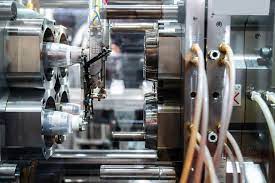
Plastic injection mold tooling is a crucial step in the manufacturing process that determines the quality, cost, and efficiency of plastic part production. The tooling process involves designing and manufacturing the molds used to shape plastic parts. A well-made mold ensures precise, repeatable, and durable products. This guide explains the different types of tooling, materials used, key considerations, and common challenges in plastic injection mold tooling.
What is Plastic Injection Mold Tooling?
Injection mold tooling refers to the process of designing and fabricating the mold used in plastic injection molding. The mold is a precision-engineered tool that shapes molten plastic into a final part. Since the mold directly affects the quality of the finished product, it must be carefully designed to meet the requirements of production.
Tooling is one of the most expensive parts of the injection molding process. The complexity, size, and material of the mold all affect the overall cost and production time. Proper tooling ensures efficiency, reduces production defects, and extends the lifespan of the mold.
Types of Plastic Injection Mold Tooling
Prototype Tooling
Prototype molds are used for testing and refining a part before mass production. These molds are often made from aluminum or soft steel, making them quicker and cheaper to produce. Prototype molds allow manufacturers to make design changes and test different materials before committing to full-scale production.
Production Tooling
Production molds are designed for high-volume manufacturing. These molds are made from durable steel alloys that can withstand repeated use. They are more expensive but provide long-term reliability, making them ideal for mass production.
Soft Tooling vs. Hard Tooling
- Soft tooling refers to molds made from aluminum or softer steels like P20. These molds are used for low-volume production and prototyping. They have a shorter lifespan but lower upfront costs.
- Hard tooling is made from hardened steel and designed for high-volume production. These molds are more durable and provide consistent quality over time but require a higher initial investment.
Single Cavity vs. Multi-Cavity Molds
- Single cavity molds produce one part per cycle. These are used for low-volume production or larger parts that require more material.
- Multi-cavity molds can produce multiple parts in one cycle, increasing efficiency and reducing costs per unit. These molds are ideal for high-volume manufacturing.
Family Molds
Family molds are designed to produce multiple different parts in a single cycle. These molds are useful for products that require several components molded from the same material.
Hot Runner vs. Cold Runner Molds
- Hot runner molds use a heated system to keep the plastic molten as it flows into the mold cavity. This reduces waste and speeds up production but increases mold complexity and cost.
- Cold runner molds allow plastic to cool in the runner system, leading to more waste but a simpler, lower-cost mold design.
Materials Used in Mold Tooling
Aluminum
Aluminum is used for prototype and short-run molds. It is easy to machine and offers quick turnaround times. However, it wears out faster than steel and is not suitable for long-term production.
P20 Steel
P20 steel is a popular choice for mid-volume production molds. It is easier to machine than hardened steel and offers a balance between cost and durability.
Hardened Steel (H13, S136, etc.)
Hardened steel molds are used for high-volume production. These molds last for hundreds of thousands or even millions of cycles. Although expensive to manufacture, they provide excellent durability and precision.
Stainless Steel
Stainless steel molds are corrosion-resistant and used in industries requiring high cleanliness, such as medical and food-grade production. They are more costly but offer long-term performance.
Key Factors in Mold Tooling Design
Mold Life Expectancy
The material and construction of the mold determine its lifespan. Steel molds last longer than aluminum molds and require less maintenance. Choosing the right material depends on production volume and cost considerations.
Cooling System
A well-designed cooling system improves production efficiency and prevents defects. Cooling channels are added to regulate the temperature inside the mold, ensuring uniform cooling and reducing cycle times.
Ejector System
The ejector system helps remove the finished part from the mold. Ejector pins, plates, and air blasts are commonly used to ensure smooth ejection without damaging the part.
Shrinkage Compensation
Plastics shrink as they cool, so molds must be designed to compensate for shrinkage. The shrinkage rate varies depending on the type of plastic used. Proper calculations help maintain accurate part dimensions.
Surface Finish
The surface texture of a mold affects the appearance and functionality of the final product. Polished molds create smooth, glossy parts, while textured molds add grip or aesthetic appeal.
Common Challenges in Injection Mold Tooling
High Initial Costs
Injection mold tooling requires significant upfront investment. However, the cost per part decreases with higher production volumes. Proper design optimization can help reduce tooling expenses.
Long Lead Times
The process of designing and manufacturing a mold can take several weeks or months. Using CNC machining, EDM (electrical discharge machining), and rapid prototyping techniques can speed up production.
Mold Wear and Maintenance
Frequent use causes wear and tear on the mold. Regular maintenance, such as cleaning, lubrication, and inspecting for cracks, extends mold life and prevents production downtime.
Defects and Quality Issues
Poor mold design can lead to defects like warping, flash, short shots, and sink marks. Proper gating, cooling, and venting design help prevent these issues.
How to Choose the Right Mold Tooling Supplier
Experience and Expertise
Choose a tooling supplier with experience in plastic injection molding. A skilled manufacturer can optimize mold design for better performance and cost savings.
Quality Control Measures
A good supplier should have strict quality assurance procedures, including mold testing, material inspection, and dimensional accuracy checks.
Flexibility and Support
Tooling requirements may change, so a flexible supplier who can adjust designs, provide modifications, and offer ongoing support is important.
Cost and Lead Time
Compare pricing and lead times from different suppliers to find a balance between cost and delivery speed. While lower costs are attractive, quality and durability should not be compromised.
Conclusion
Plastic injection mold tooling is a vital part of the manufacturing process, affecting the quality, cost, and efficiency of production. Different types of molds, materials, and design considerations must be carefully evaluated to ensure successful manufacturing. While tooling requires an initial investment, a well-designed mold leads to long-term savings and consistent high-quality parts. Choosing the right materials, designing for efficiency, and working with an experienced supplier can help businesses achieve the best results in plastic injection molding.