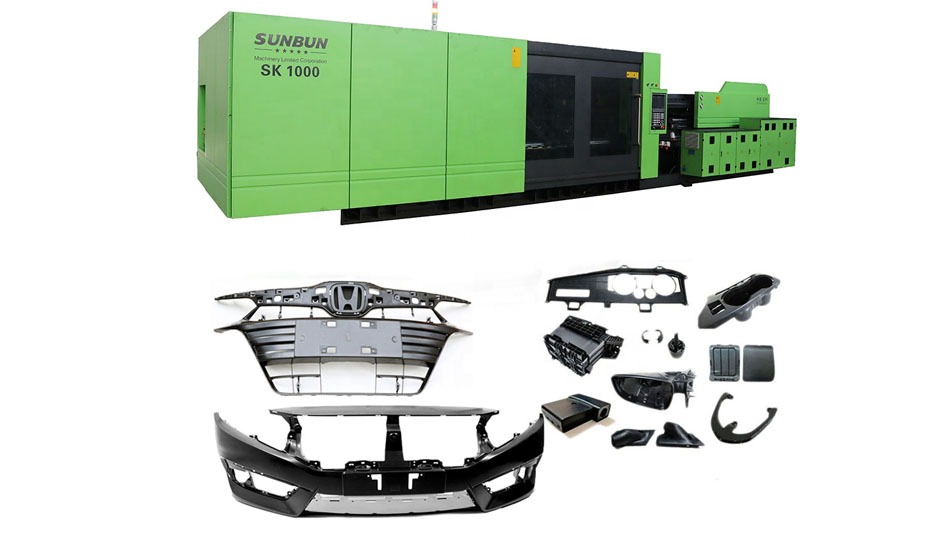
Plastic injection molding machine spare parts are replacement parts for use in plastic injection molding machines. These spare parts are used to replace worn or damaged parts in the machine to ensure that it continues to operate correctly and efficiently. Some examples of spare parts for plastic injection molding machines include:
- Screws and barrels: These are the parts that melt the plastic and inject it into the mold. They can wear out over time and need to be replaced.
- Nozzles: These are the parts that control the flow of melted plastic into the mold. They can become clogged or damaged and need to be replaced.
- Heaters and thermocouples: These are the parts that heat the plastic to its melting point. They can wear out or malfunction and need to be replaced.
- Hydraulic and pneumatic components: These are the parts that power the movement of the machine's various components. They can wear out or malfunction and need to be replaced.
- Control systems and electrical components: These are the parts that control the machine's operation and can wear out or malfunction and need to be replaced.
- Moulds: The moulds are the parts that give shape to the final product, they can wear out or malfunction and need to be replaced.
Plastic injection moulding is an important process used to manufacture plastic products. It involves the process of heating and then injecting molten plastic into a mould, which is then cooled and solidified. Plastic injection moulding machines are an important part of the plastic injection moulding process. They are responsible for ensuring the efficient, reliable, and cost-effective production of quality plastic products. To ensure that the plastic injection moulding process is successful, it is important to have the right spare parts for the plastic injection moulding machine. In this blog article, we will discuss the essential spare parts for plastic injection moulding machines, the types of spare parts available, how to identify the essential spare parts, and how to maintain them.
Introduction to Plastic Injection Moulding
Plastic injection moulding is a process used to manufacture plastic products. It involves the injection of molten plastic into a mould, which is then cooled and solidified. The injection moulding machine is the most important part of the process, as it is responsible for controlling the temperature, pressure, and speed of the moulding process. Plastic injection moulding machines are designed to be precise, efficient, and cost-effective. They are used in a variety of industries, including automotive, medical, aerospace, and consumer products.
The plastic injection moulding process is typically divided into three steps: injection, cooling, and ejection. In the injection step, molten plastic is injected into the mould. In the cooling step, the mould is cooled to allow the plastic to solidify. In the ejection step, the mould is opened and the plastic product is ejected.
The injection moulding machine is an essential part of the process, as it is responsible for controlling the temperature, pressure, and speed of the moulding process. The machine consists of a hopper, where the plastic is stored, a heating system, which heats the plastic, and a plunger, which injects the molten plastic into the mould.
Benefits of Using Plastic Injection Moulding
Plastic injection moulding is a cost-effective way to manufacture plastic products. It is fast and efficient, and can produce high-quality products in large quantities. It also allows for the production of complex designs, which are not possible with other manufacturing processes. Additionally, it is highly customizable, allowing for the production of products in a variety of shapes, sizes, and colours.
In addition to being cost-effective and efficient, plastic injection moulding is also a safe process. The plastic is heated to a precise temperature, and the pressure is carefully controlled to ensure the safety of the operator. Furthermore, plastic injection moulding is environmentally friendly, as it produces minimal waste and uses recycled materials.
Types of Spare Parts for Plastic Injection Moulding Machines
In order to ensure the efficient and cost-effective production of quality plastic products, it is important to have the right spare parts for the plastic injection moulding machine. There are several types of spare parts available for plastic injection moulding machines, including:
- Heating components: These include heating elements, temperature controllers, and thermocouples.
- Hydraulic components: These include pumps, valves, and filters.
- Mechanical components: These include bearings, gears, and screws.
- Electrical components: These include switches, relays, and motors.
- Pneumatic components: These include cylinders, solenoid valves, and air compressors.
How to Identify the Essential Spare Parts for Plastic Injection Moulding
In order to identify the essential spare parts for plastic injection moulding, it is important to consider the type of plastic product being manufactured. Different products require different types of spare parts, and some may require more than others. Additionally, it is important to consider the type of machine being used, as some machines require specific types of spare parts. It is also important to consider the environment in which the machine is being used, as some parts may be more suitable for certain environments than others.
Once the necessary spare parts have been identified, it is important to purchase quality parts that are designed to last. It is also important to purchase parts that are compatible with the machine, as some parts may not be compatible with certain machines. Additionally, it is important to purchase parts that are designed for the specific type of plastic being used, as some parts may not be suitable for certain types of plastics.
The Most Commonly Used Spare Parts for Plastic Injection Moulding Machines
The most commonly used spare parts for plastic injection moulding machines are heating components, hydraulic components, mechanical components, electrical components, and pneumatic components.
Heating components are essential for controlling the temperature of the molten plastic, and include heating elements, temperature controllers, and thermocouples. Hydraulic components are used to control the pressure of the injection process, and include pumps, valves, and filters. Mechanical components are used to move the parts of the machine, and include bearings, gears, and screws. Electrical components are used to control the operation of the machine, and include switches, relays, and motors. Pneumatic components are used to control the flow of air, and include cylinders, solenoid valves, and air compressors.
Tips for Choosing the Right Spare Parts for Plastic Injection Moulding
When choosing spare parts for plastic injection moulding, it is important to purchase parts that are compatible with the machine, and designed for the specific type of plastic being used. Additionally, it is important to purchase quality parts that are designed to last. It is also important to consider the environment in which the machine is being used, as some parts may not be suitable for certain environments.
When purchasing spare parts for plastic injection moulding, it is also important to purchase parts from a reputable supplier. It is important to ensure that the supplier has a good reputation, and is willing to provide technical support and advice if needed. Additionally, it is important to purchase parts that are covered by a warranty, as this will provide peace of mind in the event of any issues.
How to Maintain the Spare Parts for Plastic Injection Moulding
In order to ensure the efficient and cost-effective production of quality plastic products, it is important to maintain the spare parts for plastic injection moulding. Regular maintenance of the spare parts will ensure that they are in good working condition, and can help to reduce the risk of any issues.
It is important to clean the spare parts regularly, as this will help to prevent any build-up of dirt or dust. Additionally, it is important to check the spare parts for any signs of wear and tear, and to replace any parts that are damaged or worn. It is also important to lubricate the parts regularly, as this will help to ensure that they are in good working condition.
Benefits of Using the Right Spare Parts for Plastic Injection Moulding
Using the right spare parts for plastic injection moulding can help to ensure the efficient and cost-effective production of quality plastic products. The right spare parts can help to improve the performance of the machine, and reduce the risk of any issues. Additionally, using the right parts can help to extend the life of the machine, and reduce the cost of maintenance and repairs.
Conclusion
In conclusion, it is essential to have the right spare parts for plastic injection moulding machines in order to ensure the efficient and cost-effective production of quality plastic products. There are several types of spare parts available, and it is important to identify the essential spare parts for the specific type of plastic product being manufactured. Additionally, it is important to purchase quality parts that are designed to last, and to maintain them regularly. By using the right spare parts for plastic injection moulding, it is possible to benefit from improved performance, extended life, and reduced maintenance and repair costs.