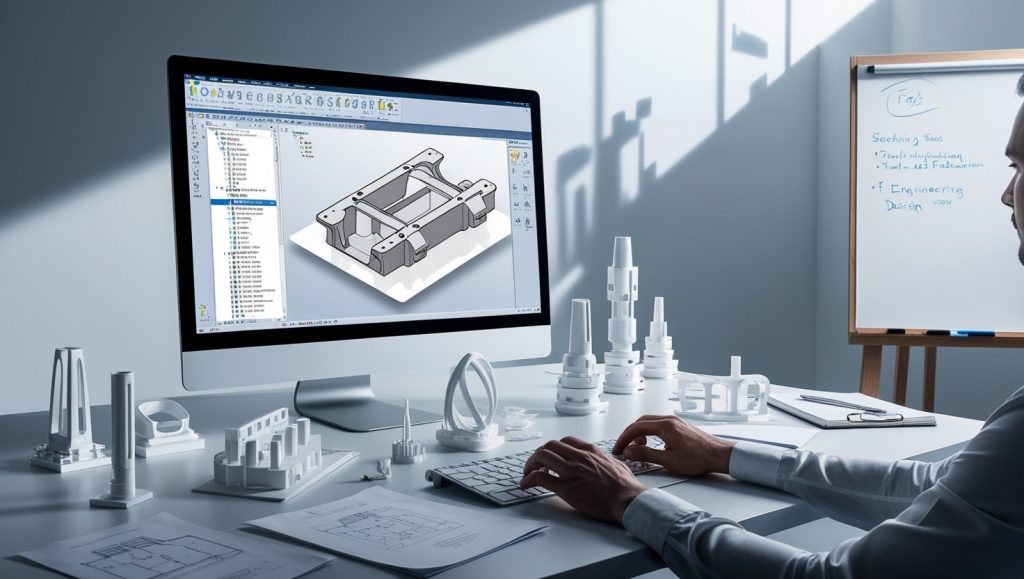
Plastic tooling plays a critical role in modern manufacturing, enabling the mass production of high-quality plastic components with precision and efficiency. Whether for automotive parts, medical devices, or consumer electronics, plastic tooling ensures consistency and durability in production. This article explores the design and fabrication of plastic tooling, covering materials, processes, challenges, and future trends.
Understanding Plastic Tooling
Plastic tooling refers to the specialized molds and dies used to shape plastic materials into desired forms. These tools are essential in manufacturing processes like injection molding, blow molding, and thermoforming. Industries such as automotive, aerospace, medical, and packaging heavily rely on plastic tooling for producing components with tight tolerances and complex geometries.
Types of Plastic Tooling
Injection Molding Tooling
Injection molds are the most common type, used to produce complex plastic parts by injecting molten plastic into a mold cavity. This process allows for high precision and repeatability.
Blow Molding Tooling
Blow molds are designed for hollow plastic products such as bottles and containers. This method involves inflating molten plastic inside a mold to achieve the desired shape.
Thermoforming Tooling
Thermoforming molds shape plastic sheets by heating them and forming them over a mold. This technique is widely used in packaging and disposable product manufacturing.
Compression Molding Tooling
Compression molds apply heat and pressure to shape plastic materials, making them suitable for high-strength and heat-resistant components.
Materials Used in Plastic Tooling
Choosing the right material for plastic tooling is crucial for achieving durability, cost-efficiency, and performance.
- Aluminum – Lightweight and cost-effective, suitable for low to medium production runs.
- Steel – Offers high durability and precision, ideal for large-scale production.
- Hybrid Materials – Combine the benefits of steel and aluminum for optimized performance.
Each material has trade-offs in terms of cost, lifespan, and ease of machining, making selection an important design consideration.
Key Considerations in Plastic Tooling Design
Part Geometry and Complexity
The geometry and complexity of a plastic part significantly impact the tooling design process. Complex designs require advanced mold-making techniques to ensure accuracy, minimize defects, and optimize production efficiency.
Multi-Cavity and Family Molds
- Multi-cavity molds produce multiple identical parts simultaneously, increasing production efficiency. These are ideal for high-volume manufacturing.
- Family molds produce different parts in the same mold, reducing tooling costs and enabling efficient production of related components.
Thin Walls and Structural Integrity
- Thin-walled parts require specialized mold designs to prevent warping or collapse under injection pressure.
- Reinforcement ribs or optimized wall thickness distribution help maintain structural integrity.
Gate Placement and Flow Balancing
- Proper gate placement ensures uniform filling and prevents defects like weld lines or air traps.
- Flow-balancing techniques, such as multi-gate designs or sequential valve gating, improve consistency in part formation.
Mold Flow Analysis
Mold flow analysis is a crucial step in tooling design, using computer simulation to predict how molten plastic will flow, cool, and solidify in a mold. This helps in optimizing design parameters before physical tooling is produced.
Benefits of Mold Flow Analysis
- Prevents Defects – Identifies potential issues such as warping, sink marks, and air traps.
- Optimizes Gate and Runner Design – Ensures uniform material flow and reduces pressure imbalances.
- Improves Cooling Efficiency – Determines the best cooling channel layout to minimize cycle time and thermal stress.
Tolerances and Precision Requirements
Plastic parts often require tight tolerances to ensure they fit correctly with other components. Achieving these tolerances depends on:
Material Shrinkage Considerations
- Different plastics shrink at different rates; tooling must compensate for this variability.
- Predictive modeling helps adjust the mold dimensions accordingly.
Machining Accuracy in Tooling Fabrication
- CNC machining and EDM (Electrical Discharge Machining) are used to create high-precision mold cavities.
- Surface finish and texture play a crucial role in the final product’s dimensional accuracy.
Tolerance Stacking in Assemblies
- When multiple plastic parts need to fit together, cumulative tolerance variations must be managed.
- Adjustments in mold design help maintain assembly integrity.
Draft Angles and Undercuts
Proper draft angles and undercuts are essential for efficient part ejection and maintaining mold durability.
Draft Angles
- A draft angle (typically 1-3 degrees) allows parts to be released from the mold without excessive force.
- Lack of draft angles can cause surface defects or damage to the mold.
Undercuts and Side Actions
- Features like clips, threads, or recessed areas require special mold mechanisms such as lifters, sliders, or collapsible cores.
- Side actions increase mold complexity but allow for intricate designs.
Steps in Plastic Tooling Fabrication
Design and Prototyping
The design phase is crucial in determining the success of a plastic tooling project. Engineers use CAD (Computer-Aided Design) software to create 3D models of the mold and conduct virtual simulations.
Key Aspects of Mold Design
- Material Selection – Choosing the right metal (steel, aluminum) based on production volume and durability requirements.
- Gate and Runner Design – Optimizing the flow of molten plastic to avoid defects.
- Cooling System Layout – Ensuring uniform cooling to prevent shrinkage and warping.
Prototyping and 3D Printing
- 3D-printed molds allow for quick testing before full-scale production.
- Soft tooling (e.g., silicone molds) enables low-volume trial runs to refine part geometry.
CNC Machining and EDM
Once the mold design is finalized, it moves into the manufacturing phase.
CNC Machining (Computer Numerical Control)
- CNC milling and turning create precise mold cavities and components.
- High-speed machining ensures accuracy and repeatability in mold fabrication.
Electrical Discharge Machining (EDM)
- EDM is used to create complex features that are difficult to machine conventionally.
- It is particularly useful for deep cavities, fine details, and hardened steel molds.
Surface Finishing and Texturing
The surface finish of a mold affects the final appearance and performance of plastic parts.
Polishing Techniques
- Mirror Finish – Used for transparent plastics (e.g., optical lenses).
- Matte or Textured Finish – Achieved through bead blasting or chemical etching for aesthetic or functional purposes.
Texture Application
- Textures can be laser-etched, chemically applied, or mechanically engraved.
- Surface texturing enhances grip, reduces glare, or mimics natural materials.
Assembly and Testing
Once the individual mold components are ready, they are assembled and tested before production begins.
Mold Assembly
- Components like cores, cavities, ejector pins, and cooling lines are precisely fitted together.
- Proper alignment ensures smooth operation and longevity.
Testing and Trial Runs
- First Article Inspection (FAI) ensures that the first molded parts meet design specifications.
- Mold trials help fine-tune parameters like injection pressure, temperature, and cycle time
Advanced Technologies in Plastic Tooling
The plastic tooling industry has embraced advanced technologies to improve efficiency, accuracy, and cost-effectiveness. Here are some of the latest innovations:
CAD/CAM Software for Design
Computer-Aided Design (CAD) and Computer-Aided Manufacturing (CAM) software enable precise mold design, ensuring optimal part geometry and mold functionality. These tools help engineers simulate mold flow, predict shrinkage, and optimize cooling systems before production begins.
3D Printing for Rapid Prototyping
Additive manufacturing, or 3D printing, has revolutionized tooling design by allowing for rapid prototyping. This technology reduces development time and costs by creating accurate prototypes before finalizing the mold. 3D-printed molds are sometimes used for small production runs or testing.
AI and Automation in Tooling Fabrication
Artificial Intelligence (AI) and automation are increasingly being integrated into plastic tooling. AI-driven mold design helps identify potential defects before production, while automated CNC machining and robotic systems enhance precision and reduce human errors.
Common Challenges in Plastic Tooling
Despite technological advancements, plastic tooling presents several challenges that manufacturers must address:
Warpage and Shrinkage Issues
Plastic materials contract as they cool, which can lead to warping and dimensional inaccuracies. Engineers use mold flow analysis and proper cooling techniques to minimize these issues.
Cooling and Cycle Time Optimization
Efficient cooling is essential for maintaining production speed and quality. Poor cooling can lead to defects like sink marks. Optimized cooling channels and conformal cooling techniques help improve cycle times.
Wear and Tear of Molds
Continuous use of molds leads to wear and tear, especially with abrasive materials. Using high-quality steels and coatings can extend mold lifespan and reduce maintenance costs.
Cost Factors in Plastic Tooling
Understanding the costs associated with plastic tooling is essential for manufacturers looking to optimize their budgets.
Initial Investment vs. Long-Term Savings
High-quality molds require a significant upfront investment but provide long-term savings by minimizing production defects and downtime.
Factors Affecting Tooling Cost
- Material Choice – Steel molds are costlier but more durable than aluminum.
- Complexity – More intricate designs increase machining time and costs.
- Production Volume – Higher production runs justify more expensive, durable molds.
Cost-Saving Strategies
- Using modular mold designs for flexibility
- Employing hybrid materials to balance cost and durability
- Regular mold maintenance to extend lifespan
Quality Control in Plastic Tooling
Ensuring high-quality plastic tooling is critical for producing defect-free parts.
Inspection Techniques
- CMM (Coordinate Measuring Machines) – Checks mold dimensions with high precision.
- Laser Scanning – Captures detailed surface data for accuracy verification.
- Ultrasonic Testing – Detects internal mold defects or inconsistencies.
Common Defects and Their Solutions
- Flashing – Caused by excessive injection pressure; resolved by adjusting clamping force.
- Short Shots – Incomplete filling of the mold; fixed by increasing injection pressure.
- Sink Marks – Result from poor cooling; solved by optimizing cooling channels.
Maintenance and Longevity of Plastic Tooling Design and Fabrication
Proper maintenance extends mold life and ensures consistent production quality.
Cleaning and Lubrication
Regular cleaning prevents buildup that can affect mold performance. Applying lubricants reduces friction and wear on moving parts.
Preventive Maintenance Strategies
- Routine inspections to identify early signs of wear
- Applying protective coatings to reduce corrosion
- Keeping detailed maintenance logs for efficient servicing
Custom Plastic Tooling and Its Benefits
Custom plastic tooling offers numerous advantages over standard molds:
- Tailored Designs – Allows manufacturers to create unique parts with specific requirements.
- Increased Efficiency – Custom molds are optimized for production speed and material usage.
- Enhanced Performance – Provides better product quality and longevity compared to off-the-shelf solutions.
Sustainability in Plastic Tooling
Sustainability is becoming a key focus in manufacturing, including plastic tooling.
Eco-Friendly Materials and Processes
Using recyclable plastics and biodegradable materials reduces environmental impact. Some manufacturers are adopting bio-based resins to create greener products.
Recycling and Waste Management
Efforts to recycle plastic waste from tooling processes help minimize landfill contributions. Closed-loop manufacturing systems ensure that scrap materials are reused effectively.
Future Trends in Plastic Tooling
The future of plastic tooling is being shaped by technological advancements and sustainable practices.
Smart Molds and IoT Integration
IoT-enabled molds can provide real-time data on temperature, pressure, and cycle times. These smart molds help optimize production and detect defects early.
Sustainable Manufacturing Practices
With growing environmental concerns, manufacturers are shifting towards energy-efficient machinery and recyclable tooling materials to reduce their carbon footprint.
Conclusion Plastic Tooling Design and Fabrication
Plastic tooling design and fabrication are essential for modern manufacturing, enabling the production of precise, high-quality plastic components. Advances in materials, automation, and sustainability are shaping the industry's future. By adopting best practices in mold design, maintenance, and quality control, manufacturers can optimize costs and enhance efficiency.
FAQs Plastic Tooling Design and Fabrication
1. What is the lifespan of a plastic mold?
The lifespan depends on the material and production volume. Steel molds can last for millions of cycles, while aluminum molds are suitable for lower production runs.
2. How can I reduce tooling costs without sacrificing quality?
Using hybrid materials, optimizing mold design, and performing regular maintenance can help lower costs while maintaining quality.
3. What are the most common defects in plastic molding, and how can they be fixed?
Defects like warping, sink marks, and flashing can be minimized with proper cooling, mold flow analysis, and process optimization.
4. How does 3D printing impact plastic tooling?
3D printing allows for rapid prototyping, reducing development time and costs before finalizing the mold.
5. What are the benefits of smart molds?
Smart molds provide real-time data, improving production efficiency, reducing defects, and enabling predictive maintenance.