Plastic tooling is essential in the manufacturing of consumer products, enabling mass production of high-quality, durable, and cost-effective plastic components. From household appliances and electronic enclosures to packaging and toys, plastic tooling allows manufacturers to produce intricate designs with precision and consistency.
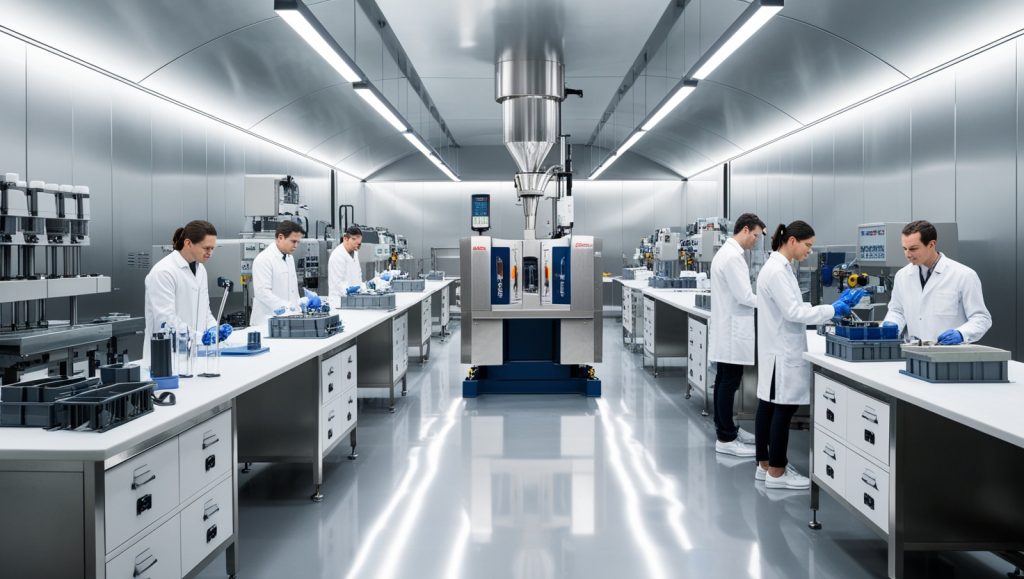
With advancements in manufacturing technologies, plastic tooling has evolved to accommodate complex geometries, enhance production efficiency, and reduce costs. Various tooling techniques, such as injection molding, thermoforming, and 3D printing, cater to different product requirements, making plastic a versatile choice for consumer goods.
This article explores the various plastic tooling methods used in consumer product manufacturing, design considerations, challenges, cost-effective strategies, and future trends shaping the industry.
Understanding Plastic Tooling for Consumer Products
Definition and Purpose
Plastic tooling refers to the process of designing and manufacturing molds, dies, or tools used to shape plastic materials into consumer products. These tools are used in mass production to create parts with high precision, ensuring uniformity, strength, and aesthetic appeal.
Applications in Consumer Products
Plastic tooling is widely used in various consumer industries, including:
- Electronics – Enclosures, connectors, and casings for smartphones, laptops, and appliances.
- Household Goods – Plastic utensils, containers, and furniture components.
- Automotive Accessories – Interior trim, dashboards, and handles.
- Packaging – Bottles, caps, and custom plastic containers.
- Toys and Recreational Items – Action figures, game controllers, and outdoor equipment.
Common Plastic Tooling Techniques for Consumer Products
Injection Molding
Injection molding is the most common plastic tooling method, used for high-volume production of detailed plastic components. It involves injecting molten plastic into a mold cavity under high pressure, which then cools and solidifies into the desired shape.
Advantages
- High precision and repeatability
- Suitable for complex and detailed designs
- Works with various plastic materials
Limitations
- High initial tooling costs
- Design modifications can be expensive once the mold is created
Blow Molding
Blow molding is used to create hollow plastic products, such as bottles, containers, and plastic drums. The process involves inflating a heated plastic tube inside a mold, shaping it into the final form.
Advantages
- Cost-effective for producing lightweight plastic products
- High production speed and efficiency
Limitations
- Limited to hollow structures
- Less control over wall thickness compared to injection molding
Thermoforming
Thermoforming is a process in which a plastic sheet is heated and molded into a desired shape using vacuum or pressure. It is commonly used for packaging materials, trays, and disposable containers.
Advantages
- Lower tooling costs compared to injection molding
- Fast production cycles for large plastic parts
Limitations
- Not ideal for highly detailed or intricate designs
- Limited to thin-walled plastic products
3D Printing (Additive Manufacturing)
3D printing is increasingly used for prototyping consumer products before mass production. It allows manufacturers to test designs and make quick modifications without requiring expensive molds.
Advantages
- No need for traditional molds, reducing upfront costs
- Customization and design flexibility
- Ideal for low-volume production and prototyping
Limitations
- Slower production speed compared to injection molding
- Limited material options for mass production
CNC Machining for Plastic Components
CNC machining is used to cut plastic materials with high precision, often for enclosures, mechanical parts, and specialty components. It is useful for producing durable and heat-resistant plastic parts.
Advantages
- High accuracy and detail
- Suitable for complex geometries and custom designs
Limitations
- Higher material waste compared to other methods
- Not ideal for mass production due to longer processing times
Key Design Considerations for Plastic Consumer Products
Material Selection
Choosing the right plastic material is crucial to ensuring the durability, flexibility, and performance of consumer products. Some commonly used plastics include:
- ABS (Acrylonitrile Butadiene Styrene) – Strong and impact-resistant, commonly used in electronic casings and automotive parts.
- Polycarbonate – Highly durable and heat-resistant, ideal for optical lenses and safety equipment.
- Polypropylene (PP) – Lightweight and chemical-resistant, used in food containers and packaging.
- PET (Polyethylene Terephthalate) – Transparent and recyclable, widely used in beverage bottles and packaging.
Aesthetic and Functional Design
Consumer products must balance aesthetics and functionality. Key design considerations include:
- Smooth surface finishes for an appealing look
- Ergonomic designs for better user experience
- Durability to withstand wear and tear
Mold Complexity and Tooling Costs
Complex designs require advanced mold-making techniques. To minimize costs:
- Use modular tooling for interchangeable parts
- Optimize designs to reduce material waste
- Implement draft angles to facilitate easy mold release
Challenges in Plastic Tooling for Consumer Products
Cost Management
- High initial tooling costs can be a barrier, especially for small-scale production.
- Efficient material usage and lean manufacturing help reduce expenses.
Durability and Quality Control
- Ensuring consistency in mass production is critical.
- Proper mold maintenance and process monitoring help prevent defects.
Sustainability and Environmental Concerns
- The growing demand for eco-friendly products requires sustainable material choices.
- Biodegradable and recycled plastics are becoming popular alternatives.
Cost-Effective Strategies for Plastic Tooling in Consumer Products
- Optimize Mold Design – Reducing complexity in molds can lower manufacturing costs.
- Use Rapid Prototyping – 3D printing prototypes help refine designs before investing in expensive molds.
- Invest in Multi-Cavity Molds – Producing multiple parts per cycle increases efficiency.
- Automate Production – Advanced automation reduces labor costs and enhances consistency.
Future Trends in Plastic Tooling for Consumer Products
- Smart Manufacturing – AI and IoT integration for enhanced production efficiency.
- Sustainable Materials – Increased use of biodegradable and recycled plastics.
- Advanced 3D Printing – Improved additive manufacturing for high-quality, customizable products.
- Hybrid Manufacturing – Combining multiple techniques, such as injection molding and 3D printing, for greater flexibility.
Plastic Tooling for Medical Devices
Plastic tooling in the medical industry is a crucial process that allows manufacturers to produce high-precision, biocompatible, and sterile medical components. Medical devices often require intricate designs, tight tolerances, and exceptional quality control to ensure patient safety and regulatory compliance. Unlike other consumer products, medical plastic components must adhere to stringent industry standards to avoid contamination, degradation, or failure in critical applications. Plastic tooling enables mass production of disposable syringes, IV connectors, surgical instruments, and diagnostic equipment while maintaining consistent quality.
Regulatory and Compliance Requirements (FDA, ISO Standards)
Due to the sensitive nature of medical devices, plastic tooling must adhere to strict regulatory guidelines set by organizations such as the U.S. Food and Drug Administration (FDA) and the International Organization for Standardization (ISO 13485). These regulations ensure that medical-grade plastics are safe, non-toxic, and resistant to chemicals and sterilization processes. The compliance process involves rigorous testing of materials, validation of the tooling process, and quality assurance measures such as cleanroom manufacturing to minimize contamination risks.
Material Selection for Biocompatibility and Sterility
Medical devices require specialized plastic materials that can withstand sterilization methods such as autoclaving, gamma radiation, and ethylene oxide exposure. Common medical-grade plastics include:
- Polycarbonate (PC) – Used for surgical instruments and housings due to its high strength and transparency.
- Polyether Ether Ketone (PEEK) – A biocompatible and chemically resistant plastic used in implants and orthopedic components.
- Polypropylene (PP) – A cost-effective, flexible plastic used in syringes, labware, and disposable medical tools.
- Thermoplastic Elastomers (TPEs) – Used in medical tubing and seals for their flexibility and rubber-like properties.
Material selection directly impacts the performance, durability, and sterility of medical devices, making it a critical factor in plastic tooling for healthcare applications.
Plastic Tooling Techniques for Medical Devices
Injection Molding for Precision Medical Parts
Injection molding is the most widely used method for producing medical-grade plastic components. This process allows for the mass production of highly detailed, precise, and sterile parts at a low cost per unit. Medical injection molding involves specialized cleanroom environments, medical-grade resin selection, and post-processing sterilization. It is particularly useful for producing complex parts such as surgical handles, ventilator components, and drug delivery systems.
Micro-Molding for Small and Intricate Components
Micro-molding is an advanced variation of injection molding that enables the production of ultra-small plastic components, often weighing less than a gram. This technique is essential for manufacturing tiny medical parts such as catheter tips, hearing aid components, and microfluidic devices. Due to the small scale of these components, specialized high-precision molds and quality control systems are necessary to maintain accuracy.
3D Printing for Rapid Prototyping and Customization
3D printing, or additive manufacturing, is increasingly used in medical plastic tooling for prototyping, small-batch production, and custom medical implants. Unlike traditional injection molding, 3D printing allows for rapid design modifications, complex geometries, and patient-specific medical devices. This is particularly useful in orthopedics, dental applications, and prosthetics, where customization is required to match individual patient needs. While not yet suitable for high-volume production, 3D printing significantly reduces development time and costs.
Challenges in Medical Plastic Tooling
Ensuring High Precision and Tolerance Levels
Medical components require extremely tight tolerances, often within microns, to ensure functionality and compatibility with other medical equipment. Any deviation in size or shape can compromise the effectiveness of a device, potentially putting patients at risk. Achieving such precision in plastic tooling requires advanced mold-making technologies, real-time quality control, and specialized measurement tools.
Sterility and Contamination Prevention
Unlike other plastic applications, medical tooling must adhere to strict cleanliness standards. Even the smallest contamination can render a medical device unsafe for use. Cleanroom manufacturing environments with controlled airflow, temperature, and humidity are required to prevent airborne particles from affecting the plastic tooling process. Additionally, post-production sterilization methods such as UV treatment and chemical sanitization ensure medical plastic components remain free from harmful microbes.
Cost vs. Quality Balance in Medical-Grade Production
Developing plastic tooling for medical devices is expensive due to the high standards, regulatory requirements, and precision involved. Manufacturers must balance the cost of tooling, material selection, and compliance with maintaining profitability. Strategies such as modular tooling, automation, and lean manufacturing can help reduce costs while maintaining high-quality output.
Future Trends in Medical Plastic Tooling
Advancements in Biodegradable Medical Plastics
The medical industry is increasingly exploring biodegradable plastics for applications such as sutures, temporary implants, and drug-delivery devices. These materials break down naturally in the body or the environment, reducing medical waste and improving patient outcomes. Research into biopolyesters like PLA (Polylactic Acid) and PHA (Polyhydroxyalkanoates) is paving the way for sustainable medical solutions.
AI-Driven Design Optimizations for Medical Tools
Artificial intelligence (AI) and machine learning are transforming the way medical devices are designed and manufactured. AI-driven simulations help optimize mold designs, predict material behavior, and improve manufacturing efficiency. Automated quality control systems using AI-powered vision technology are also reducing defects and increasing production accuracy.
Automation in Medical Device Manufacturing
Automation is playing a crucial role in improving consistency, reducing labor costs, and increasing production efficiency. Robotic-assisted plastic tooling allows for faster cycle times, precise material handling, and real-time monitoring of quality standards. The adoption of Industry 4.0 technologies, such as smart sensors and IoT integration, is further enhancing the reliability of medical plastic tooling.
Conclusion
Plastic tooling is a cornerstone of consumer product manufacturing, offering cost-effective, durable, and scalable solutions for a wide range of applications. Whether through injection molding, thermoforming, or 3D printing, manufacturers continue to refine plastic tooling techniques to enhance product quality and efficiency.
As sustainability and technological advancements reshape the industry, manufacturers must adapt to eco-friendly materials, smart automation, and innovative design strategies. By optimizing tooling methods, businesses can reduce costs while delivering high-quality consumer products.
Frequently Asked Questions (FAQs)
1. Why is plastic tooling important in consumer product manufacturing?
Plastic tooling allows manufacturers to create high-quality, cost-effective, and durable plastic components for consumer products. It ensures consistency and efficiency in mass production while enabling complex designs.
2. What is the best plastic tooling method for mass production?
Injection molding is the most effective method for mass production due to its high precision, repeatability, and ability to produce large volumes at a relatively low cost per unit.
3. How can manufacturers reduce costs in plastic tooling?
Cost-saving strategies include optimizing mold designs, using modular tooling, implementing automation, and leveraging rapid prototyping to refine designs before mass production.
4. What are the best plastics for consumer products?
Commonly used plastics include ABS for impact resistance, polycarbonate for durability, polypropylene for lightweight packaging, and PET for recyclable applications.
5. How is sustainability impacting plastic tooling?
Sustainability is driving the adoption of biodegradable and recycled plastics, energy-efficient production methods, and eco-friendly design strategies to reduce plastic waste.