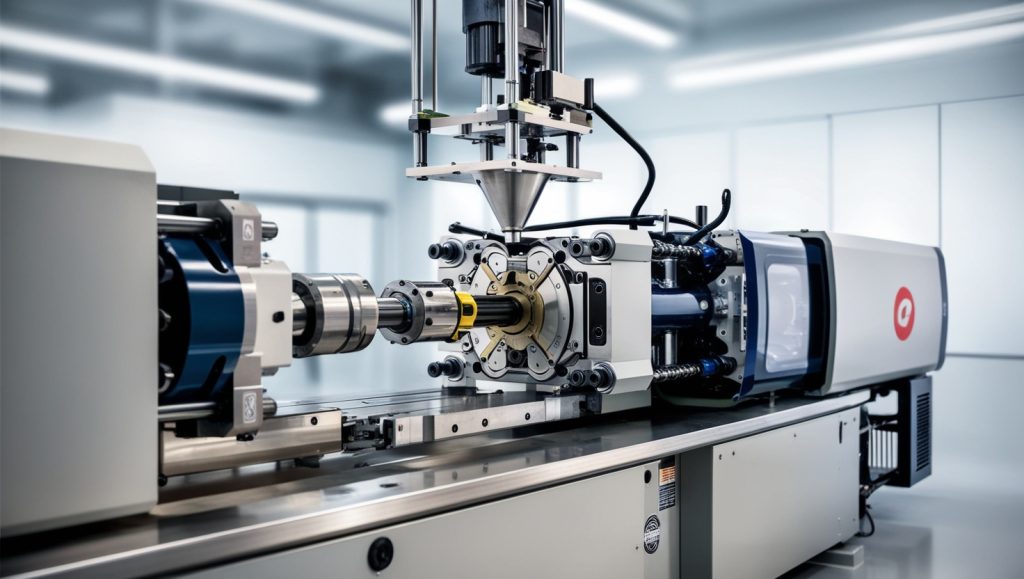
Manufacturing is no longer just about mass production. Companies are increasingly looking for flexible, cost-effective solutions for smaller product batches. That’s where low-volume plastic injection molding (LVPIM) comes in.
Unlike traditional injection molding, which prioritizes high production volumes, LVPIM is optimized for runs as small as 100 to 10,000 units. Whether for prototyping, bridge production, or limited market demand, this method is gaining traction across industries like automotive, healthcare, and consumer goods.
What is Low-Volume Plastic Injection Molding?
At its core, injection molding is a process where molten plastic is injected into a mold, cooled, and then ejected as a finished part. High-volume injection molding typically involves hardened steel molds designed for hundreds of thousands of cycles.
Low-volume injection molding, on the other hand, is designed for smaller batches, using materials like:
- Aluminum molds – Cheaper and faster to produce but less durable.
- Soft steel molds – Offer a middle ground between durability and cost.
- 3D-printed molds – Ideal for very low runs or quick prototyping.
Benefits of Low-Volume Injection Molding
Cost-Effectiveness
One of the main advantages of low-volume injection molding is that it lowers initial costs. Traditional high-volume injection molding requires expensive steel molds, which can cost tens of thousands of dollars. In contrast, low-volume production often uses aluminum molds, which are cheaper and quicker to produce. This makes it a great option for startups, small businesses, or companies testing new products before committing to full-scale manufacturing. Additionally, because the mold-making process is faster, companies save both time and money during the early stages of product development.
Another cost-saving factor is reduced material waste. Since fewer parts are produced, companies avoid the expenses of excess production and storage. This is especially useful for industries where design changes are frequent, such as medical devices or consumer electronics.
Faster Lead Times
Low-volume injection molding speeds up production significantly. While traditional molds may take weeks or even months to manufacture, aluminum molds for low-volume production can be made in days. Once the mold is ready, parts can be produced quickly, sometimes within a few hours.
This fast turnaround is especially helpful for companies developing prototypes or limited-run products. It allows businesses to test products in the market, gather feedback, and make adjustments without waiting for long production cycles. Faster lead times also mean companies can respond quickly to changes in demand, reducing the risk of overproduction or inventory shortages.
Design Flexibility
Another major advantage is the ability to make design changes easily. In high-volume production, modifying a steel mold is costly and time-consuming. However, in low-volume molding, aluminum molds can be adjusted or replaced at a much lower cost. This allows engineers and designers to refine their product without worrying about major financial losses.
This flexibility is particularly valuable in industries where products must meet strict standards, such as aerospace and medical manufacturing. If a design needs improvement, low-volume injection molding allows for rapid updates without delaying the entire project. It is also useful for creating customized or specialty products that do not require mass production.
Process Overview
Tooling and Mold Design
The first step in low-volume injection molding is creating the mold, which shapes the plastic parts. For low-volume production, molds are often made from aluminum instead of steel. Aluminum molds are quicker and cheaper to manufacture, making them ideal for short production runs. Despite being softer than steel, they can still produce thousands of high-quality parts. The mold design includes features like cooling channels, ejector pins, and parting lines to ensure smooth production. Proper mold design helps prevent defects such as warping, sink marks, or uneven filling.
Injection Molding Setup
Once the mold is ready, it is installed in the injection molding machine. The setup process involves securing the mold, setting the correct temperature, and adjusting pressure settings. The temperature is carefully controlled to ensure the plastic melts properly before being injected into the mold. Pressure settings must be optimized to fill the mold completely without causing defects. The machine is then tested with a few trial runs to ensure everything is working correctly before full production begins.
Production Cycle
The production process follows a series of steps to create each plastic part:
- Clamping – The two halves of the mold are securely closed and held together under pressure.
- Injection – Molten plastic is injected into the mold at high pressure, filling every cavity.
- Cooling – The plastic cools and hardens inside the mold. Cooling channels help speed up this process.
- Ejection – Once the plastic has solidified, the mold opens, and the part is pushed out using ejector pins.
This cycle is repeated continuously to produce multiple parts in a short amount of time. The efficiency of this process allows manufacturers to produce hundreds or even thousands of parts quickly.
Quality Control and Post-Processing
After the parts are molded, they go through inspection to check for defects like warping, incomplete filling, or surface imperfections. Quality control methods include visual inspection, measuring dimensions with calipers, and using advanced tools like coordinate measuring machines (CMMs) for precise checks.
If needed, post-processing steps such as trimming excess material, sanding rough edges, or adding coatings are performed to improve the final product’s appearance and functionality. In some cases, additional machining may be required to achieve tight tolerances or specific design features.
Material Selection
Common Thermoplastics
Different types of plastic materials are used in low-volume injection molding, depending on the product’s requirements. Some commonly used thermoplastics include:
- ABS (Acrylonitrile Butadiene Styrene) – Strong, impact-resistant, and easy to process, making it suitable for consumer goods and automotive parts.
- Polypropylene (PP) – Lightweight, flexible, and resistant to chemicals, often used in packaging, medical devices, and automotive components.
- Polycarbonate (PC) – Extremely durable and transparent, commonly found in protective gear, optical lenses, and electrical enclosures.
Material Properties
The choice of material affects the performance, cost, and durability of the final product. For example, a part that needs high impact resistance may require ABS or polycarbonate, while a lightweight, cost-effective solution may use polypropylene. Some materials offer heat resistance, UV stability, or chemical resistance, making them suitable for specialized applications.
Design Considerations
Wall Thickness
Maintaining a uniform wall thickness is crucial in injection molding. If the walls are too thick, the plastic may cool unevenly, leading to warping, sink marks, or internal stress. On the other hand, if the walls are too thin, the part may become weak or fail to fill properly. A recommended thickness range is typically between 1.0 mm to 3.0 mm, depending on the type of plastic used. Designers should avoid sudden changes in thickness, as these can create weak points or cause defects during molding.
Draft Angles
Draft angles are slight tapers added to the walls of a molded part to help with ejection from the mold. Without proper draft angles, parts may get stuck or be damaged during removal. A general rule is to apply at least 1 to 2 degrees of draft per inch of depth, but this can vary based on the material and surface finish required. Including draft angles reduces wear on the mold and improves production efficiency.
Radii and Corners
Sharp edges and corners can lead to stress concentrations and weak points in the molded part. To prevent cracking or failure, designers should use rounded corners whenever possible. Adding a radius of at least 0.5 times the wall thickness improves material flow during molding, reduces stress buildup, and enhances the strength of the part.
Comparison with Other Manufacturing Methods
3D Printing
3D printing is well-suited for very low volumes (1-100 parts) and complex geometries that would be difficult or impossible to mold. It allows for rapid prototyping and quick design iterations without expensive tooling. However, 3D-printed parts often lack the durability, surface finish, and material properties of injection-molded parts, making them unsuitable for large-scale production or end-use applications requiring high strength.
CNC Machining
CNC machining is ideal for creating strong, precise parts from solid blocks of material. It is commonly used for metal or high-performance plastic parts where strength and dimensional accuracy are critical. However, CNC machining is typically slower and more expensive than injection molding for producing large quantities of plastic parts. It is best used for low-volume production when molding is not feasible due to material or design constraints.
Urethane Casting
Urethane casting is a bridge between 3D printing and injection molding. It is used for mid-range production (10-1,000 parts) and produces high-quality, durable parts with good surface finishes. Silicone molds are used to cast liquid polyurethane, which cures into the final shape. While it has lower tooling costs than injection molding, urethane casting is less durable for high-volume production. It is often used for prototypes, market testing, or limited-edition products.
Selecting a Low-Volume Injection Molding Partner
Experience and Expertise
Choosing a manufacturing partner with experience in low-volume production is essential. A skilled partner understands the unique challenges of small-batch manufacturing and can help optimize the design for cost and efficiency. Look for a company with a track record of working with different materials and industries.
Quality Assurance
Quality control is critical in low-volume injection molding to ensure parts meet design specifications. A reliable partner should have inspection processes in place, such as dimensional checks, material testing, and mold maintenance, to prevent defects. Certifications such as ISO 9001 or ISO 13485 (for medical devices) indicate a strong commitment to quality.
Flexibility and Responsiveness
In low-volume manufacturing, design changes and quick turnaround times are common. A good manufacturing partner should be flexible in accommodating modifications, adjusting production schedules, and offering feedback to improve the design. Strong communication and responsiveness are key factors in selecting the right supplier.
Conclusion
Low-volume plastic injection molding provides several benefits, including lower costs, faster production, and greater design flexibility. It is an excellent choice for prototyping, small-batch production, and bridge manufacturing before full-scale production.
Businesses looking for a reliable way to produce high-quality plastic parts without large upfront investments should consider low-volume injection molding. Whether for testing new designs, manufacturing custom products, or producing limited runs, this method offers a cost-effective and efficient solution.