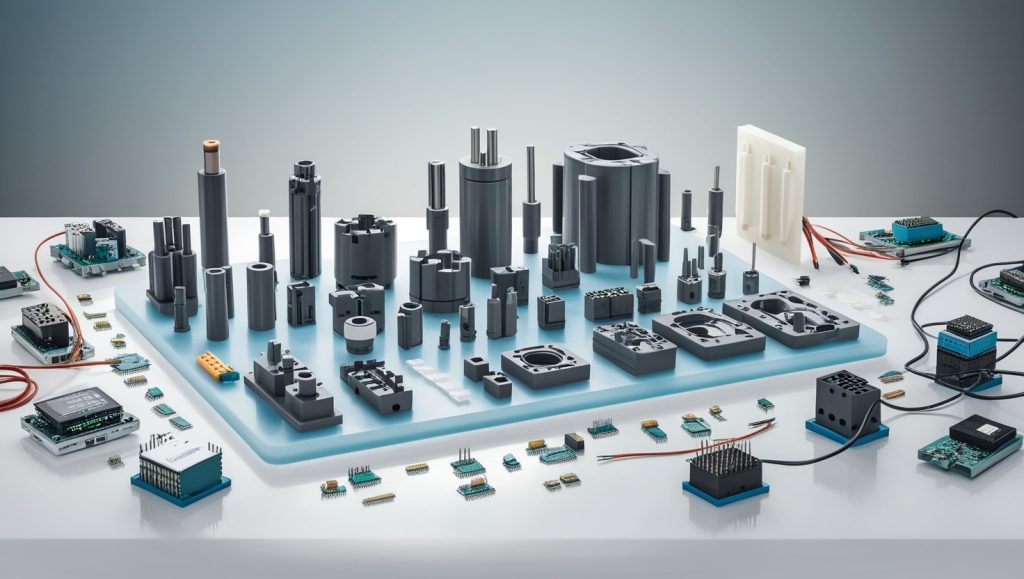
Plastic tooling in electronics manufacturing involves designing and producing molds or tools used to shape plastic components for various electronic devices. These components include casings, connectors, switches, and circuit board housings. Plastic tooling enables high-precision, durable, and cost-effective production, ensuring that electronic products meet industry standards for performance, durability, and aesthetics.
Applications of Plastic Tooling in Electronics
Plastic tooling is essential in producing a wide range of electronic devices, including:
- Consumer Electronics – Smartphone casings, laptop covers, gaming controllers, remote controls.
- Home Appliances – Plastic enclosures for televisions, washing machines, and refrigerators.
- Automotive Electronics – Dashboard panels, electronic control units (ECUs), and sensor housings.
- Industrial Electronics – Housings for power supplies, sensors, and communication devices.
Common Plastic Tooling Techniques for Electronics
Injection Molding for High-Precision Electronic Parts
Injection molding is the most widely used plastic tooling technique for electronics due to its ability to produce consistent, high-quality parts in large volumes. This process involves injecting molten plastic into a mold cavity under high pressure, which then cools and solidifies into the desired shape.
Advantages:
- High precision and repeatability
- Suitable for complex geometries and small components
- Compatible with various plastic materials, including flame-retardant plastics
Limitations:
- High initial mold-making costs
- Limited design modifications after mold fabrication
Overmolding for Multi-Material Electronic Components
Overmolding is a specialized injection molding technique that involves molding one plastic material over another to create a multi-layered structure. It is commonly used in electronics to improve grip, aesthetics, and durability.
Applications:
- Soft-touch coatings on device casings and buttons
- Protective rubberized layers on cables and connectors
- Sealed enclosures for waterproof electronics
Insert Molding for Embedded Metal Components
Insert molding integrates metal components, such as connectors, screws, and terminals, directly into a plastic part during the molding process. This technique enhances the durability and functionality of electronic components by providing strong mechanical bonds between plastic and metal.
Benefits:
- Reduces assembly steps by integrating multiple materials in one process
- Increases the structural integrity of electronic connectors
- Improves resistance to environmental factors, such as heat and moisture
Thermoforming for Large Electronic Housings
Thermoforming is used for producing large plastic housings for electronic devices. The process involves heating a plastic sheet until it becomes pliable, then shaping it over a mold using vacuum or pressure.
Best for:
- Television and monitor casings
- Large appliance control panels
- Electrical enclosures for industrial equipment
3D Printing for Prototyping and Customization
3D printing, or additive manufacturing, is widely used in the electronics industry for rapid prototyping and small-scale production. This process allows engineers to test designs, modify prototypes, and create customized components without the need for expensive molds.
Advantages:
- Enables design flexibility and iteration
- Reduces development time for new electronic products
- Ideal for low-volume, high-customization applications
Limitations:
- Slower than injection molding for mass production
- Limited selection of electronic-grade plastic materials
Key Design Considerations for Electronic Plastic Components
Material Selection for Electronic Plastic Parts
Selecting the right plastic material is crucial for ensuring durability, heat resistance, and electrical insulation. Some commonly used plastics in electronics manufacturing include:
- ABS (Acrylonitrile Butadiene Styrene) – Strong, impact-resistant, and widely used for device casings.
- Polycarbonate (PC) – Heat-resistant and transparent, ideal for screen protectors and LED covers.
- Polyamide (Nylon) – Used in connectors and circuit board mounts due to its high strength and wear resistance.
- Polyetherimide (PEI) – High-temperature-resistant plastic used in advanced electronic applications.
- Flame-Retardant Plastics – Special formulations of ABS, PC, and polyethylene that comply with fire safety regulations.
Durability and Heat Resistance
Electronic components often generate heat, so plastic materials used in enclosures and housings must withstand elevated temperatures without degrading. Additionally, plastics must be impact-resistant to protect delicate internal components from damage during handling and transport.
Precision and Dimensional Stability
Many electronic components require tight tolerances to ensure proper assembly and functionality. Precision tooling techniques, such as CNC machining and high-tolerance injection molding, are necessary to achieve consistent part dimensions.
Aesthetic and Ergonomic Design
Consumer electronics demand visually appealing and ergonomic designs. Textured surfaces, glossy finishes, and soft-touch coatings can enhance the user experience. Overmolding and custom coloring options allow manufacturers to create distinctive designs that improve brand identity.
Challenges in Plastic Tooling for Electronics
Miniaturization of Electronic Components
As electronic devices become smaller and more compact, plastic tooling must accommodate ultra-precise designs with intricate details. Micro-molding and precision CNC machining help achieve the necessary accuracy for small electronic parts.
Electromagnetic Interference (EMI) Shielding
Plastic enclosures must protect electronic circuits from electromagnetic interference. Manufacturers often apply conductive coatings, such as metalized paints or embedded shielding materials, to plastic components to prevent interference.
Compliance with Industry Regulations
Electronics manufacturers must adhere to strict safety and environmental regulations, such as:
- RoHS (Restriction of Hazardous Substances) – Limits hazardous materials in electronic components.
- UL 94 (Flammability Standard for Plastics) – Ensures plastics used in electronics meet fire safety requirements.
- ISO 9001 and IPC Standards – Regulate quality and reliability in electronic manufacturing.
Sustainability and E-Waste Reduction
With growing concerns about electronic waste, manufacturers are exploring sustainable plastic materials, such as biodegradable plastics, recycled ABS, and plant-based polyesters. Designing plastic components for easier recycling and reusability is becoming a priority in the industry.
Cost-Effective Strategies for Plastic Tooling in Electronics
- Optimize Mold Design – Reducing complexity in molds lowers production costs and material waste.
- Use Multi-Cavity Molds – Producing multiple parts per cycle increases manufacturing efficiency.
- Implement Automated Production – Robotics and AI-driven automation improve consistency and reduce labor costs.
- Leverage 3D Printing for Prototyping – Reducing the need for costly mold modifications during product development.
Future Trends in Plastic Tooling for Electronics
Smart Manufacturing and Industry 4.0
The integration of AI, IoT, and robotics in plastic tooling processes is improving efficiency, reducing errors, and enabling real-time monitoring of production. Smart factories are using data-driven insights to optimize material usage and enhance product quality.
Sustainable Materials and Circular Economy
Manufacturers are increasingly using recycled plastics, biodegradable materials, and eco-friendly manufacturing practices to reduce the environmental impact of electronic waste. The development of self-healing and recyclable polymers is expected to revolutionize plastic tooling in electronics.
Advanced 3D Printing for Functional Electronic Components
3D printing is evolving beyond prototyping, with researchers developing conductive plastics and printed circuit board (PCB) embedding technologies that integrate electronic functions directly into plastic components.
Miniaturization and High-Precision Tooling
With the demand for smaller, more compact electronic devices, micro-molding and nano-scale tooling innovations are making it possible to produce tiny yet highly functional plastic components with extreme precision.
Plastic Tooling Techniques for Electronics
Plastic tooling plays a vital role in the electronics industry, enabling manufacturers to create lightweight, durable, and cost-effective plastic components for devices ranging from smartphones to industrial control systems. Various plastic tooling techniques are used depending on the design complexity, production volume, and material requirements.
Injection Molding for High-Precision Electronic Parts
Injection molding is the most widely used plastic tooling technique in electronics manufacturing. It allows for the mass production of high-precision plastic parts, ensuring consistency and durability. The process involves melting plastic pellets and injecting them into a mold cavity under high pressure, where they cool and solidify into the final shape.
Applications in Electronics:
- Smartphone and tablet casings
- Laptop and gaming console shells
- Switches, connectors, and circuit board housings
- Remote control enclosures and battery compartments
Key Benefits:
- Produces complex geometries with high accuracy
- Offers high repeatability and consistency for large-scale production
- Works with flame-retardant and electrostatically dissipative (ESD) plastics
- Can integrate multiple functions (e.g., clips, hinges) into a single molded part
Limitations:
- High initial cost for mold design and fabrication
- Limited flexibility once the mold is created—modifications can be expensive
Overmolding for Multi-Material Electronic Components
Overmolding is a specialized injection molding technique that involves molding a second layer of plastic over an existing component. This technique is often used in electronics for improving grip, adding protective layers, and sealing parts for water resistance.
Applications in Electronics:
- Rubberized coatings on remote controls, game controllers, and phone cases
- Shock-absorbing layers on power tool grips and ruggedized electronics
- Waterproof enclosures for outdoor electronic devices
Advantages:
- Enhances product durability and comfort
- Provides insulation and protection from dust and moisture
- Reduces assembly time by integrating multiple materials in a single process
Insert Molding for Embedded Metal Components
Insert molding combines plastic and metal components within a single molded part. In this process, metal inserts (such as screws, connectors, or terminals) are placed inside the mold before plastic is injected around them.
Common Applications:
- USB ports, headphone jacks, and power connectors
- Threaded inserts in laptop hinges and device mounting points
- Electrical switches and circuit board supports
Key Benefits:
- Strengthens connections between plastic and metal parts
- Reduces assembly time and labor costs
- Increases resistance to wear and tear
Thermoforming for Large Electronic Housings
Thermoforming is used to create large plastic enclosures by heating a plastic sheet and molding it over a form. This technique is commonly used for home appliances, industrial electronics, and kiosk enclosures.
Benefits of Thermoforming:
- Lower tooling costs compared to injection molding
- Faster production cycles for large plastic parts
- Ideal for creating durable, lightweight casings for electronic devices
3D Printing for Prototyping and Customization
3D printing has revolutionized product development in the electronics industry by allowing manufacturers to create prototypes, test designs, and produce small-batch components without the need for expensive molds.
Key Advantages:
- Allows for rapid design iteration and customization
- Reduces development time and costs
- Supports complex geometries that traditional molding cannot achieve
Material Selection for Electronic Plastic Parts
Choosing the right plastic material is critical for ensuring durability, safety, and performance in electronic components. The selected plastic must withstand environmental stress, heat, and electrical insulation requirements.
Commonly Used Plastics in Electronics:
ABS (Acrylonitrile Butadiene Styrene)
- Properties: Strong, impact-resistant, and easy to mold
- Applications: Smartphone enclosures, laptop shells, remote controls
- Advantages: Cost-effective and offers good mechanical properties
- Disadvantages: Not highly resistant to heat or chemicals
Polycarbonate (PC)
- Properties: Transparent, heat-resistant, and impact-resistant
- Applications: LED covers, safety panels, optical lenses
- Advantages: High durability, flame-resistant, and lightweight
- Disadvantages: Susceptible to scratches without coatings
Polyamide (Nylon)
- Properties: High strength, chemical-resistant, and wear-resistant
- Applications: Gears, switches, and circuit board mounts
- Advantages: Flexible, durable, and self-lubricating
- Disadvantages: Can absorb moisture, affecting mechanical properties
Polyetherimide (PEI, ULTEM)
- Properties: High-temperature resistance and excellent electrical insulation
- Applications: High-performance electronics, aerospace components
- Advantages: Flame-resistant and highly durable
- Disadvantages: Expensive and harder to process than standard plastics
Flame-Retardant Plastics
- Properties: Comply with UL 94 flammability standards for electronics
- Applications: Power supply enclosures, circuit board housings, battery compartments
- Advantages: Reduces fire risks in electrical products
Challenges in Plastic Tooling for Electronics
Miniaturization and Precision Requirements
As electronic devices become smaller and more complex, plastic tooling must accommodate ultra-fine details and tight tolerances. Micro-molding and CNC machining are essential for achieving the required precision in compact devices.
Electromagnetic Interference (EMI) Shielding
Plastic enclosures must be designed to protect electronic circuits from electromagnetic interference (EMI), which can disrupt device performance. Manufacturers use:
- Conductive coatings (e.g., metalized paints)
- Embedded shielding materials (e.g., carbon-filled plastics)
Environmental Compliance and Sustainability
The electronics industry is under pressure to comply with regulations such as:
- RoHS (Restriction of Hazardous Substances) – Limits toxic substances in electronics.
- WEEE (Waste Electrical and Electronic Equipment Directive) – Promotes recycling and e-waste reduction.
Future Trends in Plastic Tooling for Electronics
Smart Manufacturing and Industry 4.0
AI-driven design and IoT-enabled manufacturing systems are transforming plastic tooling. Real-time monitoring, predictive maintenance, and automated quality control help manufacturers improve efficiency and reduce costs.
Sustainable and Recycled Plastics
With increasing concerns over electronic waste, manufacturers are exploring:
- Recycled ABS and polycarbonate plastics
- Biodegradable polymers for temporary and disposable electronics
Advancements in 3D Printing for Functional Electronic Parts
3D printing is evolving beyond prototyping, with new developments in conductive plastics and printed circuit board (PCB) integration. This could enable electronics to be embedded directly into plastic parts, eliminating the need for separate PCBs.
Cost-Effective Strategies for Plastic Tooling in Electronics
- Optimize Mold Design – Reducing complexity and minimizing material waste.
- Use Multi-Cavity Molds – Producing multiple parts per cycle to improve efficiency.
- Leverage Automation – Using robotics and AI-driven monitoring to enhance consistency.
- Invest in Rapid Prototyping – Using 3D printing for early design validation before committing to expensive molds.