Mold manufacturing is instrumental across a wide range of industries by providing the capability to produce intricate parts and components. At ACE, we understand the complexity of this process and the importance of having precision, knowledge, and advanced technology to obtain successful results. This blog will give you the opportunity to gain a deeper insight into our mold manufacturing process; from the design phase up to quality control. Through constant efforts in innovating and perfecting our processes, ACE is proud to have built a reputation as an industry leader.
I. The Art of Mold Design:
Mold design forms the foundation of successful mold manufacturing. ACE focuses on collaborating closely with its clients to understand their unique requirements and develop tailored solutions. The design phase involves considering factors such as part geometry, material selection, and production volume. ACE's team of skilled designers leverages computer-aided design software and their extensive knowledge to create precise and efficient mold designs.
1.1 Understanding Unique Requirements:
The first step in ACE's mold design process is to thoroughly understand the unique requirements of each client. This involves close collaboration and clear communication to identify key factors such as part geometry, material selection, and production volume. By gaining a deep understanding of the client's needs, ACE can ensure that the mold design aligns perfectly with the intended purpose and specifications of the final product.
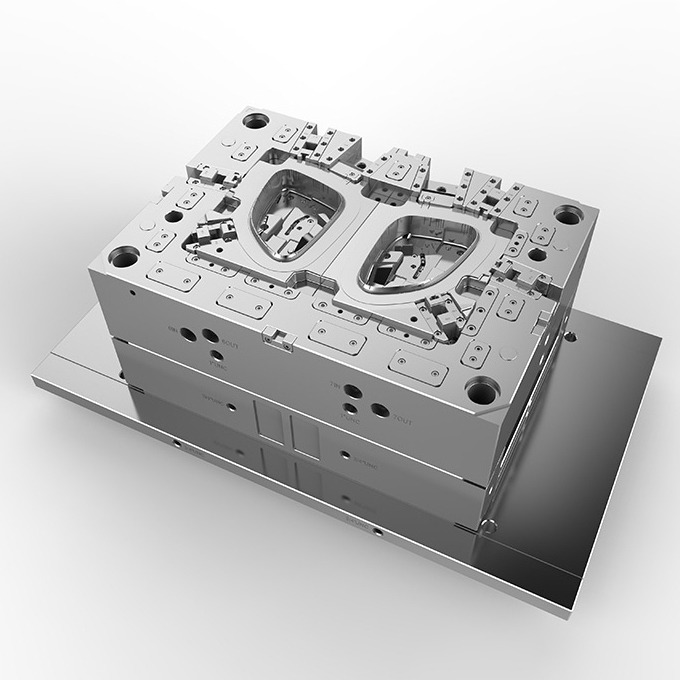
1.2 Creating Precise and Efficient Mold Designs:
With a deep understanding of the client's requirements and the aid of CAD software, ACE's skilled designers craft precise and efficient mold designs. They meticulously consider factors such as parting lines, gate locations, cooling systems, and ejection methods to optimize the mold's performance and maximize productivity. ACE's focus on precision ensures that the mold design will result in high-quality finished products with minimal defects, reducing manufacturing costs and improving overall customer satisfaction.
II. Prototyping: From Concept to Reality:
Prototyping is a critical step in mold manufacturing, allowing for the validation and refinement of designs before proceeding to mass production. ACE employs various prototyping techniques, such as 3D printing and CNC machining, to produce functional prototypes that closely resemble the final product. By thoroughly testing these prototypes, ACE ensures that the molds are optimized for performance, functionality, and manufacturability.
2.1 Optimized Performance and Functionality
Through rigorous testing of their prototypes, ACE ensures that the molds they design offer optimal performance and functionality. By simulating real-world conditions and subjecting prototypes to various stress tests, they can identify potential flaws and make necessary refinements. This iterative process guarantees that the final mold will meet the required specifications and deliver outstanding results during production.
2.2 Enhanced Manufacturability
In addition to performance and functionality, ACE prioritizes the manufacturability of its mold designs. With their prototyping expertise, they can identify any potential manufacturing challenges early in the design phase. By fine-tuning the prototypes, ACE optimizes the mold's construction and ensures seamless integration with the production process, ultimately reducing costs and improving overall efficiency.
III. Tooling: Precision in Action:
Tooling is a fundamental aspect of mold manufacturing, where ACE excels. The company utilizes advanced machinery and cutting-edge technologies to fabricate high-quality molds with exceptional precision. Computer numerical control (CNC) machines, wire electrical discharge machining (EDM), and high-speed milling are just a few examples of the tools and techniques employed by ACE. By leveraging these technologies, ACE achieves tight tolerances and intricate features, ensuring the molds are built to exact specifications.
3.1 Advanced Machinery for Superior Results
ACE understands that precision is key in mold manufacturing, and that's why they have invested in state-of-the-art equipment. The company boasts an impressive array of tools and machinery, including Roeder's high-speed CNC, Makino EDG3 precision EDM, and the Erowa system, known for its highest repeat-positioning accuracy. These cutting-edge technologies enable ACE to handle the most demanding mold manufacturing projects with ease.
3.2 Versatile Mold Offerings
ACE takes pride in its ability to cater to a wide range of mold manufacturing needs. They produce a variety of injection molds, ranging from single-cavity SPI class 103 molds to multi-cavity SPI class 101 molds. This versatility allows them to serve diverse industries and accommodate different production requirements. ACE's mold types include standard molds with side actions and lifters, hot runner molds, unscrewing molds, 2K molds, and insert-type over molds. Whatever the specifications, ACE has the expertise and resources to deliver outstanding results.
IV. Machining: Transforming Raw Materials into Precision Molds:
Machining is a critical stage in mold manufacturing, where ACE transforms raw materials into functional molds. The company employs a wide range of machining processes, such as milling, turning, and grinding, to shape and refine the molds. ACE's skilled machinists work with various materials, including metals and plastics, to create molds that can withstand the rigors of production. Through their expertise and attention to detail, ACE ensures the final molds meet the highest standards of quality and performance.
4.1 Meeting Industry Standards
ACE understands the importance of adhering to industry standards when it comes to mold manufacturing. Their molds are constructed to precise DME and Hasco mold standards, ensuring compatibility and interchangeability. Moreover, ACE can provide brand name mold components such as HASCO, DME, PROGRESSIVE, MISUMI, Parker, and many others. This commitment to quality and adherence to recognized standards further enhances the reliability and performance of ACE's molds.
4.2 Efficiency and Capacity
ACE Mold is not only committed to precision and quality but also to efficiency and capacity. With their advanced machinery and streamlined processes, they can achieve an annual output of over 300 sets of plastic production molds, weighing up to 10 tons. Moreover, ACE has the capability to handle 30 sets of molds simultaneously, allowing for increased productivity and reduced lead times. This efficiency and capacity make ACE an ideal partner for companies seeking high-quality molds delivered in a timely manner.
V. Quality Control: Delivering Excellence:
ACE recognizes the importance of rigorous quality control throughout the mold manufacturing process. At every stage, quality checks are performed to verify the accuracy, durability, and functionality of the molds. Advanced measuring equipment, such as coordinate measuring machines (CMM), is utilized to ensure precise dimensional accuracy. Additionally, ACE follows stringent quality management systems to adhere to industry standards and customer requirements, further enhancing its reputation for excellence.
Conclusion:
Mold manufacturing is a complex and intricate process that requires expertise, precision, and continuous innovation. ACE, as a leading manufacturer, exemplifies these qualities in its approach to mold manufacturing. From the initial design phase to the final product, ACE leverages advanced technologies, skilled professionals, and stringent quality control measures to deliver molds that meet the highest standards. By continually refining its processes and embracing new advancements, ACE remains at the forefront of the industry, contributing to the success of numerous businesses across various sectors.