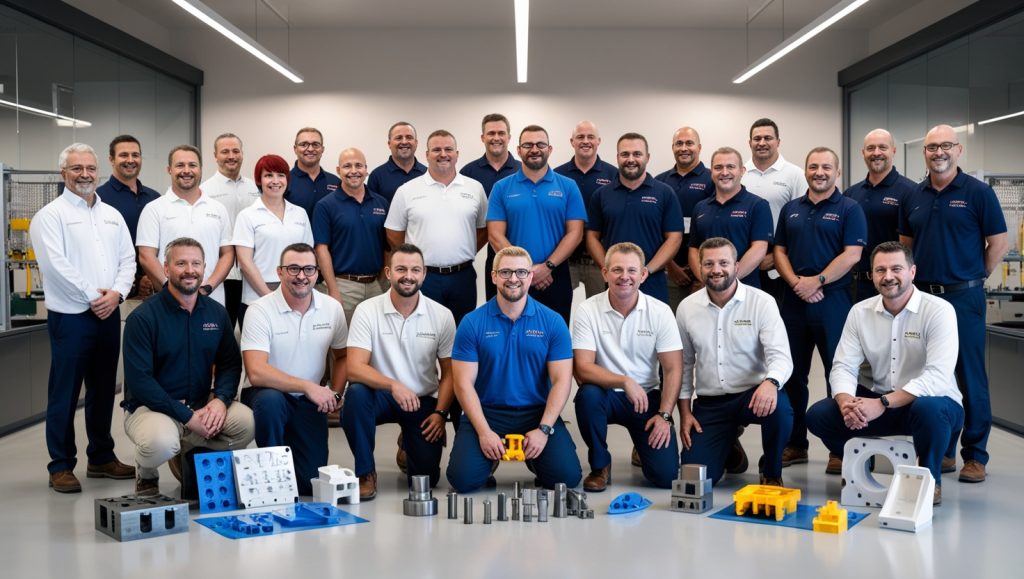
Plastic tooling suppliers play a crucial role in the manufacturing industry, providing the molds, dies, and other essential components required for plastic part production. Choosing a reliable supplier ensures product consistency, quality, and cost-efficiency.
What Are Plastic Tooling Suppliers?
Plastic tooling suppliers provide molds, dyes, and tooling components required for shaping plastic materials into finished products. These suppliers may specialize in injection molding, blow molding, compression molding, extrusion, or thermoforming.
Importance of Reliable Plastic Tooling Suppliers in Manufacturing
Working with a trusted plastic tooling supplier can:
- Improve production efficiency with high-quality molds.
- Reduce defects and waste, ensuring uniform product quality.
- Lower long-term costs by providing durable and precise tooling.
- Ensure timely delivery to prevent production delays.
Industries That Depend on Plastic Tooling Suppliers
Several industries rely on plastic tooling suppliers for high-precision manufacturing, including:
- Automotive – Producing dashboards, bumpers, and engine components.
- Medical – Manufacturing syringes, surgical instruments, and prosthetics.
- Consumer Goods – Creating household products, packaging, and toys.
- Electronics – Developing casings, connectors, and circuit board components.
- Aerospace – Providing lightweight, high-strength plastic parts for aircraft.
Types of Plastic Tooling Supplies
Different plastic tooling supplies are available depending on the manufacturing process.
Injection Molding Tooling Supplies
Injection molding is one of the most common methods for mass-producing plastic components. Suppliers provide:
- Steel and aluminum molds for injection molding.
- Hot runner systems for improving efficiency.
- CNC-machined mold inserts for high precision.
Blow Molding Tooling Supplies
Blow molding is used for hollow plastic items like bottles and containers. Tooling supplies include:
- Blow molds made from aluminum or steel.
- Parison programming tools for controlling material thickness.
Compression Molding Tooling Supplies
Compression molding involves pressing heated plastic into a mold. Supplies include:
- Metal molds with high heat resistance.
- Hydraulic presses for uniform compression.
Extrusion Molding Tooling Supplies
Extrusion molding is used for making pipes, tubes, and sheets. Suppliers offer:
- Die heads for extrusion machines.
- Cooling and calibration tools for shaping materials.
Thermoforming Tooling Supplies
Thermoforming involves heating plastic sheets and forming them over a mold. Supplies include:
- Vacuum forming molds.
- Pressure forming dies for detailed parts.
How to Choose the Right Plastic Tooling Supplier
Selecting the right plastic tooling supplier is critical to ensuring high-quality products.
Evaluating Supplier Experience and Reputation
A reputable supplier should have:
- Years of experience in plastic tooling.
- Positive customer reviews and testimonials.
- A strong track record in your specific industry.
Assessing Manufacturing Capabilities and Technology
The best suppliers invest in cutting-edge technology, including:
- CNC machining for high-precision molds.
- 3D printing for rapid prototyping.
- EDM (Electrical Discharge Machining) for fine details.
Quality Standards and Certifications
Ensure the supplier follows industry standards such as:
- ISO 9001 – Quality Management System.
- ISO 13485 – Medical device manufacturing compliance.
- IATF 16949 – Automotive industry tooling standards.
Pricing and Cost Considerations
Compare multiple suppliers and assess:
- Initial tooling costs vs. long-term durability.
- Bulk order discounts for large-scale production.
- Hidden fees for maintenance and modifications.
Lead Times and Delivery Efficiency
A good supplier should have:
- Fast production times for urgent orders.
- Reliable delivery networks to avoid delays.
- Efficient customer service for order tracking and troubleshooting.
Top Plastic Tooling Suppliers Worldwide
Here are some of the best plastic tooling suppliers globally:
Best Plastic Tooling Suppliers in the USA
- Proto Labs – Specializes in rapid injection molding and CNC machining.
- EVCO Plastics – Experts in large-scale plastic molding.
- Xometry – Offers custom plastic tooling services.
- Rodon Group – Known for high-precision tooling.
Leading European Plastic Tooling Suppliers
- LEMOINE (France) – High-precision plastic tooling specialists.
- GÜNTHER Hot Runner Systems (Germany) – Experts in hot runner injection molding.
- Stork IMM (Netherlands) – Focuses on high-speed plastic molding solutions.
Top Asian Plastic Tooling Suppliers
- Shenzhen Silver Basis Technology Co., Ltd. (China) – A leading mold manufacturer.
- Him Technoforge Ltd. (India) – Supplies durable plastic tooling solutions.
- Juken Technology (Singapore) – Experts in plastic injection molding tools.
Innovations and Trends in Plastic Tooling Supply
The plastic tooling industry is evolving with technological advancements that improve efficiency, sustainability, and product quality. Here are some of the latest trends:
Use of AI and Automation in Plastic Tooling
Artificial intelligence (AI) and automation are transforming how plastic tooling suppliers operate by:
- Optimizing mold design through AI-assisted CAD software.
- Automating quality control to detect defects before production.
- Using predictive maintenance to extend the lifespan of molds.
Sustainable and Eco-Friendly Tooling Materials
With increased environmental awareness, plastic tooling suppliers are adopting:
- Recyclable plastics and biodegradable alternatives.
- Energy-efficient manufacturing to reduce carbon footprints.
- Water-saving cooling systems for molds.
3D Printing and Rapid Tooling Advancements
3D printing is revolutionizing the tooling industry by:
- Reducing lead times for prototype molds.
- Allowing for more complex and intricate mold designs.
- Lowering costs for low-volume production and testing.
Industry 4.0 and Smart Manufacturing Integration
Plastic tooling suppliers are adopting smart manufacturing with:
- IoT-connected machines that track production efficiency.
- Cloud-based data analysis for better decision-making.
- Automated production lines to increase speed and accuracy.
Challenges in Plastic Tooling Supply and How to Overcome Them
Despite the continuous advancements in plastic tooling technology, businesses still face several challenges in sourcing, maintaining, and managing tooling supplies. From quality control issues to rising costs and supply chain disruptions, these challenges can significantly impact production efficiency and profitability. However, implementing the right strategies can help businesses mitigate these challenges and maintain a steady supply of high-quality plastic tooling components.
Quality Control and Defect Management
Challenge: Inconsistent mold quality can lead to defects in production, which increases waste, slows down manufacturing, and affects the final product’s reliability. Poor-quality molds may result in uneven plastic distribution, warping, or short-shot defects, ultimately leading to product recalls or customer dissatisfaction.
Solution: Implementing automated inspection systems and strict quality control measures can significantly reduce defects. Using computer-aided design (CAD) software and high-precision CNC machining ensures that molds meet tight tolerances. Manufacturers should also conduct rigorous testing through first-article inspections (FAI) and trial runs before full-scale production. Additionally, adopting real-time monitoring systems in manufacturing allows for quick identification and correction of mold defects, preventing costly recalls.
Supply Chain Disruptions and Delays
Challenge: Global supply chain disruptions, such as shipping delays, raw material shortages, and geopolitical instability, can lead to extended lead times for plastic tooling. Delayed mold deliveries can halt production lines, leading to financial losses and unmet customer demands.
Solution: To mitigate supply chain risks, businesses should:
- Diversify their supplier base – Working with multiple suppliers across different regions ensures backup options in case of disruptions.
- Partner with domestic manufacturers – Sourcing molds locally can reduce reliance on overseas shipping and help avoid geopolitical risks.
- Implement inventory management strategies – Stocking critical tooling components and using predictive demand forecasting can prevent last-minute shortages.
- Adopt just-in-time (JIT) and lean manufacturing – These strategies help optimize inventory levels and minimize supply chain bottlenecks.
Rising Costs of Raw Materials
Challenge: The cost of steel, aluminum, and plastic resins continues to rise due to increasing global demand, supply chain constraints, and fluctuations in commodity markets. Higher raw material costs make it expensive to manufacture new molds, increasing overall production expenses.
Solution: Businesses can manage costs by:
- Selecting cost-efficient materials – Instead of fully hardened steel molds, companies can opt for pre-hardened steel or aluminum molds for short production runs.
- Using modular and multi-use molds – Designing interchangeable mold inserts allows businesses to reuse tooling across different products, reducing the need for new molds.
- Leveraging supplier relationships for better pricing – Bulk purchasing and long-term contracts can help lock in stable pricing.
- Investing in recycled and sustainable plastics – Some plastic tooling components can be produced from recycled materials, lowering material expenses.
Compliance with Industry Regulations
Challenge: Different industries, such as automotive, aerospace, medical, and food packaging, have stringent safety and quality regulations. Non-compliance can lead to product recalls, fines, and legal issues.
Solution: To ensure compliance, businesses should:
- Choose ISO-certified suppliers – Suppliers with certifications such as ISO 9001, ISO 13485 (medical devices), or IATF 16949 (automotive) demonstrate adherence to quality and safety standards.
- Regularly audit suppliers and tooling processes – Conducting internal and third-party audits ensures that tooling meets industry regulations.
- Use validated tooling materials – Some industries require FDA-approved plastic resins or high-heat-resistant materials for safety and performance compliance.
Cost of Plastic Tooling Supplies – What to Expect
Understanding the cost structure of plastic tooling supplies is essential for budgeting and maximizing return on investment. Several factors influence the cost of tooling, and businesses must strategically manage these expenses.
Factors That Affect Plastic Tooling Prices
- Material Choice – Steel molds are more expensive but offer superior durability, while aluminum molds are more affordable and suitable for shorter production runs.
- Complexity of Mold Design – Multi-cavity and intricate molds require more machining time, increasing costs.
- Production Volume – Higher production volumes allow manufacturers to distribute tooling costs over many units, reducing per-unit expenses.
- Supplier Location – Asian suppliers generally offer lower-cost molds than those in North America or Europe, but businesses must consider shipping costs and lead times.
Budgeting for Different Tooling Needs
- For Prototyping: Consider 3D-printed molds or soft tooling for quick, cost-effective testing.
- For Small Production Runs: Use aluminum molds or low-cost rapid tooling to minimize expenses.
- For High-Volume Production: Invest in high-quality steel molds, as they offer long-term savings by lasting through millions of cycles.
Cost-Saving Strategies When Purchasing Tooling Supplies
- Use standardized mold bases – Standardized components reduce custom machining costs and lead times.
- Buy in bulk – Ordering large quantities of tooling components can help negotiate better pricing.
- Partner with local suppliers – Reducing reliance on overseas shipping can lower transportation and import costs.
- Consider mold refurbishment instead of full replacements – Reconditioning or modifying existing molds can extend their lifespan and reduce the need for new molds.
Final Thoughts
Despite the plastic tooling industry challenges, businesses can strategically manage risks and expenses by implementing quality control systems, diversifying their supplier base, optimizing raw material usage, and ensuring compliance with industry regulations. By planning ahead and adopting cost-effective procurement strategies, companies can minimize disruptions and maintain efficient, high-quality production.
The plastic tooling industry is rapidly evolving with smart manufacturing, sustainable materials, and automation. Businesses that adapt to these changes will stay ahead of competitors and reduce production costs while improving product quality.
FAQs
1. What are the most important factors when selecting a plastic tooling supplier?
Look for experience, certifications, production capabilities, pricing, and customer service when selecting a supplier.
2. How can I ensure high-quality plastic tooling supplies?
Choose ISO-certified suppliers, inspect sample molds, and request detailed quality reports before purchasing.
3. What is the average cost of plastic tooling supplies?
Plastic tooling costs vary depending on material, mold complexity, and production volume, typically ranging from $5,000 to $100,000 for molds.
4. Which industries require plastic tooling suppliers the most?
Automotive, medical, consumer goods, electronics, and aerospace industries heavily rely on plastic tooling for manufacturing components.
5. How can I reduce lead times when sourcing plastic tooling?
- Work with local suppliers to avoid international shipping delays.
- Use rapid tooling methods like 3D printing for prototypes.
- Plan ahead and order tooling supplies early to prevent production interruptions.