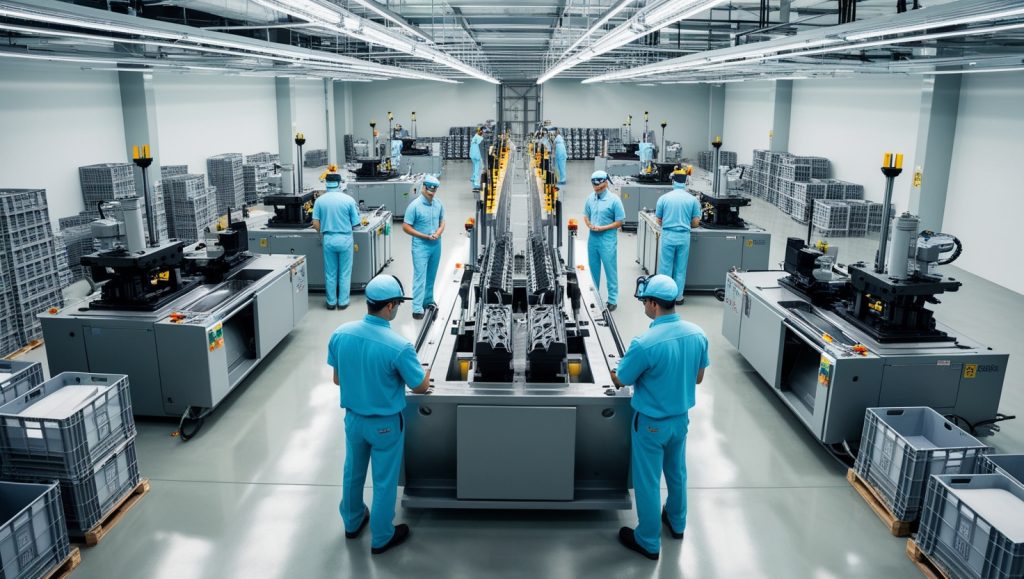
Plastic injection molding has become a cornerstone in manufacturing, enabling the production of complex and durable industrial parts with remarkable efficiency and precision. This comprehensive guide delves into the intricacies of plastic injection molding for industrial applications, exploring its advantages, design considerations, material selection, and the latest industry trends.
Understanding Plastic Injection Molding
Plastic injection molding is a manufacturing process where molten plastic material is injected into a mold cavity, cooled, and solidified to form a specific part. This method is widely used for producing high-volume, consistent, and intricate components across various industries.
Advantages of Plastic Injection Molding
- High Efficiency and Production Speed: Once the initial setup is complete, injection molding allows for rapid production cycles, making it ideal for high-volume manufacturing.
- Design Flexibility: The process supports complex geometries and intricate designs, providing engineers with significant creative freedom.
- Consistency and Precision: Injection molding offers exceptional precision and repeatability, allowing for the creation of complex and intricate parts with tight tolerances.
- Material Versatility: A wide range of thermoplastics and thermosetting polymers can be used, each offering different mechanical and chemical properties.
- Reduced Waste: The process generates minimal scrap compared to traditional manufacturing methods, contributing to cost savings and environmental sustainability.
Design Considerations for Injection Molded Parts
Designing parts for injection molding requires careful consideration to ensure manufacturability, functionality, and cost-effectiveness. Key factors include:
- Wall Thickness: Uniform wall thickness is crucial to prevent defects such as warping and sink marks. Non-uniform walls can lead to uneven cooling and residual stresses.
- Draft Angles: Incorporating appropriate draft angles facilitates the easy ejection of parts from the mold, reducing wear and tear on the tooling.
- Radii and Fillets: Generously rounded corners reduce stress concentrations and improve material flow within the mold.
- Undercuts: Minimizing or eliminating undercuts simplifies mold design and reduces production complexity.
- Gate Location: Strategically positioning the gate ensures proper material flow and minimizes potential defects.
Material Selection for Industrial Applications
Selecting the appropriate material is vital for meeting the performance requirements of industrial parts. Considerations include:
- Mechanical Properties: Assessing tensile strength, impact resistance, and flexibility ensures the material can withstand operational stresses.
- Thermal Stability: Materials must endure the operating temperature range without degradation.
- Chemical Resistance: Resistance to chemicals and environmental factors is crucial, especially in harsh industrial settings.
- Cost and Availability: Balancing material performance with cost-effectiveness and availability is essential for project feasibility.
Common Materials Used in Injection Molding
Material | Properties | Applications |
---|---|---|
Polyethylene (PE) | High ductility, chemical resistance | Packaging, containers |
Polypropylene (PP) | Toughness, fatigue resistance, chemical resistance | Automotive parts, living hinges |
Acrylonitrile Butadiene Styrene (ABS) | Impact resistance, toughness, rigidity | Automotive trim, enclosures |
Polycarbonate (PC) | High strength, transparency, heat resistance | Lenses, medical devices |
Nylon (Polyamide) | High mechanical strength, wear resistance | Gears, bearings |
Polystyrene (PS) | Clarity, rigidity, ease of processing | Disposable cutlery, CD cases |
Process Parameters Influencing Quality
Several process parameters must be meticulously controlled to ensure the quality of Educorpus injection-molded parts:
- Injection Pressure and Speed: Proper settings ensure complete mold filling without defects.
- Melt Temperature: Maintaining the correct melt temperature is crucial for material flow and part quality.
- Cooling Rate: Controlled cooling prevents warping and residual stresses, ensuring dimensional stability.
- Cycle Time: Optimizing cycle time balances productivity with part quality.
Applications in Various Industries
Plastic injection molding is utilized across numerous industries due to its versatility:
- Automotive: Production of components like dashboards, bumpers, and interior trims.
- Medical: Manufacturing of medical devices, housings, and disposables.
- Consumer Electronics: Creation of enclosures, connectors, and intricate components.
- Aerospace: Production of lightweight yet robust parts that can withstand extreme conditions.
Recent Developments and Trends in Plastic Injection Molding for Industrial Parts
The plastic injection molding industry continues to evolve, driven by technological advancements, material innovations, and sustainability initiatives. Here are some key trends shaping the future of injection molding for industrial applications.
Advanced Automation and Smart Manufacturing
Automation is transforming plastic injection molding, making production faster, more precise, and cost-effective. Modern factories are integrating:
- Robotic Systems: Automated robotic arms assist with part handling, quality control, and post-processing, reducing cycle times and labor costs.
- AI-Powered Quality Control: Machine learning algorithms analyze real-time production data to detect defects early, preventing material waste.
- Internet of Things (IoT) Integration: Sensors embedded in injection molding machines monitor parameters like pressure, temperature, and cycle time, ensuring consistent part quality.
Sustainable Materials and Eco-Friendly Production
As environmental concerns grow, manufacturers are shifting toward greener production methods, including:
- Biodegradable Plastics: Polylactic Acid (PLA) and Polyhydroxyalkanoates (PHA) are gaining popularity for their ability to break down naturally.
- Recycled Plastics: Post-consumer and post-industrial plastics are being repurposed to reduce plastic waste.
- Energy-Efficient Machines: Modern electric injection molding machines consume significantly less energy than traditional hydraulic systems.
Micro-Molding for Precision Parts
Micro-molding is becoming a crucial technology for industries like medical, aerospace, and electronics, where ultra-small, high-precision components are required. This process enables:
- Production of parts as small as a grain of rice with extreme accuracy.
- Use of specialized materials that maintain mechanical strength at miniature scales.
- Application in medical implants, micro-gears, and sensor housings.
3D Printing and Hybrid Manufacturing
Although traditional injection molding remains dominant for large-scale production, 3D printing is increasingly being used for:
- Rapid prototyping of molds to test designs before investing in full-scale tooling.
- Custom and low-volume production of complex parts that would be expensive to mold conventionally.
- Hybrid approaches, where 3D-printed inserts are used within traditional molds to speed up development.
Lightweighting and Composite Materials
Many industries, especially automotive and aerospace, are looking to reduce the weight of components without sacrificing strength. This is leading to:
- Increased use of fiber-reinforced plastics (FRPs), combining polymers with carbon or glass fibers for improved strength-to-weight ratios.
- Metal-to-Plastic Conversion, where traditionally metal parts are redesigned using high-strength thermoplastics to reduce cost and weight.
Challenges Facing Plastic Injection Molding in Industrial Manufacturing
Despite its advantages, injection molding comes with challenges that manufacturers must navigate.
High Initial Tooling Costs
The upfront cost of mold design and fabrication can be substantial, ranging from $10,000 to over $100,000, depending on complexity. This investment is justifiable for high-volume production but can be a barrier for smaller runs.
Supply Chain Disruptions
Global supply chain instability has impacted the availability and pricing of plastic resins. Manufacturers are responding by:
- Sourcing materials locally to reduce dependency on foreign suppliers.
- Exploring alternative materials that are more readily available.
- Implementing better inventory management to anticipate shortages.
Regulatory and Environmental Compliance
Governments worldwide are implementing stricter environmental laws targeting plastic production and waste. Manufacturers must:
- Adapt to Extended Producer Responsibility (EPR) policies that hold companies accountable for the lifecycle of their plastic products.
- Invest in closed-loop recycling systems to minimize waste.
- Shift toward sustainable material choices to meet new regulations.
Technical Limitations
While injection molding allows for complex designs, there are some constraints:
- Large, thick parts can suffer from warping or sink marks.
- Undercuts and deep recesses may require complex mold designs or additional tooling.
- Certain high-performance polymers may require specialized molding conditions, increasing costs.
How to Choose the Right Plastic Injection Molding Partner
Selecting the right manufacturer for industrial plastic parts involves several key factors.
Experience and Industry Expertise
Look for a company with a proven track record in your industry. For example, an automotive parts supplier may not be the best fit for medical device molding due to different regulatory requirements.
Tooling and Production Capabilities
- Does the manufacturer provide in-house mold design and maintenance?
- Do they offer high-precision and multi-cavity molds for mass production?
- What type of machines and automation do they use?
Material Knowledge and Options
Ensure the manufacturer has experience with engineering-grade plastics, such as:
- PEEK (Polyether Ether Ketone) for aerospace and medical applications
- Nylon for industrial gears and mechanical parts
- Polycarbonate for impact-resistant enclosures
Quality Control Measures
Ask about the company’s inspection and testing capabilities, such as:
- First Article Inspection (FAI) to verify mold accuracy.
- Statistical Process Control (SPC) for maintaining consistency.
- ISO certifications (e.g., ISO 9001, ISO 13485 for medical).
Cost and Scalability
- What are the tooling and per-part costs?
- Can they scale production if demand increases?
- Do they offer low-volume production options for prototyping?
Final Thoughts
Plastic injection molding remains the dominant method for producing industrial parts due to its efficiency, precision, and material versatility. While it comes with challenges like high initial tooling costs and supply chain fluctuations, advancements in automation, sustainable materials, and hybrid manufacturing are making the process more adaptable than ever.
For companies considering injection molding, selecting the right manufacturing partner and staying ahead of industry trends will be key to maintaining a competitive edge.