What does mean by plastic mould?
A tool or piece of machinery called a plastic mould is employed to produce plastic goods. A hollowed-out cavity is employed to mould molten plastic material, which is subsequently cooled and solidified to create a final plastic product. This mould is made by first designing the mould, choosing the right material, and then utilizing specialized tools to make the mould. They are commonly utilized in manufacturing because they provide a practical and economical means of mass-producing plastic goods with dependability and accuracy. Due to their adaptability and affordability, plastic moulds are a preferred option among producers. Plastic moulds offer a vast range of design possibilities that may be used to develop inventive and one-of-a-kind products. They can produce intricate parts, prototypes, and products quickly and efficiently. They have many benefits over traditional manufacturing methods, such as lower costs, more precision, greater complexity, and shorter lead times.
How Plastic Moulds Revolutionized Manufacturing?
In many ways, these moulds have revolutionized the manufacturing sector. They have enhanced product quality, provided more design flexibility, increased productivity, decreased prices, and positively affected the environment. Plastic moulds are anticipated to play a significant part in the manufacturing sector for many years as technology develops. These moulds are a crucial component of the production process, transforming the sector in numerous ways. Here are some significant effects of these moulds on manufacturing:
- Higher Efficiency:
The efficiency of the manufacturing process has been greatly boosted thanks to the usage of plastic mould. The process of making this mould can be automated, making it possible to complete it quickly and accurately. Efficiency is further increased by producing plastic products on a wide scale after the mould has been made.
- Economical production:
Manufacturing is becoming more affordable thanks to these moulds. A mould can be costly at first, but after it is made, it can be used numerous times to make different plastic objects. As a result, each product has a lower cost per unit than it would have if it had been produced differently.
- A higher standard of product:
Moulds made of plastic are also essential for assuring the excellent quality of plastic items. The goods made using the moulds are constant in size and shape because the moulds are made to exact specifications. Many items, especially those that require a high degree of precision, such as medical devices or automobile parts, depend on this constancy.
- Conceptional Flexibility:
More design freedom is also made possible via these moulds. Manufacturers can build goods that specifically address their client's needs because of the versatility of moulds, which may be made in almost any shape or size. Furthermore, moulds are simple to alter, allowing producers to change product designs quickly.
- Protects the environment:
The ecology has benefitted from the use of these moulds. Utilizing moulds reduces waste generation while manufacturing plastic products compared to alternative techniques. Moulding also enables the production of light products, which can save shipping costs and transportation-related carbon emissions.
What are the benefits of Using Plastic Moulds?
These moulds are a crucial component of the production process and provide many advantages. The following are a few of the main advantages of using plastic moulds in manufacturing:
- Cost-Effective Production:
Making plastic goods at a reasonable price is one of the main advantages of using moulds in manufacturing. A mould can initially be expensive, but after it is made, it can be used repeatedly to produce various plastic goods. As a result, each product has a lower cost per unit than it would have if it had been produced differently. Moulds can also produce lightweight goods, which helps lower shipping costs and transportation-related carbon emissions.
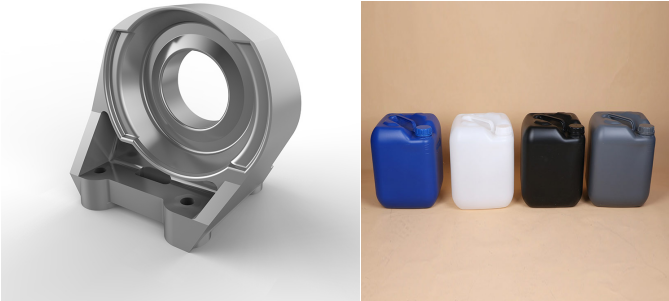
- Product Quality Improvement:
Utilizing plastic moulds also enhances product quality, which is a benefit. Because these moulds are made to exact specifications, the goods made with them are uniform in size and shape. This consistency is crucial for many products, especially those that need a high degree of precision, like medical devices or automotive parts. In addition to ensuring that the goods are free of flaws, using plastic mould lowers the requirement for rework and raises the general level of product quality.
- Design Flexibility:
Moulds made of plastic also provide designers with more design freedom. Moulds can be made in almost any shape or size, allowing producers to produce goods tailored to their client's requirements. Additionally, moulds are simple to alter, allowing producers to change the designs of their products quickly. This adaptability is crucial in consumer electronics, where product designs change frequently.
- Longevity and Robustness:
Moulds made of plastic are renowned for being strong and long-lasting. Moulds may be used repeatedly with little to no wear and tear since they are made to resist the high temperatures and pressures needed to mould plastic items. These moulds are a worthwhile investment for producers due to their strength and lifespan because they may be used for many years before needing to be replaced.
- Labour Costs Are Lower:
Additionally, producers' labour expenses are decreased through the usage of plastic moulds. Mould-based plastic product production can be automated, requiring less human involvement than other techniques. The production process becomes faster and more efficient thanks to this automation, lessening the demand for physical labour.
Conclusion:
An inventive new method called plastic mould has completely changed the manufacturing sector. It makes producing intricate parts and forms more accurately, swiftly, and affordably possible. The ACE mission statement states, To provide our customers with the highest quality moulds and exceptional service at the quickest possible delivery time and best pricing. ACE consistently give 100% of our attention to carefully examining the customer's project and selecting the best approach to design and manufacture the moulds to ensure that all the products produced in our shop may finally help our clients obtain maximum profits and market share.