To stay competitive in today's rapidly evolving industrial landscape, it's important to constantly innovate and adapt. One area of innovation that has seen significant advancements is prototyping metal parts, and it's a game changer for many industries. ACE is at the forefront of this revolution. In this blog post, we will explore how prototyping metal parts can benefit your business and discuss how ACE can drive a competitive advantage for your company.
How Can Prototyping Metal Parts Benefit Your Industry?
Prototyping metal parts is a pivotal process that brings numerous benefits to various industries. Whether you're in aerospace, automotive, medical, or any other sector, the advantages are manifold.
1.1 Precision and Accuracy
One of the primary benefits of prototyping metal parts is the ability to achieve unparalleled precision and accuracy. ACE employs cutting-edge technologies such as Computer Numerical Control (CNC) machining and 3D printing to create metal prototypes with tight tolerances. This precision ensures that the final production parts will meet the desired specifications, reducing the risk of costly errors down the line.
1.2 Speed and Efficiency
Traditional metal manufacturing processes can be time-consuming and expensive, especially when creating custom or complex parts. Prototyping metal parts with ACE significantly reduces lead times. Rapid prototyping allows for quick iterations and modifications, accelerating the product development cycle and enabling you to get your innovations to market faster.
1.3 Cost Savings
By creating prototypes before committing to full-scale production, you can identify design flaws and potential manufacturing issues early in the process. This proactive approach can save your industry substantial amounts of money by avoiding costly rework or tooling changes. ACE's expertise in prototyping metal parts can help optimize designs for cost-effective production.
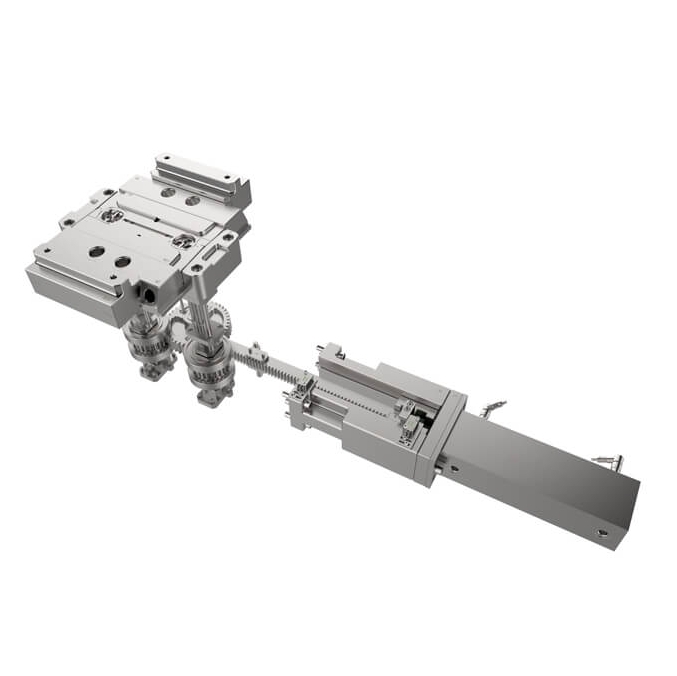
Are You Exploring the Full Potential of Prototyping Metal Parts?
While the benefits of prototyping metal parts are clear, many industries may not be fully aware of the potential that lies within this innovative approach. Here are some additional ways you can harness the power of metal prototyping:
2.1 Customization and Complexity
Prototyping metal parts allows for intricate and highly customized designs that might be impossible or cost-prohibitive using traditional manufacturing methods. This opens up new possibilities for creating unique and specialized products tailored to your industry's specific needs.
2.2 Material Exploration
ACE offers a wide range of metal materials for prototyping, including aluminum, stainless steel, titanium, and more. This versatility allows your industry to explore different materials and their properties to find the perfect fit for your application, whether it's for lightweight aerospace components or durable automotive parts.
2.3 Risk Mitigation
By prototyping metal parts early in the design process, your industry can identify and address potential issues before they become major problems. This risk mitigation strategy helps ensure the reliability and safety of your final products, which is crucial in industries like healthcare, where lives are at stake.
What Are the Latest Innovations in Prototyping Metal Parts?
The world of prototyping metal parts is constantly evolving, and ACE is committed to staying at the cutting edge of these innovations. Here are some of the latest advancements in the field:
3.1 Additive Manufacturing
Additive manufacturing, often referred to as 3D printing, has revolutionized the way metal parts are prototyped. ACE utilizes advanced 3D printing technologies that enable the creation of complex geometries and intricate structures with ease. This innovation not only saves time but also reduces material waste.
3.2 Digital Twin Technology
Digital twin technology involves creating a digital replica of a physical part or system. ACE leverages digital twin technology to simulate and optimize prototypes before physical production. This not only enhances the design process but also reduces the number of physical prototypes required, further saving time and resources.
3.3 AI-Driven Design
Artificial intelligence is being used to analyze and optimize designs for prototyping metal parts. ACE employs AI algorithms to generate design suggestions, predict potential manufacturing issues, and fine-tune designs for improved performance and efficiency.
What Are the Top Techniques for Prototyping Metal Parts?
ACE employs cutting-edge techniques to provide the highest-quality metal prototypes. Here are some of the top methods used in metal prototyping:
4.1 CNC Machining
Computer Numerical Control (CNC) machining is a precise and versatile technique that ACE utilizes for metal prototyping. It involves removing material from a solid block of metal using computer-controlled tools. CNC machining can produce intricate and complex metal parts with exceptional accuracy.
4.2 3D Printing
Additive manufacturing, commonly known as 3D printing, has transformed the world of metal prototyping. ACE uses advanced 3D printing technology to build metal parts layer by layer. This method allows for the creation of complex geometries and intricate structures, reducing material waste and production time.
4.3 Sheet Metal Fabrication
For industries requiring thin and flat metal components, ACE offers sheet metal fabrication services. This technique involves cutting, bending, and shaping metal sheets to create prototypes with precision. It's an excellent choice for industries like electronics and telecommunications.
Are Prototyping Metal Parts the Solution to Rapid Innovation?
Innovation is the lifeblood of any industry, and prototyping metal parts plays a pivotal role in driving rapid innovation.
5.1 Shortened Development Cycles
Prototyping metal parts with ACE allows your industry to test and refine new ideas quickly. By reducing lead times and streamlining the design process, you can bring innovative products and solutions to market faster than your competitors.
5.2 Enhanced Collaboration
Metal prototypes facilitate collaboration among different departments within your industry. Engineers, designers, and manufacturers can work closely together, testing and optimizing designs in real time, resulting in more innovative and successful products.
Cost-Effective Innovation
Innovation can be costly, but prototyping metal parts helps mitigate these expenses. Early identification and resolution of design issues lead to cost savings in the long run. ACE's expertise ensures that your industry can innovate efficiently and cost-effectively.
How Does Prototyping Metal Parts Drive Competitive Advantage?
In today's fiercely competitive business environment, gaining a competitive advantage is crucial for survival and growth. Prototyping metal parts with ACE can be a key driver of that advantage.
6.1 Faster Time-to-Market
By reducing the time it takes to develop and iterate prototypes, your industry can bring products to market faster than competitors. This agility allows you to respond to market demands more rapidly and seize new opportunities ahead of the competition.
6.2 Enhanced Product Quality
ACE's commitment to precision and accuracy ensures that your industry's prototypes are of the highest quality. This translates into better-performing final products, reducing defects, recalls, and costly post-production fixes.
6.3 Cost Efficiency
The cost savings achieved through prototyping metal parts can be reinvested into research and development, marketing, or other areas of your industry. This financial flexibility allows for more aggressive pricing strategies or the development of new product lines.
Conclusion
In conclusion, prototyping metal parts is a transformative process that can greatly benefit your industry. ACE, as a leading manufacturer in this field, offers the precision, speed, and innovation required to stay competitive in today's fast-paced world. Embrace the full potential of metal prototyping to drive your industry forward and secure a brighter future.