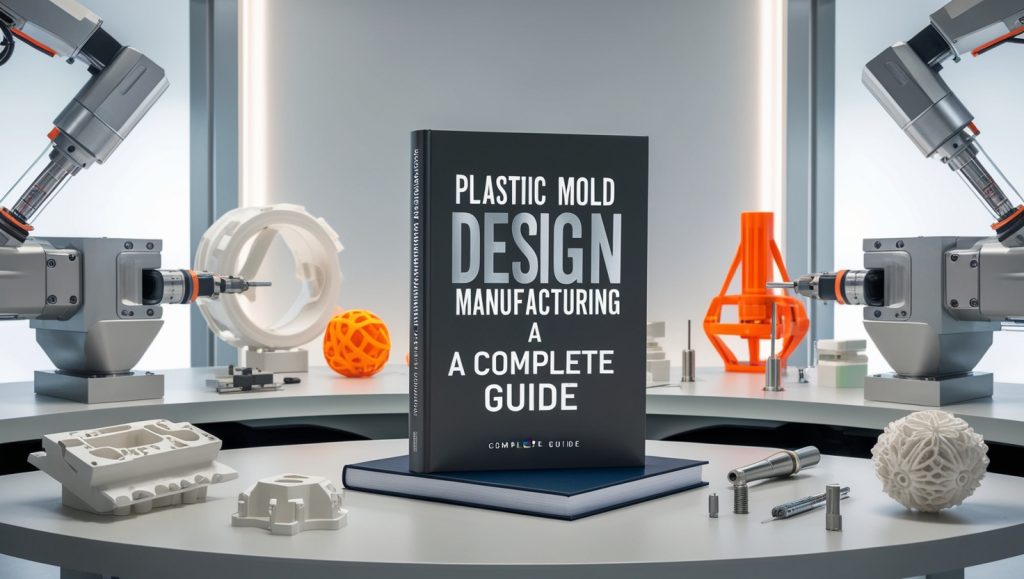
Plastic mold design and manufacturing are critical processes in modern manufacturing, enabling the mass production of plastic parts with precision and efficiency. From automotive components to medical devices, plastic molds are essential for creating consistent and durable products.
Why is mold design so important? A well-designed mold ensures smooth production, minimizes material waste, and reduces defects. With advancements in technology, mold design has become more sophisticated, incorporating computer-aided design (CAD), automation, and high-precision machining.
In this guide, we’ll explore everything you need to know about plastic mold design and manufacturing, from the basics to cutting-edge innovations shaping the industry.
What is Plastic Mold Design?
Plastic mold design refers to the process of creating the blueprint for molds used in plastic manufacturing. These molds define the shape, structure, and quality of the final plastic product.
Key Factors in Mold Design
- Product Geometry: The complexity of the final plastic part determines mold structure.
- Material Selection: Different plastics behave differently during molding.
- Cooling System Design: Affects cycle time and part quality.
- Durability: High-quality molds must withstand repeated use.
A well-designed mold optimizes production efficiency, reduces waste, and improves part consistency.
Types of Plastic Molds
Different manufacturing processes require different types of molds.
1. Injection Molds
- Used in plastic injection molding.
- Creates highly detailed parts with tight tolerances.
2. Blow Molds
- Used for making hollow plastic objects like bottles.
- Relies on air pressure to shape the plastic.
3. Compression Molds
- Used in thermoset molding processes.
- Plastic material is placed in the mold and compressed into shape.
4. Transfer Molds
- Used for complex thermoset plastic parts.
- Material is preheated and transferred into a closed mold.
Materials Used in Plastic Mold Design
Selecting the right material for a mold impacts its durability, cost, and performance.
Common Metals Used in Molds
- Steel (P20, H13, S136): High durability, best for long-term production.
- Aluminum: Lightweight, good for prototype and low-volume production.
- Beryllium Copper: Excellent for high-heat dissipation, used in inserts.
Surface Treatments and Coatings
- Nickel Plating: Prevents corrosion.
- Titanium Coating: Increases hardness.
- Teflon Coating: Reduces friction and wear.
The Mold Design Process
Creating a plastic mold involves several steps to ensure efficiency and accuracy.
Initial Concept and CAD Modeling
- Designers use software like SolidWorks and AutoCAD to create 3D models.
- The design must accommodate material shrinkage and flow behavior.
Mold Flow Analysis and Prototyping
- Simulations predict plastic flow and identify potential defects.
- Prototypes allow testing before full-scale production.
Finalizing the Mold Design for Production
- Adjustments are made based on prototype testing.
- The design is optimized for durability and cost-effectiveness.
Key Components of a Plastic Mold
A plastic mold consists of several essential components:
Core and Cavity
- The core creates the internal structure of the part.
- The cavity forms the external shape.
Runner System
- Hot Runner: Keeps plastic molten, reducing waste.
- Cold Runner: Solidifies excess plastic, increasing material waste.
Cooling Channels
- Ensures uniform cooling to prevent defects like warping.
Ejector System
- Helps remove the final molded part from the mold cavity.
Factors Affecting Mold Design
Designing a high-quality plastic mold involves several key considerations to ensure efficiency, durability, and product quality.
Part Geometry and Complexity
- The more complex a plastic part, the more intricate the mold must be.
- Features like undercuts, thin walls, and complex shapes require advanced mold components such as slides, lifters, or inserts.
Material Shrinkage and Flow Properties
- Different plastics shrink at different rates when cooled, affecting final part dimensions.
- Mold designers must compensate for shrinkage by adjusting mold dimensions accordingly.
Production Volume and Mold Longevity
- High-volume production molds are made of hardened steel for durability.
- Low-volume production molds may use aluminum or soft steel for cost savings.
By considering these factors, manufacturers can ensure efficient mold performance and consistent product quality.
Once a mold design is finalized, the actual manufacturing process begins. It involves several precise machining techniques to ensure the mold is accurately created.
CNC Machining
- Computer-controlled machining cuts mold components from raw metal blocks.
- Ensures high precision and repeatability.
Electrical Discharge Machining (EDM)
- Used to create intricate details and sharp edges in molds.
- Ideal for complex part geometries.
Mold Assembly and Finishing
- Individual mold components are assembled and polished for smooth operation.
- Surface textures may be applied for aesthetic or functional purposes.
Mold Testing and Validation
- Trial runs are conducted to check mold accuracy and part quality.
- Any defects are corrected before full-scale production begins.
Challenges in Plastic Mold Design and Manufacturing
While plastic mold manufacturing is highly efficient, it does come with some challenges.
Common Defects and Solutions
- Warping: Caused by uneven cooling—resolved by optimizing cooling channels.
- Sink Marks: Occur when material shrinks excessively—solved with proper injection pressure and cooling time.
- Flashing: Excess plastic on part edges—fixed by improving mold clamping force.
Cost vs. Quality Trade-Offs
- Higher-quality molds cost more upfront but last longer.
- Lower-cost molds may wear out faster and require frequent maintenance.
Maintenance and Lifespan Considerations
- Regular cleaning and lubrication prevent mold wear.
- Preventive maintenance ensures consistent production quality.
Innovations in Plastic Mold Manufacturing
Recent technological advancements have improved the efficiency and sustainability of plastic mold manufacturing.
3D Printing for Rapid Prototyping
- Allows for faster mold development and testing.
- Reduces cost and time for design iterations.
AI and Automation in Mold Making
- AI-powered software optimizes mold design for better efficiency.
- Automated machining and inspection reduce human error.
Sustainable Mold Materials and Eco-Friendly Practices
- Recyclable mold materials are being explored for sustainability.
- Energy-efficient mold heating and cooling systems reduce carbon footprint.
Cost Considerations in Mold Design and Manufacturing
Mold manufacturing costs vary based on several factors.
Factors Affecting Cost
- Material Selection: Steel molds cost more but last longer, while aluminum molds are cheaper but wear out faster.
- Complexity: More intricate mold designs require advanced machining, increasing costs.
- Production Volume: High-volume molds justify higher investment due to long-term savings.
Strategies for Cost Reduction
- Using modular mold designs to create multiple part variations.
- Conducting thorough mold flow analysis to reduce trial-and-error costs.
- Outsourcing mold production to specialized manufacturers for cost efficiency.
- While expensive upfront, high-quality molds save costs in long-term production.
- Minimized defects and longer mold lifespan result in better profitability.
Choosing the Right Mold Manufacturer
Selecting the right mold supplier is critical to achieving high-quality production.
Key Considerations When Selecting a Supplier
- Experience in mold making and track record of successful projects.
- Availability of advanced machining equipment and technology.
- Ability to meet specific industry requirements and tolerances.
Industry Standards and Certifications
- ISO 9001: Ensures quality management in manufacturing.
- ISO 13485: Required for medical-grade plastic molding.
- IATF 16949: Standard for automotive plastic mold manufacturing.
Case Studies of Successful Mold Designs
- Leading manufacturers use precision molds for industries like automotive, aerospace, and consumer electronics.
Maintenance and Care of Plastic Molds
Proper mold maintenance extends lifespan and ensures consistent quality.
Routine Cleaning and Inspection
- Molds must be cleaned regularly to prevent residue buildup.
- Inspection identifies early signs of wear or damage.
Preventive Maintenance Practices
- Lubrication of moving parts prevents friction-related wear.
- Scheduled downtime for maintenance reduces unexpected failures.
Repairing Common Mold Wear and Tear
- Polishing worn-out surfaces restores mold accuracy.
- Damaged ejector pins or cooling channels can be replaced.
Applications of Plastic Mold Design in Different Industries
Plastic mold design plays a crucial role in various industries.
Automotive Components
- Used to produce dashboards, bumpers, and engine components.
- Requires high precision and durability.
Medical Devices
- Molds for syringes, surgical tools, and diagnostic equipment.
- Must meet strict regulatory and hygiene standards.
Consumer Goods and Packaging
- Used for making plastic containers, household items, and electronic casings.
- Allows for creative and functional product designs.
Future Trends in Plastic Mold Design and Manufacturing
The future of mold design and manufacturing is shaped by technological advancements and sustainability efforts.
Advanced Materials and Smart Molds
- High-performance alloys and coatings extend mold life.
- Smart molds with built-in sensors monitor production quality.
Integration of IoT for Real-Time Mold Monitoring
- IoT-enabled molds provide real-time data on temperature, pressure, and cycle time.
- Improves efficiency and reduces downtime.
Future Outlook for Plastic Mold Technology
- AI-driven design optimization will reduce trial-and-error in mold making.
- Increased focus on recyclable and biodegradable plastics.
Conclusion
Plastic mold design and manufacturing are essential for producing high-quality plastic parts across industries. While the process involves complex considerations like material selection, mold design, and manufacturing precision, advancements in technology continue to enhance efficiency and sustainability.
Investing in high-quality molds may have higher upfront costs, but the long-term benefits—such as durability, precision, and reduced defects—make it a worthwhile investment. With the rise of AI, automation, and IoT integration, the future of mold design and manufacturing is set for even greater efficiency and innovation.
FAQs
1. What software is used for plastic mold design?
Popular software includes SolidWorks, AutoCAD, CATIA, and Moldflow for mold simulation.
2. How long does it take to manufacture a plastic mold?
It depends on complexity but typically takes 4 to 12 weeks.
3. What is the lifespan of a plastic injection mold?
High-quality steel molds can last for millions of cycles with proper maintenance.
4. How can defects in mold design be prevented?
By conducting mold flow analysis, optimizing cooling channels, and using high-quality materials.
5. What are the most cost-effective materials for mold manufacturing?
Aluminum is cost-effective for prototyping, while hardened steel is best for high-volume production.