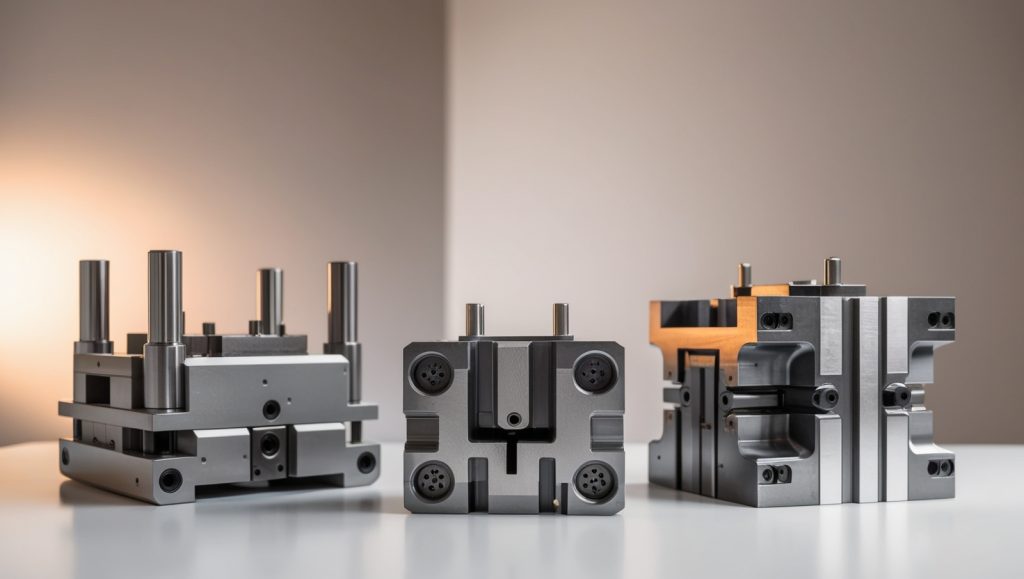
Low-volume plastic tooling is an essential manufacturing approach that fills the gap between prototyping and mass production. It allows businesses to create high-quality plastic components in limited quantities, typically between 100 and 10,000 units. This method provides a cost-effective and flexible alternative to traditional high-volume injection molding, making it an attractive option for industries that require short production runs, customized components, or rapid iterations.
This guide explores low-volume plastic tooling in depth, examining its advantages, various methods, industry applications, key considerations, and how businesses can leverage it to optimize their production strategy.
Understanding Low-Volume Plastic Tooling
Traditional plastic manufacturing relies heavily on high-volume injection molding, a process that demands significant upfront investment in tooling. This method is ideal for large-scale production but can be prohibitive for smaller projects due to high mold costs and long lead times. Low-volume plastic tooling presents an alternative that maintains high quality while reducing costs and production time.
What is Low-Volume Plastic Tooling?
Low-volume plastic tooling refers to manufacturing processes designed for small-scale production, utilizing cost-efficient molds and flexible tooling techniques. This approach benefits companies that need limited runs of plastic parts for market testing, product development, or specialized applications. The goal is to achieve a balance between affordability, speed, and durability without committing to expensive mass production molds.
How Does It Work?
Unlike traditional steel molds used in mass production, low-volume tooling often employs alternative materials such as aluminum or 3D-printed mold inserts. These materials are easier to machine, allowing for rapid prototyping and quick adjustments. The process typically involves:
- Design and prototyping – Engineers create CAD models and prototypes to test form and function.
- Tooling production – Molds are fabricated using CNC machining, 3D printing, or urethane casting.
- Injection molding or casting – The selected process is used to manufacture parts from the molds.
- Final testing and iteration – The produced components are evaluated, and molds can be adjusted if necessary.
Why is it Important?
Low-volume tooling is crucial for businesses looking to validate product designs before full-scale production. It provides a testing ground for design improvements, reduces the financial risk of launching new products, and enables companies to meet the demands of niche markets without excessive inventory.
Who Benefits?
- Startups and small businesses testing new product designs.
- Established companies creating limited-edition or custom products.
- Industries requiring short-run parts, such as aerospace, automotive, and medical sectors.
- Research and development teams iterating on designs before mass production.
Advantages of Low-Volume Plastic Tooling
Cost Savings
One of the most significant advantages of low-volume plastic tooling is the reduction in tooling costs. Traditional injection molding relies on steel molds, which are durable but expensive to manufacture. In contrast, low-volume tooling often uses aluminum or hybrid molds, significantly cutting down initial costs. By lowering the financial barrier, businesses can allocate resources to other critical aspects like marketing, testing, and distribution.
- Example: A startup developing a new consumer electronics product may need only 1,000 units for initial testing. Instead of investing $50,000+ in steel molds, they can opt for an aluminum mold that costs around $5,000-$10,000, significantly reducing upfront expenses.
Faster Time-to-Market
Speed is crucial in today’s competitive markets. Low-volume plastic tooling accelerates production cycles by reducing mold manufacturing time. Aluminum molds, for instance, can be machined in a fraction of the time required for steel molds. This allows businesses to launch products quickly, gather user feedback, and make necessary modifications without waiting months for traditional tooling.
- Example: In the medical industry, rapid response to evolving patient needs is vital. Low-volume tooling enables medical device manufacturers to quickly develop and distribute new components without being constrained by long production lead times.
Design Flexibility and Iteration
Unlike mass production, where mold changes are costly and time-consuming, low-volume plastic tooling allows for quick modifications. Businesses can refine product designs, test different materials, and improve functionality without the financial risk of scrapping expensive steel molds.
- Example: An automotive company designing custom dashboard components can produce multiple design iterations in small batches to evaluate performance and user experience before finalizing a mass production model.
Risk Reduction
For new product launches, market uncertainty is always a concern. Low-volume production reduces the financial risks associated with large inventory commitments. Instead of mass-producing thousands of units with uncertain demand, companies can test the market with smaller batches and scale production based on actual sales data.
- Example: A startup introducing a smart home device can use low-volume tooling to produce an initial batch of 2,000 units. If demand exceeds expectations, they can scale up production while refining their design.
Comparison of Low-Volume Plastic Tooling Methods
Choosing the right tooling method is essential for balancing cost, speed, and part quality. Below is a comparison of some of the most commonly used low-volume plastic tooling methods:
Method | Description | Ideal For |
---|---|---|
Rapid Tooling | Uses CNC machining or 3D printing to create quick-turnaround molds, ideal for prototyping and testing. | Small production runs, design validation. |
Cast Urethanes | Utilizes silicone molds to produce high-quality plastic parts from liquid urethane resins. Good for low-cost short runs. | Prototypes, functional testing, low-volume production. |
Injection Molding (Soft Tooling) | Uses aluminum or hybrid molds instead of steel, providing a cost-effective alternative to traditional injection molding. | Short-run production of injection-molded components. |
3D Printing for Molds | Directly prints mold inserts or entire molds for quick and low-cost production. | Rapid prototyping, one-off parts, customized small batches. |
Vacuum Casting | Uses a master model to create silicone molds, which are then used to cast plastic parts in a vacuum chamber. | Low-volume runs of flexible or rigid plastic parts. |
Each of these methods serves a unique purpose, and selecting the right one depends on factors such as production volume, material requirements, and lead time.
Industry Applications of Low-Volume Plastic Tooling (500+ words)
Low-volume plastic tooling is a versatile solution that benefits multiple industries. Some of the key sectors leveraging this approach include:
Medical Devices
The medical field requires precision, customization, and quick turnaround times. Low-volume tooling is widely used for:
- Custom prosthetics tailored to individual patients.
- Surgical instruments for specialized procedures.
- Medical device housings that need regular updates based on patient feedback.
Automobile manufacturers use low-volume tooling for:
- Custom interior and exterior components in high-end vehicles.
- Replacement parts for classic or discontinued models.
- Short-run specialty modifications for performance tuning.
Aerospace
Aerospace applications require lightweight, durable components in limited quantities. Low-volume tooling supports:
- Prototyping new parts before full-scale manufacturing.
- Creating lightweight components for aircraft interiors.
- Manufacturing drone parts for testing and performance validation.
Consumer Electronics
The consumer electronics industry thrives on innovation and rapid development. Low-volume tooling helps:
- Test new product concepts before mass production.
- Produce limited-edition or regional product versions.
- Develop high-quality enclosures for IoT and smart home devices.
Key Considerations When Choosing Low-Volume Plastic Tooling (500+ words)
To maximize the benefits of low-volume plastic tooling, consider these factors:
- Material Selection – Choose plastics suited for your product’s durability, flexibility, and environmental resistance.
- Tooling Material – Decide between aluminum, hybrid, or 3D-printed molds based on cost and expected lifespan.
- Production Volume – Ensure the method aligns with your batch size requirements.
- Lead Time – Factor in how quickly you need parts to be manufactured.
By carefully evaluating these aspects, businesses can effectively integrate low-volume plastic tooling into their manufacturing strategy.
Final Thoughts
Low-volume plastic tooling offers a practical, cost-effective solution for producing small batches of plastic components. It provides flexibility, accelerates product development, and reduces financial risk, making it an invaluable tool for businesses across industries. Whether for prototyping, custom production, or market testing, this approach ensures companies can stay adaptable in an ever-changing market landscape.
Frequently Asked Questions (FAQ) on Low-Volume Plastic Tooling
1. What is the typical production range for low-volume plastic tooling?
Low-volume plastic tooling is designed for production runs ranging from 100 to 10,000 units, depending on the method used. Some processes, like urethane casting or rapid tooling, are best suited for prototyping and small batches (100–1,000 units), while soft tooling with aluminum molds can support up to 10,000 units before requiring mold replacement or reinforcement.
2. How does low-volume tooling compare to traditional injection molding in terms of cost?
Traditional injection molding requires expensive hardened steel molds, which can cost between $20,000 and $100,000 or more, making it impractical for small runs. Low-volume tooling, on the other hand, uses cost-effective aluminum, soft steel, or 3D-printed molds, reducing initial investment to $5,000–$15,000 while maintaining high-quality output. This makes it an ideal option for businesses that need limited production without committing to high upfront costs.
3. What materials can be used with low-volume plastic tooling?
A wide range of plastics can be used, including:
- ABS (Acrylonitrile Butadiene Styrene) – Durable and impact-resistant.
- Polycarbonate (PC) – High heat resistance and transparency.
- Nylon (PA) – Strong and flexible, ideal for mechanical parts.
- Polypropylene (PP) – Lightweight and chemically resistant.
- Urethane Resins – Used in vacuum casting for short-run parts.
Material selection depends on the required strength, flexibility, temperature resistance, and intended application of the final product.
4. What are the lead times for low-volume plastic tooling?
Lead times vary depending on the tooling method:
- 3D-printed molds – As fast as 1–2 weeks for prototyping.
- Aluminum injection molds – Typically 3–6 weeks, much faster than steel molds, which take 8–12 weeks or more.
- Urethane casting – 2–3 weeks for silicone mold preparation and production.
Since tooling production is streamlined, businesses can bring products to market much faster than with traditional molding.
5. Is low-volume plastic tooling suitable for end-use parts or just prototypes?
While many businesses use it for prototyping and product validation, low-volume plastic tooling is also suitable for final end-use products. Many industries, including medical devices, aerospace, and automotive, rely on it for custom components, limited-edition parts, and specialty production. Certain materials and processes can produce parts that match the strength and durability of mass-produced components, making it a practical alternative to large-scale injection molding.