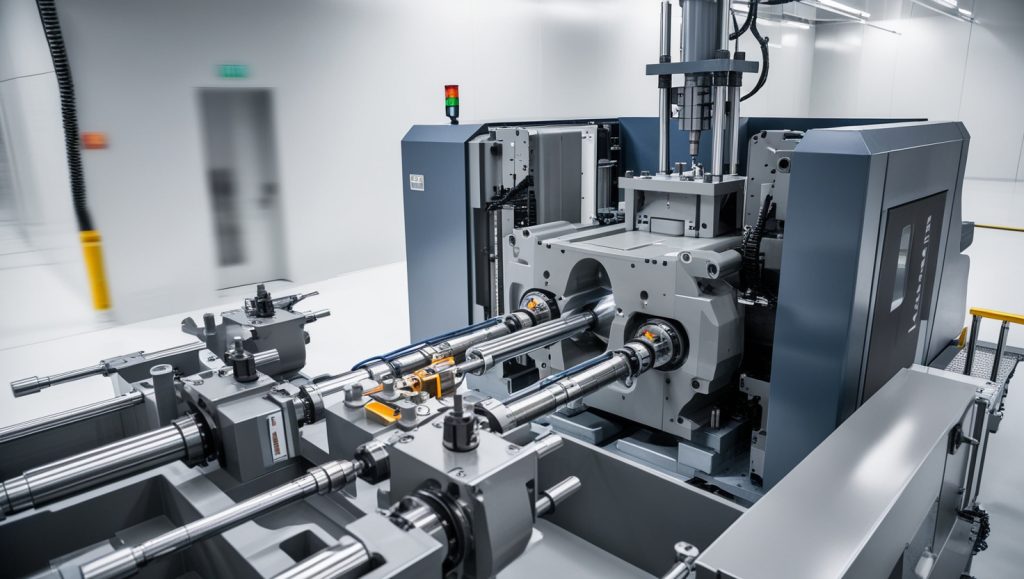
Plastic injection molding is one of the most widely used manufacturing processes for producing plastic components. When it comes to large parts, the process becomes more complex, requiring specialized techniques, equipment, and materials. This guide will explore the challenges of molding large plastic parts, strategies to overcome these issues, and real-world applications where large-scale injection molding is essential. Additionally, we will delve deeper into innovative solutions, industry trends, and future advancements that are shaping this critical manufacturing sector.
Understanding Plastic Injection Molding for Large Parts
Injection molding works by injecting molten plastic into a mold cavity, where it cools and solidifies into a specific shape. For large plastic parts, this process requires extra considerations to maintain structural integrity, dimensional accuracy, and consistent material flow. Achieving a defect-free part while maintaining production efficiency demands optimized design, advanced materials, and precision engineering.
Key Characteristics of Large Part Injection Molding:
- Higher Material Volume – Requires large shot sizes to fill the mold.
- Increased Cooling Time – Larger parts require longer cooling cycles.
- Stronger Clamping Force – Needed to keep the mold closed under high pressure.
- Complex Mold Design – To ensure even material distribution and minimal defects.
- Reinforced Structural Components – Necessary to maintain durability under stress.
- Specialized Injection Molding Machines – Larger platen sizes and higher tonnage capacity.
Challenges in Molding Large Parts
Manufacturing large plastic components introduces unique challenges compared to standard injection molding. Below are the most significant issues:
Material Flow and Fill Challenges
Larger molds require consistent material flow to prevent defects such as short shots, sink marks, and weld lines. The risk of uneven flow increases with larger distances, which can lead to variations in part strength and appearance. Proper material selection and injection speed adjustments play a critical role in mitigating these issues.
Additionally, shear heating and cooling rate inconsistencies in large molds can result in incomplete filling or air entrapment, leading to part failures. Flow analysis software can help manufacturers simulate the injection process, allowing them to make adjustments before committing to production.
Cooling and Warpage Issues
- Large parts require longer cooling times, increasing cycle durations.
- Uneven cooling may lead to warping and residual stresses, affecting part quality.
- Advanced cooling techniques, such as conformal cooling channels, can help maintain uniform temperature distribution.
- Mold temperature controllers are often required to balance cooling rates, reducing cycle time without compromising part integrity.
Mold cooling is one of the most influential factors in determining production efficiency. Poorly designed cooling systems can extend cycle times by several minutes, significantly impacting manufacturing costs.
High Clamping Force Requirements
Larger parts require higher clamping force to prevent the mold from opening under pressure. This often means using large-tonnage injection molding machines, typically 1,000 to 3,000 tons of clamping force. Some ultra-large components, such as those found in automotive and aerospace applications, may require machines exceeding 4,000 tons.
Mold and Equipment Limitations
Standard injection molding machines may not accommodate large molds. Specialized machines with larger platens, extended injection units, and high-tonnage capabilities are necessary to handle bigger mold dimensions and shot sizes. Two-shot and gas-assisted injection molding are sometimes employed to optimize material distribution.
Injection Pressure and Melt Density
- Larger parts require higher injection pressure to fill the mold properly.
- Poor pressure management can lead to inconsistent part density and internal voids.
- Using gas-assisted injection molding can help optimize material distribution.
- Multi-gate injection can prevent weld line formation and promote even material distribution.
Cycle Time and Productivity
- Extended cycle times for injection, cooling, and ejection can reduce production efficiency.
- Manufacturers must balance quality with speed by fine-tuning mold temperature control and material selection.
- High-output injection molding machines with servo-driven pumps improve cycle efficiency and reduce energy consumption.
Strategies to Overcome Challenges
To achieve high-quality large plastic parts, manufacturers must implement key solutions:
Optimized Mold Design
- Uniform wall thickness reduces the risk of sink marks and warping.
- Proper rib placement enhances structural integrity without adding excess weight.
- Conformal cooling channels provide better heat dissipation, reducing cycle time.
- Mold surface coatings and texturing techniques help improve material flow and part release.
- Employing advanced ejection mechanisms such as air-assisted or robotic systems reduces defects and improves production rates.
Material Selection
Choosing the right plastic material is crucial for strength, flexibility, and processability. Popular materials for large injection-molded parts include:
Material Type | Characteristics | Common Applications |
---|---|---|
Polypropylene (PP) | Lightweight, chemical-resistant | Automotive, consumer goods |
Acrylonitrile Butadiene Styrene (ABS) | Impact-resistant, rigid | Electronics, enclosures |
Polycarbonate (PC) | High strength, optical clarity | Medical, aerospace |
Nylon (PA) | High durability, heat-resistant | Industrial parts, gears |
High-Density Polyethylene (HDPE) | Tough, moisture-resistant | Industrial, outdoor uses |
Advanced Process Simulation
Using mold flow analysis software helps manufacturers predict and correct:
- Potential fill issues
- Cooling inconsistencies
- Pressure variations
- Stress accumulation and potential weak points
- Fiber orientation in reinforced plastics
Specialized Injection Molding Machines
For large parts, high-tonnage injection molding machines are used. Features include:
- Multi-cavity molds to increase productivity.
- Gas-assisted injection molding for reduced material usage and weight.
- Low-pressure molding to minimize stress on delicate sections.
- Hybrid electric/hydraulic machines for improved precision and energy savings.
Real-World Applications of Large Part Injection Molding
Automotive Industry
Large plastic components in automobiles and heavy equipment include:
- Bumpers and dashboards
- Interior panels and trim
- Under-hood components
- Truck bed liners
- Large air ducts and cooling system components
Medical Equipment
- Housings for diagnostic machines
- Sterilizable trays and equipment cases
- MRI and CT scan machine covers
- Durable prosthetic components
Consumer Goods
- Large storage containers and bins
- Plastic furniture (chairs, tables, shelving)
- Recreational equipment (kayaks, coolers)
- Children’s play structures and ride-on toys
Industrial and Construction
- Plastic pallets and crates
- Machine guards and enclosures
- Piping components and tanks
- Heavy-duty electrical enclosures
Future Trends in Large-Scale Injection Molding
Automation and Robotics
- Automated part removal and inspection
- Collaborative robots (cobots) assisting in post-processing
- AI-driven quality control and defect detection
Sustainable Materials
- Use of biodegradable plastics and recycled resins
- Lightweighting strategies to reduce raw material consumption
- Carbon fiber-reinforced plastics for enhanced strength with reduced weight
3D Printing for Mold Making
- Rapid prototyping of molds before mass production
- Hybrid manufacturing combining 3D printing and injection molding
- Tool-less production for low-volume, customized parts
Conclusion
Plastic injection molding for large parts presents unique challenges, from material flow and cooling to clamping force and cycle time. However, by implementing optimized mold design, advanced materials, and process simulations, manufacturers can produce high-quality, durable plastic components for automotive, medical, and industrial applications. The industry continues to evolve with advancements in automation, sustainability, and hybrid manufacturing techniques, ensuring that large-scale injection molding remains a dominant force in modern production.